Neuigkeiten und Hintergründe aus der Dichtungstechnik erfahren, innovative Produkte kennenlernen – im kostenlosen E-Mail-Newsletter von Freudenberg Sealing Technologies.
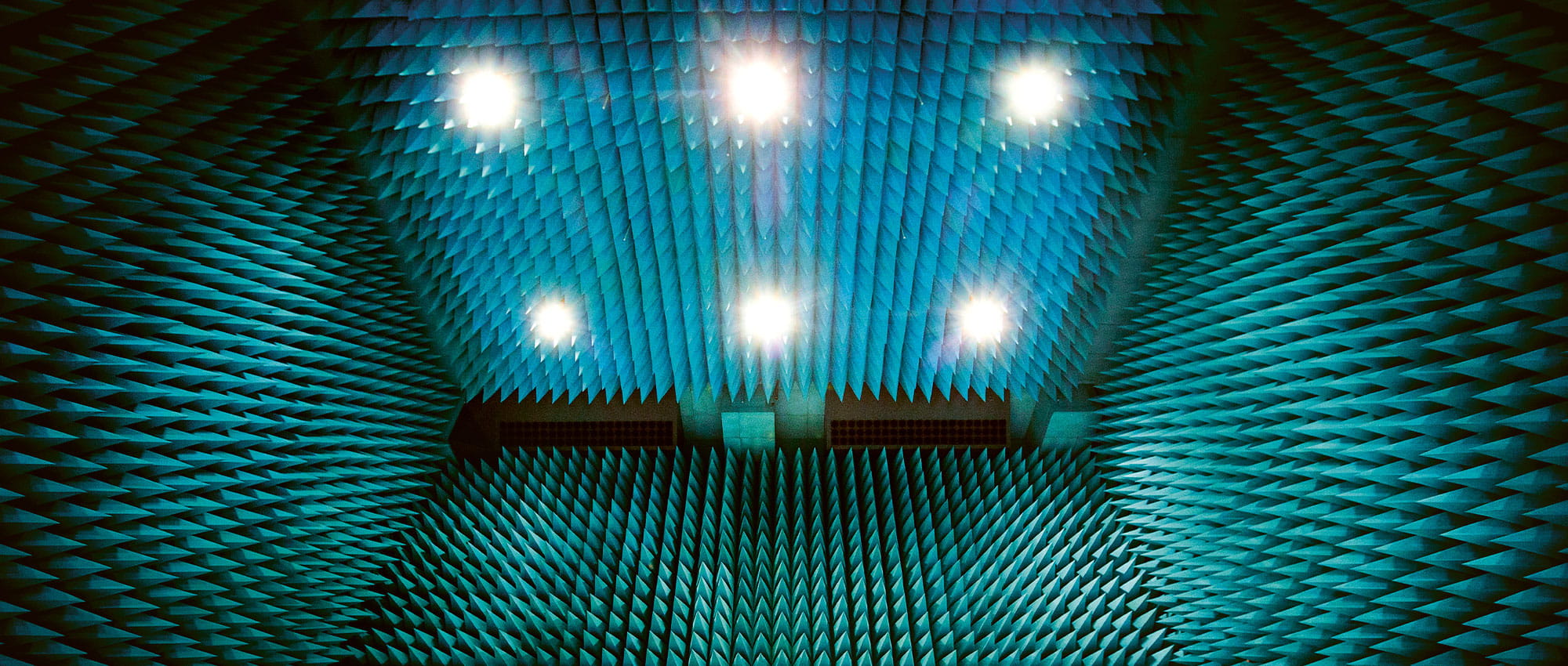
Ungestörte Leichtigkeit
Kunststoffe können nicht nur isolieren, sondern auch Strom leiten. Wer braucht so etwas? Zum Beispiel das Elektroauto der Zukunft. Mithilfe von Spezialkunststoffen und Beschichtungen von Freudenberg Sealing Technologies kann es einige überflüssige Pfunde verlieren.
Wo Strom fließt, da entstehen immer auch elektrische und magnetische Felder. Im Elektroantrieb fließt der Strom allerdings – außer bei bestimmten Ladevorgängen – selten kontinuierlich in eine Richtung. Die Leistungselektronik peitscht Wechselstrom mit hohen Frequenzen in die Adern des Elektromotors, der – je nach Bauart – mit Frequenzen von bis zu 30.000 Umdrehungen pro Minute arbeitet. Entsprechend schnell wechseln die Feldstärken und erzeugen dabei elektromagnetische Wellen, die sich mit Lichtgeschwindigkeit durch den Raum bewegen. Würden sie nicht gestoppt, käme es vor allem in der Vielzahl von Steuerungen an Bord zu Störungen, vielleicht sogar in dem Auto, das nebenan an derselben Ampel hält. Die einzig zuverlässige Waffe im Kampf gegen elektromagnetische Wellen besteht darin, elektrische Komponenten in ein Gehäuse einzusperren, das aus einem elektrisch und gegebenenfalls magnetisch leitenden Material gearbeitet ist oder dessen elektrisch leitfähige Oberfläche die Wellen reflektiert.
Für die Massenproduktion haben wir verschiedene kostengünstige Alternativen entwickelt.
Volker Schroiff, Leiter Technologiemanagement von Freudenberg Sealing Technologies
Kunststoff ersetzt Aluminium
In den Elektroautos der aktuellen Generation bestehen die Gehäuse für Akkus, Motoren und Leistungselektronik daher fast ausnahmslos aus Aluminium. Es ist einerseits ein guter Stromleiter, andererseits ein Leichtmetall mit niedrigem spezifischem Gewicht. Zudem lässt es sich im Druckguss gut verarbeiten und ist daher entsprechend kostengünstig. Den Ex¬perten von Freudenberg Sealing Technologies ist gut aber nicht gut genug. Denn jedes Kilo Hüftspeck geht beim Elektroauto auf die Reichweite. Könnte man die vielen Alubauteile durch Kunststoffe ersetzen, dann wären einige Dutzend Kilo zu gewinnen – entsprechend kleiner könnte der teure Akku sein. Die Hürde: Man braucht dafür einen elektrisch leitfähigen Kunststoff. Den gibt es zwar, das recht teure Material wird allerdings fast ausschließlich in der Elektronikfertigung, beispielsweise für Displays, eingesetzt.
Ein Ziel, mehrere Wege
„Auch für uns hat sich der Einsatz solch intrinsischer, also von sich aus leitfähiger Kunststoffe, als zu kostspielig erwiesen“, weiß Volker Schroiff, der das Technologiemanagement von Freudenberg Sealing Technologies leitet. „Für die Massenproduktion haben wir allerdings verschiedene Alternativen entwickelt, die deutlich kostengünstiger sind.“ Alternative eins besteht darin, ein Kunststoffgehäuse mit einer leitfähigen Beschichtung zu versehen. Aufgetragen wird sie ähnlich wie ein Lack. Schroiff arbeitet derzeit gemeinsam mit seinen Kollegen aus dem Geschäftsbereich Special Sealing am Konzept einer entsprechenden Anlage zur industriellen Umsetzung. Alternative zwei basiert auf der Idee, dem Kunststoff vor dem Spritzguss Partikel aus einem leitfähigen Material zuzugeben. Vorteil dieses Weges: In der Produktion sind keine zusätzlichen Prozessschritte notwendig, was besonders bei kleineren Bauteilen einen Kostenvorteil bieten kann. Und schließlich gibt es einen dritten Weg, der sich insbesondere für große Oberflächen – etwa den Gehäusedeckel einer Traktionsbatterie – eignet. Hierfür wird in der Herstellung ein Vlies, dessen Fasern zuvor eine elektrisch leitfähige Beschichtung erhalten haben, in das Werkzeug eingelegt, in dem ein Kunststoff-Bauteil produziert wird. „Bei dieser Lösung arbeiten wir eng mit den Vliesstoffexperten von Freudenberg Performance Materials zusammen“, erläutert Schroiff.
Ab einer Jahresproduktion von mindestens 30.000 Bauteilen haben die Spezialkunststoffe von Freudenberg Sealing Technologies gegenüber Aluminium Gewichts- und Kostenvorteile.
Erste Pilotprojekte mit drei großen Direktlieferanten von Elektroantrieben zeigen: Die aus der Physik des Elektromagnetismus abgeleiteten Ideen funktionieren auch in der Praxis an realen Bauteilen. Und ab einer Jahresproduktion von mindestens 30.000 Bauteilen haben die Spezialkunststoffe von Freudenberg Sealing Technologies gegenüber Aluminium einen Kostenvorteil. Derweil geht Schroiff schon wieder neue Wege. Künftig könnte die leitende Schicht auch aus einem hauchdünnen Elastomer bestehen, das im Zweikomponenten-Spritzgießverfahren gemeinsam mit dem Gehäuse in einem Werkzeug gefertigt würde. Das Elastomer dient dann nicht nur als Schutzschild gegen elektromagnetische Wellen, sondern auch zur Abdichtung gegen flüssige und gasförmige Medien.
Ein Kunststoff, der auch Magnetfelder abschirmt
Inzwischen haben sich Schroiff und sein Team einer weiteren Herausforderung von Elektrofahrzeugen gewidmet. Zahlreiche Kundengespräche haben die Experten für die notwendige Abschirmung gegen Magnetfelder im Kilohertzbereich sensibilisiert. Den Elektroantrieb umgebende Magnetfelder sind für den Menschen schädlich. Bislang stehen den Herstellern nur Behelfslösungen zur Verfügung, um diese einzudämmen. Auch Aluminium bietet hier keine vollständige Abhilfe. Warum also nicht auch hier eine kunststoffbasierte Lösung finden? „Mit unseren bisherigen Ansätzen kamen wir in dieser Hinsicht nicht weiter. Wir haben deshalb zur weiteren Analyse einen Prüfstand gebaut, um Lösungen für eine zuverlässige Abschirmung zu finden und zu testen“, erläutert Schroiff. Die Ergebnisse sind vielversprechend und wurden bereits OEMs vorgestellt. „Mit einer von uns entwickelten Hybrid-Technik sind wir der Lösung auf der Spur und haben das Interesse der Hersteller geweckt. Wir ergreifen nun die nächsten Schritte, denn unser Ziel lautet, einen Prototyp herzustellen“, blickt der Technologieexperte zuversichtlich voraus. Auf diese Weise würde Kunststoff elektrische und magnetische Felder im Zaum halten und somit zwei Fliegen mit einer Klappe schlagen.
Dieser Beitrag stammt aus unserem Unternehmensmagazin „ESSENTIAL“, in dem wir kontinuierlich über Trends und Schwerpunktthemen aus unseren Zielindustrien und -märkten berichten. Weitere Beiträge des Magazins finden Sie hier.
Weitere Storys zum Thema E-Mobilität
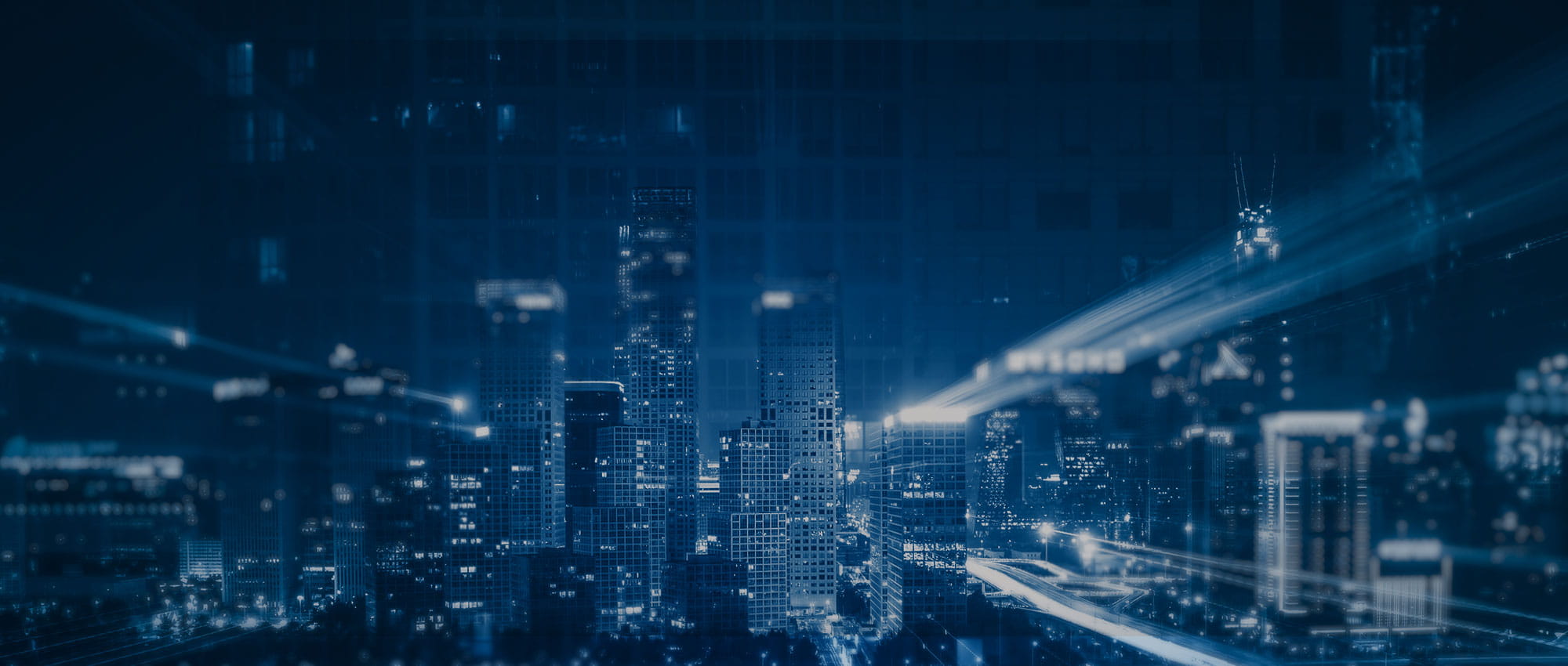
Join Us!
Freudenberg Sealing Technologies, seine Produkte und Serviceangebote in Wort und bewegten Bildern erleben, sich mit Mitarbeitenden und Stakeholdern vernetzen und dabei wertvolle geschäftliche Kontakte knüpfen.
Auf LinkedIn vernetzen! open_in_new