Neuigkeiten und Hintergründe aus der Dichtungstechnik erfahren, innovative Produkte kennenlernen – im kostenlosen E-Mail-Newsletter von Freudenberg Sealing Technologies.
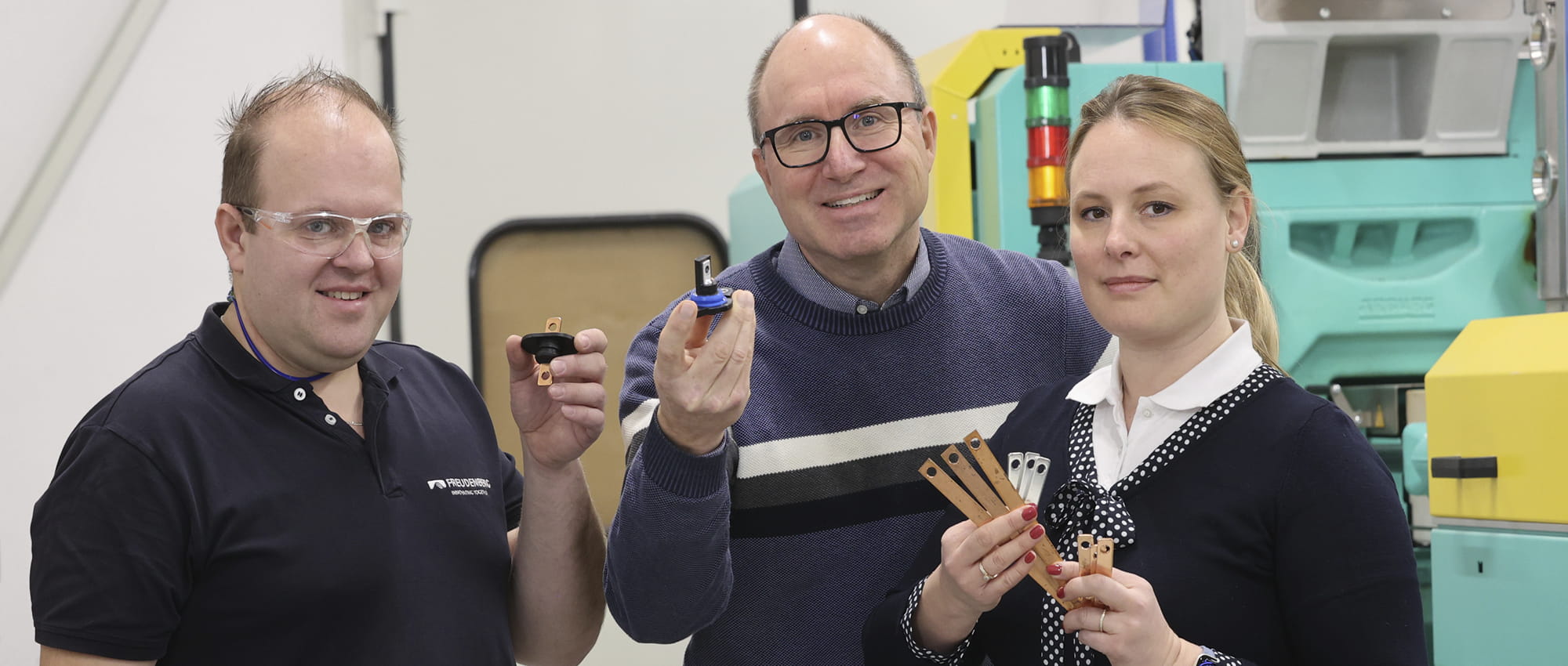
Innovative Dichtungslösung für Busbars
Stromschienen aus Kupfer oder Aluminium werden in allen Elektrofahrzeugen verbaut. Die Busbars genannten Komponenten garantieren den Stromfluss in der Antriebstechnik. Das rechteckige Design der Busbars erschwerte bislang das zuverlässige Abdichten. Jetzt hat Freudenberg Sealing Technologies eine ebenso überzeugende wie gefragte Lösung gefunden, auch für hohe Fertigungsstückzahlen.
Was die Kunststoff- und Dichtungsexperten von Freudenberg Sealing Technologies zuletzt entwickelt haben, hört sich ein wenig nach der Quadratur des Kreises an. Sie haben eine Dichtungslösung entwickelt, die rechteckige Stromschienen aus Kupfer oder Aluminium, auch Busbars genannt, chemisch verbunden absolut sicher umschließt. Auf diese Weise verhindert die Dichtung verlässlich das Eindringen jeglicher Flüssigkeiten entlang der Busbars in sensible Bereiche, zum Beispiel in die Leistungselektronik von E-Autos.
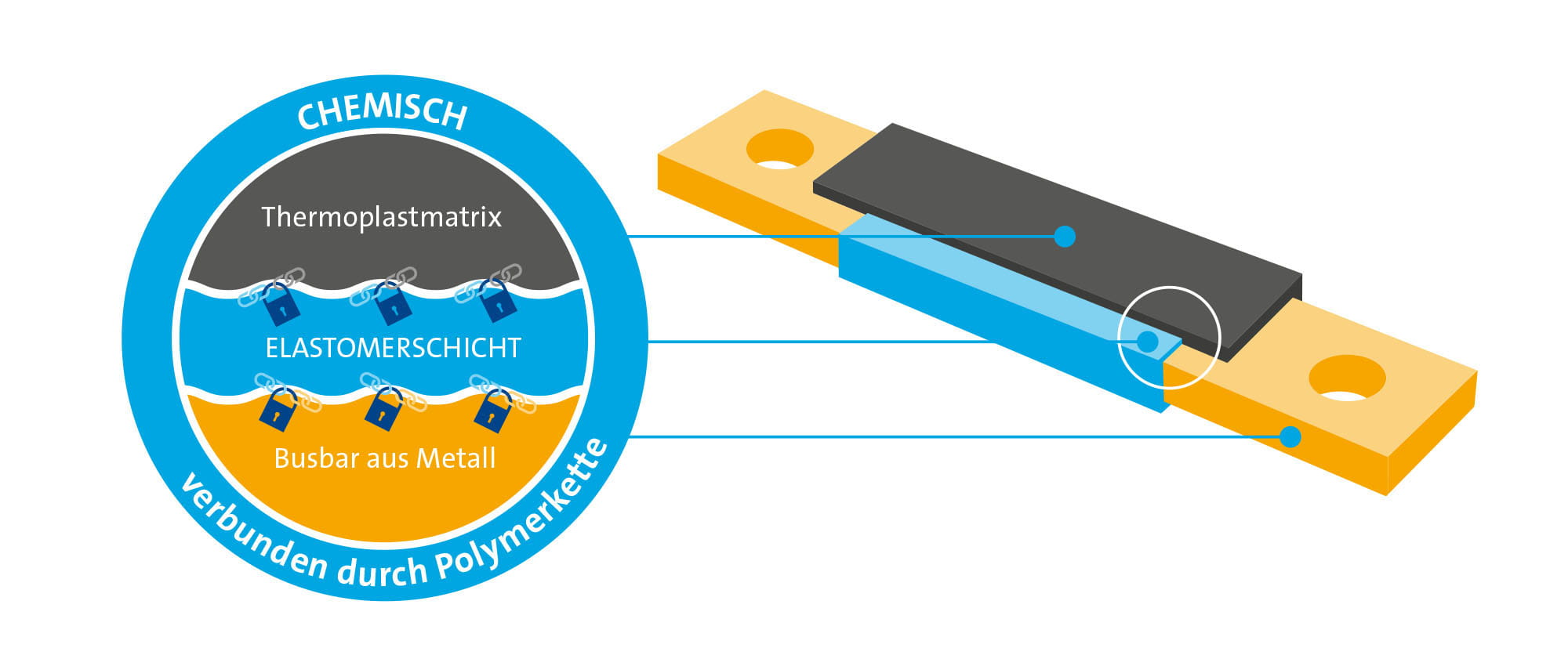
Doch warum sind rechteckige Querschnitte eigentlich so schwer abzudichten? „Insbesondere die Ecken bereiten konventionellen Dichtungen Probleme“, sagt Parisa Burger, Business Development Manager aus dem Busbar Incubation Team bei Freudenberg Sealing Technologies. „Denn sie erschweren eine gleichmäßige Kompression des Dichtungswerkstoffs an die abzudichtende Oberfläche, weshalb die Stelle anfällig für Leckagen bleibt.“ Umso mehr bei einer Abdichtung von Kupfer, das sich beim Stromtransport erwärmt und damit ausdehnt, nur um sich beim Erkalten wieder zusammenzuziehen. Dieses Ausdehnen und Zusammenziehen – in der Fachsprache „Wärmeausdehnungskoeffizient“ genannt - erfolgt bei Kupfer schneller als bei Kunststoff oder Elastomeren. Deshalb kriechen Flüssigkeiten langsam zwischen Kupfer und Kunststoff entlang und führen so zu einer Leckage.
Busbars transportieren und verteilen Strom
Busbars haben sich inzwischen in vielen Anwendungen und verschiedenen Industrien bewährt. Die rechteckigen Stromschienen beziehungsweise stromführenden Leiter sind überall relevant, wo eine hohe Stromstärke fließen muss. Auch in der Elektromobilität sind sie für den Transport und die Verteilung von Energie zuständig. In E-Fahrzeugen werden sie deshalb an zahlreichen Stellen verbaut: im Ladesystem, im Batteriemanagementsystem, in der Leistungselektronik und auch im elektrischen Antriebsstrang. Je nach Einsatzgebiet variieren sie in Länge und Querschnitt. Die meisten Busbars finden sich in kompakter Ausführung in der Antriebsbatterie. Im Gegensatz zu isolierten Kupferkabeln haben Busbars geometrische Vorteile. „Darüber hinaus sind sie robust, leichter zu fertigen und damit wettbewerbsfähiger“, sagt Marco Sutter, Global Market Segment Manager bei Freudenberg Sealing Technologies.
Nun verfügen viele Elektroautos über ölgekühlte Elektromotoren. Die sensible Leistungselektronik des Inverters muss deshalb vor eindringendem Öl aus dem E-Motor geschützt sein. Um dies sicherzustellen, bedarf es einer effizienten Dichtungslösung für das Busbar-Modul, bei dem die Kupferschiene von einem Kunststoffgehäuse aus Thermoplast umschlossen wird. Die Aufgabe der Dichtung ist es, den Spalt zwischen Kupfer und Kunststoff zuverlässig zu schließen. Bislang gab es keine restlos überzeugenden Lösungen am Markt. „Rund gestaltete Busbardurchführungen verschlingen mehr Platz und sind teurer“, weiß Parisa Burger. Auch das Potting, bei dem eine Masse wie zähflüssiger Kleber um den Busbar herum aufgebracht wird, ist nicht ideal. Denn es beeinflusst die Designgebung und bietet dennoch keinen hundertprozentigen Leckage-Schutz. „Letztlich stellen alle bisherigen Ansätze am Markt lediglich Bastel-Lösungen dar“, verdeutlicht die Managerin.
Cooling & Flame Protection
Freudenberg Sealing Technologies bietet für Busbars in Elektrofahrzeugen nicht nur Dichtungslösungen an. Bestimmte Busbar-Abschnitte lassen sich auch mit Materialien ummanteln, die entweder kühlende oder flammschützende Eigenschaften besitzen. Hitzeabführende Elastomere verhindern beispielsweise zu heiße Stromschienen, die sonst die Leistungselektronik oder andere elektrische Komponenten schädigen würden. Spezielle Flammschutzwerkstoffe wie etwa das Thermoplast Quantix® ULTRA, sorgen wiederum dafür, dass die Busbars in einer Batterie Flammen standhalten und im Falle eines Brandes weiterhin isolieren.
Individuelle Lösung: Freudenberg Sealing Technologies stellt die Busbar-Module mit der integrierten Dichtung so her, wie es die Fahrzeugherstellern vorgeben. So könnten diese die Busbars genauso führen und verbauen, wie es ihren Designvorgaben entspricht.
Freudenberg kreiert völlig neuen Lösungsansatz
Freudenberg Sealing Technologies hatte das Problem erkannt und ist es in den letzten Jahren von Grund auf angegangen. Ein interdisziplinäres Team aus Materialentwicklern und Prozessfachleuten setzte sich mit den Erkenntnissen auseinander, die es aus dem Vertriebsteam erhalten hatte, und wählte einen anderen Lösungsansatz. „Unser Vorteil ist, dass wir seit langem darin geübt sind, Gummi sowohl an Metall als auch an Kunststoff chemisch anzubinden“, erklärt Parisa Burger. „Um die Busbar-Module abzudichten, hatten unsere Chemiker die Idee, eine Elastomer-Dichtung zu entwickeln, die auf der einen Seite mit dem Kupfer und auf der anderen Seite mit dem Kunststoffgehäuse – man könnte sagen – verschmilzt. Alle drei Komponenten werden so stoffschlüssig verbunden und damit letztlich zu einer undurchdringlichen Einheit.“ Die Idee nahm Gestalt an und ist inzwischen ausgereift.
Die Lösung basiert auf der Verwendung vulkanisierbarer Hochleistungselastomere als abdichtende Gummischicht, die sich mit den beiden anderen Materialien stoffschlüssig verbindet. „Bei den Elastomeren bedienen wir uns aus unserem reichhaltigen Werkstoff-Baukasten“, erläutert Marco Sutter. „Je nachdem, gegen welche Flüssigkeiten das Modul abzudichten ist, und welche Temperaturen und Druckverhältnisse herrschen, suchen wir den passenden Werkstoff aus.“ Durch ein neuartiges Verfahren wird der erwünschte Stoffschluss per Reaktion erzeugt. Das Ergebnis kann man sich wie eine Kette mit zusammengeschweißten Kettengliedern vorstellen. „Dabei verbinden sich die Molekülketten des abdichtenden Gummis mit dem Kupfer auf der einen und mit dem Kunststoffgehäuse auf der anderen Seite. Sie werden gewissermaßen zu einem Teil, was das Eindringen von Flüssigkeiten unmöglich macht“, weiß Parisa Burger. „Indem wir keine mechanische Verbindung herstellen, wie es bei klassischen Dichtungen üblich ist, sondern eine chemische Verbindung der Komponenten herbeiführen, haben wir ein wirklich revolutionäres Verfahren entwickelt“, unterstreicht sie.
Unsere Kunden bekommen ein völlig auf sie zugeschnittenes Busbar-Modul, das sowohl technisch als auch wirtschaftlich die beste Lösung darstellt.
Katinka Raschke, Busbar Incubation Team bei Freudenberg Sealing Technologies
Keinerlei Design-Einschränkungen
Die „mediendichte Umspritzung von rechteckigen Busbars“ ist eine ebenso faszinierende wie überzeugende Innovation. Bei der Herstellung der Busbar-Module für Elektrofahrzeuge geht das eigens dafür zuständige Busbar Incubation Team bei Freudenberg Sealing Technologies auf die Vorgaben der Fahrzeughersteller ein. So bleibt gewährleistet, dass die Autobauer die Busbars genauso führen und verbauen können, wie es ihren Designvorgaben entspricht. Die integrierte Freudenberg-Dichtung ist dabei kein limitierender Faktor, da sie keinen zusätzlichen Raum einnimmt. Auch der vom Kunden gewünschte Kunststoff wird bei der Realisierung der Module berücksichtigt. Am Ende beziehen die Kunden das gesamte Busbar-Modul von Freudenberg Sealing Technologies. „Unsere Kunden bekommen ein völlig auf sie zugeschnittenes Modul, das sowohl technisch als auch wirtschaftlich die beste Lösung darstellt“, betont Katinka Raschke aus dem Busbar Incubation Team.
Inzwischen sind mehrere Hersteller von Elektrofahrzeugen auf die innovative Dichtungslösung aufmerksam geworden. Derzeit befindet sich Freudenberg Sealing Technologies mit mehreren Kunden in der Prototypenphase und führt Validierungstests durch. Parisa Burger und Katinka Raschke blicken deshalb gemeinsam mit ihrem Team optimistisch in die Zukunft: „Wir sind sehr zuversichtlich, dass unsere Dichtungsinnovation schon bald in den ersten Fahrzeugmodellen in Serie gehen wird.“
Dieser Beitrag stammt aus unserem Unternehmensmagazin „ESSENTIAL“, in dem wir kontinuierlich über Trends und Schwerpunktthemen aus unseren Zielindustrien und -märkten berichten. Weitere Beiträge des Magazins finden Sie hier.
Weitere Storys zum Thema E-Mobilität
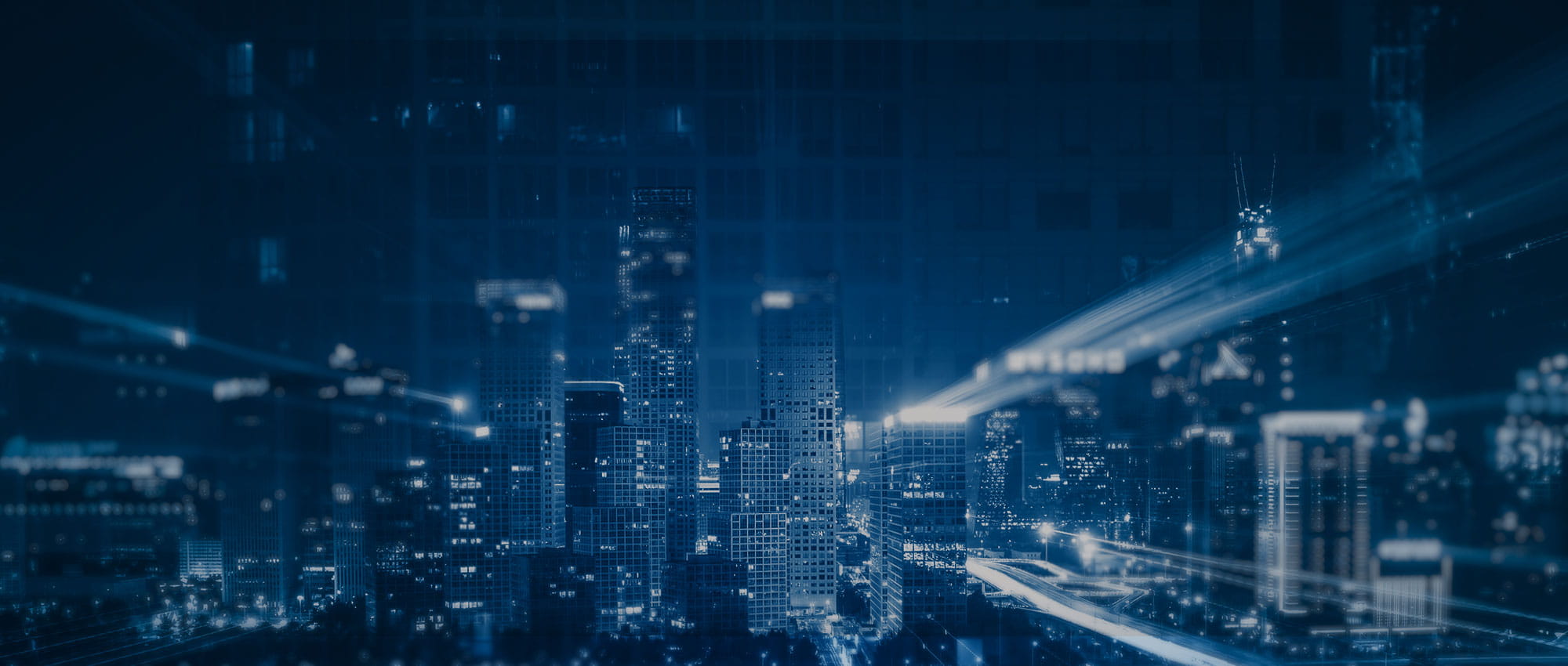
Join Us!
Freudenberg Sealing Technologies, seine Produkte und Serviceangebote in Wort und bewegten Bildern erleben, sich mit Mitarbeitenden und Stakeholdern vernetzen und dabei wertvolle geschäftliche Kontakte knüpfen.
Auf LinkedIn vernetzen! open_in_new