Obtain news and background information about sealing technology, get in touch with innovative products – subscribe to the free e-mail newsletter.
13.01.2025 | News
Consider Seals at an Early Stage
Bipolar plates are the centerpieces of fuel cells and electrolyzers. Graebener, a German mechanical engineering company with a rich legacy, has already spent 20 years developing production technologies for this core element of a sustainable, hydrogen-based energy economy. Freudenberg Sealing Technologies is an important partner to the company in this process.
In a white paper, Graebener Bipolar Plate Technologies outlines the key factors for the successful production of metallic bipolar plates. In this “roadmap for the future of the hydrogen market”, two sealing experts discuss the topic in an in-depth interview: Jürgen Emig, Director Pre-Product Development Hydrogen Applications, and Dr. Dominik Kraus, Head of Stamping Technology.
One of the key statements made by the two Freudenberg-Experts is that the crucial role of seals has not been getting enough attention in the production of bipolar plates. The two experts say that the seal should ideally be considered even before a bipolar plate design is developed. “Previously, the seal issue was often underestimated. Most engineers have now understood the importance of the seal and the fact that it is only possible to work in a limited way with standard parts available in catalogs. We would therefore be delighted to be involved in developments at a sufficiently early stage,” Emig points out. The reason, according to Kraus: “From a production perspective, the metallic bipolar plate is a highly complex component.”
This means that the sealing solutions are also highly sophisticated. To provide outstanding and consistently reliable sealing efficiency, media resistance and permeation, the sealing materials and designs usually have to be reconfigured. Freudenberg Sealing Technologies has already scored remarkable achievements. “Silicone is often what first springs to mind when it comes to durability, however silicone is not sufficient. Silicone, for example, is not at all appropriate for high-temperature fuel cells. This is why we have developed separate materials specifically for use in fuel cells,” Emig explains. 35 FCPO 100 is a proprietary development by Freudenberg that is like liquid silicone in terms of processing. 70 FKM 256261 is a material that the company has developed specifically for the requirements of PEM electrolysis and high-temperature PEM fuel cells.
The fact that various electrolysis and fuel cell technologies exist in parallel and so far no standards have been set for either of them is particularly challenging. “There is currently barely any standardization in the market in terms of plate design,” Kraus says about the situation. Consequently, there is a need for universally valid specifications for plate designs that simplify the seal application and thus speed up the process. As Emig puts it: “Sealing 3D structures is a challenge. If you take certain requirements into account and standardize them, your chances of getting a robust seal are very high. It would be preferable if the design features were much more standardized – then we could perhaps already be producing higher quantities more cheaply.”
In the Graebener interview, he also mentions another objective: “Our customers are looking to acquire a plate from a single source – the ‘assembly-ready’ plate with a seal.” Freudenberg Sealing Technologies’ expertise in process engineering is a major advantage here. “Over the long term we need production processes with high quality standards in order to satisfy market requirements with regard to costs and output. Our customers know that we are able to meet the requirements of high-volume scenarios. We have been active in the automotive sector for many years, with much success, and we have quality standards which the automotive industry demands.” The automotive industry’s stringent quality requirements could also offer guidance when it comes to defining sealing standards for bipolar plates.
However, the development times for hydrogen are shorter than those in the automotive industry. This makes it all the more important to have informative test capabilities in laboratories and testing facilities, which Freudenberg Sealing Technologies is currently investing in. When it comes to the company’s comprehensive research and development work, its credo is: We want to understand the whole cell!
The information sharing and collaboration with Graebener are valuable building blocks in this process. “Before series-production readiness, we go through numerous iteration loops together with the customer. It is therefore a huge advantage to be able to access the relevant equipment to produce prototypes and small series,” Kraus explains. Graebener offers these capabilities in a partnership-based development cooperation to Freudenberg Sealing Technologies.
More news on the subject Sustainability
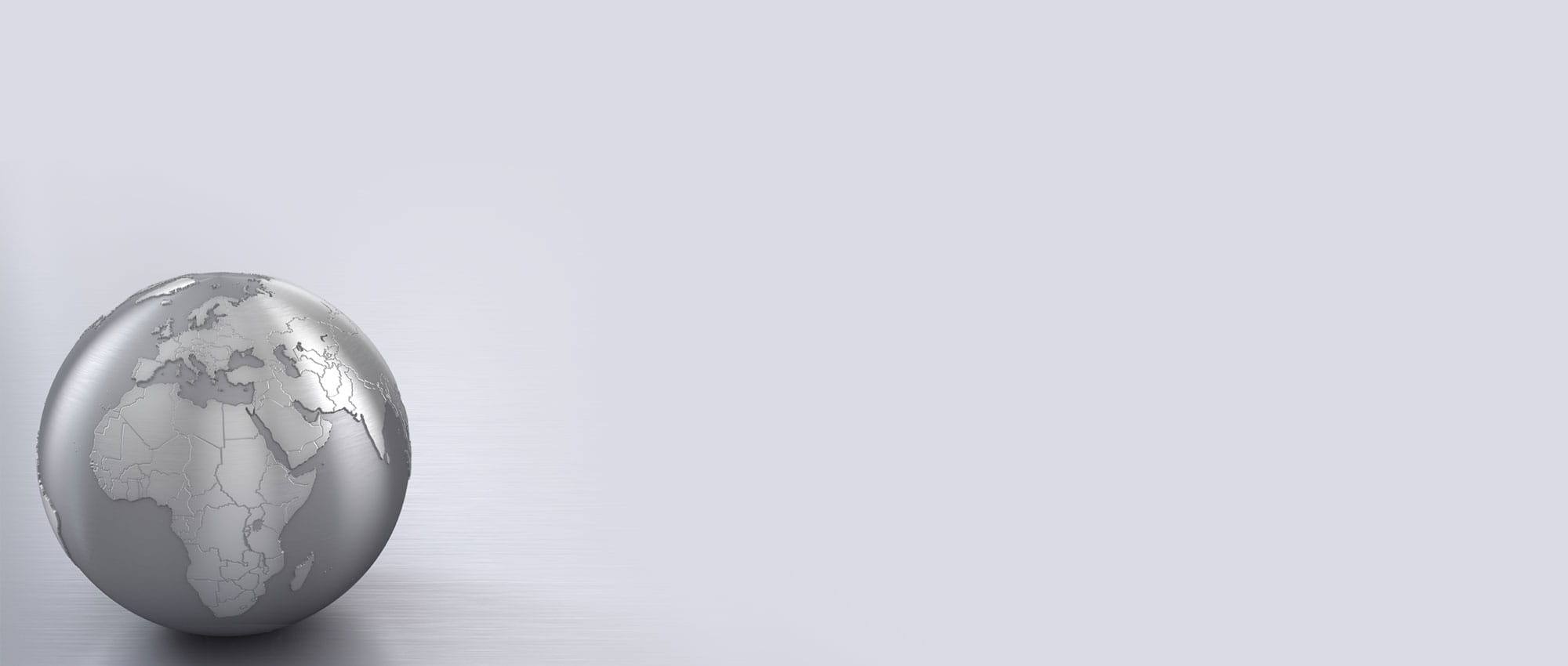
First Hand News
Best of all, keep up with the latest developments
with the Freudenberg Sealing Technologies newsletter.