Neuigkeiten und Hintergründe aus der Dichtungstechnik erfahren, innovative Produkte kennenlernen – im kostenlosen E-Mail-Newsletter von Freudenberg Sealing Technologies.
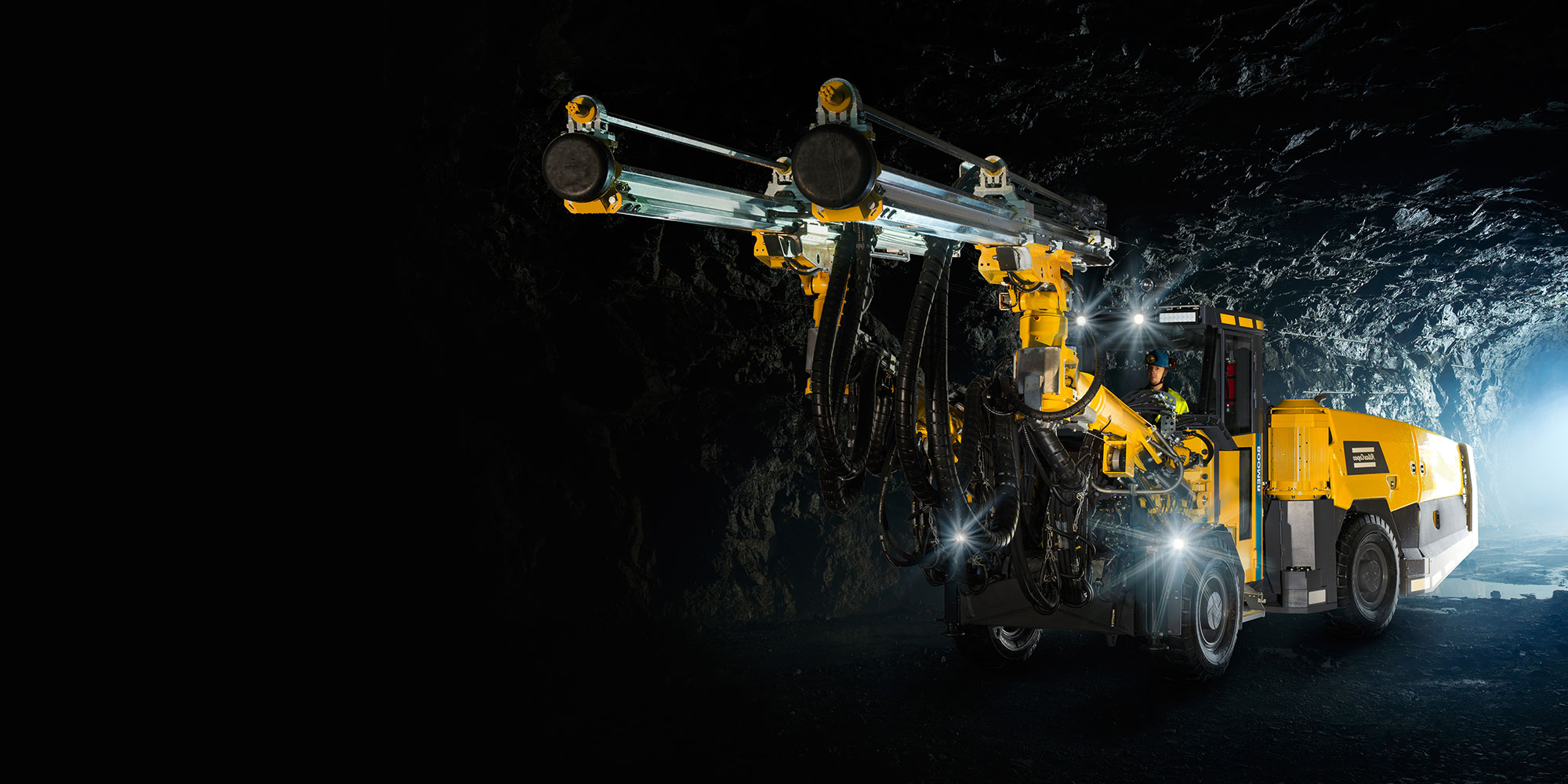
Rohe Kräfte, geeignete Dichtung
In der Bauindustrie eingesetzte Maschinen sollen langlebig sein und seltener gewartet werden müssen. Ein Ansatzpunkt: Effiziente Dichtungssysteme.
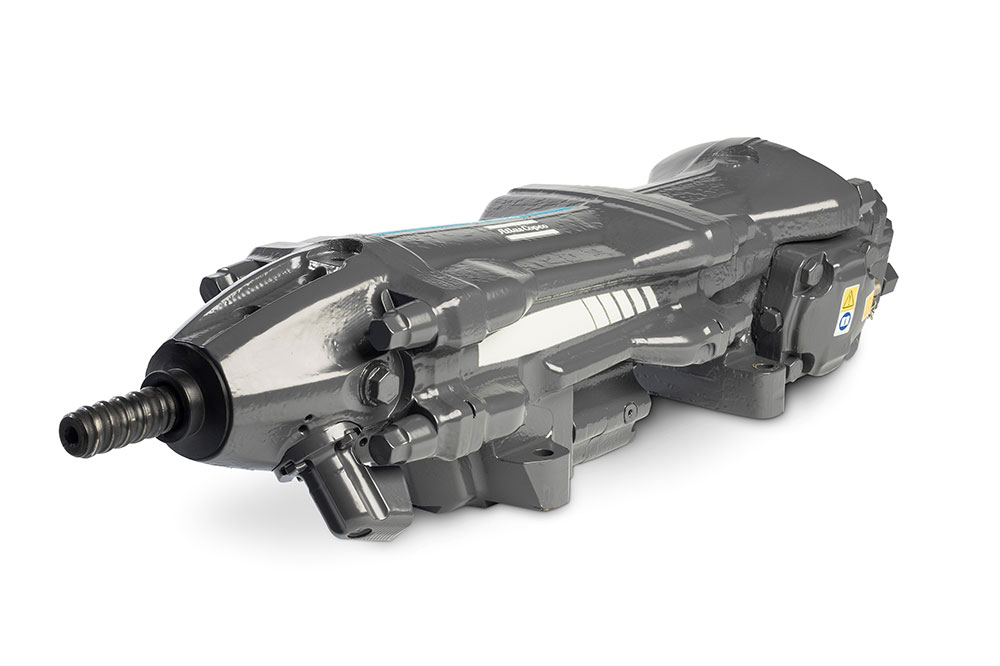
Das Ziel: Verdoppelung der Wartungsintervalle
Die Bohrmeißel der Maschinen von Atlas Copco schlagen bis zu 140 Mal in der Sekunde auf das Gestein. Die Wucht die dabei punktgenau wirkt, entspricht in etwa 25 Tonnen. Bei solch brachialer Kraft ist der Verschleiß vorprogrammiert. Die Maschinen mussten deshalb alle 400 Betriebsstunden generalüberholt werden. Für die Abnehmer der Generalbohrhämmer bedeutete das einen temporären Ausfall der Maschine, Wartungskosten inklusive. Atlas Copco reagierte und verfolgte seit einigen Jahren ein ehrgeiziges Ziel: Die Wartungsintervalle sollten auf über 1.000 Betriebsstunden nach oben geschraubt werden. Eine Maschine könnte so mehr als ein Jahr im Einsatz sein, ohne gewartet werden zu müssen.
Die Analyse: Auswerten der Schäden
Ein wichtiges Puzzleteil zur Verlängerung des wartungsfreien Zeitraums waren die Dichtungen. Sind sie beschädigt, dann vermindert sich zunehmend die Kraft, die der Bohrer entfalten kann. Ein Problem, dessen sich die Dichtungsexperten von Freudenberg Sealing Technologies annahmen. Gunnar Pettersson betreut im Vertrieb die skandinavischen Kunden und begleitete die Suche nach einer Lösung: „Die Ingenieure von Atlas Copco und unsere Entwickler haben alle im Betrieb auftretenden Schäden gemeinsam analysiert. Erst dadurch haben wir die harten Einsatzbedingungen genau verstanden und konnten Abhilfe schaffen.“
Es war richtig, sich nicht zu verzetteln, sondern sich mit aller Kraft um eine einzige erfolgskritische Komponente zu kümmern.
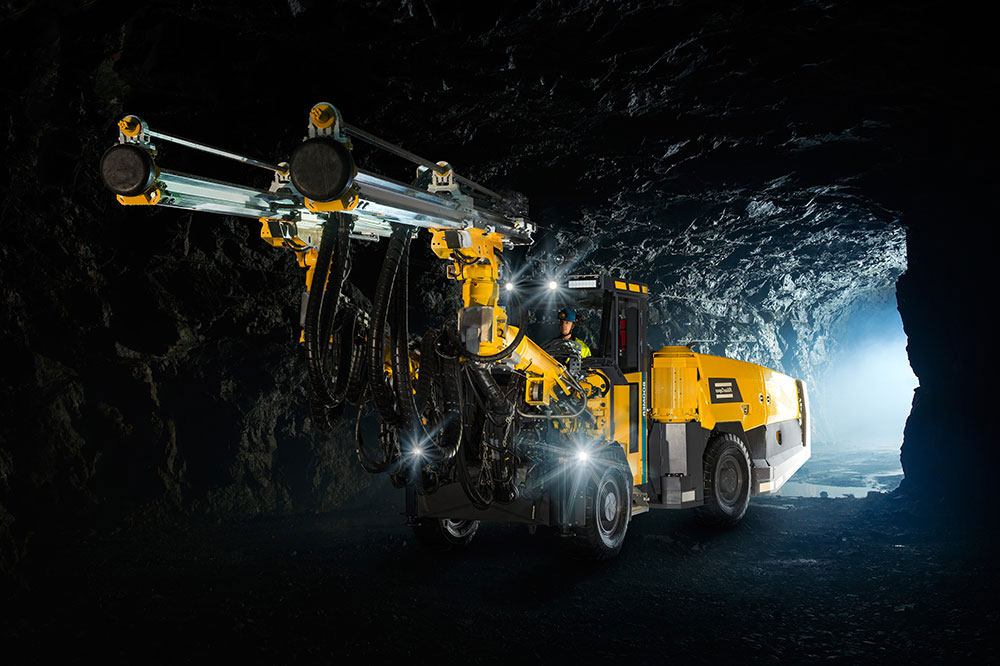
Die Lösung: Neukonzeption der Dichtung
Insbesondere auf dem Kolben, der den Bohrmeißel antreibt, lag ein Augenmerk aller Beteiligten. Der der Kolben bewegt sich nicht zur vor und zurück, sondern rotiert zugleich ein wenig um die eigene Achse. Eine enorme Belastung für den Meißel, aber auch für das Dichtungssystem. „Unsere Analyse hat uns selbst überrascht“, gibt Pettersson zu. „Die Dichtung dreht sich relativ beständig mit 300 bis 400 Umdrehungen in der Minute.“ Sie musste deshalb grundlegend überdacht werden. Neben einer veränderten Zusammenstellung des Materials überarbeitete Freudenberg Sealing Technologies auch die Konstruktion der zu verwendeten Dichtung. Mit Erfolg: Die Dichtung hielt, was sich alle von ihr versprachen. Das zeigten sowohl die Tests im Prüfstand von Atlas Copco, als auch der Einsatz unter Praxisbedingungen. Über ein Jahr musste sich die neue Maschine mit der eigens angefertigten Dichtung unter Tage beweisen. Für Pettersson war es richtig, „sich nicht zu verzetteln, sondern sich mit aller Kraft um eine einzige erfolgskritische Komponente zu kümmern.“ Inzwischen ist die Maschine auf dem Markt und kommt bereits in Minen zum Einsatz.
Weitere verwandte Artikel
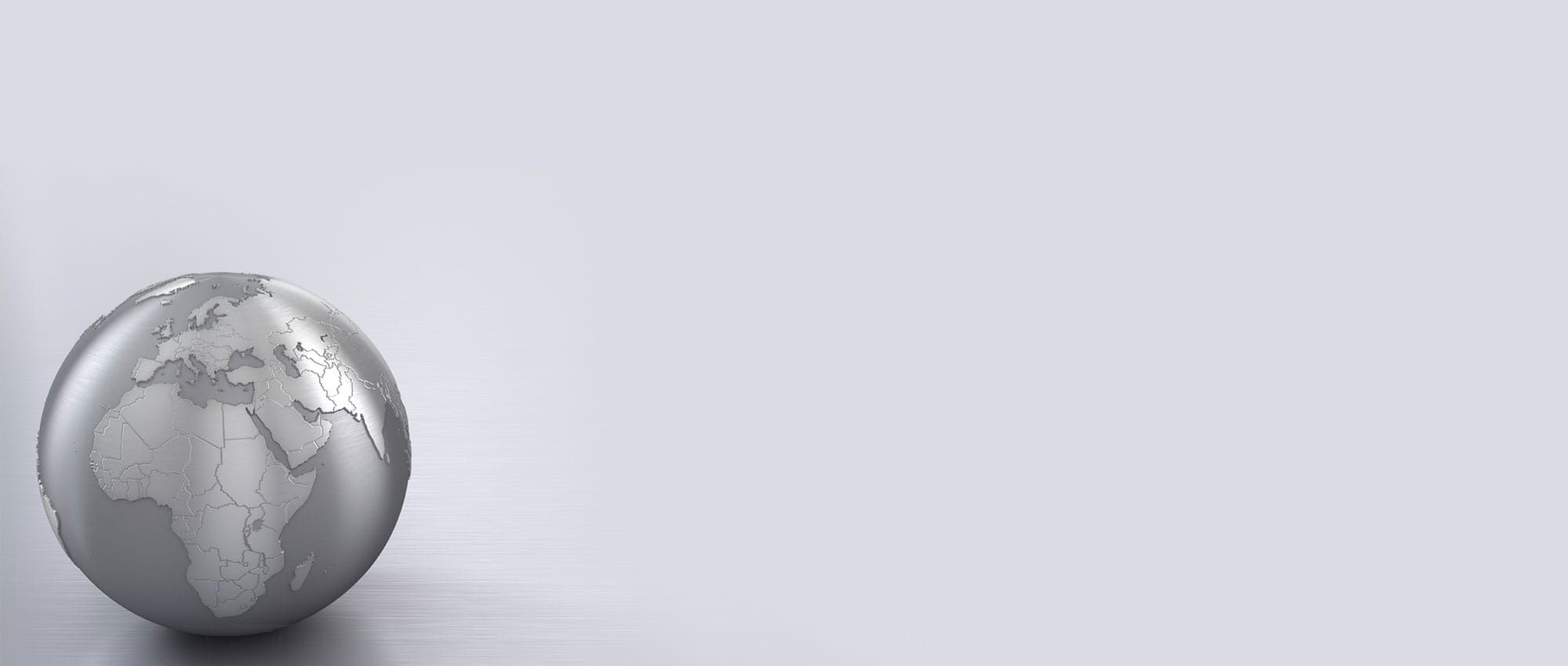
Immer informiert
Auf dem Laufenden bleiben:
Mit dem Newsletter von Freudenberg Sealing Technologies.