Obtain news and background information about sealing technology, get in touch with innovative products – subscribe to the free e-mail newsletter.
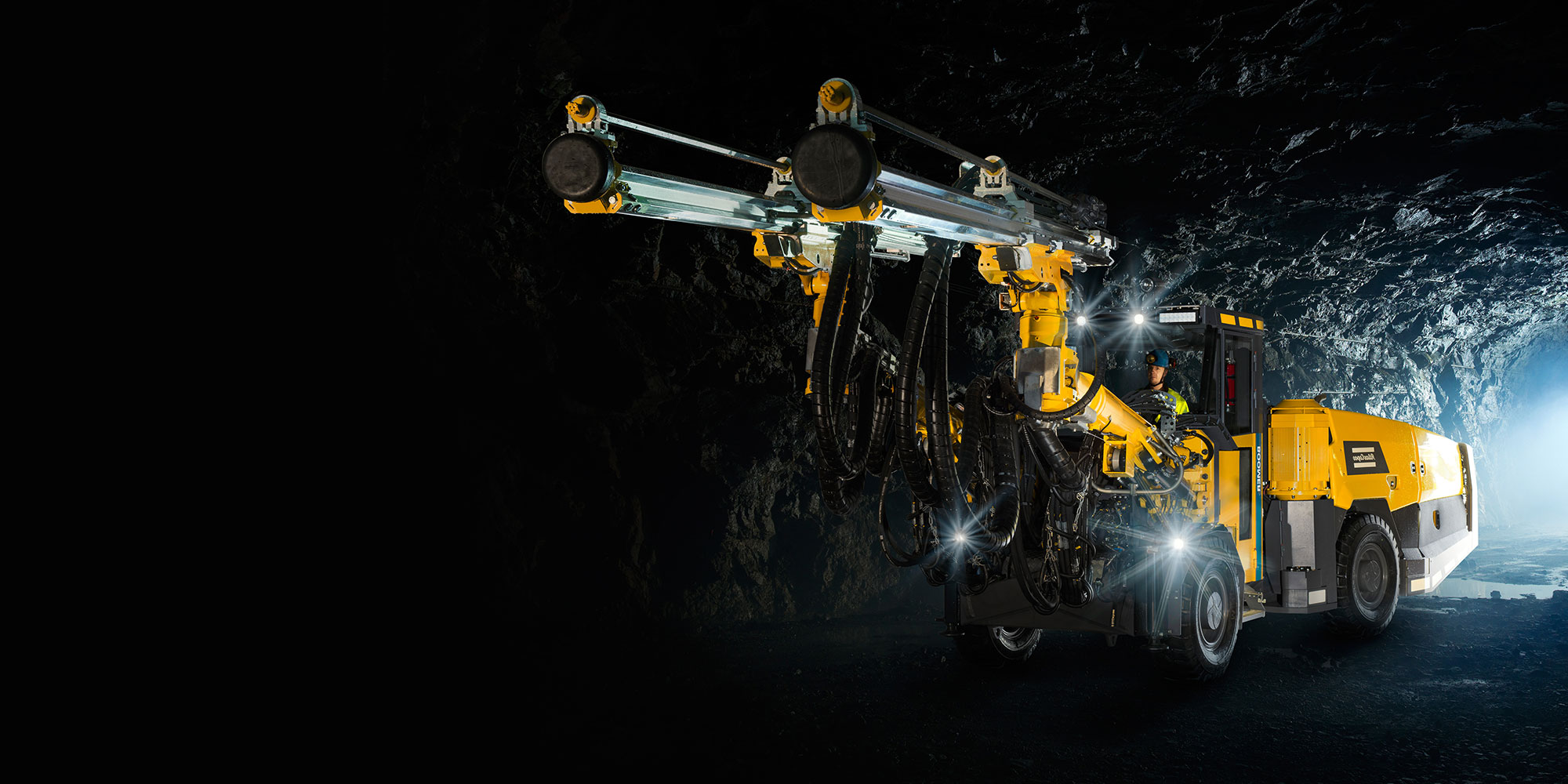
13.06.2017 | Story
The Right Seal for Powerful Forces
Today equipment used in the construction industry is supposed to have a long lifespan and require maintenance less often. One starting point: efficient sealing systems.
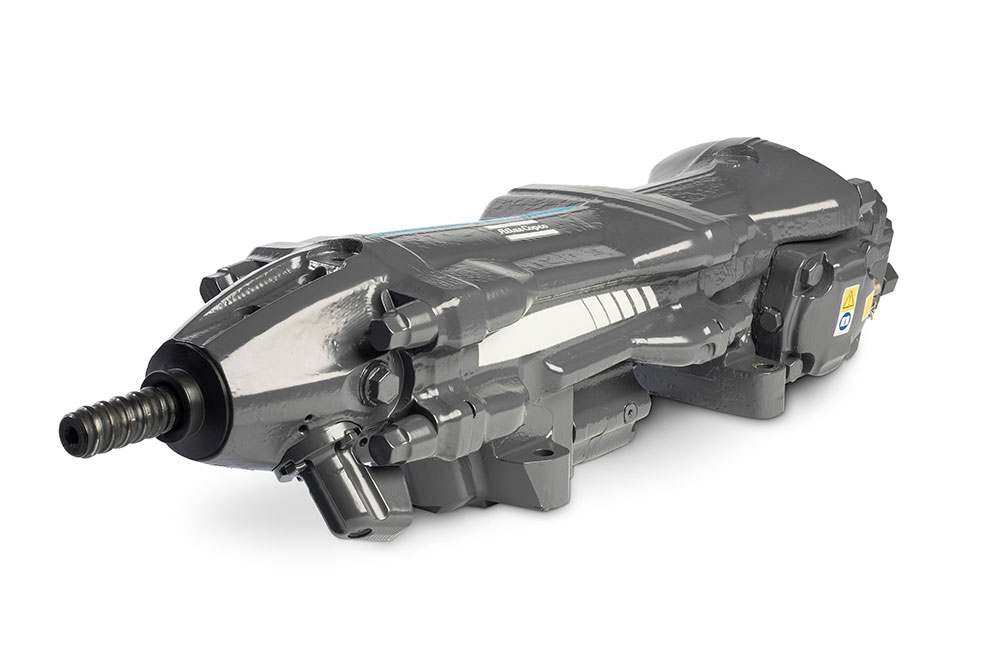
The Goal: To Double Maintenance Intervals
The drill bits used in Atlas Copco equipment hit the rock up to 140 times per second. The force, which is applied with pinpoint precision, is the equivalent of about 25 tons. With such brute force, wear is unavoidable. That’s why the machines had to undergo a general overhaul after every 400 hours of operation. For the buyers of a typical rock drill, this involved a temporary machine shutdown and the expense of maintenance. Responding to the situation, Atlas Copco pursued an ambitious goal for several years: to extend maintenance intervals to more than 1,000 operating hours. In this way, the machine could be run for more than a year without maintenance.
Analysis: Damage Evaluation
Seals were an important piece of the puzzle in extending the maintenance-free interval. If they are damaged, the power that the drill can apply steadily declines. It was a problem that the sealing experts at Freudenberg Sealing Technologies tackled. Gunnar Pettersson, a member of the company’s sales organization who supports Scandinavian customers, guided the search for an answer. “Engineers from Atlas Copco and our developers teamed up to analyze all the damage that occurred during operation. This was the only way for us to precisely understand the harsh operating conditions and create a solution.”
It was the right approach to tackle a single component critical to success with all our strength instead of dissipating our efforts.
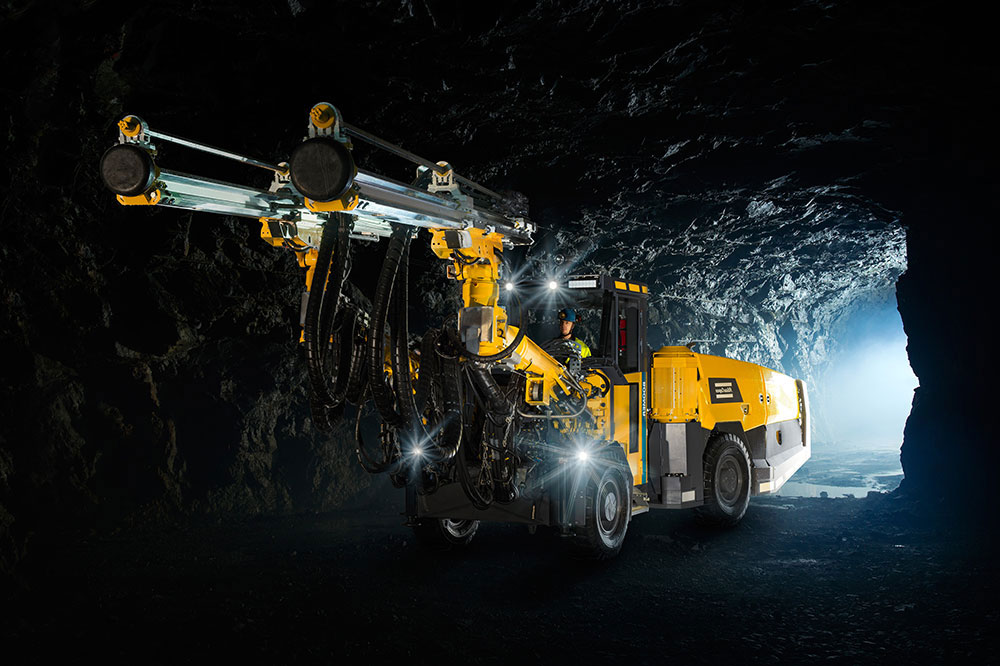
The Solution: A Re-conception of the Seal
All the participants paid special attention to the piston that drives the drill bit. The piston not only moves forward and backward while rotating slightly around its own axis. This represents an enormous load on the sealing system as well as on the bit. “Our analysis even surprised us,” Pettersson admitted. “The seal rotates fairly constantly at 300 to 400 revolutions per minute,” which is why it had to be fundamentally reconsidered. Besides changing its material composition, Freudenberg Sealing Technologies reworked the seal’s design for this application. The project was a success: The seal delivered the results that everyone had promised. This was proven in test-stand trials and usage under real-life conditions. The new machine with its specially fabricated seal had to prove itself underground for an entire year. Pettersson said it was the right approach “to tackle a single component critical to success with all our strength instead of dissipating our efforts.” The machine is now on the market and already in use in mines.
More news on the subject Material Expertise
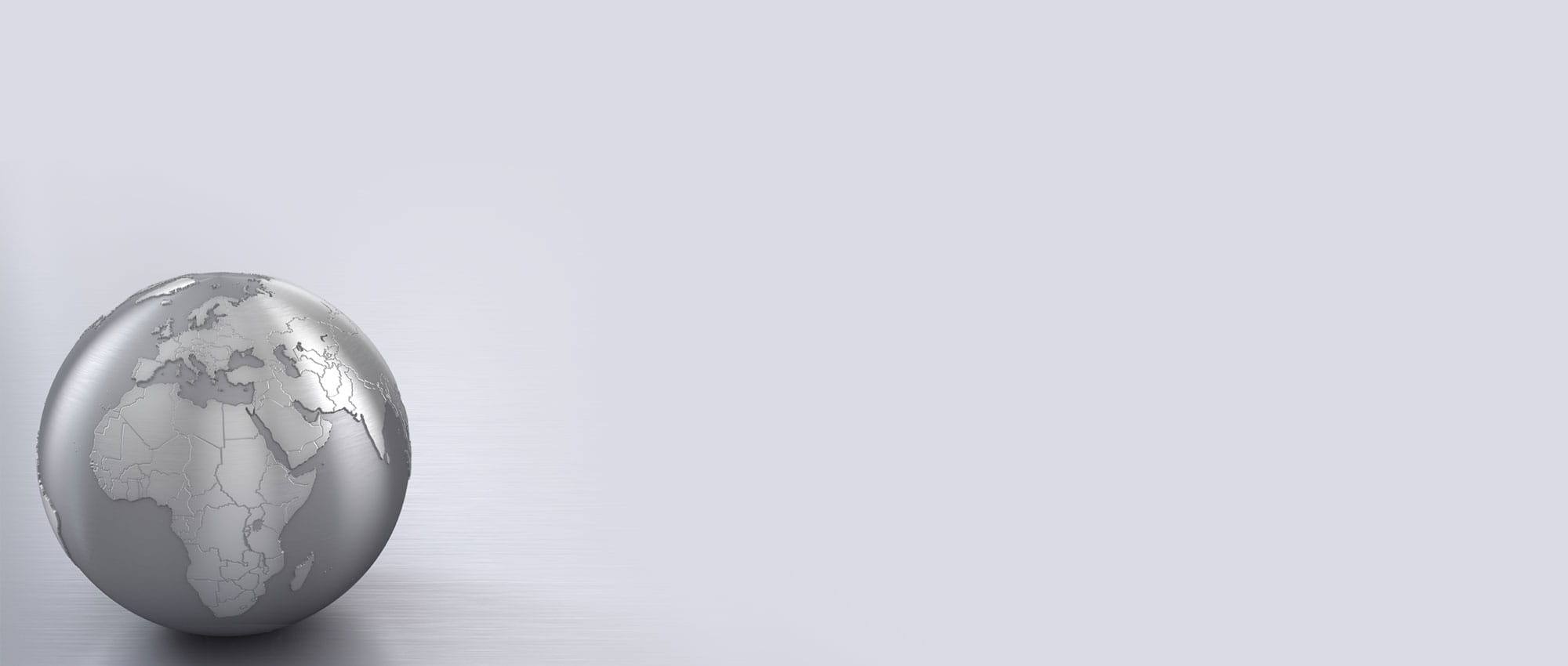
First Hand News
Best of all, keep up with the latest developments
with the Freudenberg Sealing Technologies newsletter.