Obtain news and background information about sealing technology, get in touch with innovative products – subscribe to the free e-mail newsletter.
06.12.2024
Climate-Neutral Substations: Future-Oriented and Sealed with a Sophisticated Switchgear Ring
These model series utilize vacuum technology, synthetic air and have zero global warming potential (GWP = 0). Freudenberg Sealing Technologies and Siemens Energy have rapidly developed a market-ready solution for high-voltage switchgear for the operation and expansion of voltage grids that completely eliminates sulphur hexafluoride (SF6) as an insulating gas. The reasoning behind this development? With a GWP of 24,300, SF6 has a very high global warming potential.
In March 2024, EU regulation 2024/573 for the use of fluorinated greenhouse gases came into effect. It replaces all previous provisions on emission control for the use, recovery, recycling, reclamation and destruction of fluorinated greenhouse gases. For the energy sector, this means nothing less than the complete conversion of long-established energy infrastructure to solutions with a GWP < 1.
Focus on compact switchgear design
Large spaces are particularly rare in urban areas and the optimal utilization of space is also important when operating substations on the outskirts. From this perspective, a comparison shows that gas-insulated switchgear requires only around one fifth of the space of a corresponding open air-insulated system. In such a compact setup, SF6 has performed successfully as an insulating gas in extra-high voltage grids as well as in high- and medium-voltage networks.
While SF6 is a non-toxic gas, its release into the atmosphere has a significant and long-lasting impact on the climate. The worldwide reports of climate-induced weather phenomena are a drastic indicator of the need for rapid and rigorous action to protect our atmosphere. The industrial use of greenhouse gases, often dubbed “climate killers”, must be phased out step by step.
Thinking ahead: Leveraging synergies and expertise
Freudenberg Sealing Technologies and Siemens Energy demonstrate how technical expertise and material innovation can be harnessed to construct and operate substations with climate-neutral solutions. The replacement of SF6 in switchgear was achieved within a short period – before the European regulation came into effect.
As Key Account Manager in Distribution, Martin Müller was involved in the various process steps from the outset. With a smile, he says: “It’s clear that our long-standing, reliable customer-supplier relationship has made this project a success. Our profound material expertise has dovetailed perfectly with the technical know-how of Siemens Energy and, to be honest, we’re quite proud of what we accomplished together within a short time.”
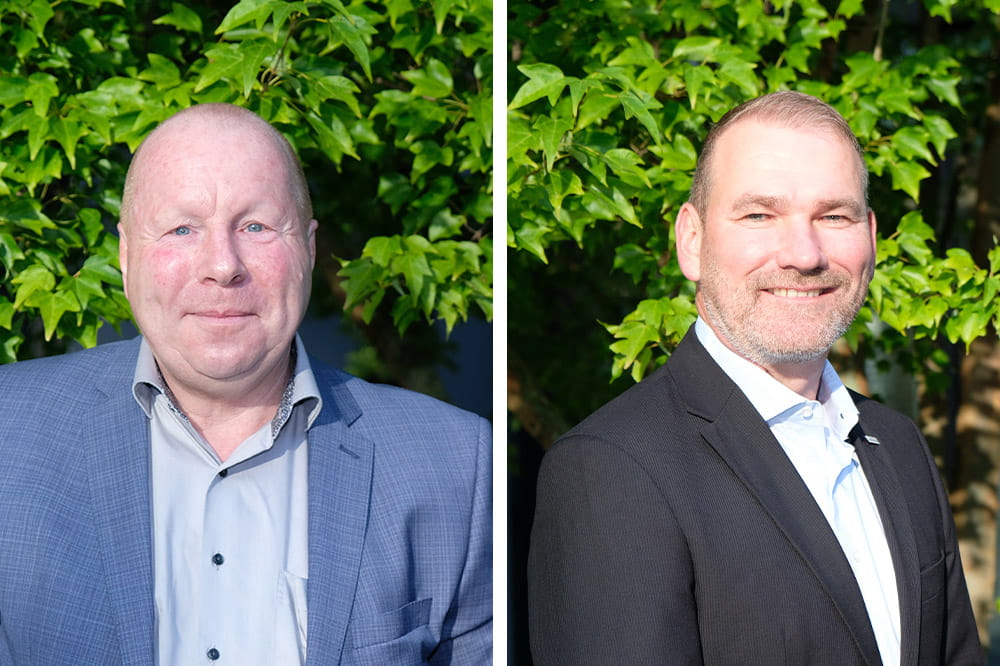
Living a culture of innovation: Staying ahead of legal requirements
Freudenberg started to develop climate-neutral insulating materials for the energy sector back in 2018. At that time, Siemens Energy already offered its first products using synthetic air as an insulating medium. Eliminating the reliable sulphur hexafluoride requires the use of other gas mixtures that must be both insulating and climate-neutral. Variations of synthetic air and other gas mixtures usually have a smaller molecular size, which in turn necessitates new materials with a structure that can prevent the escape of even the smallest particles of insulating gas. The collaboration, which merged design know-how with material expertise, resulted in a synthetic rubber based on chlorobutyl (CIIR) – a material remarkable for its low gas permeation. It is also suitable for use in a wide range of temperatures as low as -60° C. Another advantage is that the developed material contains no compounds from the group of perfluorinated and polyfluorinated alkyl substances (PFAS).
Karsten Löhn, Global Key Account Manager, recalls: “At the time, we focused on chlorobutyl rubber for switchgear and developed our product 70 CIIR 236460. This enabled us to directly support our colleagues at Siemens Energy in developing new switchgear with appropriate seals for the various series. As a result, Siemens Energy was able to use an extremely well-suited sealing material in its ‘Blue’ products within just a few months.”
Product-specific analysis: Environmental impacts and life cycle stages
A direct comparison of the life cycle analysis (LCA) of a 420 kV GIS with synthetic air and SF6 reveals a clear outcome: When using synthetic air as insulating gas, the total CO2 equivalents (CO2e) are 81% lower than those for the SF6 switchgear. The more renewable energies can be incorporated into the supply chains and production of switchgear, the more reductions will follow in the future.
Future in action: Vacuum switching technology and synthetic air
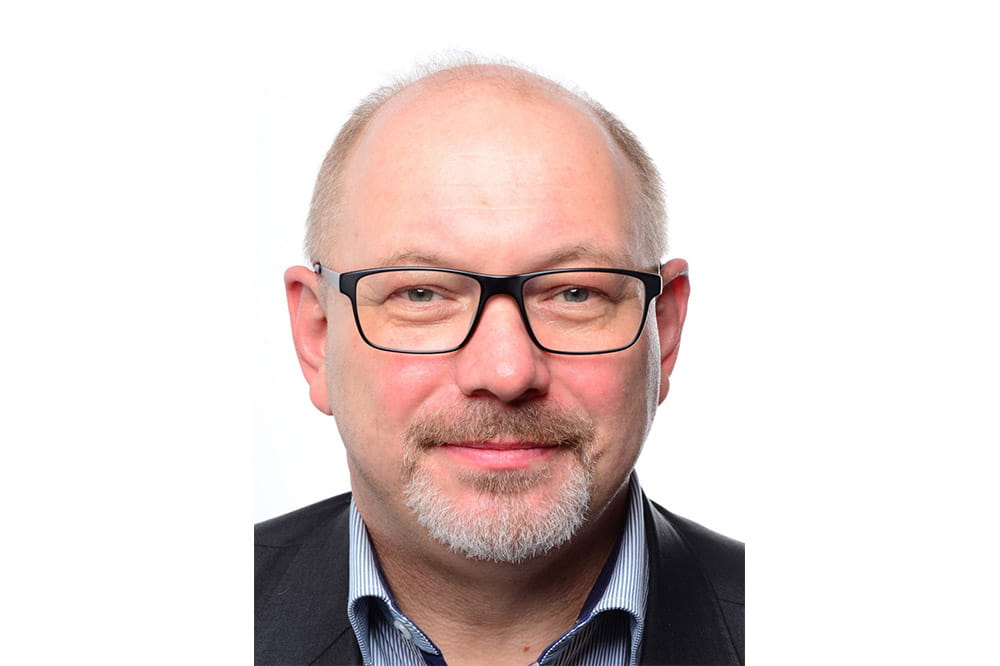
Siemens Energy installed its newly developed, tested and certified switchgear from the “Blue” portfolio for the first time in 2010. The first site was a substation in France. This innovative process went smoothly: Pre-tested at the factory, the equipment made it possible to quickly install and commission the GIS system – which included performing the high-voltage and partial discharge tests on site. Siemens Energy has used the CIIR sealing material as a standard for “Blue” products since 2023. It has been much easier to handle the synthetic air than other insulating gases; the existing plant quality procedures were also adapted to the synthetic air. As a result, the impermeability of the products is comparable to that of the SF6 equipment.
Karsten Pohlink, Head of Development for gas-insulated switchgear at Siemens Energy, notes: “Our goal is to have a completely F-gas free portfolio by 2030. To achieve this, we invested over 60 million euros in a new production facility in Berlin. And with Freudenberg Sealing Technologies, we have a partner at our side whose unique materials expertise has enabled the rapid adaptation of our switchgear to future requirements.”
Learn more about our seals for energy transmission and distribution.
Further Articles With These Taggings
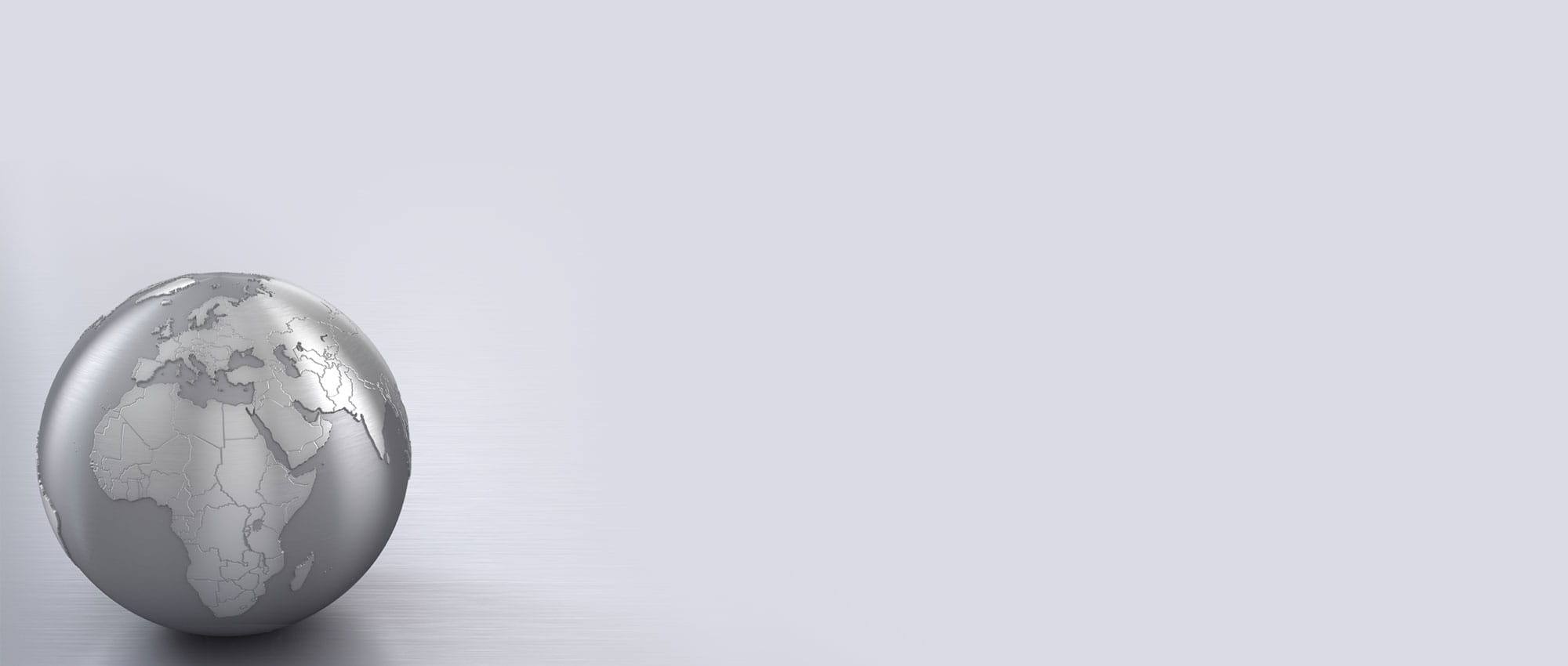
First Hand News
Best of all, keep up with the latest developments
with the Freudenberg Sealing Technologies newsletter.