Obtain news and background information about sealing technology, get in touch with innovative products – subscribe to the free e-mail newsletter.
20.07.2021
From Manufactory To Gigafactory
The global production capacity for green hydrogen could increase to more than 250 gigawatts by 2030, according to a study by the International Renewable Energy Agency (IRENA). The technologies needed to split water by using green power – experts are calling this “electrolysis” – are already well-advanced. Experts believe that membrane electrolysis, which in principle works like a fuel cell in reverse, is particularly suitable for intermittent production with a highly fluctuating power supply. However, similar to the established process of alkaline electrolysis, systems for polymer membrane electrolysis so far have only been built in small quantities. Series production has only become attractive with the increased climate protection plans in China, Europe and the United States. By now, the first manufacturers are planning “gigafactories” where electrolyzers with a high degree of automation can be built at significantly lower costs.
Component Size Is a Challenge
This kind of production concept, however, requires components that are designed for mostly automated assemblies from the start. This applies especially to seals which provide reliable media separation during the electrolysis. The component size itself is one of the challenges: In some cases, seals with a diameter of up to one meter are used. Not only does this make the seals more difficult to handle, it also places high demands on the installation quality to ensure that the surface pressure is uniform and the tightness is guaranteed for the entire service life.
One of the solutions pursued by Freudenberg Sealing Technologies is based on molding the sealing material directly onto the functional part. The company is already using a similar process to produce gas diffusion layers in fuel cells. Alternatively, the seal can be applied to or inserted into specialized carriers, which in turn is easy to transport and install. “In principle, we face similar challenges as when we seal large battery housings in electric vehicles,” explains Technical Director Gaskets, Robert Lidster. “That’s why we can transfer our expertise to the electrolyzer market.” Through its work on fuel cell components, Freudenberg has also gained more than 20 years of experience in handling hydrogen. At its Munich development center in Germany, the company is even developing complete fuel cell systems now for use in commercial vehicles and ships.
Individual Development, Standardized Production
“There is no catch-all solution yet, regardless of how the electrolyzer is designed,” explains Global Segment Manager Hydrogen Technologies, Artur Maehne. “That’s why we always offer individual seal development to our customers for their specific systems.” To this end, Freudenberg experts have developed materials with very low permeability for hydrogen. These include special rubbers based on EPDM or fluoroelastomers (FKM). Extensive testing of the materials against aggressive media combinations in electrolysis is underway. For polymer membrane electrolysis, materials that promise a long service life of over 50,000 operating hours are already available.
Once a customer-specific solution has been found, Freudenberg Sealing Technologies’ plants can produce it in high quantities according to globalized standards. “This way we are helping the industry move from the manufacturing stage to mass production,” says Maehne.
Ulrike Reich
Head of Media Relations & Internal Communications
Telephone: + 49 (0) 6201 960 5713
ulrike.reich@fst.com chevron_rightDownload Press Release
News Service
You can subscribe to the Freudenberg Sealing Technologies news alert service, bringing you the news as soon as they are published. You can always unsubscribe from this service.
Subscribe now! chevron_rightFurther Articles With These Taggings
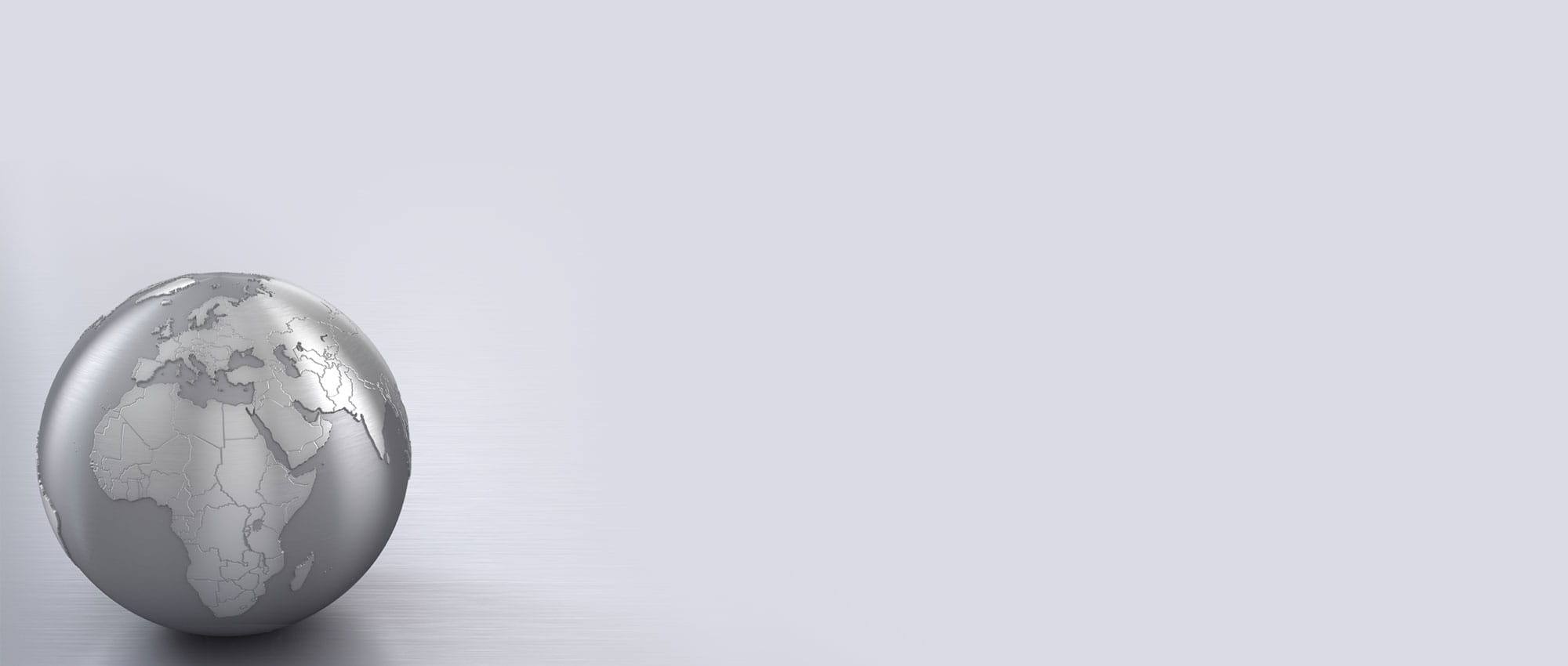
First Hand News
Best of all, keep up with the latest developments
with the Freudenberg Sealing Technologies newsletter.