Neuigkeiten und Hintergründe aus der Dichtungstechnik erfahren, innovative Produkte kennenlernen – im kostenlosen E-Mail-Newsletter von Freudenberg Sealing Technologies.
06.07.2021
Hoch hinaus... und dort stundenlang fliegen
Der neue Werkstoff 80 EPDM 426288 dichtet erfolgreich Hydrauliksysteme ab, die bei Temperaturen von bis zu -65 °C arbeiten – ein Durchbruch bei EPDM-Rezepturen. Statt großer Mengen an Weichmachern verwenden die Wissenschaftler von Freudenberg Sealing Technologies ein besonderes Polymer, um den neuen Werkstoff herzustellen.
Das Material erfüllt die strengen Anforderungen der Spezifikation AMS7361 für verbessertes Tieftemperaturverhalten in Hydrauliksystemen von Verkehrsflugzeugen. Sowohl in Labortests als auch in der Anwendung zeigt 80 EPDM 426288 ein hervorragendes Dichtungsverhalten bei niedrigen Temperaturen, nachdem es intensiven Belastungen durch Flüssigkeiten, Drücke und extremen Temperaturen ausgesetzt war. Das Material kann so hergestellt werden, dass es gegen Sonnenlicht, Ozon und chemische Zersetzung beständig ist, Phosphatester-Hydraulikflüssigkeiten und andere Flüssigkeiten effektiv abdichtet und bei Temperaturen von bis zu 150 °C einwandfrei funktioniert.
Die Herausforderung
In Verkehrsflugzeugen – die in Höhen von knapp 13.000 Metern mit bis zu 926 km/h fliegen – kommen Standard-EPDM-Werkstoffe zur Abdichtung kritischer Hydrauliksysteme beispielsweise im Fahrwerk zum Einsatz. In solchen Höhen und bei solchen Geschwindigkeiten hält die Reibungswärme, die bei der Bewegung des Flugzeugs durch die Luft entsteht, die Temperatur des Hydrauliksystems in einem Bereich, in dem herkömmliche EPDM-Komponenten ihre volle Funktionsfähigkeit behalten.
Aber Verkehrsflugzeuge sind nicht die einzigen Flugzeuge, die heute am Himmel fliegen. Auch Turboprop-Transportmaschinen und unbemannte Luftfahrzeuge, sogenannte Drohnen, sind dort unterwegs. Gerade Drohnen sind mittlerweile standardmäßig im Einsatz, wenn es um die Erfassung von Daten und die Lieferung von Gütern in Bereichen wie Medizin, Umweltschutz, Vermessung, Film und Fotografie, Strafverfolgung und Katastrophenhilfe geht.
Allerdings sind Drohnen auch eine Herausforderung für Luft- und Raumfahrtingenieure: Die Geschwindigkeiten, mit denen sie fliegen – typischerweise 160 km/h oder weniger – in Kombination mit dem Flug in den gleichen oder sogar größeren Höhen wie kommerzielle Flugzeuge reduzieren die Luftreibung und die Hitze an der Außenseite des Fluggeräts. Infolgedessen müssen sie längere Zeit sehr kalte Temperaturen aushalten, gefolgt von einem abrupten Temperaturwechsel bei der Landung. Das Gleiche gilt für Frachtmaschinen und andere langsam fliegende Flugzeuge.
Standard-EPDM-Werkstoffe werden bei längerem Einsatz in sehr niedrigen Temperaturen spröde und reißen. Diese Risse können zu Flüssigkeitslecks in wichtigen Systemen wie in den hydraulischen Bremsleitungen führen. Daher suchten Ingenieure in der Luft- und Raumfahrtbranche nach einer Lösung für solche Leckageprobleme. Gleichzeitig kamen neue Hydraulikflüssigkeiten auf den Markt, die ebenfalls die Entwicklung und Evaluierung neuer Materialrezepturen notwendig machten.
Erfolgsfaktor: Ein internationales Forschungsteam
Freudenberg Sealing Technologies erkannte den Bedarf seiner Kunden aus der Luft- und Raumfahrtbranche. Unter der Leitung von Dr. Paul Hochgesang, einem Mitarbeiter der Materialforschung in den Laboren des Unternehmens in Plymouth (USA), wurden mehrere neue EPDM-Rezepturen entwickelt. Dabei setzte das Team auf modernste Monomer- und Polymertechnologien, um ein besseres Gleichgewicht zwischen dem Verhalten bei hohen und niedrigen Temperaturen zu erreichen. Diese Formeln zeigten sehr gute Ergebnisse im Hinblick auf die in der Luft- und Raumfahrtbranche geforderten Materialstandards. Allerdings konnten die Werkstoffe längere Kältetests nicht bestehen – sie verloren an Festigkeit und wurden spröde.
„Wir haben eine Vielzahl von Inhaltsstoffen gemischt, darunter Weichmacher, Füllstoffe und Hitzestabilisatoren. Dennoch konnten wir immer noch nicht den Temperaturgradienten erreichen, den unsere Kunden benötigten“, kommentiert Hochgesang. „In dem Moment kamen die Material- und Beschaffungsexperten unseres Unternehmens in Deutschland und Japan ins Spiel.“
Sie stellten Hochgesang ein neues, weitgehend unbekanntes Industriepolymer vor. In Verbindung mit einer neuen EPDM-Rezeptur erfüllte das daraus resultierende Material nicht nur die von Kunden aus der Luft- und Raumfahrt geforderten Kalttemperaturen, sondern übertraf sie sogar. Die endgültige Entwicklung von 80 EPDM 426288 nahm dann weniger als sechs Monate in Anspruch. „Dies ist ein hervorragendes Beispiel für die internationale Zusammenarbeit der Freudenberg-Wissenschaftler. Wir können erfolgreich sein, indem wir das Wissen und die Fähigkeiten von Kollegen aus aller Welt bündeln“, so Hochgesang weiter. „Auf diese Weise haben wir bereits viele unserer schwierigsten Herausforderungen gemeistert.“
Dichtungen und Komponenten aus 80 EPDM 426288 wurden bereits in Werken von Freudenberg Sealing Technologies in Nordamerika und Europa gefertigt und von mehreren großen Herstellern und Systemlieferanten der Luft- und Raumfahrtbranche getestet. Nach den positiven Rückmeldungen von Kunden startete jetzt die Serienproduktion von O-Ringen für die Luft- und Raumfahrt aus dem neuen EPDM-Werkstoff.
Ulrike Reich
Head of Media Relations & Internal Communications
Telephone: + 49 (0) 6201 960 5713
ulrike.reich@fst.com chevron_rightPressemeldung herunterladen
News-Service
Bleiben Sie auf dem neusten Stand und erhalten Sie unsere Presseinformationen per E-Mail. Sie können sich jederzeit wieder abmelden.
Jetzt anmelden! chevron_rightWeitere verwandte Artikel
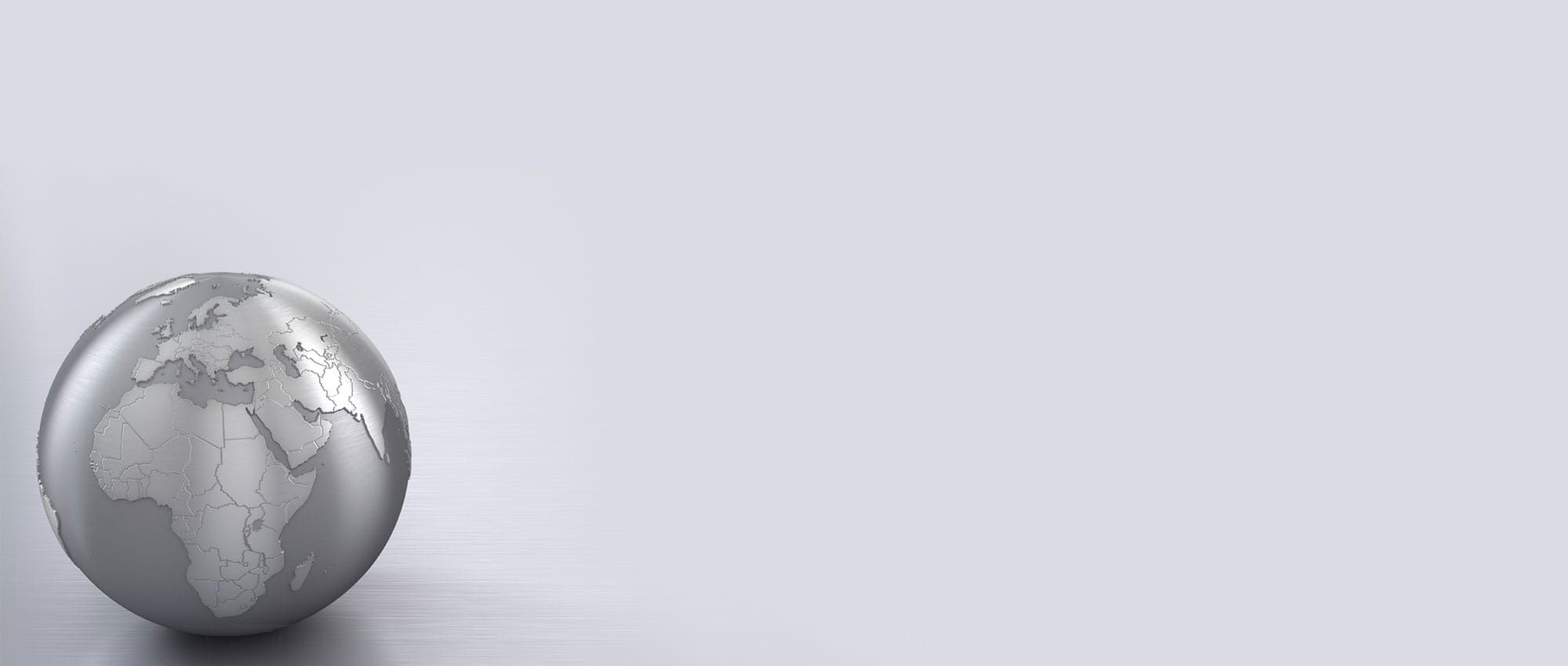
Immer informiert
Auf dem Laufenden bleiben:
Mit dem Newsletter von Freudenberg Sealing Technologies.