Neuigkeiten und Hintergründe aus der Dichtungstechnik erfahren, innovative Produkte kennenlernen – im kostenlosen E-Mail-Newsletter von Freudenberg Sealing Technologies.
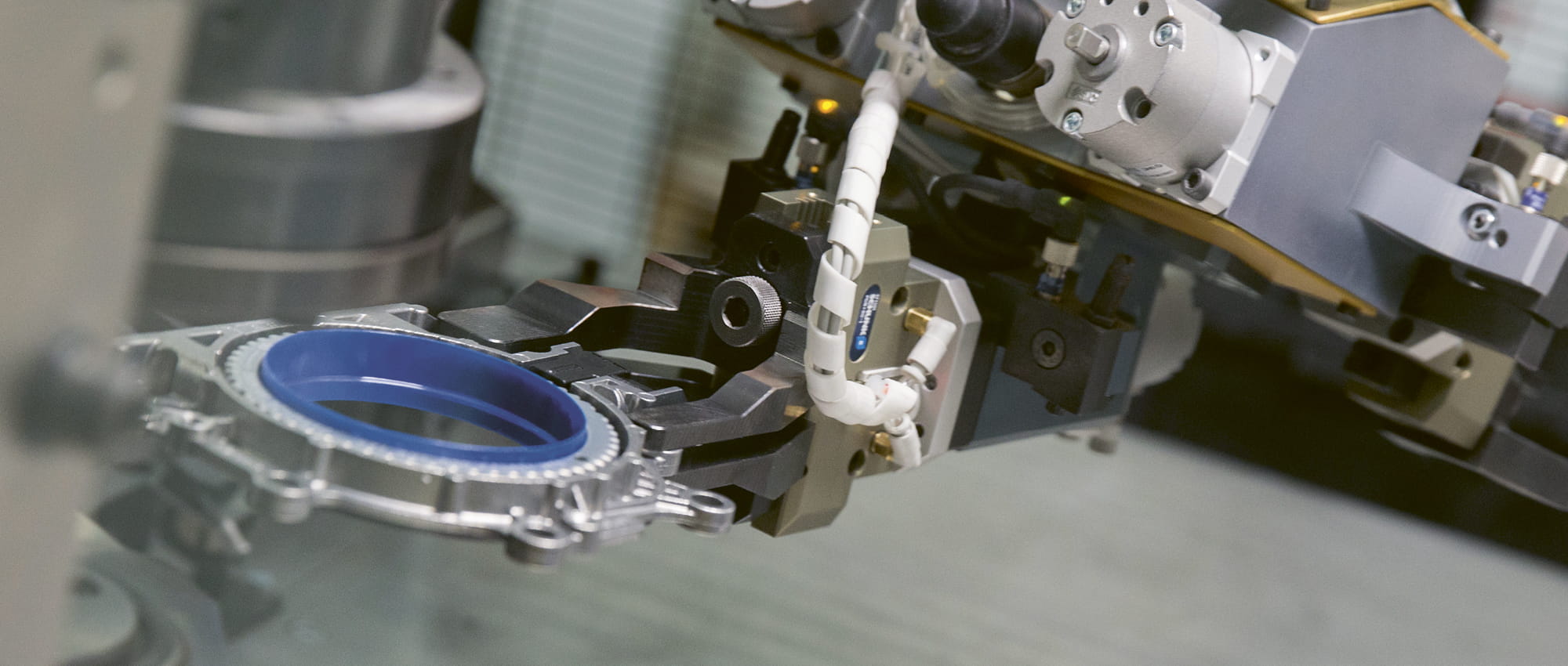
Reibungsloser Prozess
Mit seiner innovativen Levitex-Gleitringdichtung dichtet Freudenberg Sealing Technologies die Kurbelwelle nahezu reibungslos ab. Sie hilft den Kraftstoffverbrauch und die CO₂-Emissionen zu senken. Die Serienfertigung der Dichtung erfolgt im norditalienischen Werk Pinerolo. Wichtige Faktoren dabei: größtmögliche Automatisierung und integrierte Qualitätskontrollen.
Die kleine italienische Stadt Pinerolo im Winter. Im Südwesten erheben sich die Cottischen Alpen, der fast 4.000 Meter hohe Monte Viso schneebedeckt. Die Luft ist kalt und klar, und die Sonne scheint flach ins Tal. Auf dem Weg ins Piemonter Werk von Freudenberg Sealing Technologies heißt es aufzupassen, denn die Pfützen auf der Straße sind gefroren, und die Reifen verlieren immer wieder ihren Grip. Manchmal ist Reibung eben wichtig. Im Werk Pinerolo tragen die Freudenberg-Ingenieure jedoch dazu bei, Reibung zu vermeiden: nicht an den Reifen, sondern im Motorraum, am Übergang vom Motor zum Getriebe. Hier ist Reibung unerwünscht, weil sie wertvolles Drehmoment in verlorene Wärmeenergie umwandelt. Vor ein paar Jahren startete in Pinerolo die Serienproduktion für völlig reibungsfreie Dichtungen für die Kurbelwelle. Das wichtigste Ziel der Gleitringdichtungen mit dem Markennamen „Levitex“ liegt darin, den Kraftstoffverbrauch und die CO2-Emissionen von Fahrzeugen zu senken.
Von Pinerolo in die Welt
Sieben Arme: In der Produktionslinie kommen mehrere Roboter zum Einsatz, um die Herstellung weitgehend zu automatisieren.
Ende 2016 hat Freudenberg Sealing Technologies im Werk Pinerolo, wo ansonsten vor allem Ventilschaftdichtungen hergestellt werden, eine Produktionslinie für die Kleinserienfertigung der Levitex-Dichtungen in Betrieb genommen. Seitdem sind die Dichtungen gemeinsam mit einem großen europäischen Automobilhersteller zur Serienreife weiterentwickelt worden. Seit 2010 hatte Freudenberg Sealing Technologies intensiv an der neuen Technologie geforscht, ab Januar 2016 folgte die Fertigung von Prototypen auf einer eigenen Produktionslinie, um die Entwicklungsziele am realen Bauteil zu validieren, bevor die Herstellung automatisiert wurde. An den einzelnen Stationen der Produktionslinie kommen sieben Roboterarme zum Einsatz. Da die Roboter die einzelnen Arbeitsschritte immer in der gleichen Weise ausführen, lässt sich der Montageprozess gut reproduzieren. Das ist wichtig, um die Herstellung der Levitex-Dichtungen zügig auf weitere Montagelinien übertragen zu können.
Die Konstruktion der neuen Levitex-Dichtungen ist mit sehr hohen Anforderungen verbunden: Die Materialzusammensetzung muss exakt stimmen, die geometrische Form strikt eingehalten werden. Aus diesem Grund gibt es in den Produktionsprozessen an mehreren Stellen Qualitätskontrollen. Nach jedem Montageschritt messen Lasersensoren in der darauffolgenden Anlage die Geometrie und die Position des jeweiligen Bauteils exakt aus. Dadurch kontrolliert sich der Produktionsprozess gewissermaßen selbst. Außerdem setzen die Ingenieure in einem separaten Arbeitsschritt ein Weißlicht-Interferometer ein, um die Beschaffenheit der Ringoberflächen zu überprüfen. Und am Ende der Montage folgt eine Dichtheitsprüfung mit Luft, um die sichere Funktion zu gewährleisten.
Levitex: Die Dichtung mit dem Luftkissen
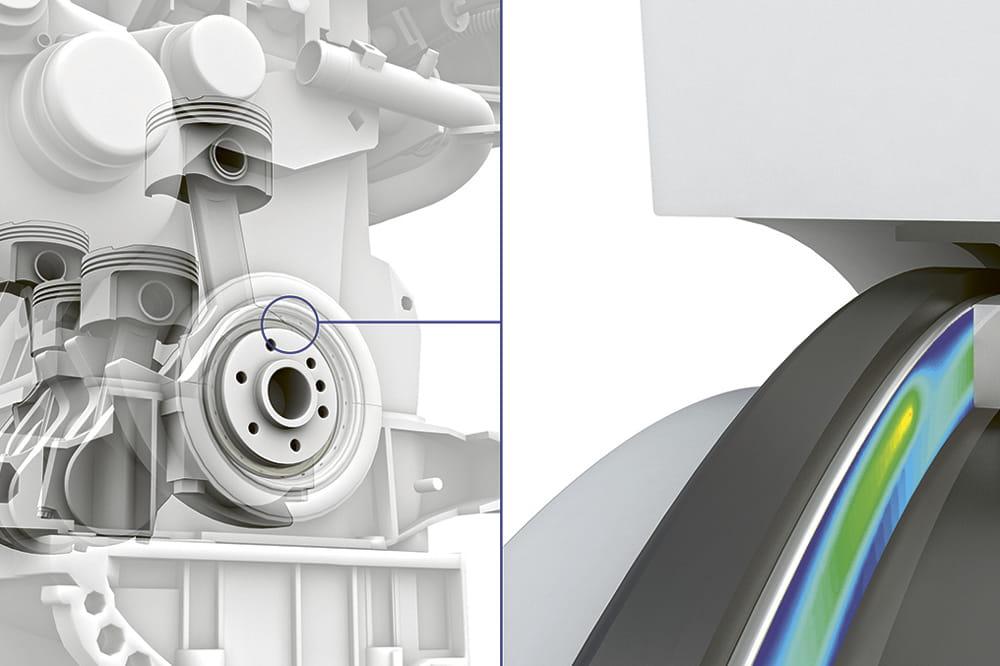
Abheben und Schweben: Sobald sich die Kurbelwelle dreht, baut die Levitex-Dichtung ein Luftkissen auf.
Bei jedem Verbrennungsmotor sorgen Dichtungen dafür, dass das Öl im Motorraum bleibt. Eine wichtige Abdichtungsstelle ist dabei der Übergang vom Motor zum Getriebe, wo die Kurbelwelle mit einer Ringdichtung zum Kurbelgehäuse abgeschlossen wird. Genau hier kommen die Levitex-Dichtungen zum Einsatz. Sie bestehen im Kern aus zwei metallischen Ringen, von denen einer mit dem Kurbelgehäuse und der andere mit der Kurbelwelle fest verbunden ist. Die Oberflächen der Ringe verfügen über kleine, nur wenige Mikrometer große Vertiefungen. Dreht sich nun die Kurbelwelle, so wird die Umgebungsluft in diese Vertiefungen hineingepresst; es entsteht ein Luftkissen, das die Dichtflächen voneinander trennt und eine nahezu reibungsfreie Rotation der Welle ermöglicht – das spart Kraftstoff und reduziert die CO2-Emissionen. Um dabei die Schwingungen des Kurbelgehäuses zu reduzieren und ein funktionsfähiges Luftpolster zu gewährleisten, ist das Trägergehäuse des statischen Metallrings mit einer Gummifeder ausgestattet. Wenn die Welle nicht mehr rotiert, dann schließen sich die Metallringe und verhindern so, dass während des Stillstands Öl aus dem Motorraum austritt. Damit dies absolut sicher geschieht, sind die Gleitringdichtungen mit einer zusätzlichen Beschichtung versehen. Zuvor kamen gasbefüllte Ringdichtungen nur in großen Industrieanlagen zur Anwendung. Erst die von Freudenberg Sealing Technologies patentierte Konstruktion und das dazugehörige Herstellverfahren ermöglichen es, die Idee auf den Fahrzeugmotor zu übertragen, wo nur sehr wenig Platz für den Einbau vorhanden ist. Und die Elektromobilität wird die nächste Herausforderung für diese Technologie sein.
Technisch anspruchsvoll, aber einfach zu montieren
Die vielen Qualitätschecks sind auch deswegen notwendig, weil der Montageablauf aus vielen einzelnen Arbeitsschritten besteht. Das Unternehmen hat sich für einen dezentralen und möglichst einfachen Ansatz entschieden, bei dem die einzelnen Fertigungsmodule unabhängig voneinander arbeiten. Jedes einzelne Modul ist so ausgelegt, dass es den jeweiligen Arbeitsschritt bestmöglich ausführen kann. So lassen sich die technisch anspruchsvollen Dichtungen mit einer relativ einfachen Architektur fertigen. Die Produktionsdaten werden dann aber zentral zusammengeführt:
Messen und Prüfen: Um bei den vielen Arbeitsschritten Fehler auszuschließen, sind in den Prozess mehrere Qualitätschecks eingebaut.
Nach der Montage graviert ein Laser auf jeden einzelnen Dichtring eine Seriennummer ein, unter der die individuellen Produkteigenschaften wie Oberflächenbeschaffenheit, Geometrie, Gewicht und Produktionsdatum hinterlegt werden. Die Möglichkeit, jedes einzelne Produkt nachverfolgen zu können, ist eine Besonderheit und war eine zentrale Anforderung an die Fertigungsplanung.
Kundenwünsche realisierbar
Die modulare Montage bietet noch weitere Vorteile. Denn dadurch können Kundenwünsche relativ einfach in den Produktionsprozess integriert werden. Die Dichtringe sind beispielsweise mit einem zusätzlichen Sensor ausgestattet, der ein elektrisches Signal zur Positionsbestimmung an die Motorsteuerung weitergibt. Durch den modularen Ansatz ließ sich diese Anforderung gut umsetzen und es war möglich, einen dafür erforderlichen antistatischen Bereich innerhalb der Fertigungslinie einzurichten. Bei der Auslegung der Endmontage lernten die Ingenieure in Pinerolo auch von den Erfahrungen mit ähnlichen Ansätzen an anderen Standorten von Freudenberg Sealing Technologies, etwa von den Kollegen im französischen Langres, wo ebenfalls Dichtungen für die Kurbelwelle hergestellt werden. Der neue Dichtungsring zeigt jedenfalls messbare Wirkung. Das Einsparpotenzial durch die geringere Reibung an der Kurbelwelle liegt bei bis zu einem Gramm pro gefahrenem Kilometer. Das summiert sich schnell auf – und fällt angesichts der anspruchsvollen CO2-Ziele umso mehr ins Gewicht. Reibung soll am besten eben nur dort entstehen, wo sie auch wirklich gebraucht wird.
Dieser Beitrag stammt aus unserem Unternehmensmagazin „ESSENTIAL“, in dem wir kontinuierlich über Trends und Schwerpunktthemen aus unseren Zielindustrien und -märkten berichten. Weitere Beiträge des Magazins finden Sie hier.
Weitere Storys zum Thema Nachhaltigkeit
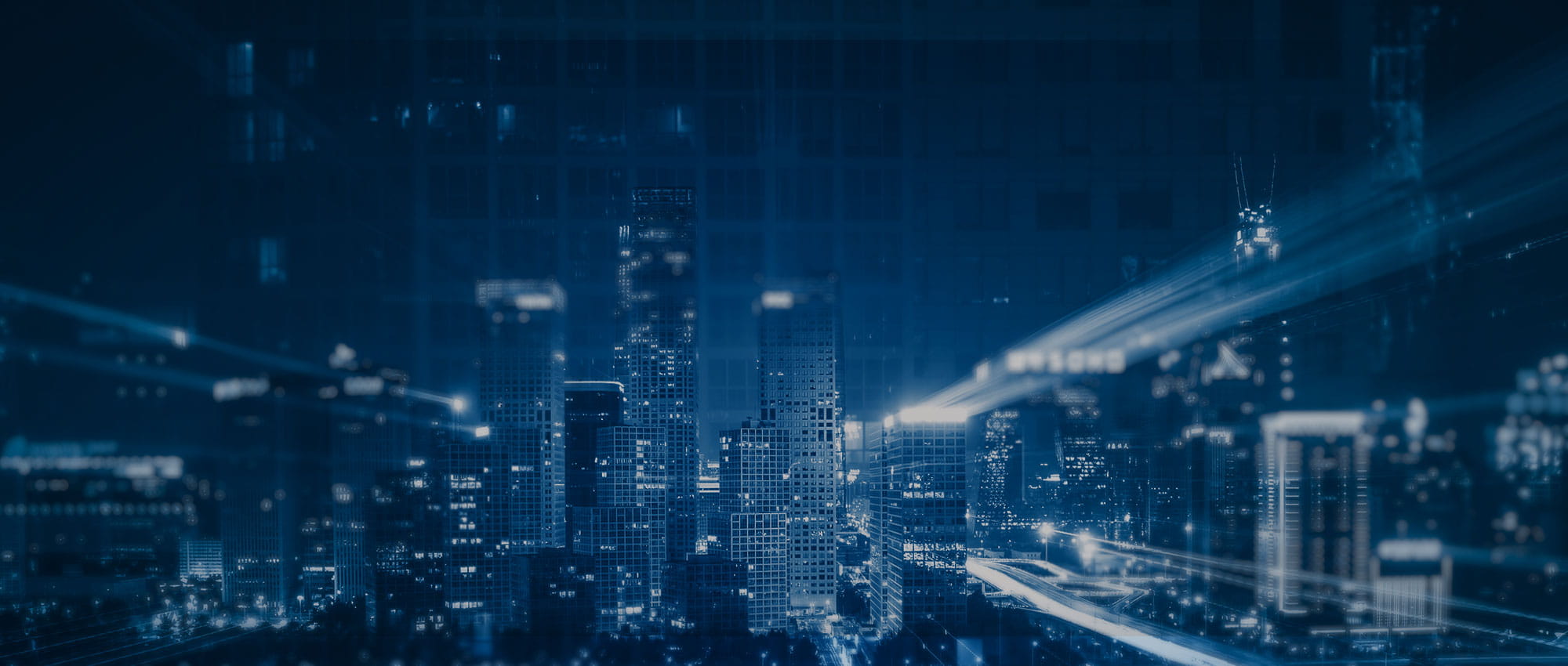
Join Us!
Freudenberg Sealing Technologies, seine Produkte und Serviceangebote in Wort und bewegten Bildern erleben, sich mit Mitarbeitenden und Stakeholdern vernetzen und dabei wertvolle geschäftliche Kontakte knüpfen.
Auf LinkedIn vernetzen! open_in_new