Obtain news and background information about sealing technology, get in touch with innovative products – subscribe to the free e-mail newsletter.
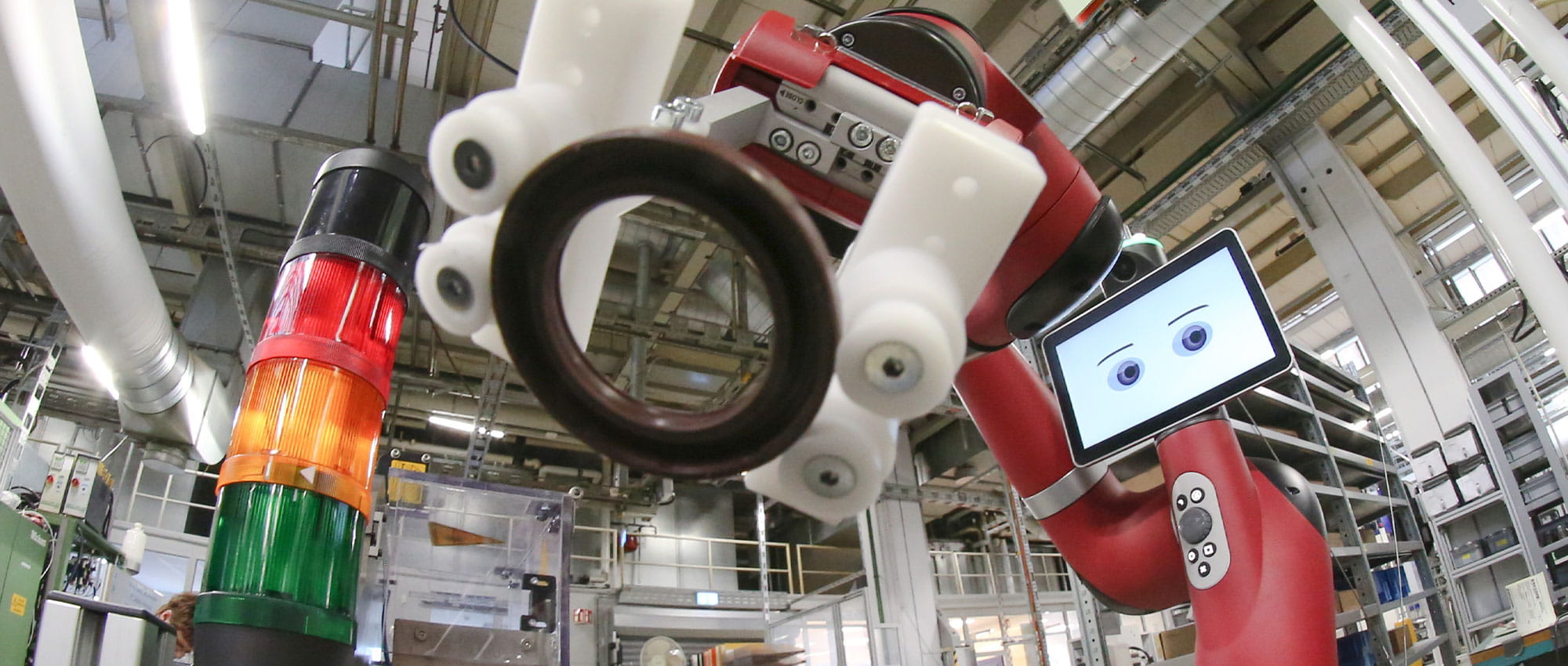
19.10.2021 | Story
Working Hand In Hand With Cobots
Some have two arms, others only one. They roll through plant aisles or are enthroned on pedestals. Robots are increasingly working with people today and they even handle monotonous work for them. Unlike classic industrial robots, cobots are small, lightweight and flexible. They are already in use in the Simmerring® final assembly area at the main Freudenberg Sealing Technologies factory in Weinheim.
At first glance, the new coworker in the Simmerring® final assembly area seems quite unremarkable. He neither rotates his head 360 degrees like R2-D2 in Star Wars nor does he speak in a tinny voice. Instead, he is enthroned on a pedestal from which he is unable to descend. His body is actually just an arm. But at least he is able to move it along seven axes, and it is equipped with a gripper. He perceives his environment with two cameras (one of them close to the gripper), and he has a monitor for a head. If you switch it on, a face appears. The eyes are still closed when the cobot is booted up. He later regards his counterpart with large round eyes.
IF ITS ARM IS STRUCK WITH A FORCE OF MORE THAN 20 NEWTONS, IT WAKES UP AND GOES INTO ITS WORKPOSITION.
The new colleague in Weinheim is a cobot. This variety of robot was created to collaborate with human beings. That is the origin of its name: cobot is short for “collaborative robot.” For years, industrial robots have not been able to work hand- in-hand with people. They could only work within cages for safety reasons. Cobots, on the other hand, are small, light and agile and are designed for small loads and slow speeds. The first examples were developed in the United States at Northwestern University in 1996.
Today they are preparing to conquer shop floors everywhere. “Freudenberg Sealing Technologies is currently using cobots at eight locations,” said Ralf Maisack, who is pressing ahead with the strategic development of cobots in the company’s Technology & Innovation unit. “For example, a stationary, one-armed robot has taken over simple assembly tasks at the Findlay facility in the United States. We are also using a two-armed cobot in Luserna, Italy, and mobile cobots in Bristol and Newcastle in the UK.”
Cobots are especially well-suited for manual activities that are constantly repeated. If they relieve workers of these tasks, the latter can deal with higher-value activities – and manufacturing output rises overall. One of these cobots works with a human colleague in the finishing area of Simmerring® production and mainly handles two tasks: first, it has to mount a spring in a Simmerring® and then fill the unit with the right quantity of grease. That certainly sounds simple, but since the cobot is not built precisely for this task, it has to be programmed first. A human worker is required at the start. At the beginning of his shift, he has to get everything ready. For instance, he has to check the amount of grease that is brought into the application station. He also loads the stock of Simmerrings onto a bar feeder that will later deliver individual Simmerrings via a dispenser. The worker then gives his cobot the signal to start. Incidentally, this is done very rudely – by giving it a shove.
The cobot is equipped with force and torque sensors. If its arm is struck with a force of more than 20 newtons, it wakes up and goes into its work position. The contact needs not be very brutal – 20 newtons corresponds to the gravitational pull that acts on an object weighing 2 kilograms (4.4 lbs). After it is booted up, it has to orient itself. The cobot uses its cameras to look for position markings in the form of QR codes that are attached to its workstation. That is how it recognizes where it is. Then it uses its arm to pass over the table where he will later deposit finished parts, to make sure no obstacles are in its way. The cobot is basically designed for collisions and could easily bump into a person-. But this isn’t dangerous because it only works with low forces and at low speeds.” When its sensors detect an obstacle, it stops immediately. If the obstacle then disappears, it starts out again in slow motion until it can be sure that the obstacle is completely gone. The areas for the cobot and the human being are precisely marked with red lines. The robot’s radius of action is relatively limited – 1.2 meters (3.39 ft).
Trust Is Good, Control Is Better
But that’s enough for the cobot to do its job. First of all, it reaches into a dispenser and removes a Simmerring® from the bar feeder. Then it swivels toward a specially developed workstation and presses the Simmerring® onto a cone so that the metal spring to be mounted springs at precisely the desired point. The cobot then takes the Simmerring® off the cone again, moves it to the lubricator and presses it with positive-locking onto a lubricating mandrel. Here the crucial factor is that the cobot is linked with the machine control system via a data cable. This allows it to communicate with the system and actively trigger the signal to perform the lubrication. The quality control after the lubrication is also important. It is only when the machine reports that the process has functioned error-free that the cobot removes the Simmerring® from the lubricating mandrel, swivels to a delivery table and stacks finished products by the dozens. A human being is then needed to carry out the final inspection and package the rings.
BUT THIS ISN’T DANGEROUS BECAUSE IT ONLY WORKS WITH LOW FORCES AND AT LOW SPEEDS.
The final-assembly process at the Weinheim facility is proving to be stable and reliable. This form of teamwork has many advantages. The worker can concentrate on the production set-up, quality control, and packaging, and is relieved of especially monotonous work. The highly flexible cobots demonstrate their strengths when ergonomics of the activity is poor. They can move their arms along many axes and reach areas that are difficult to access. These new coworkers are an aid to workers – they are not a replacement for them. A cobot never works alone. It always works with a human being. Since the speed and strength of a cobot are limited for safety reasons, it is suited for work with medium degrees of automation and complexity. It only rarely matches the speed of a human being in its work. In Weinheim, cobots are thus planned for other points in the final processing of Simmerrings. This will lead to new, exciting tasks, since there will certainly be opportunities to tinker during the set-ups.
More news on the subject Robotics
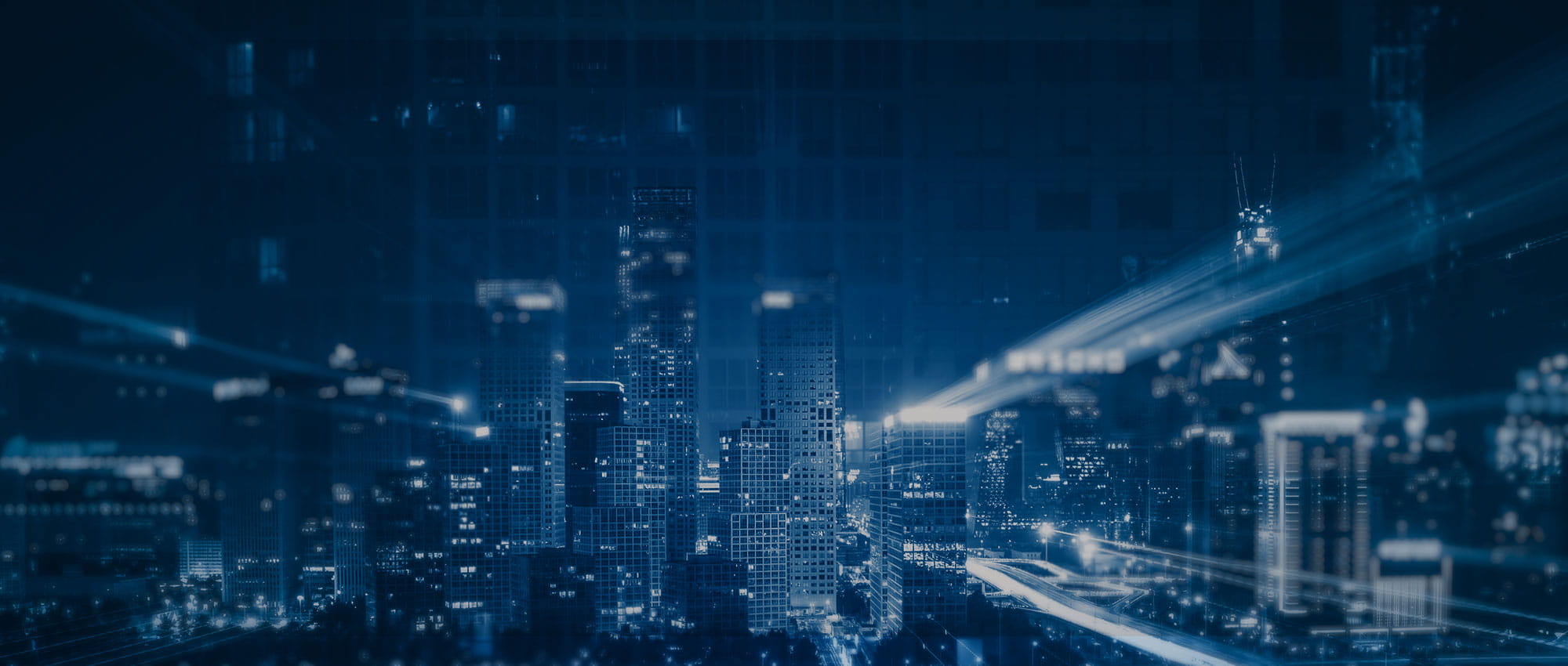
Join Us!
Experience Freudenberg Sealing Technologies, its products and service offerings in text and videos, network with colleagues and stakeholders, and make valuable business contacts.
Connect on LinkedIn! open_in_new