Obtain news and background information about sealing technology, get in touch with innovative products – subscribe to the free e-mail newsletter.
23.03.2016 | News
Interview with Dr. Ted Duclos - 27 Cubic Meters of Air for One Seal
On January 1, Dr. Theodore G. Duclos became Chief Technology Officer (CTO) at FST. In this role, he is responsible for technology, quality, and components, as well as for Health, Safety and Environment (HSE) at our company. Duclos holds a doctorate and master’s degree in biomedical engineering from Duke University and a bachelor of science degree in mechanical engineering from Stanford University.
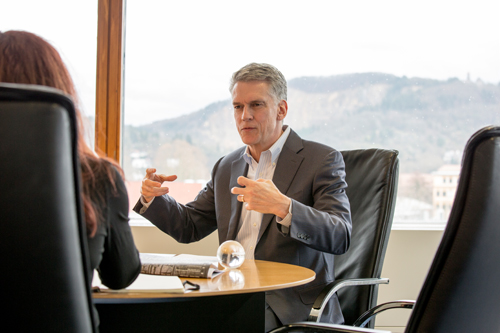
What is your impression after the first couple of weeks in your new position?
First of all, I have been with Freudenberg for nineteen years. So, having had that involvement over a long period of time, I have experienced our company from a lot of different perspectives.
The newest thing for me obviously is being located in Germany and working and living here 100 percent of the time. Since I have known my colleagues on the Board for years and I worked with them over in the Americas as well, it has been an easier transition. It is taking some time for me to come up to speed, but I am learning quickly. I am very appreciative of the help I am receiving from my colleagues and the people in the company.
You are the first American to serve on the FST Board of Management. Is this significant for the Board and for our company?
That’s very important in some ways because I think it shows that the company is truly global and diverse. The fact that someone can come from a completely different region and come into a position and responsibility like this – I think it says a lot for the way the company is developing people. It is very important for me to be a good example. I have spent a lot of time learning German, for example. I am not fluent yet but my goal is to become fluent. For me this is very important – it shows respect for the people of the country to learn about their language and their culture. On the other hand, I hope that one of the things I can bring to this role is a continually expanding view of the company as a whole global entity. I think the company has a fairly good view already, but as we continue to acquire more people in leadership positions who are not from this location, I think we will just naturally bring in new perspectives.
You will serve on the Board as the CTO. What is your responsibility for overseeing?
First, I have responsibility for all the innovation, for technology development, for the engineering side of the company. The second aspect of my role is responsibility for quality and for HSE which go hand in hand together. The third responsibility I will oversee is our corporate components facilities which include mixing, metal stamping and also metal preparation. It's a pretty broad range of things, but primarily focused on the technology and engineering aspects of the company.
How do you view the current state of FST’s focus on technology and innovation?
I think it’s very strong. It’s one of the foundations of our success. We see that through feedback we get from customers who rate us very high, relative to our competitors, in terms of our technical capabilities and innovations. But even being strong and being good, doesn't mean we cannot get better. So I see the continual need to strengthen our technology and keep innovating because the world does not stand still. There are lots of challenges in the marketplaces that we serve. We need to be nimble in order to meet those challenges. We need to respond to trends. Trends like more electric vehicles, and electrification in all kinds of different machines. And different ways of generating power. These present some challenges and some opportunities.
Would you please give an example?
When electric cars first came on the market, people were a bit worried about the ongoing need for our seals. But it turns out that in some cases in electrical vehicles there are cooling systems that require lots of seals. Because of our versatility we have been able to do a good job in innovating in those new areas. The important thing is that we continue to recognize that there are new places for us to go and we need to be open to the fact that we might not currently be serving all the customers that we could be serving.
Material Competence and High Performance Plastics
Another example of this versatility is that we really differentiate ourselves a lot with the materials we use and the development we invest in those materials. A recent example of this type of investment is that, through acquisition and internal development, we are currently building up the ability to compound our own PTFE materials. By doing things like this, we ensure our ability to create better materials at a more basic level. For instance, when we buy materials from a supplier, we get what they have decided they want to give us. So we might not get the most innovative products from them. But when we are making things for ourselves, we have the ability to pursue and create innovations that a supplier might not be interested in pursuing. But for us, those new things could be the magic material that really makes our part work. So material compounding is fundamental to our success. In addition, more recently, we’re even expanding our capability into high performance plastics and other kinds of materials beyond rubber so we can continually create new engineered solutions for people. To a large extent the same thing is going on with our process innovations. There are a huge number of process innovations going on in the company.
Such as?
There are things such as automated part handling as used in the rhapsody system in which a robot loads or unloads the press and even takes over the finishing. We are exploring net-shaped and single cavity molding (see info box). We have really pushed ourselves over the past ten years in these areas and it’s really exciting, to see them come together and start to create a modern factory floor. Process innovation is something we will continue to do a lot. Just like material innovation, process innovation, along with our lean systems, is what keeps us cost-effective – that’s what really keeps us competitive. We have to be really good at manufacturing.
Under your Board leadership, will our focus shift in a new direction?
My background is actually biomedical engineering. That has given me a very diverse and somewhat unique way of looking at technical problems. I am hoping that I can continue to expand our openness to new ideas and to new ways of doing things that bring value to the company and the customer. That’s always important. I think the good thing about our company is we focus on how to make our company successful by meeting the customers’ needs. What I can bring to this is a deep technical knowledge and a different way of looking at some things in order to create fresh approaches. But I do not see a need for a major change in direction. My goal is to make us even better at innovation. And innovation is not just a technical subject. We are working on new service concepts in the company that are innovative as well and we need to make sure we have the right products and processes to support these service concepts.
Innovations Drive Us Forward
I mentioned previously that we have a lot going on in material and process innovation. We must not forget, however, that we produce and sell products and that we need to keep innovating in the area of new products. As I have traveled around in my first months here, I am very pleased to see a significant amount of new product innovation going on in the company. We need to make sure that these launch successfully and that we are continually filling the pipeline through focused R&D projects. I don’t think we have been as successful at introducing new products in the past as we would have liked, however, I think we are well positioned for success now and I see it as my responsibility to ensure that success.
What are the major factors for sustainable success for a technology-driven company like ours?
I gave a talk on sustainability in the U.S. a couple of years ago and my theme was that sustainability has to mean more than environmental sustainability. Sustainability has to mean sustaining the business. While environmental sustainability is very important there are many things that go into a sustainable business. From my perspective, the foundation of our sustainability is in our Guiding Principles because they state what we believe in as an organization. The Guiding Principles are really what will sustain our company over a long period of time. Of course, innovation is one of the guiding principles and successful innovation requires us to invest – especially in people. Successful innovation results from a combination of factors – investments in people, in capital, laboratories, technology capabilities, partnerships and outside collaborations. It even involves creating a culture that encourages us to look at fresh approaches. We need to continually renew our business in order to sustain it long-term.
But how can we achieve this?
Well, we know we are in the sealing business and that provides us with focus. That’s another aspect of this – we have to make sure we are focused, and we understand what it is that our customers value. We open our minds to new possibilities when we remind ourselves that although we think our customers are buying rubber seals, what they are really buying is the function of the seal. If we keep that in mind, we’ll keep renewing ourselves because we will keep thinking of new ways to achieve the sealing function, even if these new ways are far different from our current methods. We also need to keep our eyes open to the outside world and avoid becoming complacent by thinking we know everything. These ingredients are the key things for sustainable success and the company has obviously done it really well over a long period of time. My goal is to push that just a little bit more by maintaining and sharpening our focus on the things that really add value.
How will your experience drive FST’s approach to technology and innovation?
My educational background is in biomedical and mechanical engineering and for me that educational experience was really great. I studied a lot about biological systems which, as an engineer, was very humbling because it’s unbelievable what biological systems do. These studies gave me a somewhat unique perspective regarding what is possible in the world of science and technology because biological systems have, through millions of years of trial and error, evolved fantastic ways of solving problems that human engineers are still not able to duplicate. This outlook along with my natural curiosity has always led me to look at problems and solutions differently. Early in my career this was very helpful in my work developing magnetorheological fluids and more recently, at FNST when I was responsible for the technical organizations and then in my role as a general manager of a global division. These experiences will help me lead the organization to look at fresh solutions.
Reorganize Materials
As an example of this, a couple years ago I started really thinking about the task of manufacturing. I thought, what is really going on when we manufacture a product? The answer is that the task of manufacturing is to reorganize materials. I then started thinking about the atoms that make up a polyurethane seal: carbon, nitrogen, hydrogen and oxygen and I realized that these atoms are in the air all around us. At that point I sat down and did a calculation and I realized that within a 27 m³ cube of air there are enough oxygen, nitrogen, hydrogen and carbon atoms to make a polyurethane seal.
And how?
You just have to reorganize the atoms. The point is that the materials are all there. How does this relate to manufacturing? Well, the challenge in manufacturing is always to reorganize materials. So I started thinking about how to do such a thing with the atoms in the air and I realized that there are already machines that do this sort of thing all the time all around us – they are called plants. Plants take materials out of the air, they take materials out of the ground, and they manufacture things – fruit for example. And they do this with energy from the sun, but without long supply chains. So I wondered if it might be technically feasible to take the atoms out of the air and make our seals.
Polymers from the air
I did some research and, to my surprise, I found that there are people working on every key step of this challenge, all the way up to making polymers out of the air. There are technologies being developed that take carbon dioxide out of the air and polymerize that carbon dioxide to make polymers. Knowing this, maybe we can start envisioning a whole different way of doing things. While it’s not immediately feasible, the interesting thing is that there are companies out there working on this kind of thing. In fact, even today, we make some seals that come from polymers that are biologically based.
Given my background, I don't get stuck thinking that the way we do things today is the way we will do them forever. In the example I give, if it is feasible, all we need is energy, water and air and if we can organize the atoms in the right way we can make seals with a very different manufacturing model. Maybe over time that will lead to different ways of actually doing our business. It’s important that we keep our minds open to things like this. Because, as I have learned from experience, if something is possible, someone will do it regardless of how it challenges the status quo. We always have to keep that in mind, even if it requires us to work very differently from how we work today. If it’s possible to do and it will affect our business, we need to make sure that we are the ones doing it!
What are your innovation and technology priorities for the various regions in which we operate?
Some priorities will differ depending upon the needs of the customers in the regions and then there will be priorities that are important to global customers and these will become global priorities. We need to make sure that we understand what is going on in the regions and we need to understand what is global. Therefore, we have to have a technical presence in each of the regions that we are operating in, because sometimes different regions do have different requirements. We have technical centers in Europe and the U.S., and we have a strong technical relationship with NOK in Asia. We have a worldwide network of resources and technical services. I think one current item that is important to us is how we build technical capabilities in China.
Being a global company, how do we maintain the technical capabilities on the right level in the various different regions?
This is the task of the global leaders such as myself and others who have global organizations. As I stated previously, the people are the key to success. We need to ensure that the missions of the regional technical capabilities are clear and that the organizations are staffed appropriately. Then there is the need to coordinate activities globally. We do this through technical exchange meetings and global organizations.
How will you focus on the area of HSE going forward?
Having a focus and having excellence in HSE is essential to achieving excellence in operations. It all starts from that. The company is committed to providing a healthy working environment and to help maintain healthy communities in which we work. This goes hand in hand with our Guiding Principles. In fact, HSE is basic to our Guiding Principles. Also, when we focus on improving safety and environmental items, we find that these are also very good business practices. For instance, good quality starts with good safety.
In other words: Poor quality is like an accident?
Yes, a quality problem is kind of an accident. If you have the basics and the fundamentals of preventing accidents and understand how to look at potential accidents, that's the basis for understanding how to have a good quality system. They really go together.
In terms of the environmental focus, a lot of environmental efforts are associated with the elimination of waste. Good operations eliminate waste and lean manufacturing is all about eliminating waste. So again, good environmental practices are just good business practices. If we can find ways to eliminate waste, we are saving money. There is no question about this. We are also reducing variation which means we make higher quality products. This is something that businesses have discovered over the last 30 years.
Excellence Is the Key
To summarize, I think the key thing is that the focus on HSE means we keep pushing ourselves to excellence in our systems, our capabilities, providing the right kind of workplace for people to work in and provide the right foundation for the business as a whole.
What is necessary to strengthen our partnership with NOK and the other Freudenberg companies?
I think the Board of Management has done a really good job over the past several years in making our relationship with NOK better and better. Through these efforts, we have developed a closer relationship. I think both companies are benefiting through the technical exchanges and the establishment of real global standards in some areas.
The nineteen years that I have been with the company were, with the exception of the past few months, within FNST. I have had a lot of experience working with NOK and I eventually served as the president of the joint venture, FNST, between NOK and Freudenberg. My experiences have taught me the value of partnerships. When you are in a partnership you have to find ways to agree, you have to find ways to create consensus and this can lead to new and better ways of working. Of course, we each take the lead in different parts of the world, but that is by agreement. The way to strengthen this relationship is to continue our open dialog, consensus building, and technical exchanges. NOK is a world-class manufacturing company which is a big advantage for us.
More news on the subject People
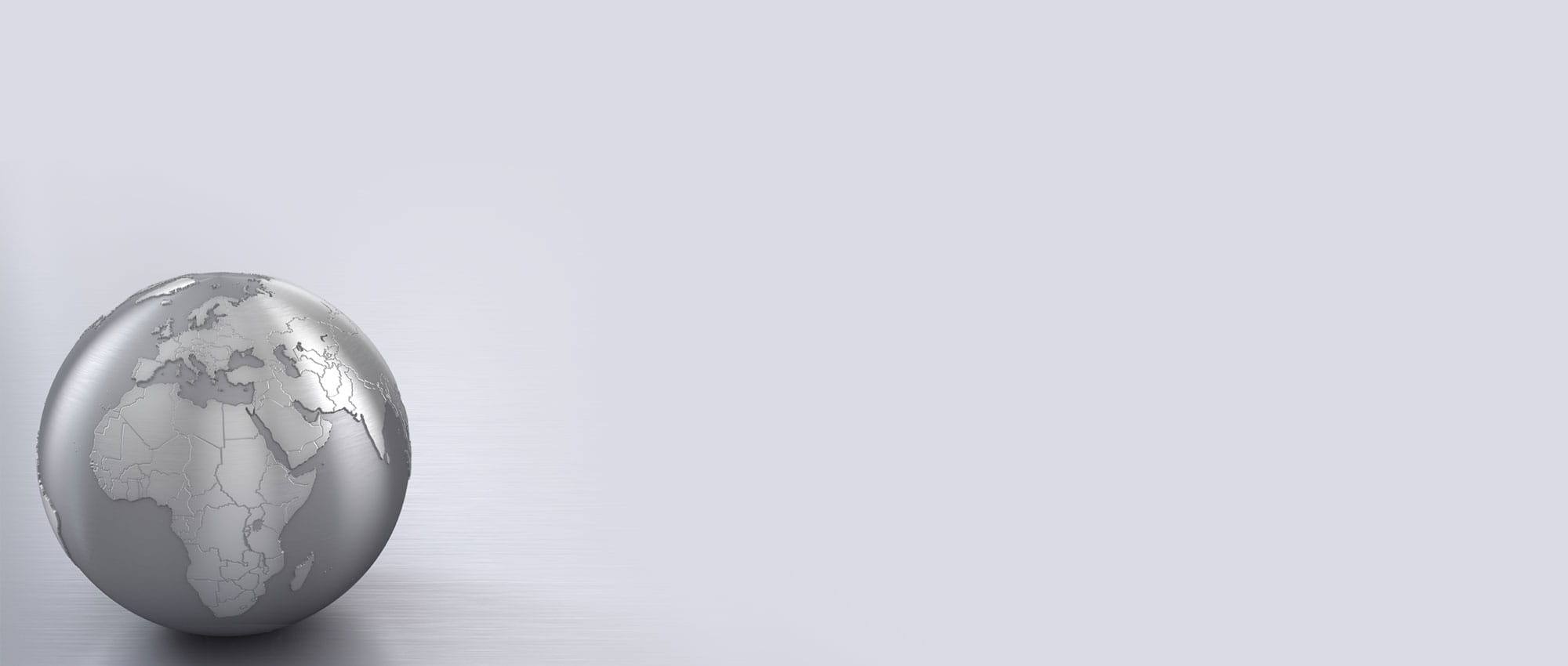
First Hand News
Best of all, keep up with the latest developments
with the Freudenberg Sealing Technologies newsletter.