Obtain news and background information about sealing technology, get in touch with innovative products – subscribe to the free e-mail newsletter.
02.06.2016
Innovative fixing elements for pouch cells
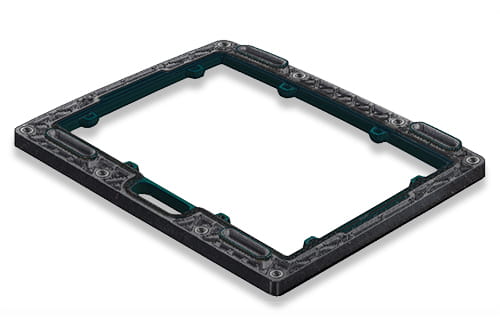
Whether in mobile or stationary applications, batteries are a key industrial component. This is true especially for lithium batteries with their high energy density. Large lithium battery systems are already used in a wide range of applications, such as micro, full and plug-in hybrid cars as well as all-electric vehicles. In industry, batteries can be found in forklifts, robots and commercial vehicles. For cells used in large systems, there are essentially three different configurations: Round and prismatic cells with rigid housings, and pouch cells with a flexible, foil-based covering.
Since pouch cells weigh less than cells with rigid housings, they offer a higher power density and can be made in any size required. They are also less costly to produce and allow a quicker production of the complete battery system. A disadvantage is that flexible pouch cells expand as they charge, which complicates their installation in rigid housings.
Pouch cells with frame seal
Freudenberg Sealing Technologies takes two approaches to developing the ideal solution for embedding pouch cells in modules and housings. One is based on a cell frame optimised for a specific cell size; the second is a profile seal that is flexible in one direction. The main difference lies in the application for which each of these is best suited: The cell frame performs best under rough conditions, while the profile-based concept addresses battery manufacturers’ need to react quickly to changes in cell design. In both approaches, the cells are attached elastically so that mechanical stress is kept as low as possible throughout the life of the battery. A safety function to remove dangerous fumes in the event of an unplanned cell rupture can be added.
In the first concept, a firm thermoplastic frame is being developed to fit the specific cell design. This holds the cell securely and enables the implementation of additional functions like a predetermined break point for cells using “blow-off channels”. If there is a malfunction (such as an internal short circuit) that causes the pressure inside the battery to rise, the break point in the seal around the cell ensures that the gas is released in a predetermined direction. This prevents its contact with live components and the associated risks.
Since high as well as varying temperatures can reduce battery life, the cells can also be cooled through the frame, either by thermally conductive but electrically insulating thermoplastics, or through coolant channels in the frame. These channels are either pipes that pass vertically through the frame, or connectors integrated in the frame.
Flexible profile seal
The second concept for embedding pouch cells in modules and housings uses a flexible profile seal. This further enhances main advantage of pouch cells over round and prismatic cells, namely the fast implementation of new outside dimensions and integration into systems within six to eight weeks. In addition, this approach lends itself to very large production quantities. Tooling costs are also moderate. Two variants are available: A single profile encloses the seam of the pouch cell, or the seam is placed between two adjacent profiles. Enclosing profiles have the advantage of reducing the harmful permeation of gas, both oxygen and water into the cell, as well as electrolyte escaping from it. This significantly increases the lifetime of pouch cells.
Further Articles With These Taggings
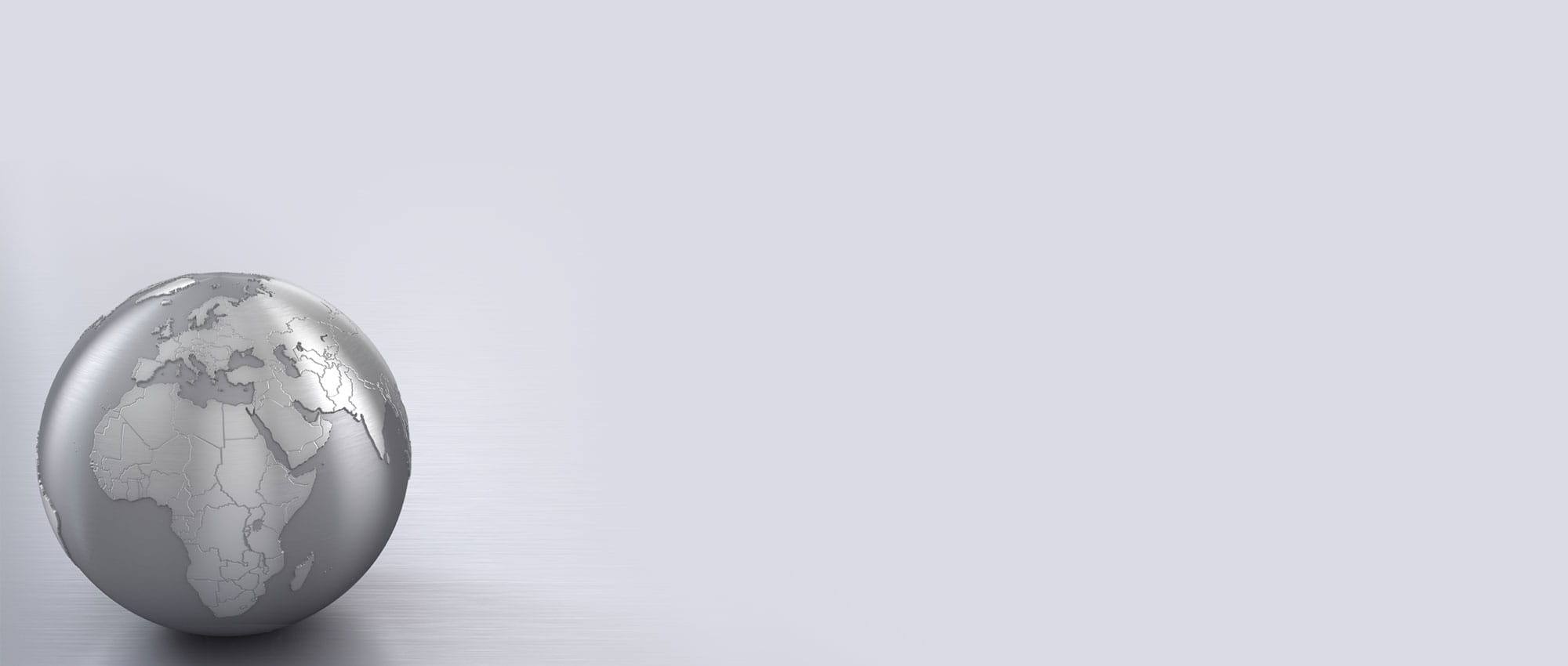
First Hand News
Best of all, keep up with the latest developments
with the Freudenberg Sealing Technologies newsletter.