Neuigkeiten und Hintergründe aus der Dichtungstechnik erfahren, innovative Produkte kennenlernen – im kostenlosen E-Mail-Newsletter von Freudenberg Sealing Technologies.
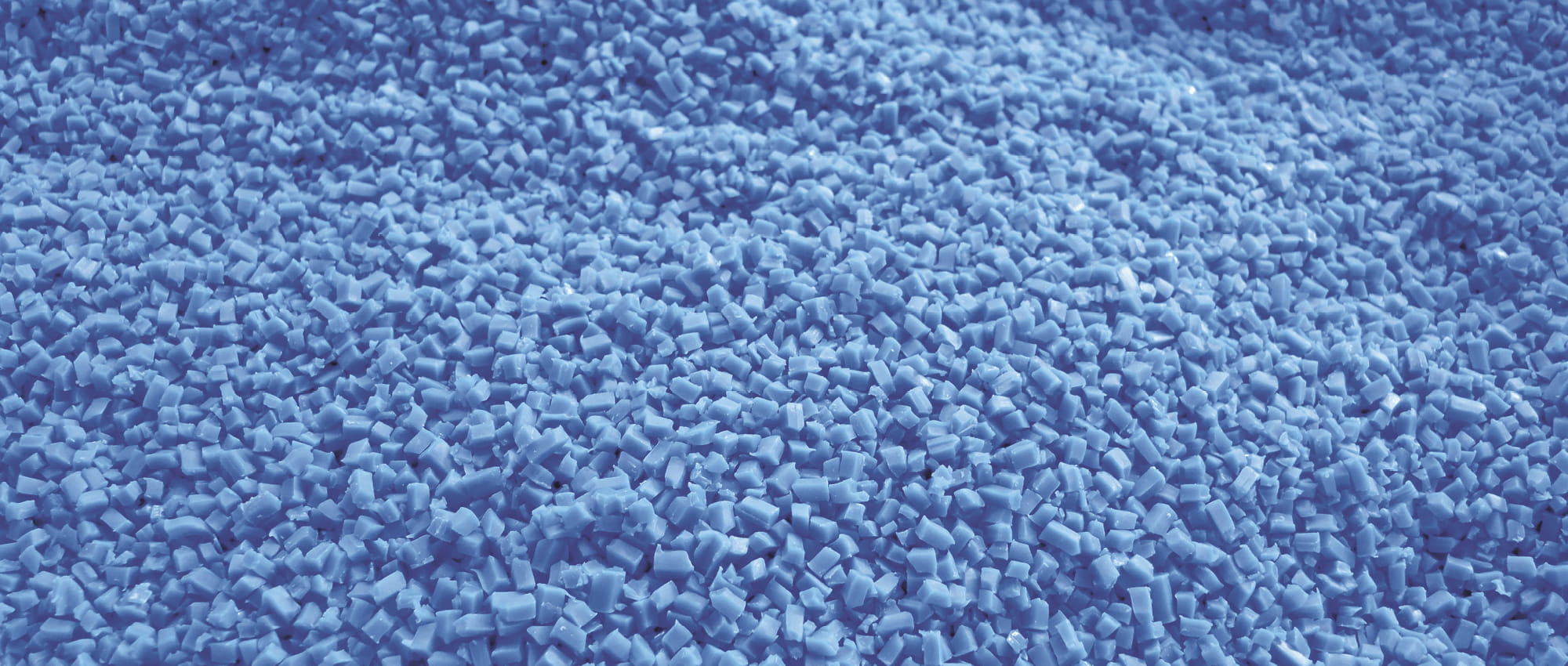
Werkstoff-Monitoring in der Produktion
Werkstoffe sind sensibel. Ist etwa das Granulat thermoplastischer Polyurethane etwas zu feucht, dann leidet die Qualität der daraus produzierten Teile. Freudenberg Sealing Technologies schiebt dem einen Riegel vor, dank digitalem Schatten.
Manchmal sind es Kleinigkeiten, die über Wohl und Wehe entscheiden. Das wissen auch die Prozessingenieurinnen und -ingenieure von Freudenberg Sealing Technologies. Bei der Herstellung von Hydraulik- und Pneumatikdichtungen, wie sie zum Beispiel in der Mobilhydraulik von Baggern verbaut werden, sind Thermoplastische Polyurethane (TPU) einer der Hauptwerkstoffe. Ihre Qualität ist mitentscheidend für die Funktionsfähigkeit der benötigten Komponenten. Ist das TPU-Granulat nur minimal zu feucht, dann ändert sich dessen Fließverhalten im Spritzgussverfahren. Die Folge: Die Polymerketten können sich nicht ausreichend ausbilden. Eigenschaften wie Zugfestigkeit und Bruchdehnung sind dann nicht so gegeben, wie sie sollten.
Unsere Stichproben ergaben, dass die KI-Vorhersagen zum Wassergehalt im Granulat lediglich um 0,005 Prozent von den Ergebnissen der manuellen analytischen Messung abwichen.
Armin Hermann, Manager, Materials Lab, Schwalmstadt plant, Freudenberg Sealing Technologies
Das Ziel: ein 24-Stunden-Monitoring
Will man also nicht erst bei der Qualitätskontrolle feststellen, dass ein ganzes Los produzierter Teile zu beanstanden ist, dann muss bereits bei der Lagerung der TPU angesetzt werden. Im Werk in Schwalmstadt, nördlich von Frankfurt/Main, lagern diese in Sechs-Tonnen-Silos. Das Bestimmen der Granulatfeuchte in den Großbehältern erfolgt manuell. Um Stichproben zu entnehmen, müssen die Silos geöffnet werden. Ein Prozess, der aber nur eine Momentaufnahme darstellt. „Was wir brauchten, war ein 24-Stunden-Monitoring“, erinnert sich Armin Hermann, Leiter des Werkstofflabors in Schwalmstadt. Seit Kurzem hat er ein solches Monitoring als Leiter eines zwölfköpfigen Projektteams realisiert.
Der Schlüssel zum Erfolg war künstliche Intelligenz. Doch bis es so weit war, wartete eine Menge Arbeit auf die Projektbeteiligten. Das begann damit, dass die Prozessingenieure in Schwalmstadt und ein IT-Expertenteam von Freudenberg Sealing Technologies lernen mussten, mit einer Sprache zu sprechen. „Man kann sich das überspitzt formuliert so vorstellen, dass Analog 2.0 auf Industrie 4.0 traf“, verdeutlicht Hermann. „Es waren zwei Welten, die sich in unserem Projektteam begegneten.“ Entpuppte sich die Kommunikation anfangs noch als Hemmschuh, so verstanden sich die beiden Gruppen bald immer besser. Um einen Algorithmus zu schreiben, war es für die IT-Fachleute unerlässlich, die Prozesse im Werk nicht nur zu verstehen, sondern inhaltlich komplett zu durchdringen. „Wir haben Fragen über Fragen gestellt, um das Problem und die Verfahren nachzuvollziehen“, berichtet Anna Lüders, Data Scientist aus dem firmeneigenen Advanced Analytics Team. Ihre Aufgabe war es, das Simulationsmodell zu erstellen, das präzise Vorhersagen zur Feuchtigkeit des TPU-Granulats erlaubt.
Die Lösung: ein digitaler Schatten
Um die Restfeuchte im TPU bestimmen zu können, war es elementar, ein maschinelles Lernmodell zu entwickeln. Ihm lag der Aufbau einer strukturierten Datenübertragung und -speicherung zugrunde, den die Fachleute des „MES and IIoT Systems Teams“ von Freudenberg verantworteten. Den Grundstock der Datenbank bildeten die Daten, die bislang manuell erfasst worden waren. Um sie mit aktuellen Daten anzureichern, installierte das Projektteam Sensorik innerhalb wie außerhalb der Silos. Sie erfasst die Temperaturen und die Luftfeuchtigkeit in beiden Umgebungen. Daneben fließen weitere Parameter wie die Lagerdauer in die Datenbank ein. Aus all diesen Merkmalen lässt sich die Materialfeuchte des Granulats ableiten. Die manuellen Messungen wurden reduziert. Sie sind aber weiter notwendig, um die Realität mit den Werten des von IT-Expertin Lüders entwickelten Algorithmus abzugleichen. Rasch wurde klar, die Arbeit des Projektteams hat sich gelohnt. „Unsere Stichproben ergaben, dass die KI-Vorhersagen zum Wassergehalt im Granulat lediglich um 0,005 Prozent von den Ergebnissen der manuellen analytischen Messung abwichen“, weiß Projektleiter Hermann. Eine zu vernachlässigende Differenz.
Bei der in Schwalmstadt etablierten Lösung spricht man in der Fachsprache übrigens von einem digitalen Schatten. Von der Idee bis zur erfolgreichen Implementierung des digitalen Schattens benötigte das Projektteam ein Jahr. Nun wird die Granulatfeuchte automatisiert berechnet und visualisiert. Werden Grenzwerte überschritten, schlägt das System Alarm, sodass die Prozesstechniker vor Ort zeitnah eingreifen können. Damit bleibt sichergestellt, dass das TPU-Granulat in der notwendigen Qualität in den Produktionsprozess gelangt. Eine Tatsache, von der sich ein Großkunde inzwischen mehrfach überzeugen konnte. Er erhält vor jeder Produktion ein Muster der für ihn vorgesehenen Charge. Seit die KI am Monitoring der Silos mitwirkt, hat er sie kein einziges Mal beanstandet. „Sein Vertrauen in uns wächst so noch mehr“, bekräftigt Projektleiter Hermann. „Und das, obwohl wir unsere Werkstoffrezeptur unverändert ließen. Wir optimieren dank der KI lediglich physikalische Werte.“
Digitaler Zwilling vs. digitaler Schatten
Ein digitaler Zwilling und ein digitaler Schatten erlauben die Echtzeitüberwachung eines realen Objekts (zum Beispiel eines Silos). Beide sammeln und analysieren Ereignisse und Prozesse rund um das Objekt und stellen die erhobenen Daten bereit. Eine Interaktion mit dem realen Objekt ist jedoch nur dem digitalen Zwilling möglich.
Die Vorteile: Störeinflüsse leichter identifizieren
Ein weiterer Nutzen ließ sich aus der Visualisierung der Prozesse ziehen. Manche Werkstoffe müssen künstlich altern. Um das zu erreichen, wird den Silos über einen bestimmten Zeitraum Warmluft zugeführt. Messungen der Abluft zeigten nun, dass die investierte Wärme dort nie erreicht wird. Tests zeigten, dass eine Isolierung der Rohre und eines Teils der Silos ausreichte, um mit weniger heißer Zuluft den gleichen Alterungseffekt beim Werkstoff zu erzielen. Eine Erkenntnis, die helfen wird, Energie einzusparen. Als Nächstes wird sich das Projektteam einem anderen Thema widmen: der Staubentwicklung in Silos. Denn Staubpartikel sorgen dafür, dass sich Fremdkörper bilden, die im Spritzguss nachteilig sind.
„Wir sind mit dem Simulationsmodell absolut zufrieden“, berichtet Hermann. „Zum einen, weil wir endlich Antworten auf bislang unbeantwortete Fragestellungen erhalten. Zum anderen aber auch, weil wir sehen, dass sich einige unserer Theorien bestätigen.“ Anna Lüders sieht die Ziele erreicht, die man sich von der Einführung der KI-basierten Methode versprach: „Durch den digitalen Schatten erkennen wir Prozessabweichungen früher und verbessern die Prozessstabilität als Ganzes. Die Quellen für Störeinflüsse sind heute leichter zu identifizieren, und unser Prozess-Know-how wächst in strukturiert erfasster Form immer weiter.“ Alles ein deutlicher Mehrwert. Dank digitalem Schatten.
Dieser Beitrag stammt aus unserem Unternehmensmagazin „ESSENTIAL“, in dem wir kontinuierlich über Trends und Schwerpunktthemen aus unseren Zielindustrien und -märkten berichten. Weitere Beiträge des Magazins finden Sie hier.
Weitere Storys zum Thema Technologie
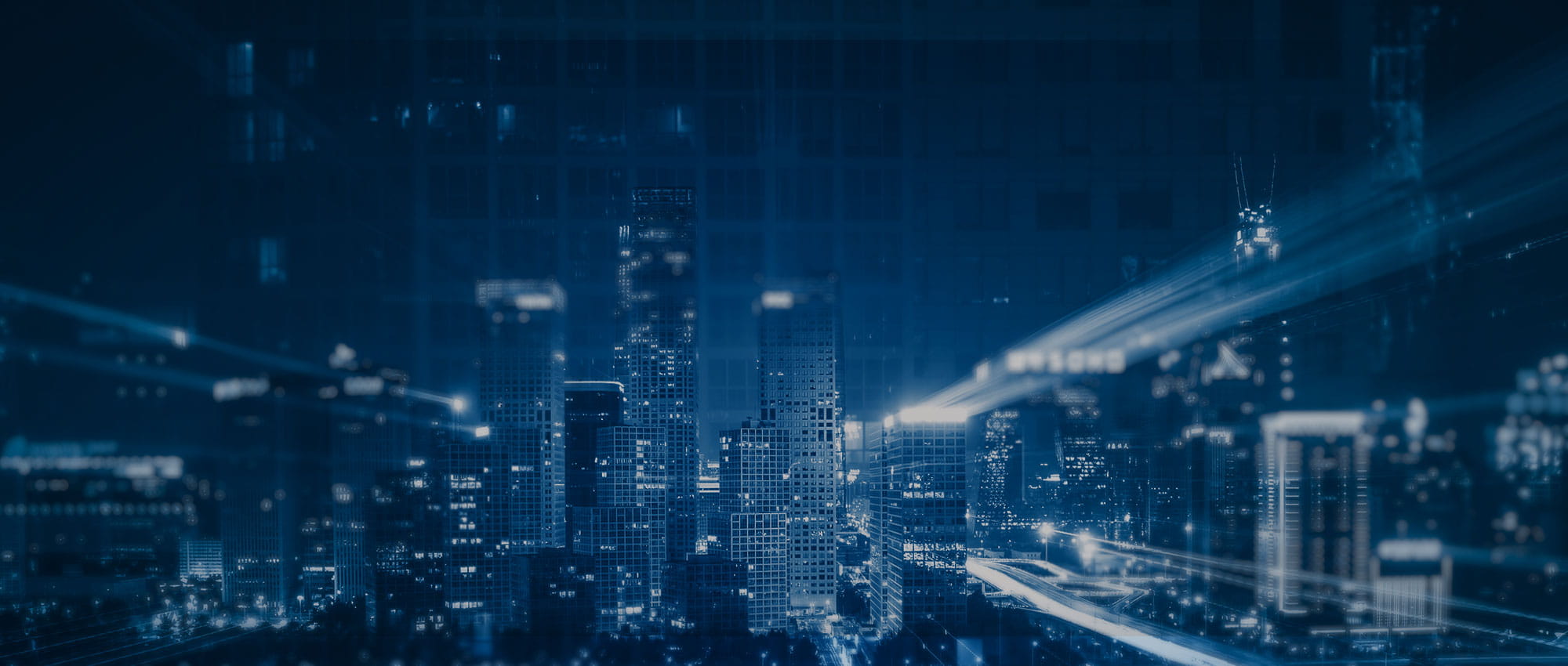
Join Us!
Freudenberg Sealing Technologies, seine Produkte und Serviceangebote in Wort und bewegten Bildern erleben, sich mit Mitarbeitenden und Stakeholdern vernetzen und dabei wertvolle geschäftliche Kontakte knüpfen.
Auf LinkedIn vernetzen! open_in_new