Obtain news and background information about sealing technology, get in touch with innovative products – subscribe to the free e-mail newsletter.
26.11.2018 | News
Materials for the World
Authorities in every country strictly limit the kinds of materials that are allowed to come into contact with food. In the past, China has followed the regulations of the United States and the European Union, but it has now enacted its own standards. The material developers at Freudenberg Sealing Technologies accepted the challenge, and their work has resulted in materials that can be used worldwide.
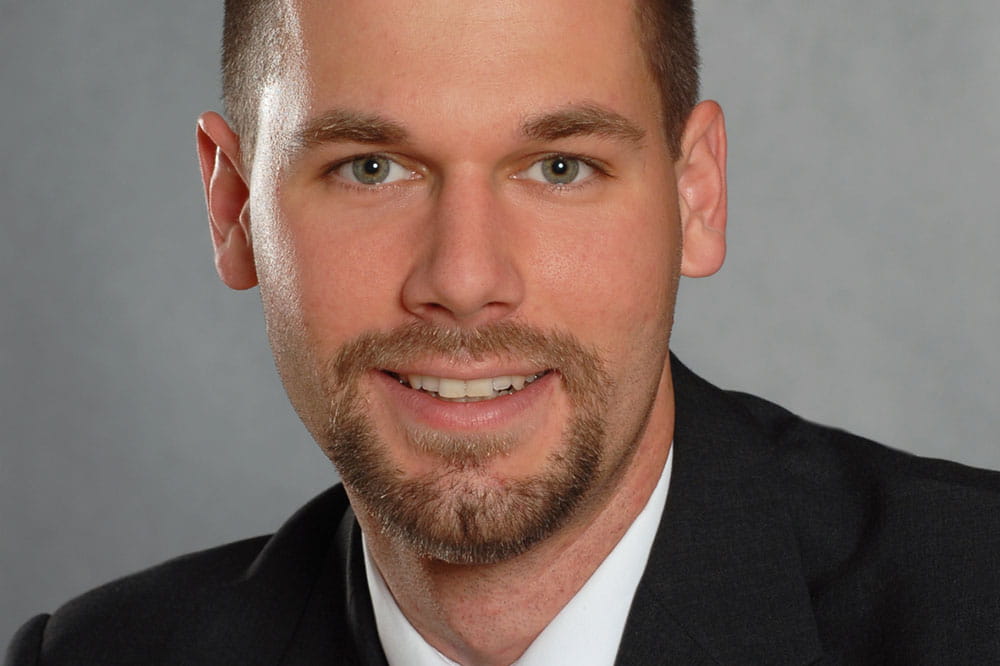
Christian Geubert, expert on the materials used in food processing and applications engineer at FST
If you have ever enjoyed a refreshing glass of mineral water on a hot summer day, you were ready to assume that your beverage contained no contaminants. Regulators enforce that level of purity. The industrial facilities that are used to produce and process foods have to meet strict hygienic requirements. This also applies to the seals that come into contact with beverages. In China, approvals from the U.S. Food and Drug Administration (FDA) and European Union (EU (Reg.) 1935/2004) have sufficed so far. But in the fall of 2016, the country laid down its own standards. For example, based on a “white list,” the Chinese standard GB 9685 determines what components may be contained in seals. Another standard, GB 4806, sets the basic requirements and defines sensory inspection and migration testing for sealing materials. The second category involves endurance tests: Elastomer materials are exposed to substances used in the food industry, such as acids or fatty media.
Comparing white lists
“With the new standard in China, we were facing an important issue,” said Christian Geubert, a Freudenberg Sealing Technologies expert on the materials used in food processing and an applications engineer in the process industry field. “Should we develop a new variant that is exclusively geared to the Chinese market or a material that takes all the requirements from the U.S., the EU and China into account?” The material developers chose a global approach. “In the end, many of our customers operate globally. A material that covers all the requirements is a great advantage for them,” Geubert said.
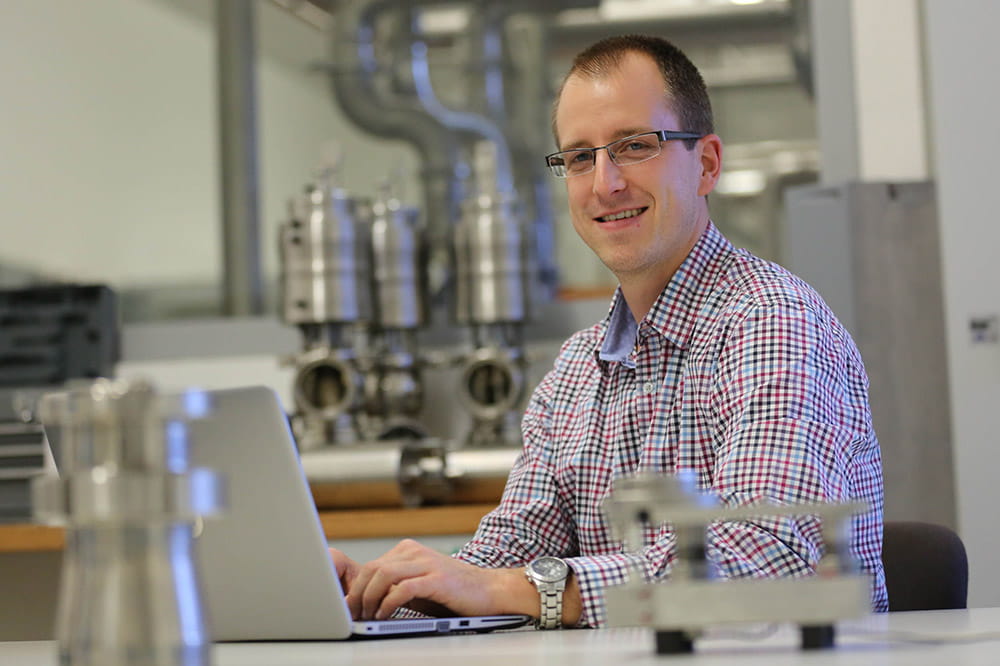
As they began developing a new recipe for EPDM synthetic rubber, the engineers first looked at the ingredients of proven material compounds and asked themselves: Are their component materials on all the white lists – even the Chinese list, which officials kept relatively short? Using this approach, they continued to develop existing materials into variations that conformed with the Chinese standard. “An elastomer compound consists of numerous components that – when skillfully combined – ultimately give the material the desired characteristics, such as media resistance, a long service life and good processing behavior,” said Dr. Robert Rotzoll, the Freudenberg Sealing Technologies expert who developed new compounds to meet the new standards. “The challenge was to develop high-performance materials that can perform the balancing act between excellent media and aging resistance on one hand and global food compliance on the other – and do it all with the limited options available.”
Application-oriented tests at the labs
Two elastomers, 75 EPDM 386 and 85 EPDM 387, were the result. They can be used nearly worldwide as a material for O-rings and machined formed parts in food industry equipment. “In addition to the tests in government labs, we carried out application-oriented tests at the Freudenberg lab in Weinheim,” Rotzoll said. “It was shown that the characteristics of the new materials are very similar to those of the proven ones.”
Equipment has to be sterilized regularly with steam heated up to 160°C so that no bacteria or other microbes can establish themselves in food-processing equipment. To minimize downtime, the sterilization mostly takes place in closed equipment – as does the cleaning. This is largely a strategy to deal with the frequent product changes. The cleaning is carried out with aggressive media such as caustic soda or nitric acid. Freudenberg’s special tests ensure that the sealing materials are resistant to steam, acids and alkaline solutions – and that they are up to the task of meeting the process industry’s high standards. The materials are exposed to the respective media over periods of 168 and 672 hours and then examined for their physical and mechanical characteristics.
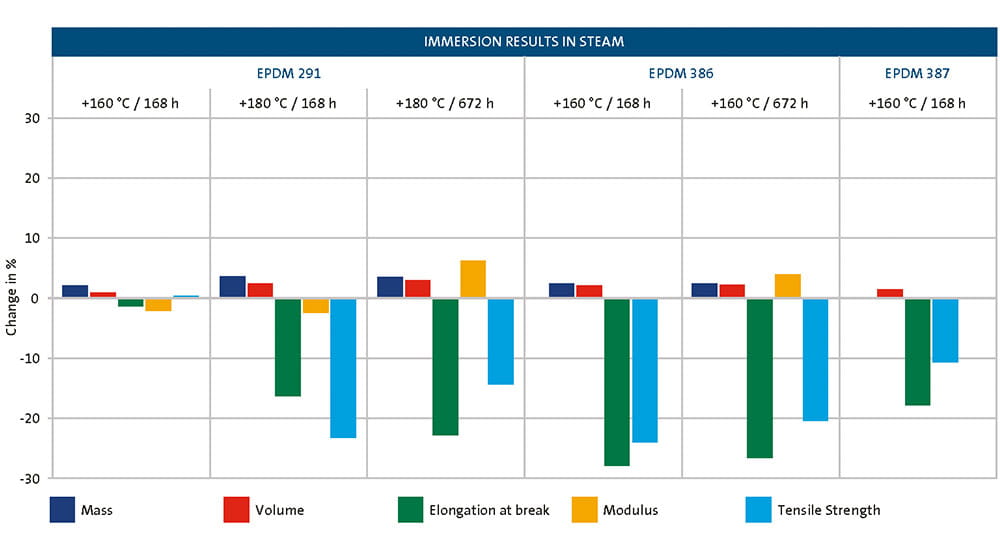
Fig. 1 Storage tests in steam
A comparison of the physical characteristics – that is, weight and volume before and after the tests – offers an indication as to whether the material has absorbed cleaning agents or has lost ingredients. But the values are merely aggregates. When both things happen at the same time, the weight and volume are absolutely the same, although the material has changed in an impermissible way. With this in mind, the materials’ mechanical characteristics are explored. If the polymer network has changed, its elongation at break – and thus its length at the point that the material tears during stretching – its tension value and tear strength at the moment of breakage will change as well. In static tests, weight and volume can only fluctuate a maximum of 10 percent. Maximum fluctuations of 30 percent are permitted for mechanical characteristics. The prescriptions are even more stringent in dynamic tests: Physical characteristics can only vary by 5 percent, and mechanical traits by only 15 percent.
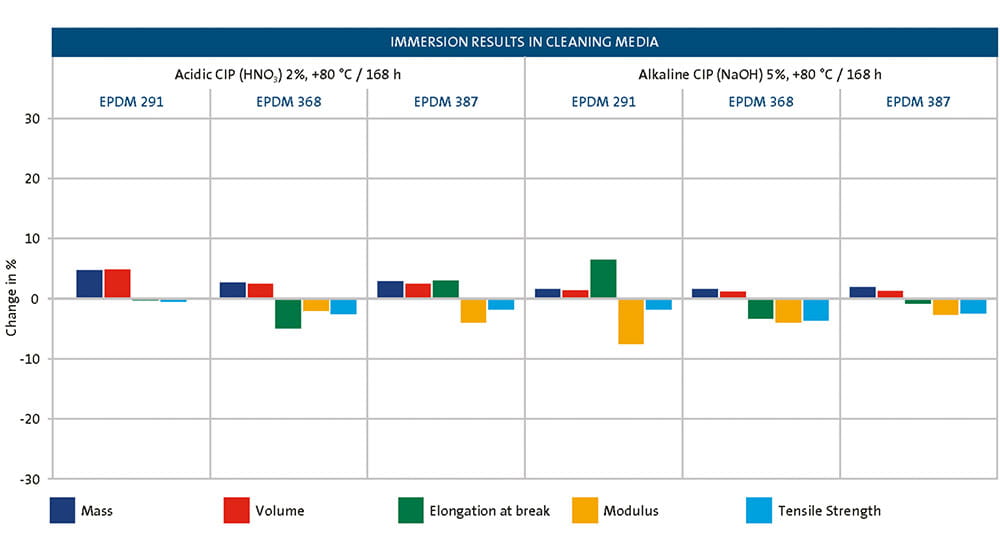
Fig. 2 Storage tests in cleaning media
Compared to earlier tried-and-tested materials, the new compounds that conform to the Chinese standard exhibit very good behavior in steam. For example, as shown in Figure 1, 75 EPDM 386 achieves similar values after 672 hours at 160°C as the tried-and-tested 75 EPDM 291 at 180°C. After a shorter test run of 168 hours, 85 EPDM 387 even displays somewhat smaller changes in its mechanical characteristics. “You can thus assume a temperature stability that is about 20°C lower in steam, but this is totally sufficient for the usual sterilization conditions,” Geubert said. The tests with cleaning agents, caustic soda and nitric acid are shown in Figure 2. They demonstrate that the mechanical characteristics of the two new materials are completely comparable to the previous compounds. In the physical tests, they even produced somewhat lower weight and volume changes; all the changes are under 5 percent. Moreover, 75 EPDM 386 and 85 EPDM 387 (Figure 3) are also impressive in comparisons with the most common competitive materials. Just like 70 EPDM 291 – which was also examined – they show smaller changes in their characteristics after storage in hot steam. At the same time, the test conditions at 168 hours and 160°C were considerably more demanding than those in the competition’s testing at 70 hours and 140°C. All in all, that means the new seals that are compliant with Chinese requirements meet the customary market standards.
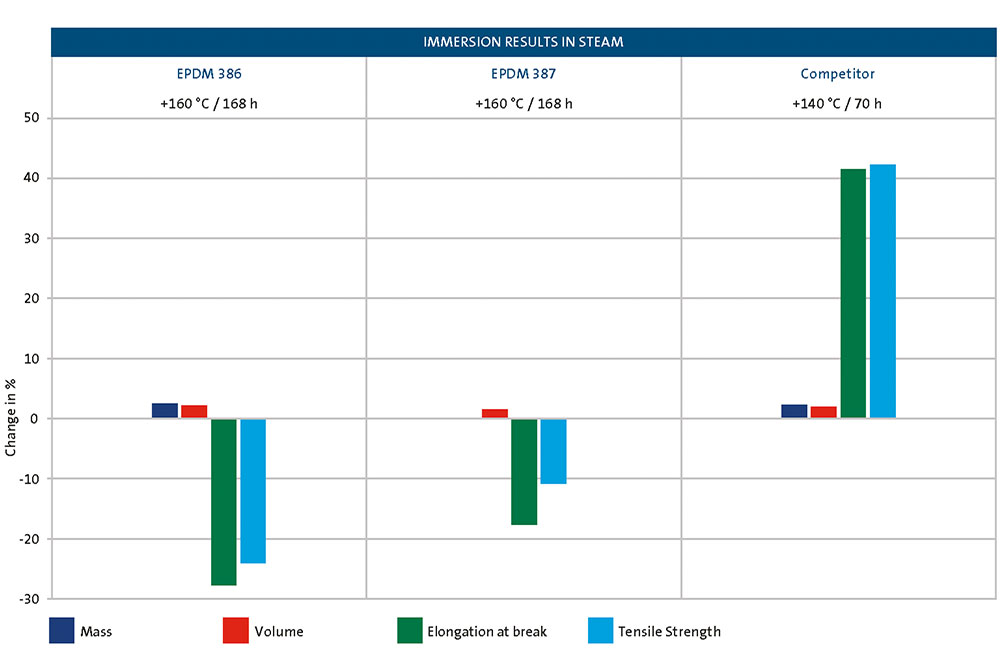
Fig. 3 Benchmarking EPDM materials
The new global materials are already available in the form of O-rings and machined seals to fill the need for replacement parts, prototypes and small production runs, among other uses. In the next stage, the new materials will be further developed into compounds suitable for injection to make formed parts and diaphragms for the food industry.
More news on the subject Material Expertise
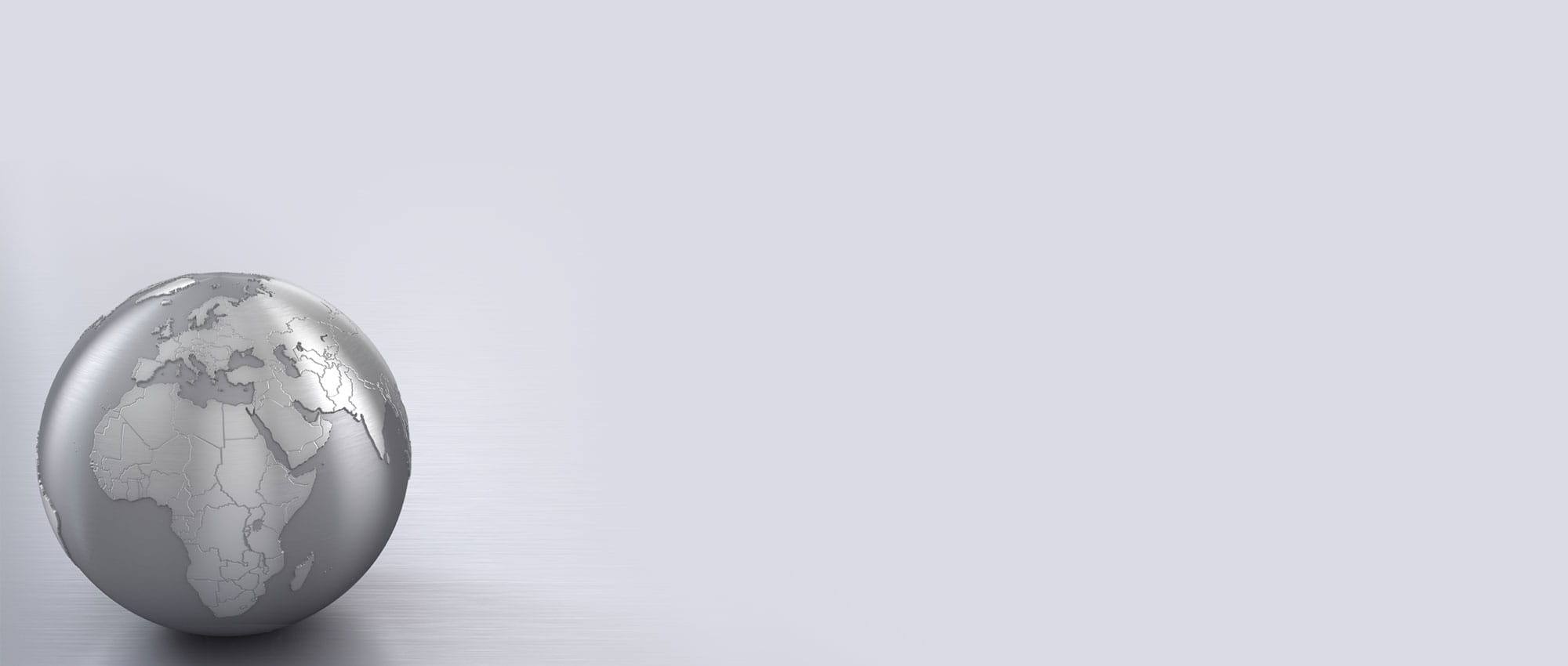
First Hand News
Best of all, keep up with the latest developments
with the Freudenberg Sealing Technologies newsletter.