Obtain news and background information about sealing technology, get in touch with innovative products – subscribe to the free e-mail newsletter.
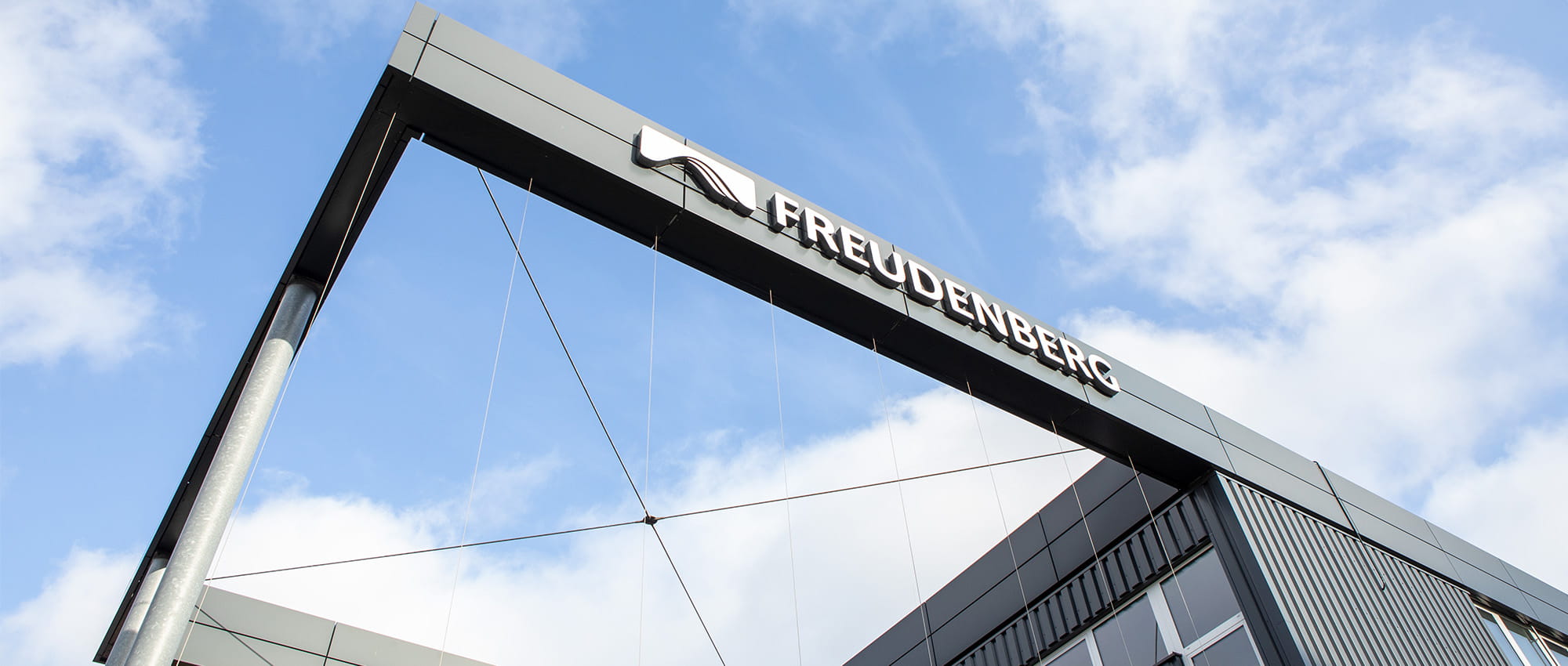
18.04.2022
No More Drafts
The project involved ventilation in the production area. The point of entry for the air supply was in the warm layers of air in the upper portion of the building. That was why it had to be infused with cold, 18 °C (64 °F) air to bring the overall temperature to less than 25 °C (77 °F) at the floor. According to Production Manager Jörn Weber, regulating the air temperature was tied to very high energy consumption, especially during the summer. The airflow posed problems from an ergonomic standpoint as well: The climate control system blew cold air into the production area from elevated metal baskets, nearly directly onto employees below, exposing them to continual drafts. The system, using a mix of ventilation to introduce fresh air and expel old air, blended clean and stale air.
To create a solution, the team in Berlin, Germany shifted the air feed to a lower area of the interior space (layer ventilation). The stiff steel baskets that were part of the system were replaced with flexible textile hoses. They now blow the cold air close to the floor. The layers of air do not mix, and there is now draft-free cooling in the work area. This approach also makes it possible to increase the air intake temperature, reducing energy consumption. Since the textile hoses can be easily moved around, they are not a hindrance in the work and transport areas.
The project has paid off in a number of ways: Reports of illness are on the decline, and air quality has improved. The plant’s energy costs are noticeably lower. The two-degree increase in the air intake temperature alone has reduced electric power consumption during the summer months by an average of 20,000 kWh a month. The investment will pay for itself within two-and-one-half years.
Another bonus: The system can be easily carried over to other locations. It is already proving to be a success at the Berlin, Germany mixing plant.
More Stories About Sustainability
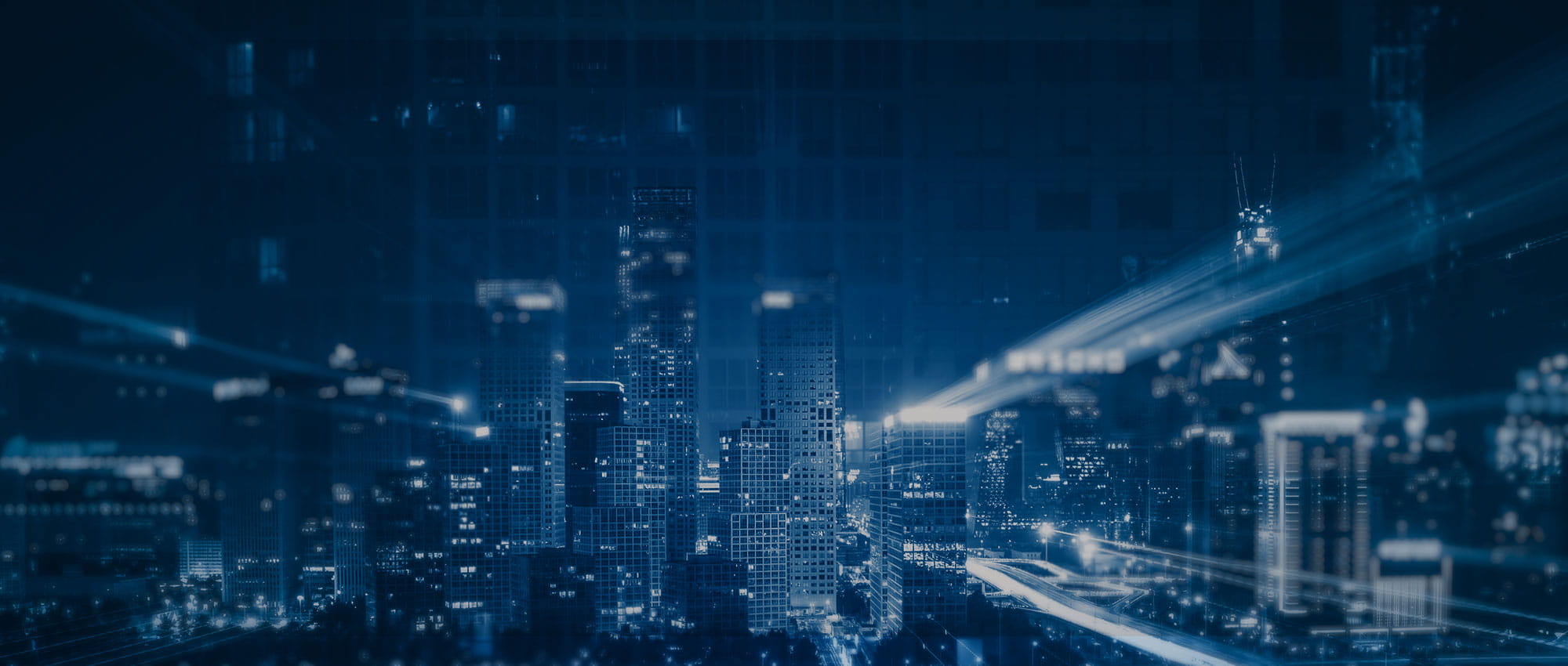
Join Us!
Experience Freudenberg Sealing Technologies, its products and service offerings in text and videos, network with colleagues and stakeholders, and make valuable business contacts.
Connect on LinkedIn! open_in_new