Obtain news and background information about sealing technology, get in touch with innovative products – subscribe to the free e-mail newsletter.
04.03.2016 | News
Electrical compressor turbo vs. “turbo lag”
Greater driving comfort and performance with low fuel consumption and reduced emissions of pollutants – those are the goals that Pierburg and Freudenberg Sealing Technologies (FST) are jointly pursuing in their development partnership. For the last two years, it has specifically involved an electric compressor – one of the key issues in engine development at this time. Pierburg is hoping the new component can deliver CO2 savings of up to 5 percent, since comparable performance can now be achieved with smaller engines or reduced rotational speeds.
A word of explanation: Diesel vehicles are almost never delivered today without exhaust gas turbochargers, and downsizing without forced induction is hardly conceivable for gasoline engines. But who isn’t familiar with “turbo lag”? When setting off or abruptly accelerating, the turbocharger takes its time to develop power. For a brief moment, the quantity of exhaust gas is insufficient to keep the turbine spinning at a high rotational speed. Due to this low speed, the compressor cannot compress the air with enough force. So far, even two- and three-stage charging systems cannot entirely eliminate this phenomenon.
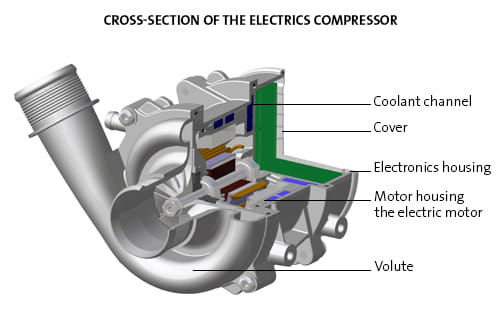
Electric compressors promise a solution. They act independently of the available gas quantity and can be turned on whenever they are needed – to supplement the classic exhaust gas turbocharger when the car is setting off or accelerating, for example. Even at low engine rotational speeds, the charging pressure builds up quickly, and the “turbo lag” very nearly becomes a thing of the past.
“The challenge is in protecting the sensitive electronics and the bearing of the electric compressor from water, dirt and oil reliably and over the long term,” said Key Account Manager Michael Schuhmann. The compressor gear wheel shaft turns at up to 80,000 rpm. In view of the resulting heat and abrasion, sealing with contact seals like the classic Simmerring® is impossible. In exhaust gas turbochargers right now, engineers are generally using piston rings to form a labyrinth to reduce leakage, but the sealing effect is incomplete. For an electric compressor, this is not enough to ensure functioning over the entire service life without additional measures or limitations on installation space.
“Together with Pierburg, we are developing a seal concept that prevents the penetration of air and reagents into the compressor’s interior,” Schuhmann said. “Together, we are on the path to the best possible technical solution for electric compressors.” The advantage: The sealing principle targeted here has already been tried and tested in other regular-production applications at a leading German automaker. “So we already have gained practical experience. We are continuing to work on the solution with Pierburg,” Schuhmann said. “We have already provided various prototype designs that have demonstrated their functionality and reliability in tests at Pierburg and various automakers.” The customer agrees. “The cooperation on this important development project with our partner Freudenberg is developing in a very promising way,” said Stefan Rothgang, senior manager, Auxiliaries and Alternative Drives in Advanced Engineering at Pierburg in Neuss. The first regular production models could benefit from this cooperation in just a few years.
More news on the subject E-Mobility
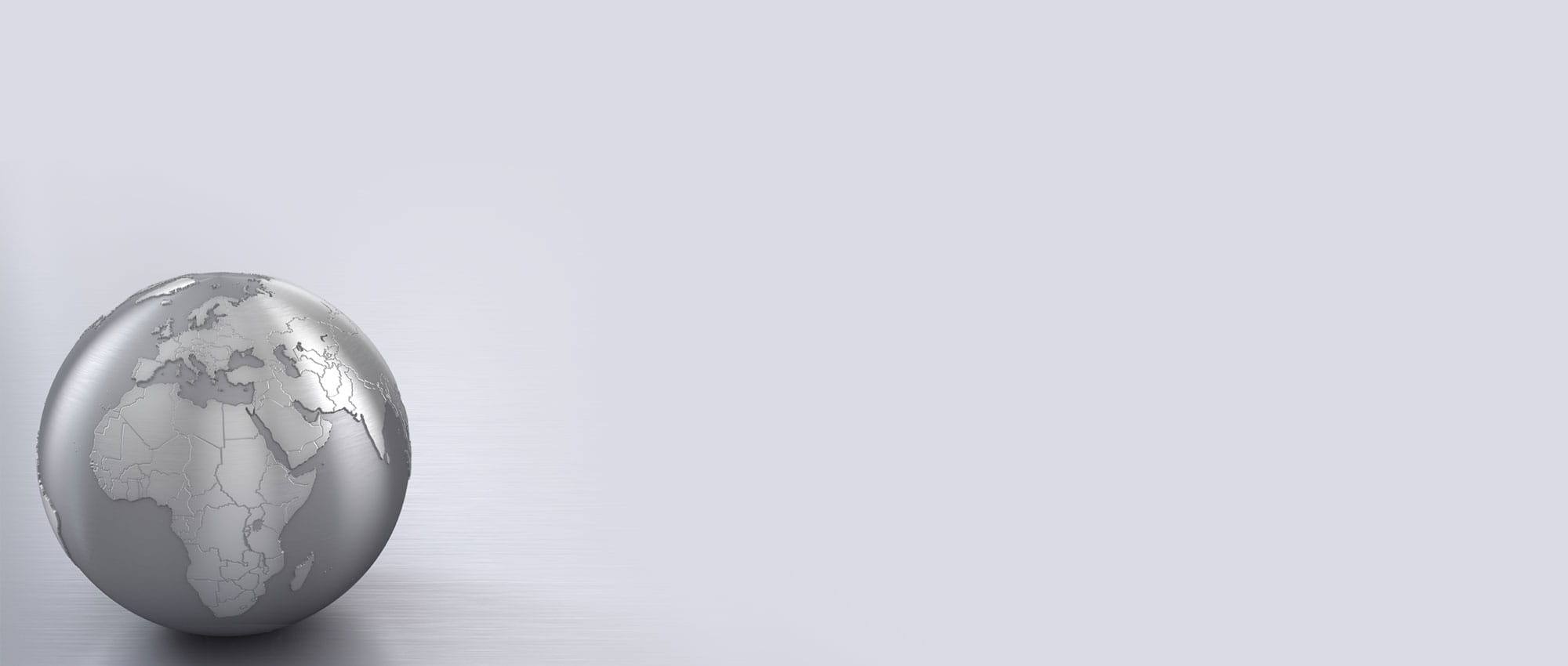
First Hand News
Best of all, keep up with the latest developments
with the Freudenberg Sealing Technologies newsletter.