Obtain news and background information about sealing technology, get in touch with innovative products – subscribe to the free e-mail newsletter.

Injection Molding Machines@Model.HeadlineTag.Tag>
Injection Molding Machines ‒ Following the Beat of the Machine
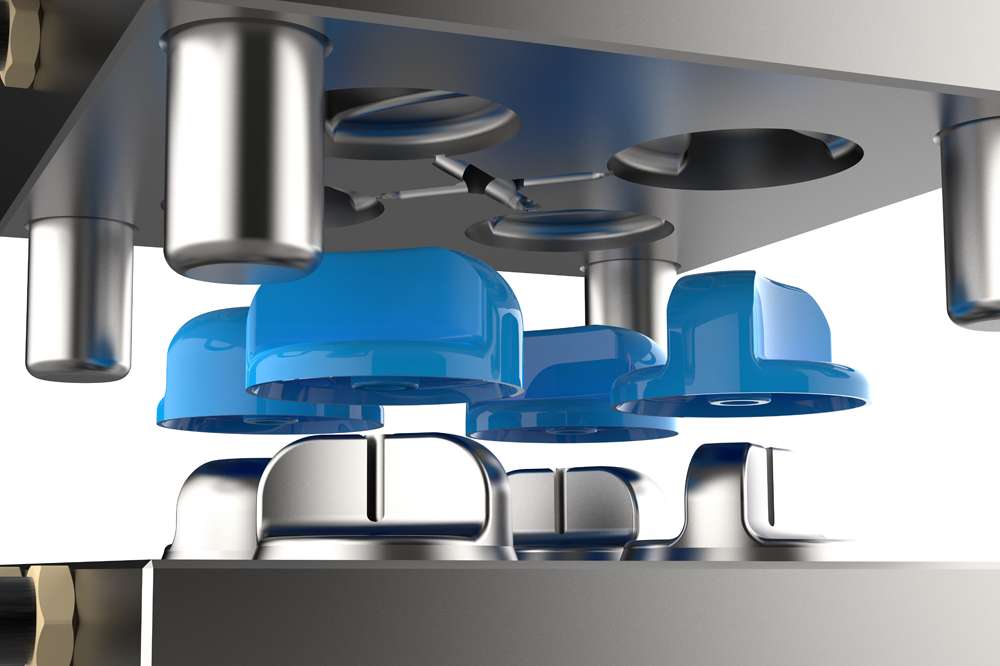
Extremely different forward and return stroke speeds, the shortest strokes at high cycle rates, sometimes under permanent load or rapid load changes - the operating conditions for seals in hydraulic cylinders for injection molding machines are diverse and always challenging. Highest reliability, stick-slip-free performance and low operating costs are the targets to meet.
Injection molding machines process plastic in granulate or powder form into a wide variety of molded parts. The structure of the machine can be described with two assemblies. The injection unit, also called the plasticizing unit, prepares the plastic raw material and injects it into the subsequent mold. The clamping unit takes care of this molding tool, opening and closing it. While electromechanical drives are increasingly used for the associated movements in smaller injection molding machines, large-format machines operate predominantly hydraulically. The advantages of a hydraulic drive are obvious. Large, precisely adjustable closing and clamping forces can be generated in a compact space.
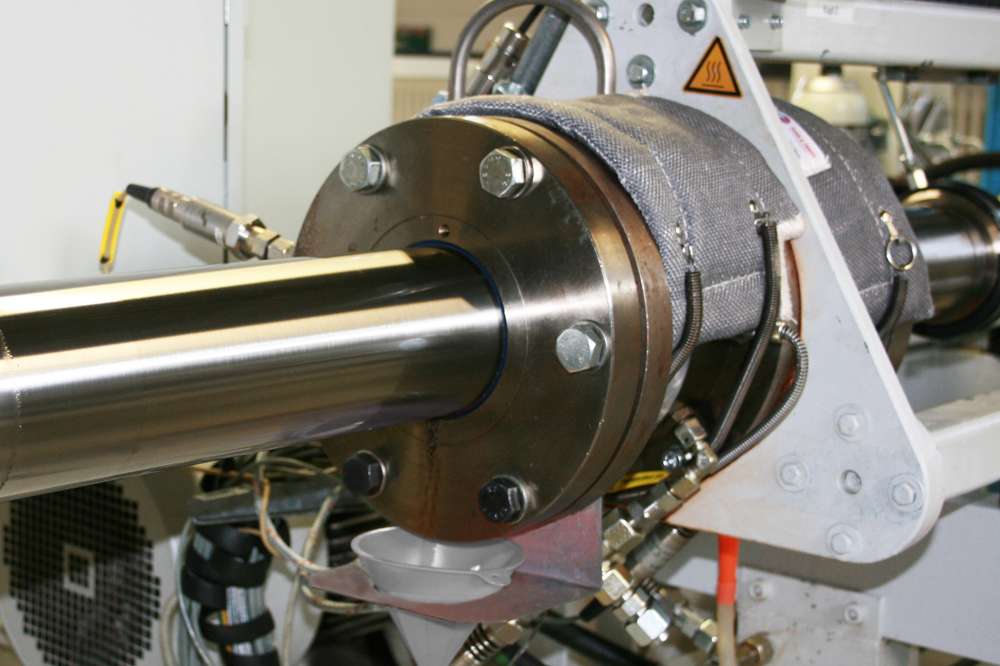
Checked to the Last Corner
The different movement patterns of the hydraulic cylinders used require specially matched sealing systems. What they all have in common is a high required sealing effect and a long functional life. Seals and sealing systems from Freudenberg Sealing Technologies (FST) have been reliably meeting these requirements for decades. Market leaders in the industry trust FST quality seals.
Sealing Systems for the Clamping Unit
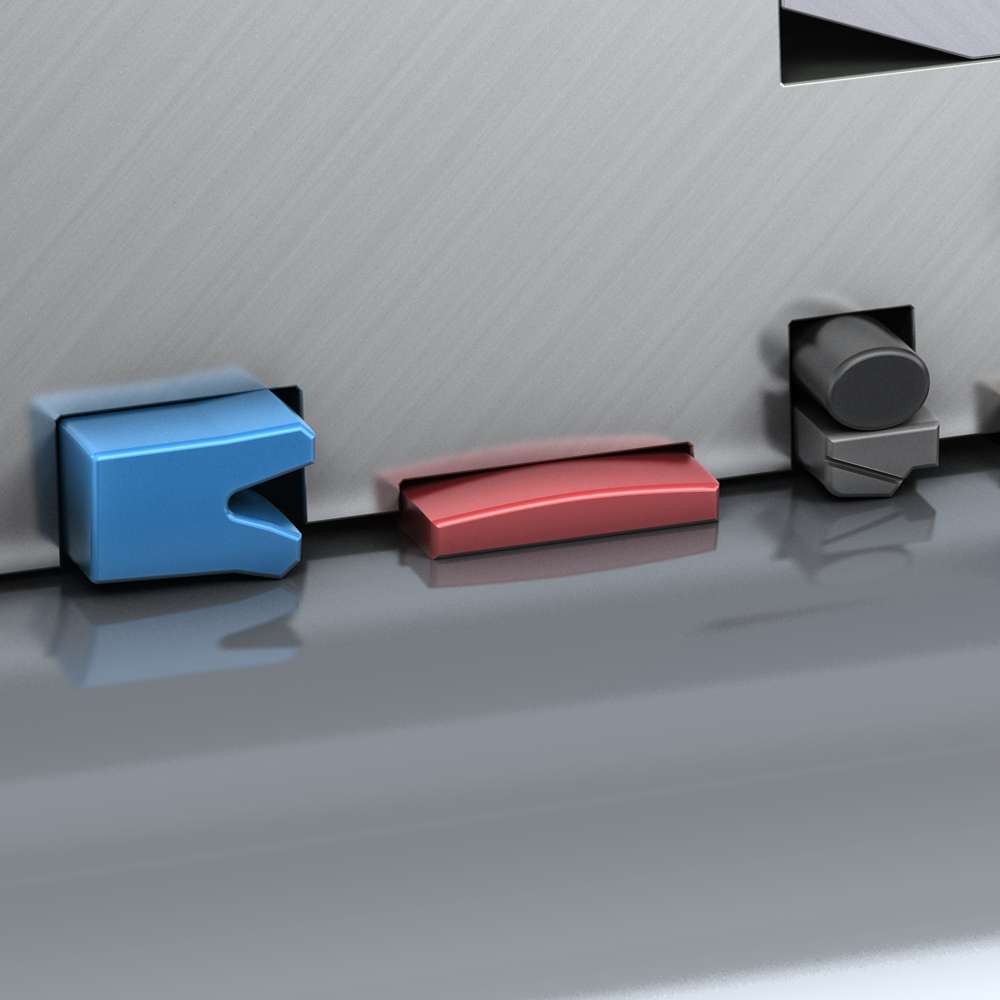
Maximum operational reliability thanks to pressure-relieved primary seal
In the quick-stroke cylinder of the clamping unit a pressure-relieved Merkel® Omegat primary seal is the first choice. It prevents a permanent pressure build-up in the space between the primary and secondary seal due to drag oil. A possible risk of extrusion for both sealing elements and thus failure of the sealing system is averted.
Typical Operating Parameters
Movement: linear
Pressure: 20 MPa
Stroke: 1000 mm
Speed: 1,0 m/s
Rod-Ø: 80 mm
Piston-Ø: 120 mm
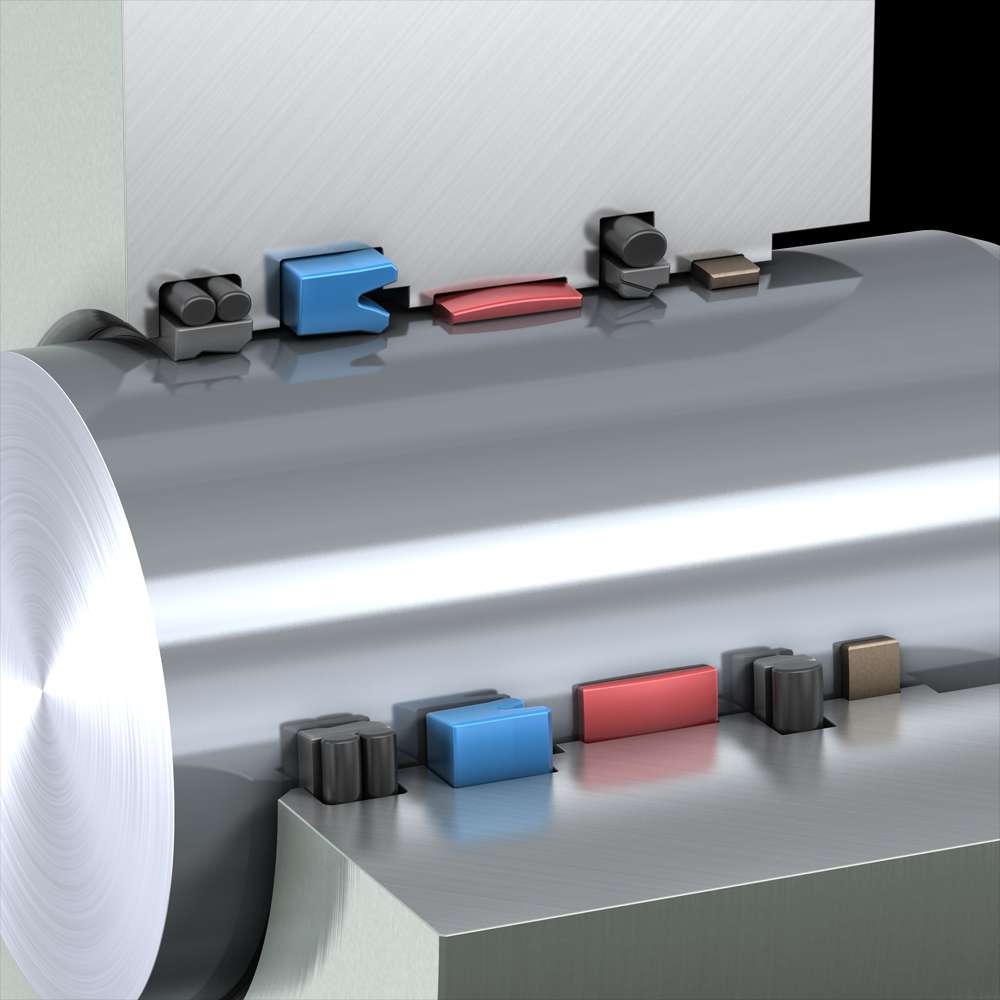
Secure, long holding of the operating pressure
The large-format plunger cylinder of the clamping unit must be able to reliably keep the working pressure for several minutes. Fast, long strokes are required here as well. For this reason, the high-performance sealing system with pressure-relieved Merkel® Omegat primary seal is also used for this application. Longevity is the result.
Typical Operating Parameters
Movement: linear
Pressure: 20 MPa in end position over 20 mm stroke
Stroke: 800 mm
Speed: 1,0 m/s at low pressure
Rod-Ø: 400 mm
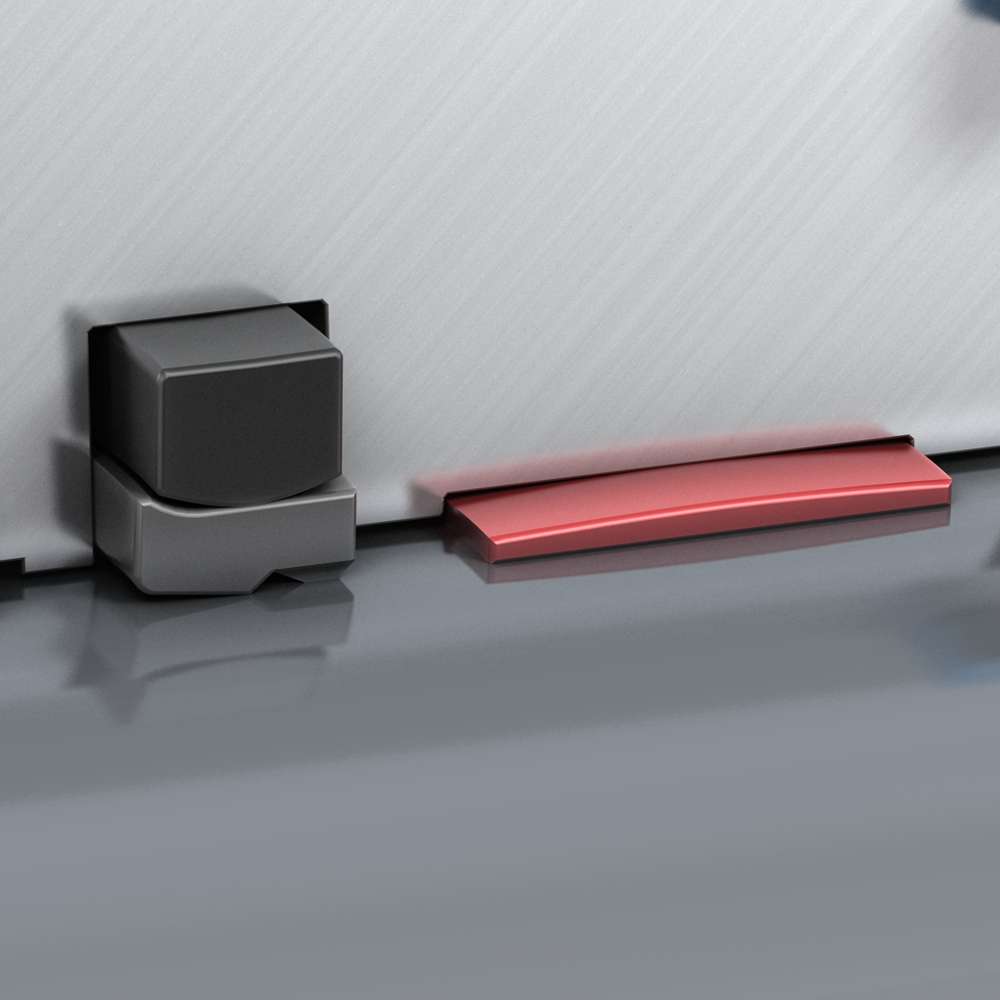
Compensate for insufficient lubrication during short strokes
In the tool clamping cylinder of the clamping unit the maximum operating pressure is applied over a short stroke at minimum speed in the end position. In this operating state, an insufficient oil film builds up under the sealing edges and the guide elements. This lack of lubrication requires the use of suitable sealing materials and a special design of the guides. The in-house PTFE glass and carbon fiber compounds are ideally suited to these operating conditions. The convex geometry of the Merkel® Guivex guide used prevents edge pressure. This favors the intake of operating medium and ensures sufficient lubrication of the guide element, which allows the shortest possible strokes.
Typical Operating Parameters
Movement: linear
Pressure: 20 MPa
Stroke: 5 mm
Speed: - m/s
Rod-Ø: 440 / 760 mm
Piston-Ø: 800 mm
From the Application Directly to the Individual Sealing System Product
Sealing Systems for the Injection Unit
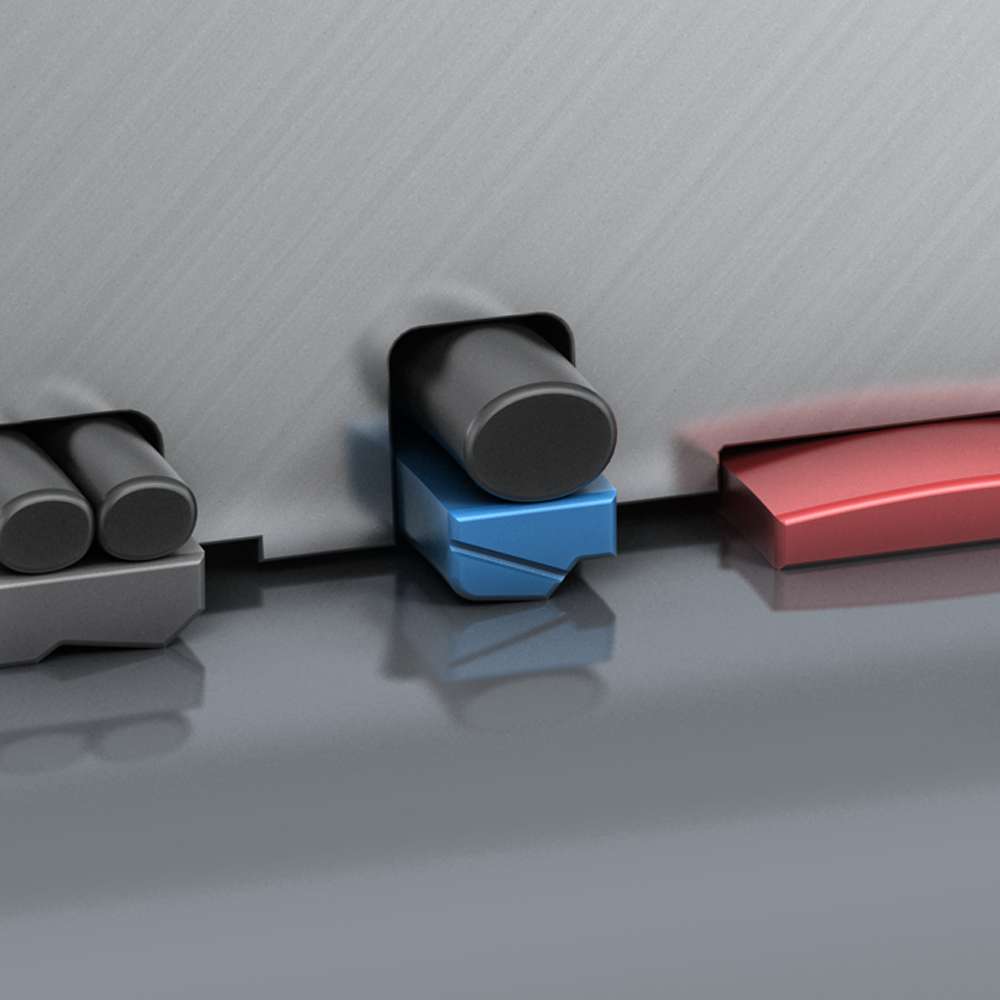
The handling of extremely different stroke speeds
The injection cylinder of the injection unit faces a special challenge: extreme differences in speed and pressure during the forward and return stroke influence the thickness of the remaining lubricant film on the cylinder rod. The oil balance is uneven, especially on the low-pressure side of the hydraulic cylinder. In order to minimize the dragged-out oil film the Merkel® Omegat OMSU-MR PR made of polyurethane is used in this application.
Typical Operating Parameters
Movement: linear
Pressure (injection): 20 MPa / 0,2 MPa
Pressure (retraction): 3 MPa / 0…3 MPa
Stroke: 120 mm
Speed (injection): 0,4 m/s
Speed (retraction): 0,04 m/s
Rod-Ø: 70 / 105 mm
Piston-Ø: 120 mm
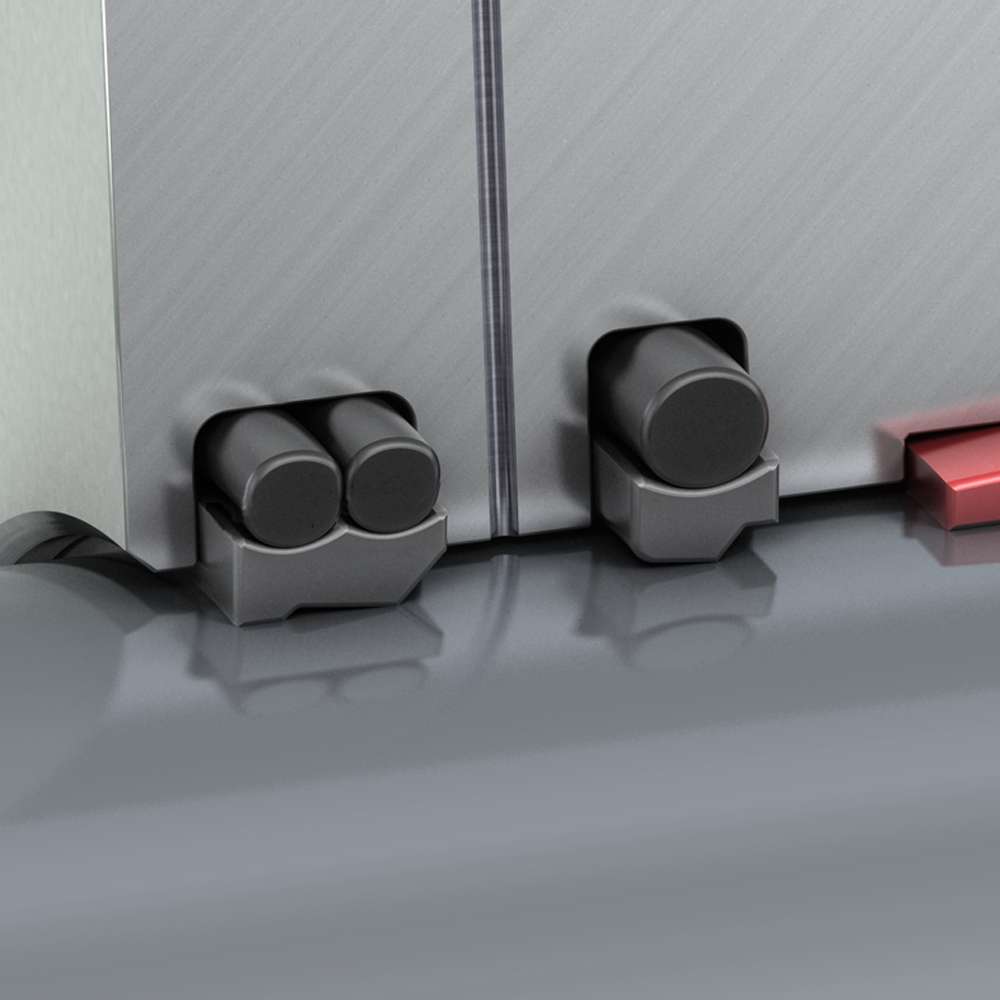
Multifunctional sealing elements for a combined stroke/rotation movement
In the rotary/stroke injection cylinder of the injection unit, the elements of the sealing system master two disciplines at once: a stroke movement with a working pressure of usually 25 MPa and a rotary movement under 2 MPa working pressure for a maximum of 5 seconds. A sophisticated geometry of the wiper and the rod and piston seals prevents undesirable rotation of the elements in the housing during rotation.
Further, typical operating parameters
Stroke: 300 mm
Speed: 0,5 m/s
Rotation Speed: 3,0 m/s
Rod-Ø: 250 mm
Piston-Ø: 300 mm
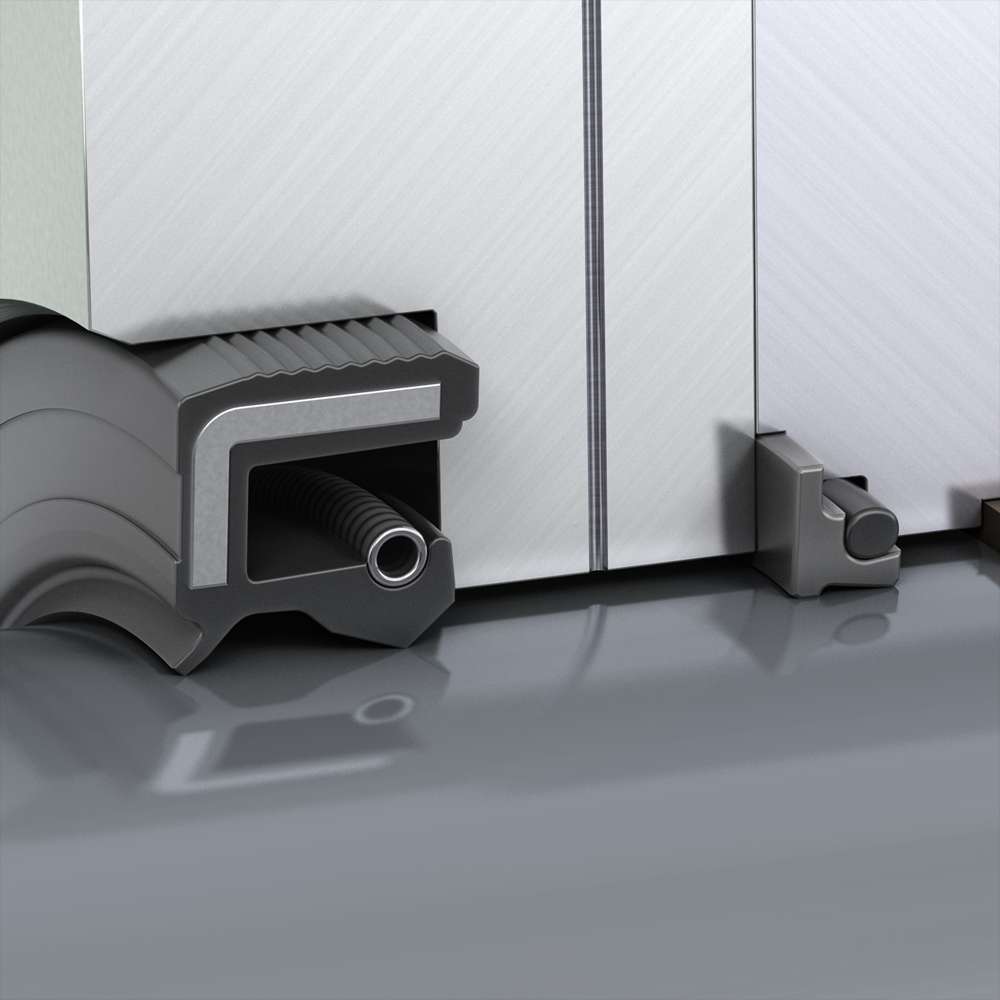
Perfectly matched: Simmerring® + Merkel® Omegat rod seal
In addition to a purely static sealing function up to 25 MPa, the sealing system for driving the injection unit is subjected to a rotational movement with short-term pressure loads of up to 2 MPa. The rod seal Merkel® Omegat OMS-DR HB with its rotary stroke functionality is ideal for this task. In this application, the Simmerring® BAUMSX7, which is designed for purely rotational movement, has a sealing edge that retains the residual oil film and an additional dust lip to protect against dirt from the outside. The Simmerring® is not pressurized in the process.
Discover the new Technical Manual
Become a sealing expert! Our new edition offers an in-depth guide to materials and product expertise, offering a holistic view of sealing technology.
Read now!Services for Injection Molding Machines
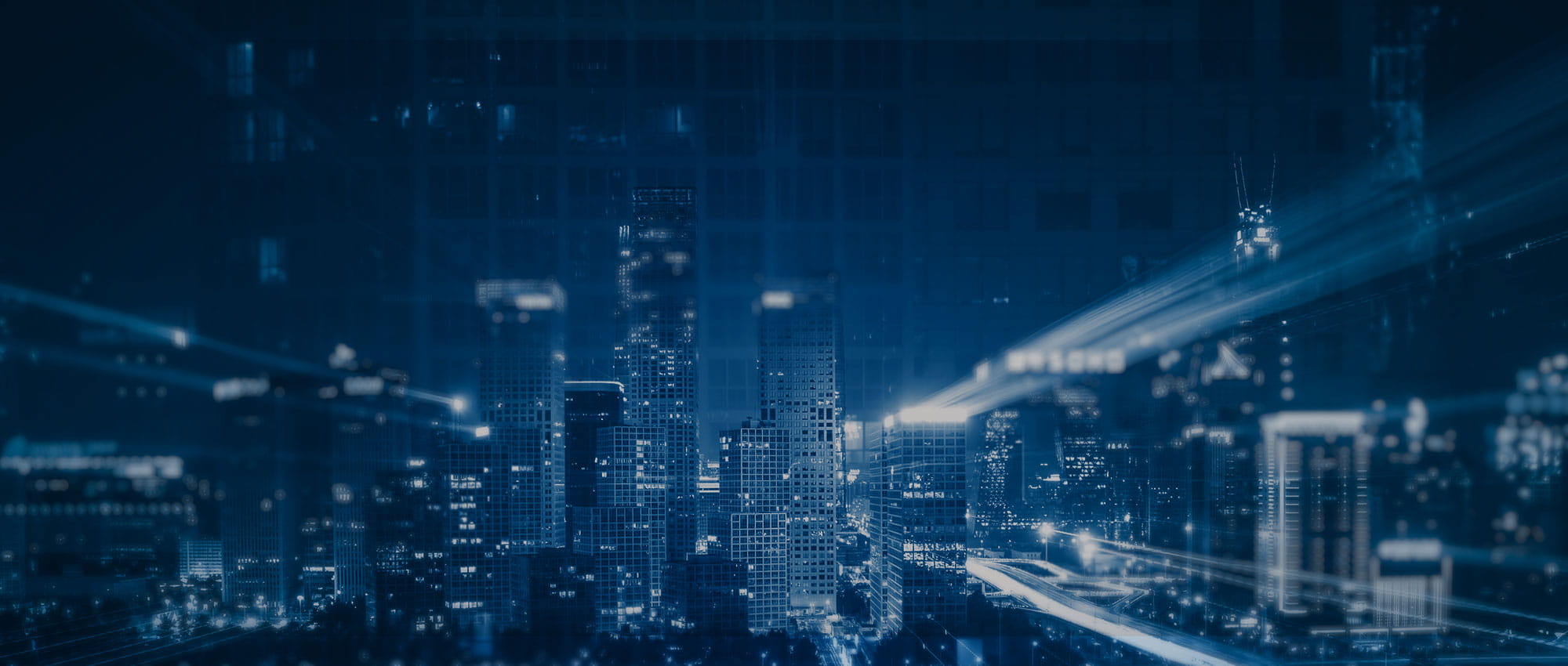
Join Us!
Experience Freudenberg Sealing Technologies, its products and service offerings in text and videos, network with colleagues and stakeholders, and make valuable business contacts.
Connect on LinkedIn! open_in_new