Neuigkeiten und Hintergründe aus der Dichtungstechnik erfahren, innovative Produkte kennenlernen – im kostenlosen E-Mail-Newsletter von Freudenberg Sealing Technologies.
13.12.2017
Bohrhammer Atlas Copco - 140 Mal pro Sekunde
Bis zu 140 Mal pro Sekunde trifft der Bohrmeißel mit einer Kraft von 25 Tonnen auf die Gesteinsoberfläche. Seine Aufgabe: 80 Löcher zu bohren, in die anschließend die Sprengladungen kommen, mit denen Versorgungstunnel im Untertage-Bergbau oder im Straßenbau in den Fels gesprengt werden. Angetrieben wird der Meißel von einem Gesteinsbohrhammer, im Englischen als „Rock Drill“ bezeichnet. Um die Betriebskosten solcher Bohrhämmer niedrig zu halten, sind zwei Faktoren ausschlaggebend: Einerseits müssen die Löcher auch in hartem Gestein wie Granit sehr schnell gebohrt werden, was den Einsatz sehr hoher Kräfte bedingt. Andererseits sollen trotz der hohen Kräfte die Wartungsintervalle gesteigert werden. Bei der Entwicklung der neuen Maschine COP MD20 hat Atlas Copco den Zielkonflikt gelöst: Bei unverminderter Vortriebsleistung konnten die Wartungsintervalle verdoppelt werden.
Die Schlüsselkomponente dafür war der Einsatz eines neuen Dichtungssystems von Freudenberg Sealing Technologies. Denn die metallischen Bauteile - insbesondere der Kolben, der den Meißel antreibt - waren zuvor bereits optimiert worden, etwa durch den Einsatz hochfester Speziallegierungen. Doch die insbesondere beim Rückfahren des Meißels auftretenden Kräfte sind so hoch, dass sie auch die Dichtungen im Hochdruck-Hydrauliksystem stark belasten. Tritt an diesen Dichtungen Verschleiß auf, kann es zu Leckagen kommen, die das Verhältnis von einzusetzender Energie und Bohrkraft sehr negativ beeinflussen – sprich die Systemeffizienz sinkt.
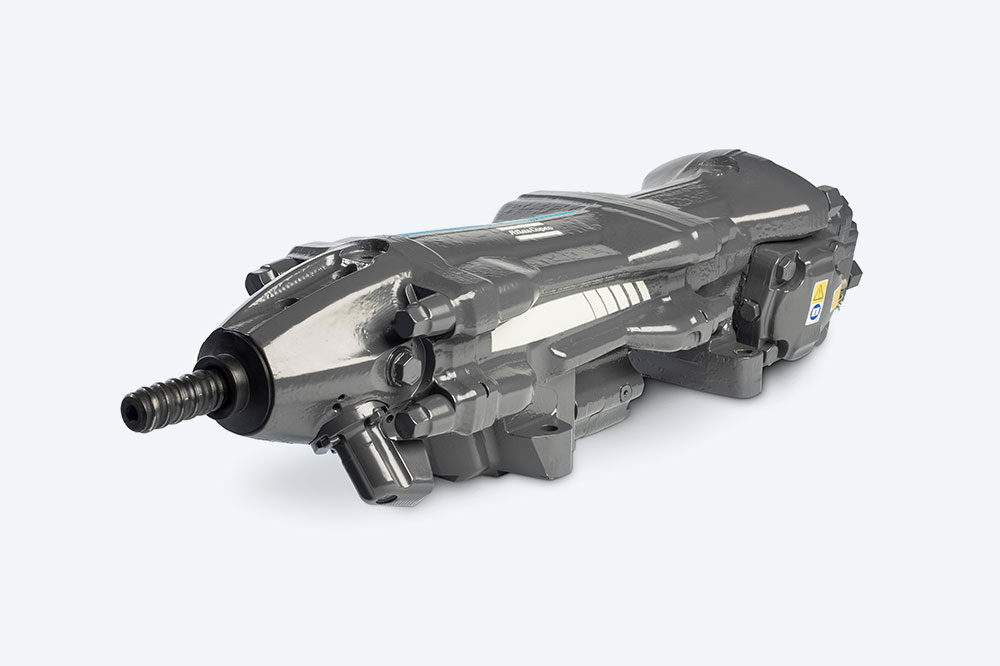
In einem von Freudenberg Sealing Technologies initiierten Workshop fanden die Entwickler die genaue Ursache für den Dichtungsverschleiß heraus: Die Dichtungen werden nicht nur durch die Längsbewegung des Kolbens beansprucht, sondern werden von diesem gleichzeitig in eine Rotationsbewegung versetzt. Die Analysen zeigten, dass sich eine der Radial-Wellendichtungen relativ konstant mit 300 bis 400 Umdrehungen pro Minute bewegt, darauf aber nicht ausgelegt war. Für die COP MD20 entwickelten die Freudenberg-Ingenieure deshalb eine Speziallösung mit einer veränderten Konstruktion sowie einem neuen Materialmix. Anschließende Tests auf dem Prüfstand sowie mit sechs Versuchsträgern, die sich unter Tage in Australien, Schweden, Spanien und Portugal bewähren mussten, erbrachten den Nachweis: die Lebensdauer der entscheidenden Dichtung konnte deutlich verlängert werden.
Der neue Gesteinsbohrhammer COP MD20 von Atlas Copco wird seit Anfang 2017 im schwedischen Örebro in Serie produziert. Freudenberg Sealing Technologies ist Alleinlieferant für alle 30 Dichtungen, die in der neuen Maschinengeneration zum Einsatz kommen. Dazu gehören neben zahlreichen Komponenten im Hydrauliksystem auch die Gehäusedichtungen, die dafür sorgen, dass weder Bohrstaub noch Feuchtigkeit eindringen.
In die Entwicklung des Dichtungssystems für die COP MD20 waren Freudenberg-Experten aus Hamburg, Schwalmstadt und Weinheim sowie aus Schweden eingebunden. Das gesamte Projekt folgte dem von Freudenberg Sealing Technologies definierten Innovationsprozess. Es begann mit einem gemeinsamen Ideen-Workshop von Kunde und Zulieferer, setzte sich in einem fünfstufigen Entwicklungsprozess fort und endete mit der Produktion einer bahnbrechenden Innovation.
Ulrike Reich
Head of Media Relations & Internal Communications
Telephone: + 49 (0) 6201 960 5713
ulrike.reich@fst.com chevron_rightDownload Dokumente
News-Service
Bleiben Sie auf dem neusten Stand und erhalten Sie unsere Presseinformationen per E-Mail. Sie können sich jederzeit wieder abmelden.
Jetzt anmelden! chevron_rightWeitere verwandte Artikel
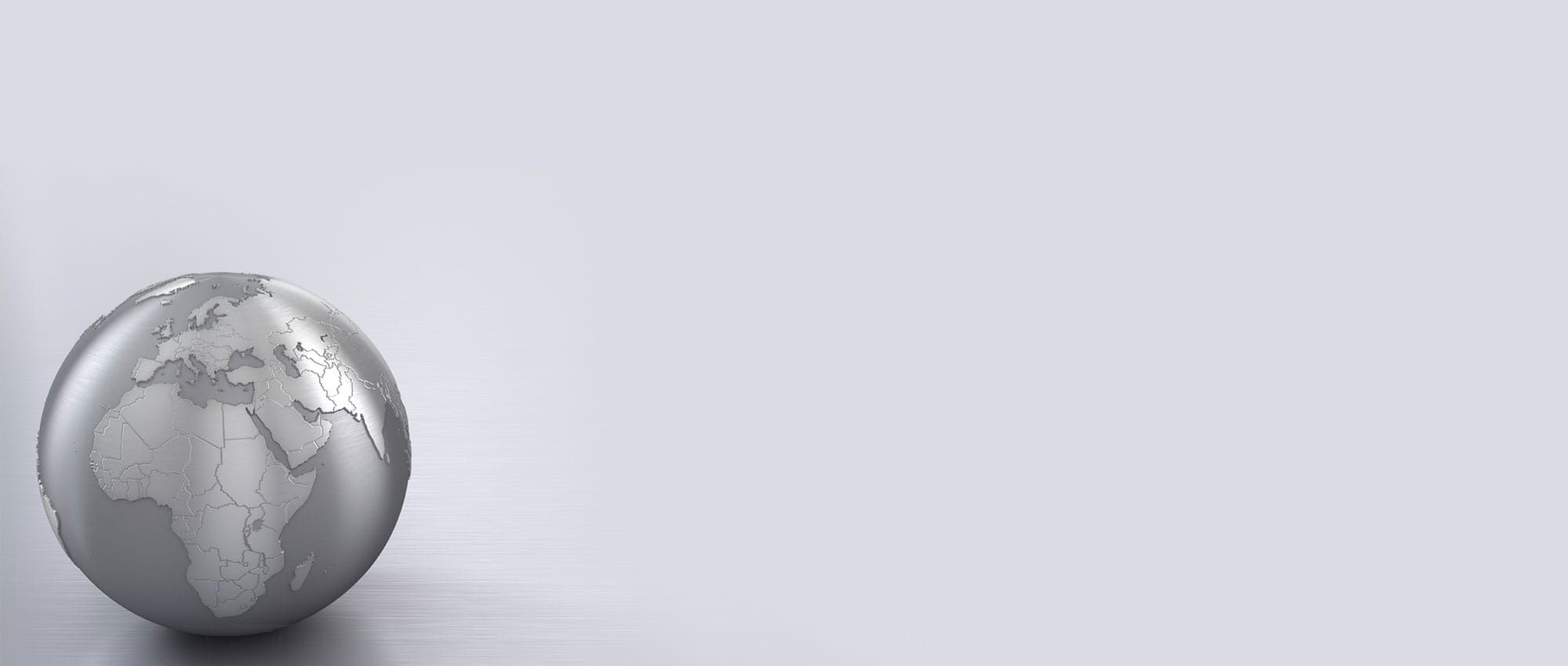
Immer informiert
Auf dem Laufenden bleiben:
Mit dem Newsletter von Freudenberg Sealing Technologies.