Obtain news and background information about sealing technology, get in touch with innovative products – subscribe to the free e-mail newsletter.
03.04.2025
Freudenberg Sealing Technologies Designs Essential Materials for Extreme Requirements
Weinheim. Seals are an essential component in many industrial sectors – from the chemical and automotive industries to medical technology. Yet the requirements for the materials are just as diverse as the applications themselves: chemical resistance, high mechanical durability, temperature resistance and a long operating life are just a few of the critical factors. In each of these widely varied areas of application, testing new sealing materials is one of Freudenberg Sealing Technologies product development focuses. The company shows what sort of unique developments are possible when well-founded material research meets individualized customer requirements, and every step from design to series production helps to create sustainable products.
Excellent materials – the foundation of product development
The quality and performance of seals largely depends on the choice of the right materials. Continual research and development generate new material solutions enabling even higher resistance and better adjustment to specific applications. Teamwork is always involved in the development of innovative materials for challenging operating conditions: In 2019, Freudenberg Sealing Technologies launched a strategic program in which six of its subsidiaries did research together on new materials for extreme operating conditions. Thanks to this close cooperation in research, development and production, it was possible to make substantial progress in a short time. This interplay of technical expertise, experience and creative engineering is paving the way for future groundbreaking material solutions.
Stress tests – how materials are tested out
First comes the engineering – then comes the testing: New industrial applications require new sealing materials, and they are typically designed to function reliably under extreme conditions and over long maintenance intervals. Meanwhile, the efficiency and safety of industrial applications are maximized with the help of innovative product lines. Freudenberg Sealing Technologies has integrated a state-of-the-art test lab into its production environment where the durability and suitability of new sealing materials are put to the test in comprehensive test series. The test processes simulate real-life operating conditions over time and allow a precise evaluation of a material’s characteristics. These intensive test series make it possible to validate a product’s performance and optimize it when necessary.
Standard and high-performance seals – geared to the operation
The application areas for seals know nearly no limits. Whether in the food and beverage industry, in fuel cells or in the world of energy technology, the applications are just as diverse as the materials and material combinations available for them. For applications where moderate mechanical, chemical or thermal loads prevail, a wide variety of tried-and-tested standards seals are available. For example, they are used in water supply systems, machine-building and general industrial applications. High-performance seals, on the other hand, are required where the conditions are extreme. They can be found in the aerospace and chemical industries, the electric mobility field, and in high-temperature processes. Freudenberg Sealing Technologies offers customers a wide range of materials that withstand extreme temperatures, aggressive chemicals or high pressures over the long haul.
Chemical resistance – a core feature of many standard seals
One of the key requirements for sealing materials is chemical resistance. Depending on the area of application, seals have to resist aggressive fluids such as acids, oils and solvents. The choice of the right elastomer – such as nitrile rubber (NBR) or polypropylene diene rubber (EPDM) – is a crucial factor for the seal’s operating life and functionality.
Mechanical resistance - indispensable under high pressures
In some areas of the process industry, polyether ether ketone (PEEK) is a useful sealing material. It is one of the robust thermoplastics with good mechanical properties. PEEK offers different ways to alter its mechanical properties with filler materials – glass fibers or carbon fibers, for example – and can also be processed with injection molding.
Thermal resistance – even suited for aerospace applications
Temperature fluctuations and extreme heat and cold can have a considerable influence on seal performance. High-performance materials designed for extreme temperatures include silicone rubber (VMQ) and fluoro rubber (FKM). Their material properties ensure that specially designed seals function reliably even under demanding conditions.
Composite materials – creating something new
The development of new sealing materials requires an tremendous understanding of the field, access to innumerable raw materials, and a superb research and test environment. But at Freudenberg Sealing Technologies, the most important ingredient in the recipe for any composite material is the capacity to innovate. The idea, the spark of genius: Engineering begins in the mind and creates new worlds. Highly advanced production processes allow Freudenberg Sealing Technologies to develop innovative materials with tailor-made characteristics as it works with its partners and customers.
Sealing dialogue – direct interaction as a driving force
Dr. Ruth Bieringer, Vice President Material Technology at Freudenberg Sealing Technologies, looks at challenges of the future pragmatically. “Technologies, knowledge and research are the trump card when it comes to our materials – and you have to keep an eye on the themes for the future if you want to be successful. Personal dialogue with experts and partners creates an ideal platform to generate valuable momentum and actively play a role in creating the sealing technology of the future.”
Further Articles With These Taggings
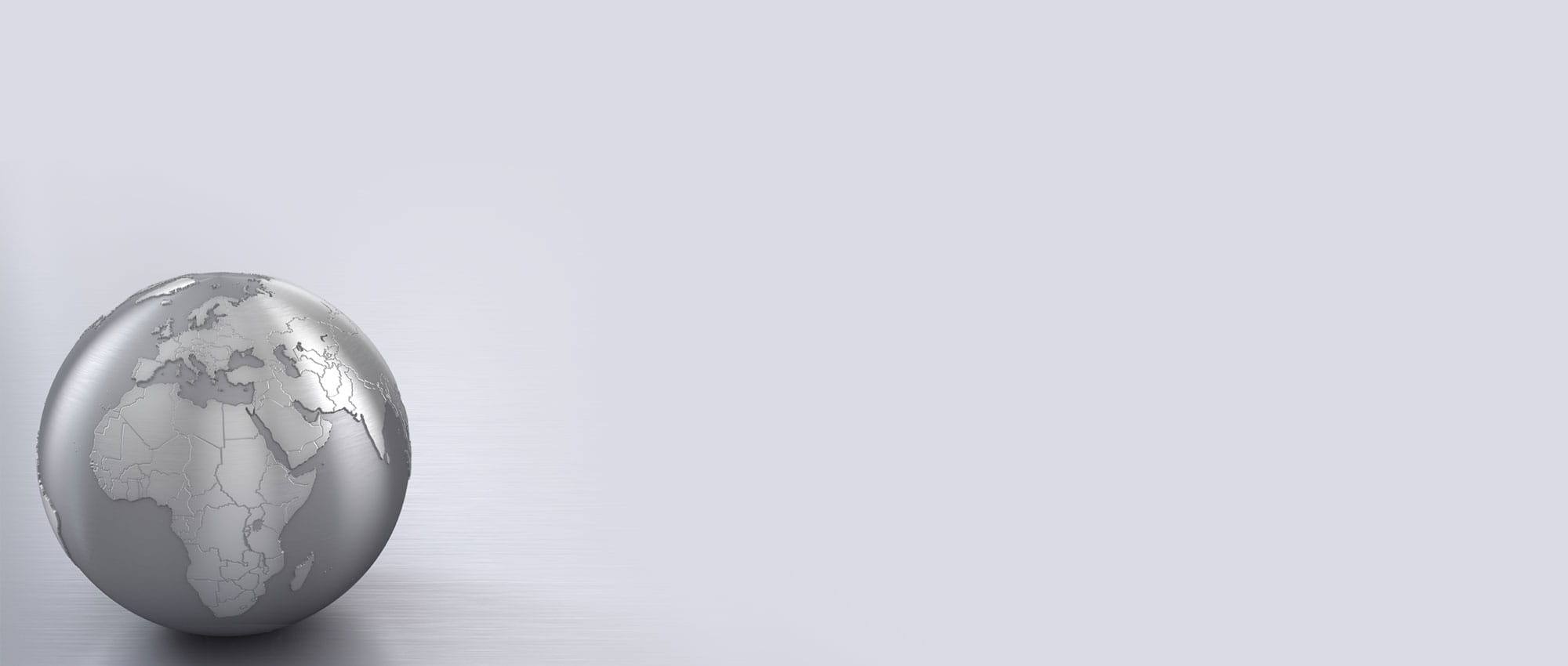
First Hand News
Best of all, keep up with the latest developments
with the Freudenberg Sealing Technologies newsletter.