Obtain news and background information about sealing technology, get in touch with innovative products – subscribe to the free e-mail newsletter.
02.04.2025
How Technical Expertise Solved Sealing Issues
Maritime and recreational boating applications can be incredibly unforgiving, with relentless forces from nature adding extra stress to sealing solutions. One of the most demanding applications for seals is in marine transmissions, which operate under conditions that include potential exposure to both fresh and salt water, varied temperatures, and constant mechanical stresses. Ensuring the integrity of these systems is crucial for the safety and performance of marine vessels.
The Challenge
When a manufacturer began experiencing difficulties with their seals in this harsh environment, they reached out to Freudenberg Sealing Technologies for support. This manufacturer, a long-term customer, had been using Dichtomatik brand NBR radial shaft seals in their marine transmissions for around ten years without a history of problems, suggesting something unusual was likely occurring. Since 2019, they had received 183 complaints, with 33 verified leaks. Although the leakage rate was 0.40% and the confirmed leak rate was 0.07%, the oldest leaky unit on record was built in 2019. Despite the relatively low failure rate, the manufacturer was concerned because they were not only building the transmission but the entire boat, which could cost between $10,000 and well over $100,000. Warranty work could therefore prove very costly.
Application Review Finding
The team at Freudenberg Sealing Technologies quickly involved several engineers to review the application, production factors, and the seals themselves. The experts swiftly identified that the manufacturer was using the wrong material NBR, which is not suitable for the demands of a marine setting. They recommended switching to FKM instead. However, they also discovered some anomalies that warranted a more in-depth review. Upon inspection, axial cracks were visible on the sealing lip, indicating signs of overheating. Consultation with the manufacturer's team revealed that the seals were installed before the exterior painting, which was baked at around +107°C (+225°F), literally baking the seals and causing them to degrade.
Additionally, the seals were not lubricated correctly. Prior to installation, the manufacturer cleaned the seals using soapy water on the outer diameter. Following this, they used petroleum jelly, commonly used for moisturizing skin, to ease installation, resulting in improper lubrication. This made installation incredibly challenging for their team and posed a significant risk of damage due to incorrect installation. Furthermore, debris and contaminants heavily impacted performance. Water splashes, fiberglass fibers, and other contaminants were found on the air side of the seal, while metal particulates from the gearing were found on the oil side. These factors are serious enough to cause a proper seal to fail, meaning that even a suitable seal would be at substantial risk of failure under these conditions.
The standard conditions of the seal showed a maximum operating temperature of +85°C (+185°F). The shaft surface speed for the 50x80mm (1.97x3.15 Inch) seal at maximum RPM was 10 m/s (32.81 ft/sec), and the media being sealed was synthetic oil (Mobil SHC 630). The applications often involved both fresh and saltwater, which needed to be considered as factors.
The solution
The team at Freudenberg Sealing Technologies took several steps to solve the problem for the customer. First, they changed the material from NBR to FKM, which offers superior resistance to heat and harsh environments. Next, they suggested upgrading from a Dichtomatik brand seal to a Freudenberg brand Simmerring®, which offers a long service life, and performs at a higher level as a premium solution. They recommended replacing not only the problematic outer seal but also the two inner seals to eliminate future risks of seal failure.
To address the challenges with installation and lubrication, they provided a chemically compatible lubricant from Klüber that matched the application media. This made installation easier and reduced the risk of damage during the process. Finally, they offered significant training to the manufacturer on the basics of sealing, including the seal's purpose, chemical compatibility, lubrication, factors affecting performance, and potential causes of seal failure. This training was instrumental in helping the manufacturer implement new procedures for caring for, storing, installing, and utilizing their seals to prevent future issues.
The solution proved effective during testing and has now been implemented in all new production applications. The upgraded seals are also being used for replacement parts in warranty requests. While using a premium seal was slightly more expensive than the industry standard version, costing around $10 each, it was well worth the peace of mind to ensure no damage occurred, avoiding expensive warranty work, and preserving the brand's reputation for performance. So far, this solution has been in use for a few months, and all testing and real-life use suggest that the problems have been completely resolved.
Understanding sealing solutions can be exceedingly difficult and requires a lot of technical expertise. If you are facing challenges with your seals, contact Freudenberg Sealing Technologies below so a sealing expert can assist you too!
Further Articles With These Taggings
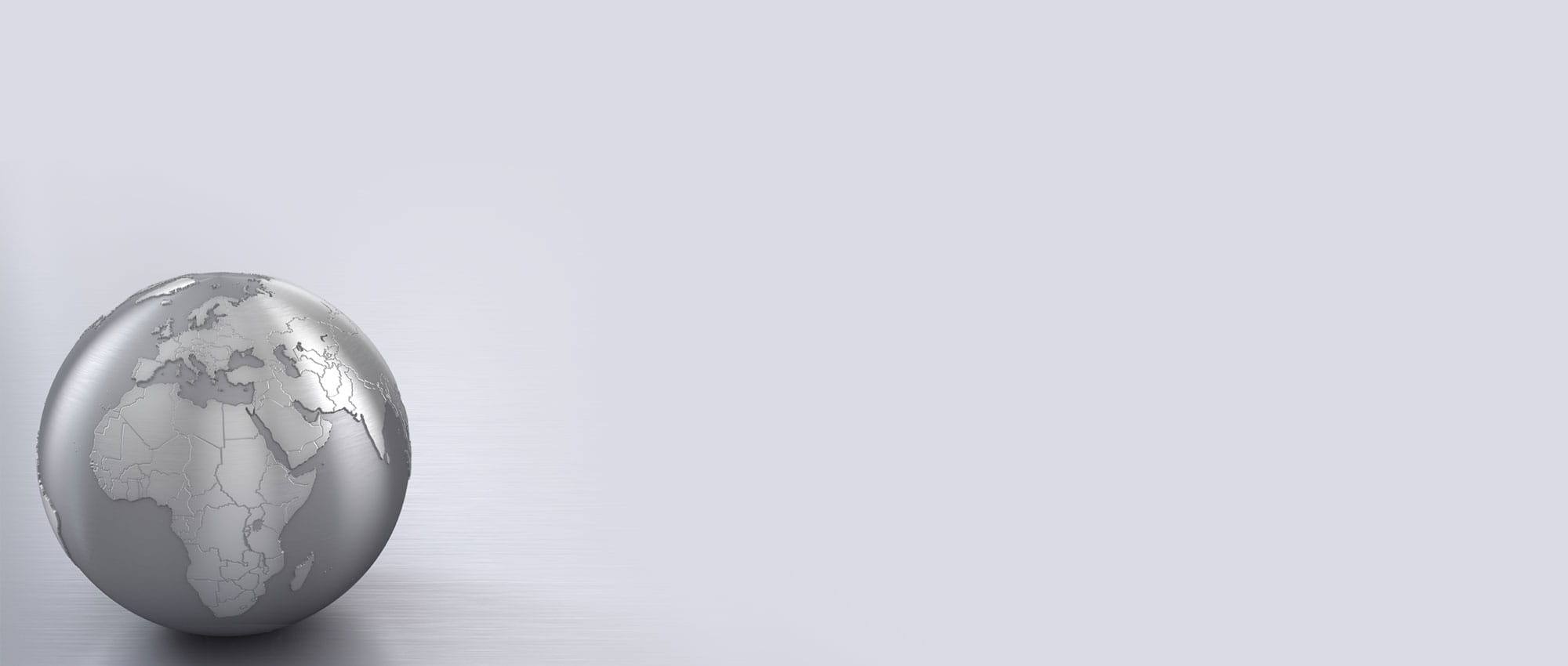
First Hand News
Best of all, keep up with the latest developments
with the Freudenberg Sealing Technologies newsletter.