Obtain news and background information about sealing technology, get in touch with innovative products – subscribe to the free e-mail newsletter.
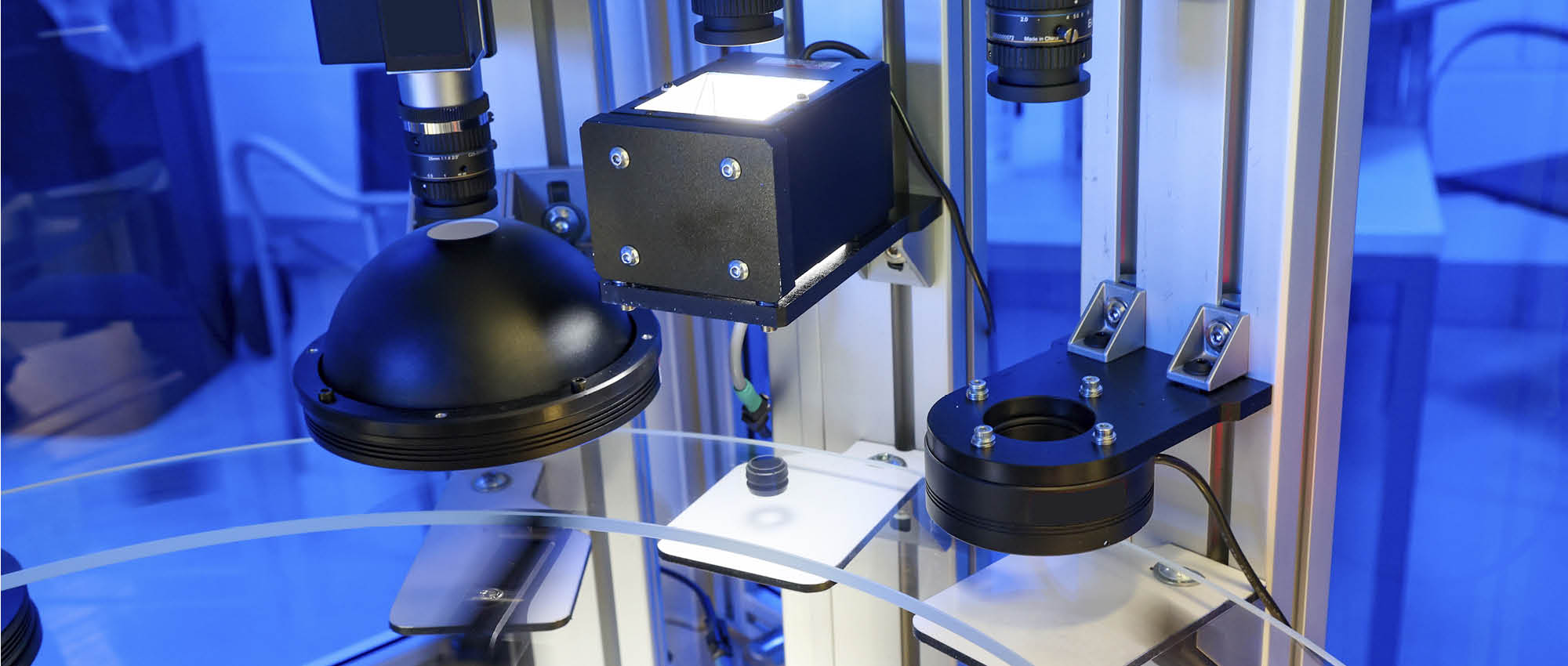
Networked Factory: The Power of Digitalization
Companies that want to be viable in the future should first look inside themselves. That’s because businesses like Freudenberg Sealing Technologies don’t just produce goods – they are simultaneously generating massive amounts of data. The proper evaluation of the information will be a crucial factor for their further success.
Oliver Müller, Vice President Digital Systems for Product Engineering and Manufacturing at Freudenberg Sealing Technologies, has a clear opinion on the matter: “Sooner or later, if a company closes itself off from the benefits of digitalization and automation, it won’t have a chance.” He cited an example: “Kodak was the global leader in cameras for decades and had even developed a digital version about 50 years ago. But it recognized that this would be photography’s future too late and missed out on the trend to digitalization. A global player went bankrupt.”
Sooner or later, a company that closes itself off from digitalization and automation won‘t have a chance.
Oliver Müller, Vice President Digital Systems for Product Engineering and Manufacturing Freudenberg Sealing Technologies
Freudenberg Sealing Technologies wants to avoid that fate. With its high-performance, innovative products, the seal manufacturer based in Weinheim, Germany, is bearing up quite well in the market. But if it doesn’t want to jeopardize its position, Müller said, it has to pursue a digital transformation. He also thinks it is crucial not to adopt a top-down approach. “Digitalization is our vision, but we can’t just impose it on our roughly 60 production facilities around the world, and we don’t want to do that. We need to agree on where our path should lead, incorporating ideas from our facilities.”
Oil well: Vice President Oliver Müller compares the collected data with crude oil that needs to be processed and enriched like in a refinery in order to get useful insights.
Using Data Like Crude Oil: From the Well to the Refinery
However, management has to lay the foundation. At Freudenberg Sealing Technologies, this is happening in the “Ready” project. In the production facilities, sensor systems, WLAN expansions and higher bandwidths are becoming more important. That’s why “Ready to Connect” is the first of several building blocks. It involves the area-wide, systematic networking of production facilities and machines based on a uniform IT standard. With this approach, Freudenberg Sealing Technologies is creating the preconditions for collecting data in real time. “Our manufacturing areas and machines are like a massive oil well to us,” Müller said. “They are constantly generating data that we collect. Then we have to understand and interpret the data correctly. That means we have to deal with the information the way a refinery deals with oil. We need to process it and enrich it. When we set the data elements in relation to one another, we get useful insights using algorithms and simulations.” Müller is convinced of the data’s value: On the shop floor, the insights enable us to take decisions that are better than ever. “This helps us stay competitive,” he said.
Two other building blocks of the “Ready” program are “Ready to Innovate” and “Ready to Operate.” The first involves IT-savvy employees who develop useful applications for their production sites with the help of a toolbox. The apps drive advances in technologization. To avoid standalone solutions, they are carried out in a uniform software landscape. At the same time, it is the job of “Ready to Operate” to ensure that IT operations are just as stable as those of a site’s production equipment. And IT security is a top priority from every perspective.
Connectivity and in-house IT developments will bring more automation to manufacturing operations – something that creates uncertainties in the minds of employees working there. “I can understand it when production employees look at digitalization skeptically,” Müller said. “After all, machines will be taking over more and more processes on their own. That’s why it is essential for a company’s communication to go hand-in-hand with the connected-factory process and highlight its advantages. In the end, we have to face reality: If the digital transformation goes better for our international competitors than it does for us, plants that are still profitable today will be at risk. The same is true for the success of the company as a whole.”
The Connected Factory Takes Shape
But how is the connected-factory approach reflected at Freudenberg Sealing Technologies today? Müller has evaluated the company’s progress. “We are already good at connecting our manufacturing operations, and we are even better at digital shopfloor management,” he said. He was talking about linking collected data with IT systems such as MSCADA. Adapted to special needs of Freudenberg Sealing Technologies, the program is already at work in several production areas. This is not just a matter of seeing in detail how the production process is running in real time. It is also a way to see the condition of a machine and how efficiently it is running. Captured quickly and easily by sensors and connected via gateways, the data from machines and the production environment around them are merged. When necessary, corrective measures can be developed from the data and then introduced – for example, by adjusting the ambient temperature so the production of sensitive compounds is not impaired. Or by adjusting machine settings. Previously, these steps would not have been introduced at all or would have been carried out at a later stage, perhaps even too late since the required data would not have been captured. The bottom line: Connectivity combined with a platform such as MSCADA promotes the efficient optimization of processes and products.
At your service: Autonomous mobile robots like this one pick up manufactured products and drive them into the warehouse independently.
Freudenberg Sealing Technologies is also taking the path of digitalization and automation in other areas. In a mixing plant and several molding operations, autonomous mobile robots are already picking up products and driving them into the warehouse independently. This still happens in response to “calls” from employees. But the systems will eventually reach the point that manufacturing machines will request the robot on their own. Freudenberg Sealing Technologies is already considering a combined approach where robots are equipped with a so-called “cobot” that grasps newly manufactured products autonomously, places them in containers and then moves into the warehouse along with the robot.
Digitalization also plays a central role in quality assurance. Freudenberg Sealing Technologies has developed an automated vision inspection system that identifies defective parts and sorts them out – an example that shows the potential that digital processes offer. “To us, there is no question that we are going to digitalize. The only questions are when we do what and how quickly,” Müller said. The company has had to act fast, for example, when it has had to provide evidence for its product data. This refers to the traceability of production steps. Thanks to digitalization, production data can help a company track the contents and quality of a product.
The Human Factor
IT is thus an increasingly important aspect of manufacturing. This also means that Freudenberg Sealing Technologies needs skilled developers who can create their own digital solutions like the automated vision inspection system. At the same time, the rest of the workforce needs a better understanding of IT. Production employees must be trained in these skills so they can fully exploit the advantages of a digital factory. “It is crucial for us to take our employees with us,” Müller said. “With our own IT experts as well as training programs and the community development for production staff, we are pursuing our goal: the connected factory. We are also guarding against a staffing shortage that demographic trends are predicting, and we are making ourselves more independent of external services.”
For us, there is no question that we will be digitalizing. The only question is what we tackle, when we do it, and how fast.
Oliver Müller, Vice President Digital Systems for Product Engineering and Manufacturing Freudenberg Sealing Technologies
Little Assistants: Freudenberg Sealing Technologies uses sensors to monitor temperature and humidity in its production facilities.
The example of HoloLens glasses shows that employees are embracing digital solutions. The glasses are proving themselves at several locations. The pressures of the corona pandemic have led to their adoption much more quickly across sites. With these mixed-reality glasses, the real environment can be associated with virtual content and information. Or interactive, three-dimensional projections can be presented in a real environment. A production worker also has the ability to link up with – and be guided by – a second person at another site. With the help of HoloLens, they are looking at the same scenario. It is a time-saving, solution-driven process.
When it comes to digitalization, Müller thinks Freudenberg Sealing Technologies is on the right track, even if the effort is like running marathon. There is already valuable momentum, and the first concrete steps have been taken. “In the end, this is about optimizing production to ever-higher levels. Data collection and evaluation help us do this. In addition, digitalization will be a huge help in developing new products properly right away. Thanks to our data, IT systems and algorithms that facilitate decision-making, we stay relevant as a company,” he said.
More Stories About Digitalization
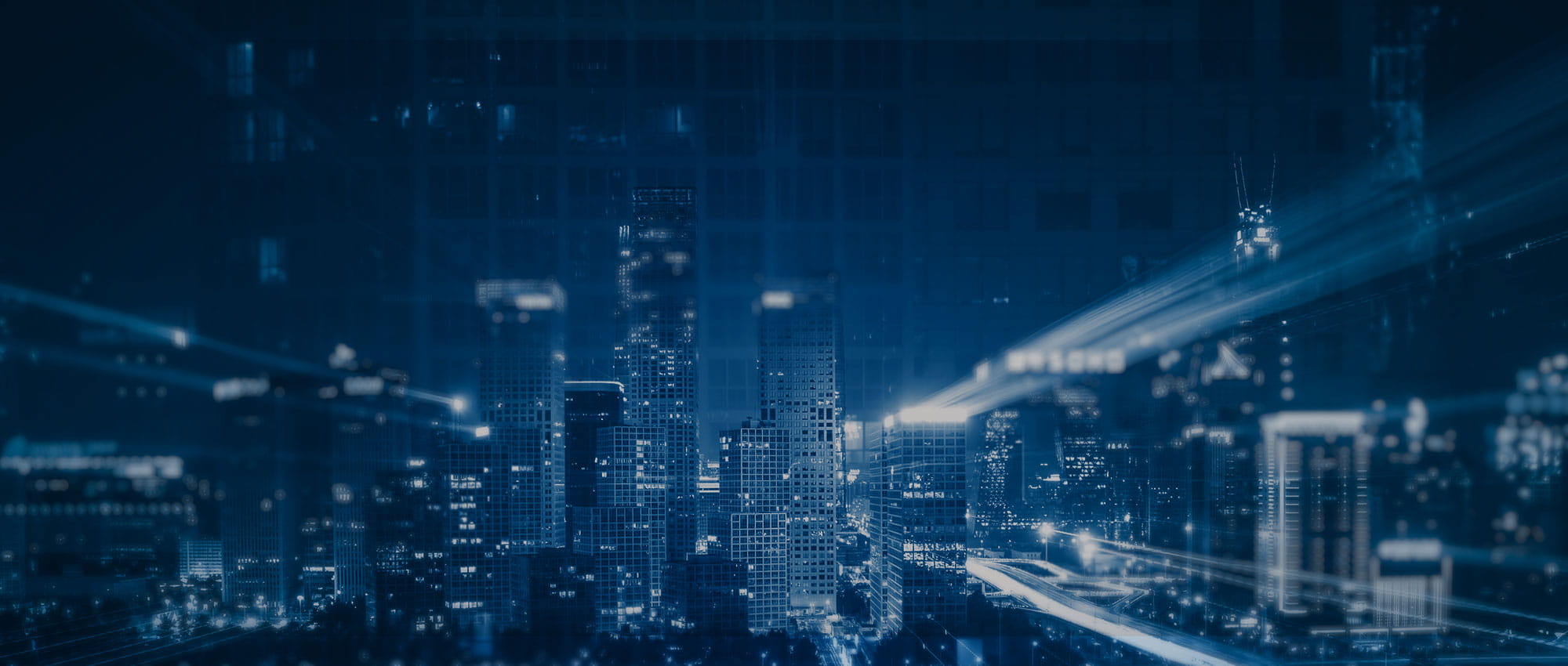
Join Us!
Experience Freudenberg Sealing Technologies, its products and service offerings in text and videos, network with colleagues and stakeholders, and make valuable business contacts.
Connect on LinkedIn! open_in_new