Obtain news and background information about sealing technology, get in touch with innovative products – subscribe to the free e-mail newsletter.
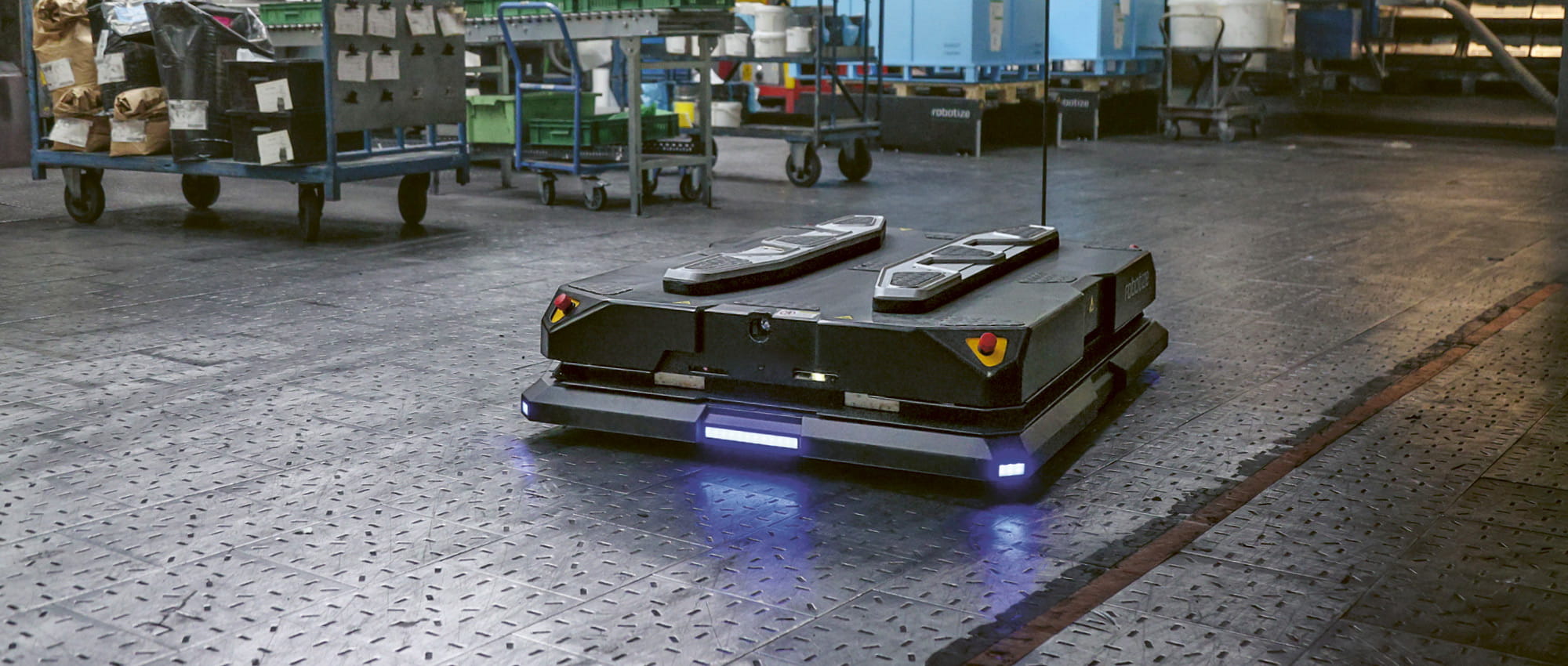
18.03.2023 | Story
Autonomous Robots
While autonomous vehicles still seem off in the future for cities, they are poised to conquer warehouses and manufacturing operations. Autonomous robots can transport raw materials and goods more selectively, safely and precisely to the right location. Freudenberg Sealing Technologies is experimenting with them as well.
People do not immediately recognize intelligence in some creatures. The rectangular, flat black box that drives around Freudenberg Sealing Technologies’ mixing plant in Weinheim seems to be single-minded and to capture the essence of monotony – but the opposite is true. The “GoPal” can make decisions on its own. “When you are in its way, it recognizes the situation and it waits,” said Christian Pfeifer, Manager, Competence Center Mixing in Weinheim. “And if it sees that you are not moving away, it recalculates its route and looks for another path” – perhaps a route to the loading station where several sacks of raw materials await it. The machine positions itself among them, extends its two rails upward, and lifts the pallet. It can carry up to 1.5 tons. “That was one of our selection criteria,” Pfeifer said. “We transport very heavy loads here.”
Logistics has long been considered a poor field for value creation: When goods only had to be carted from point A to point B, it was impossible to make money doing it. Hand trucks were followed by mechanical aids such as forklifts and conveyor belts. Conveyor belts are static and inflexible, while forklifts require a driver. In many warehouses and factories, they pose an especially high risk of accidents and injuries. “We have now entirely eliminated the use of forklifts in the production area,” Pfeifer said.
"Employees have to walk less." Machines take care of the walking: Two AMRs at the North Shields plant.
Obstacle: The Person or the Box?
The solution is known by the abbreviation “AMR,” the Autonomous Mobile Robot. It is the further development of the “AGV,” a driverless transport system. Since the start of the 2000s, AGVs have been deployed in warehouses, but they need help along their route from rack to rack to the manufacturing area. The assistance takes the form of reflectors on walls, stripes attached to the floor, or similar aids. AGV’s travel prescribed routes that – ideally – are closed off to people as much as possible. They have a tough time dealing with unforeseen disruptions. The name behind the abbreviation tells the story: AGV stands for automated guided system. These vehicles are automated, but not autonomous. And they are guided.
Robots like the “GoPal” from a Danish manufacturer actually find their way spatially on their own. They are already doing something that the auto industry and transportation policy-makers can only dream of: autonomous driving. But they naturally benefit from the technological progress now being made. Improved sensors to identify obstacles. Artificial intelligence, making it possible to interpret these obstacles rationally and constructively. Is the silhouette in front of me a pallet? Or is it a person who is likely to be moving away shortly? For human beings, this is a very simple thought. For a robot, the task is anything but trivial. In warehouses as elsewhere, time is an important factor.
A Swarm of Autonomous Robots
The Omron from the Japanese manufacturer of the same name is another version of the AMR. Some of these models are at work at Freudenberg Sealing Technologies' production facility at North Shields in England. They gather individual components and deliver them to the right locations or load and unload machines. The molding machines can even put in a call to robots on their own when they need more components. “Before the introduction, employees had to do that. It took ten minutes per machine and per shift,” said Martin Sims, Process Development Engineer at North Shields. That worked out to more than an hour and a half of non-value-creating activities per person. Two AMR units have been in operation at the plant since February. It’s a start, and it’s already paying off. “Employees have had to take fewer steps since then,” Sims said.
We have very heavy loads to transport.
Christian Pfeifer, Manager, Competence Center Mixing in Weinheim, Germany.
Two AMRs have been working at the company's mixing plant in Weinheim, and the number is expected to increase. Pfeifer would like to see a half dozen robots in operation by the end of 2025. “Then they can communicate with one another,” he said. “When we need a load, the vehicles will coordinate to see which one is in the neighborhood.” That was an impossibility technologically until a few years ago. It is the result of advances in network technologies such as 5G. The single unit is just the beginning. AMRs are opening up completely new dimensions in plant and warehouse logistics: a swarm of autonomous, communicating vehicles that, with computer support, guarantee the best possible distribution and delivery of goods and individual parts. Machines that look as though they would swarm through an area like ants. And, at the very least, operate with an ant-like level of coordination.
A Surge in Innovation and a Growing Market
Logistics and production experts worldwide are already thrilled with a level of efficiency that they could not have imagined a quarter-century ago. It is exactly the right technological leap for the current explosion in e-commerce – and it is arriving at precisely the right time. The online retailing giant Amazon first invested massively in AMR technology in 2012, leading to a surge in innovation across the sector. A decade later, Amazon introduced its first completely autonomous mobile robot, using it to move large wagons in warehouses. There has been a growing trend toward the use of AMRs worldwide, in healthcare and retail as well as logistics and production.
In Weinheim, Christian Pfeifer is well aware of the limits of the current generation of AMRs. For example, these mobile black boxes depend on the deliveries being ready for them. They cannot reach upward. That’s not a problem for Pfeifer. “Sometimes innovation is slowed by the fact that everyone immediately expects a jack-of-all-trades,” he said. But the more complexity you have, the greater the risk of losing the overview. “We are tackling this step-by-step. Our mindset is to test what is working,” Pfeifer said. Tests are also underway on new models that lift exactly the way forklifts do.
The “GoPal,” a name coined from the words “pal” and “pallet,” has already led to an unexpected side effect. “The workers in the plant have become tidier,” Pfeifer said. Previously, pallets were occasionally left in the lanes – with the knowledge that the forklift driver would climb down and remove them when necessary. “Now everyone keeps the way clear for the robots.”
More news on the subject Robotics
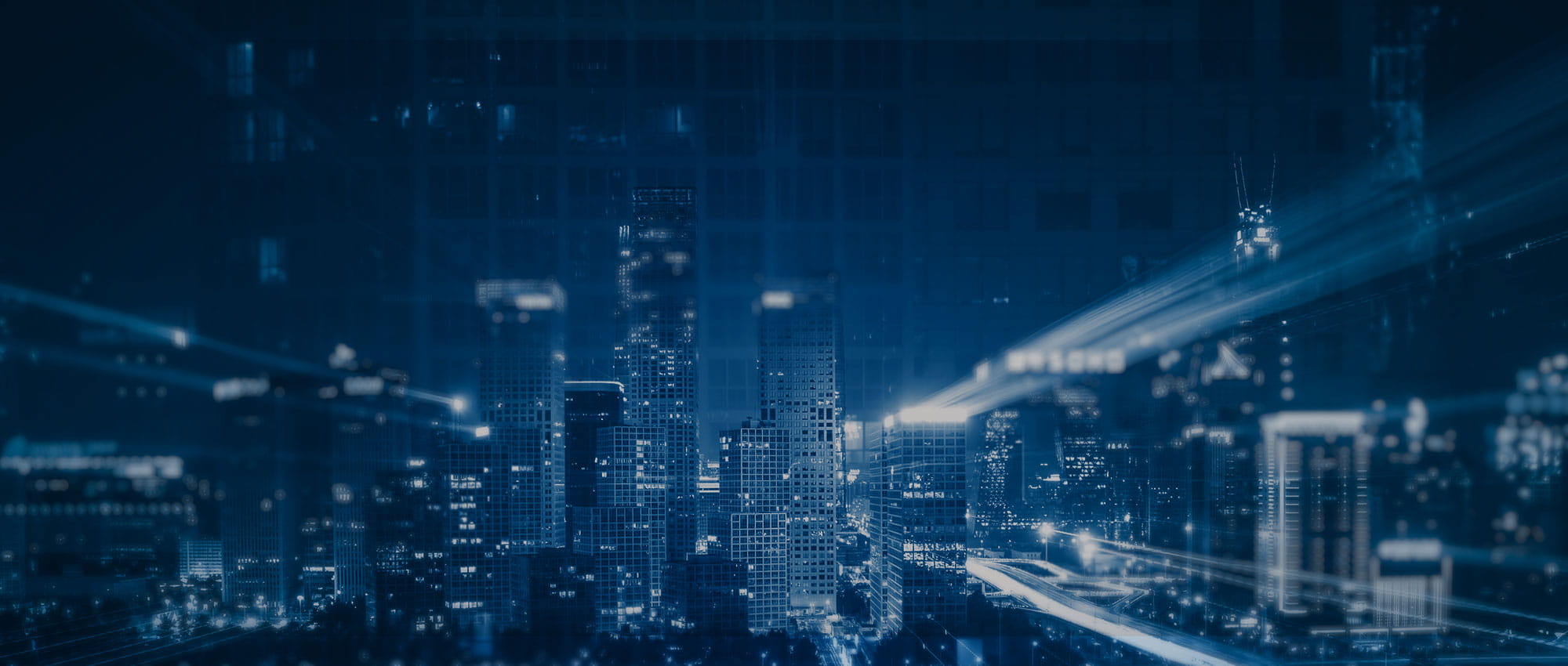
Join Us!
Experience Freudenberg Sealing Technologies, its products and service offerings in text and videos, network with colleagues and stakeholders, and make valuable business contacts.
Connect on LinkedIn! open_in_new