Obtain news and background information about sealing technology, get in touch with innovative products – subscribe to the free e-mail newsletter.
16.02.2016 | News
Delivering data, creating facts
Freudenberg Sealing Technologies (FST) plans to use an IT program to collect information that can help it cut the amount of material used in production.
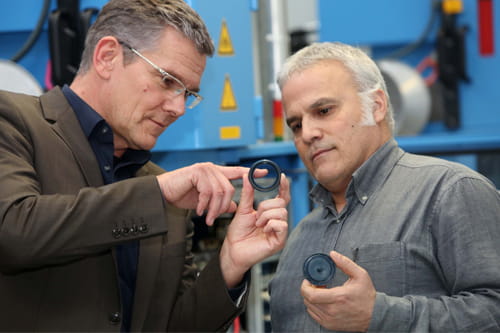
Weinheim. In sealing technology, it all comes down to the right mixture. FST's material expertise helps it assemble the right ingredients in the right quantities for a particular purpose. Many materials are extremely expensive; on average, they account for 40 percent of a seal's manufacturing costs. So eliminating waste is all the more important. This is sustainable because it reduces costs and resource consumption over the long haul.
"We need reliable data to shape our material use efficiently," said Volker Schroiff, Head of Technology Management. He has initiated and guided a master's thesis that, taking O-ring and Simmerring® production as an example, investigates where and in what amounts material "goes missing." Are compounds destroyed because they are not retrieved at the right time and exceed their maximum storage life? How much material is lost when equipment is flushed during product changes? What losses are associated with a particular manufacturing process during forming? What is the proportion of the various types of losses and where are the data located in the SAP system?
O-rings are solely composed of rubber – the technical term is elastomer – and thus are well-suited for use as reference objects. On the other hand, metallic support rings and springs come into use in Simmerring® manufacturing in Weinheim. This makes it more difficult to precisely determine compound losses. "Our goal is to develop a uniform tool in the SAP system that can be carried over to all FST facilities and production processes," Schroiff said. Furthermore, the IT program for Simmerrings must tap into and consolidate more data sources than would be necessary for less complex products. Facts in the form of concrete improvements can be created from the data. FST and SAP representatives participated in a workshop early this year to create a basis for the programming.
FST's new, original "Net-Shape" process shows the success that can be achieved with material conservation. The process eliminates the sprue screen – waste! – since a nozzle sprays the elastomer directly into the mold.
More news on the subject Material Expertise
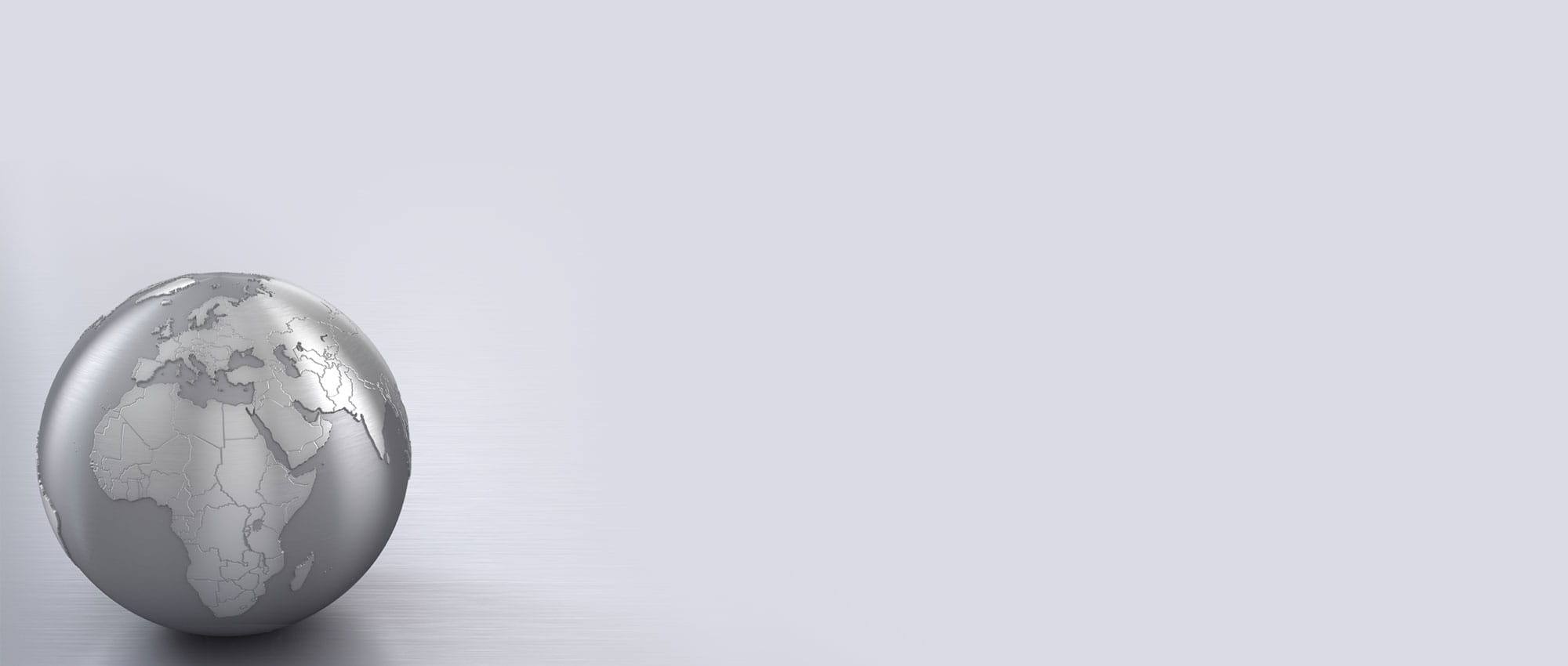
First Hand News
Best of all, keep up with the latest developments
with the Freudenberg Sealing Technologies newsletter.