Obtain news and background information about sealing technology, get in touch with innovative products – subscribe to the free e-mail newsletter.
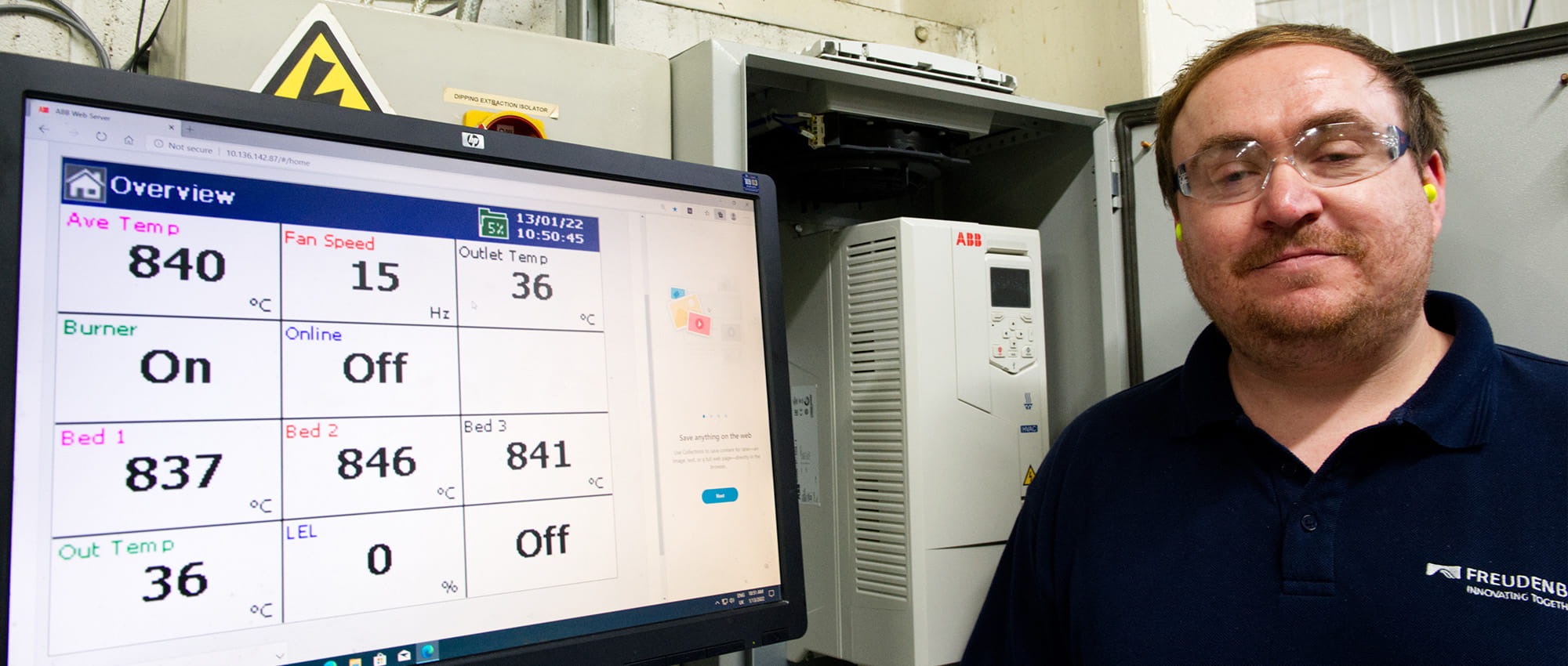
18.04.2022 | News
Trending Downward
Using a wide range of measures, the North Shields facility of the Fluid Power Division in England has greatly reduced its CO₂ footprint. Natural gas consumption for heating has fallen by nearly two-thirds during the past seven years, and electricity use has declined more than half during the same period. Water consumption was cut in half in three years.
Hot air rises. That’s something you learn in physics class. When high-ceiling rooms and factory halls are heated, the hot air produced at great expense with a great deal of energy ends up under the ceiling – where it doesn’t do any good.
So-called destratification fans redirect the air to the work areas and equalize the air temperature, even as they limit heat l loss through the roof. In short, the fans help to conserve heating energy – and save money. At Freudenberg Sealing Technologies (FST) Lead Center Damper and Steering (Fluid Power Division) in North Shields, “air mixers” are one of the plant’s tried-and-tested recipes for sustainability. In the winter, they help to reduce energy consumption, minimizing its CO2 footprint. In the summer, efficient roof ventilators draw off warm air, reducing the need for air-conditioning.
Conserving Energy Systematically
Facilities can only save energy systematically if they continually track and analyze consumption. This has proven true for North Shields thanks to its energy monitoring system, which makes it possible to identify waste and optimize machine settings.
The English site has also proven that “every little bit helps.” The efforts may involve replacing energy-intensive floodlights or fluorescent bulbs with modern lighting technology, and even reducing the number of lights based on a needs analysis. At North Shields, sensors make sure that lights are only activated when actually needed. Other factors that are key to the sustainability of North Shields’ operations are the optimization of existing installations or their replacement with high-performing, energy-consuming technologies – for example, modern condensation boilers for heating. Due to the many measures, the facility’s energy use, as measured in kilowatts per manufactured part, was significantly lower in 2021 than during previous years and even below the targets.
North Shields is considering the use of heat pumps in the future. To keep work areas comfortably warm and produce a supply of hot water, the pumps extract heat from the environment – instead of generating it from natural gas, a fossil fuel. The plant is also considering the use of warm exhaust air from compressors for heating and the replacement of its thermal oxidation technology with a biological approach. The use of photovoltaics to generate heat and the purchase of “green” electricity are also on the agenda.
More Stories About Sustainability
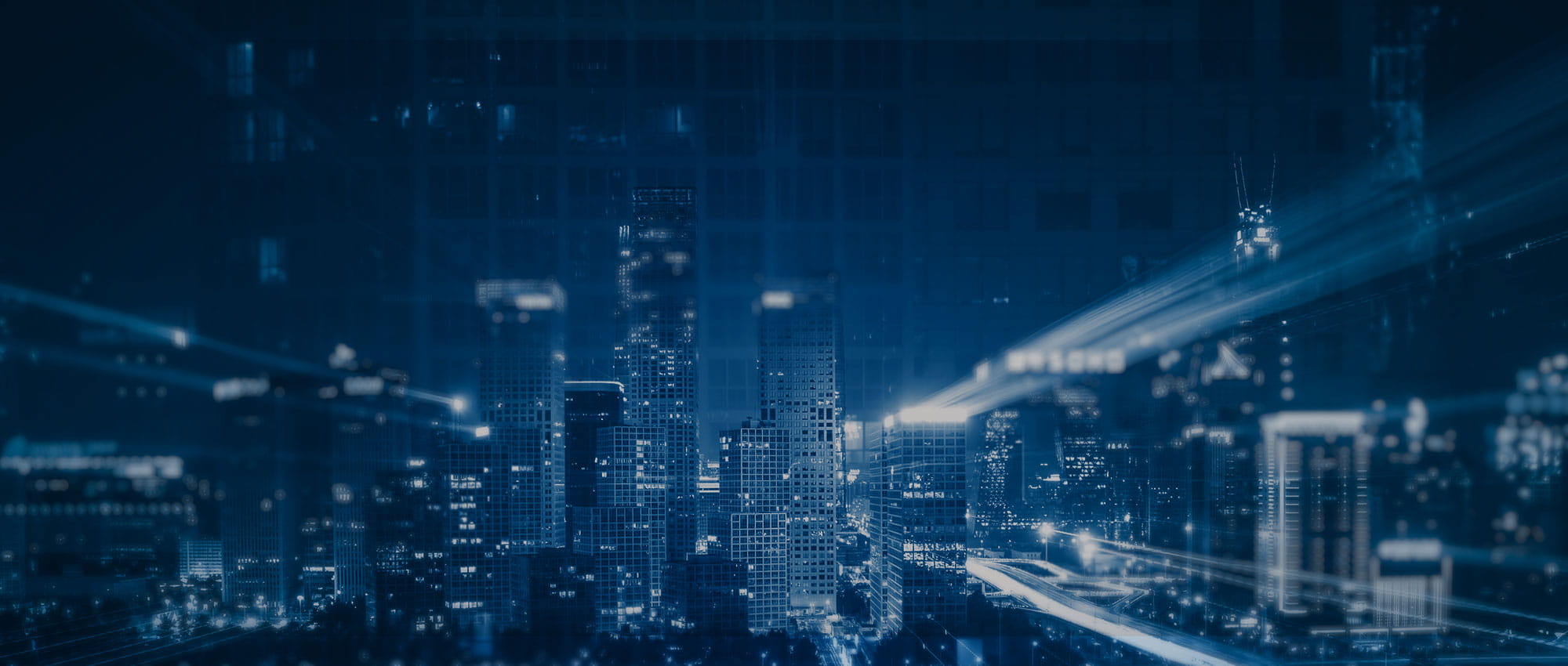
Join Us!
Experience Freudenberg Sealing Technologies, its products and service offerings in text and videos, network with colleagues and stakeholders, and make valuable business contacts.
Connect on LinkedIn! open_in_new