Obtain news and background information about sealing technology, get in touch with innovative products – subscribe to the free e-mail newsletter.
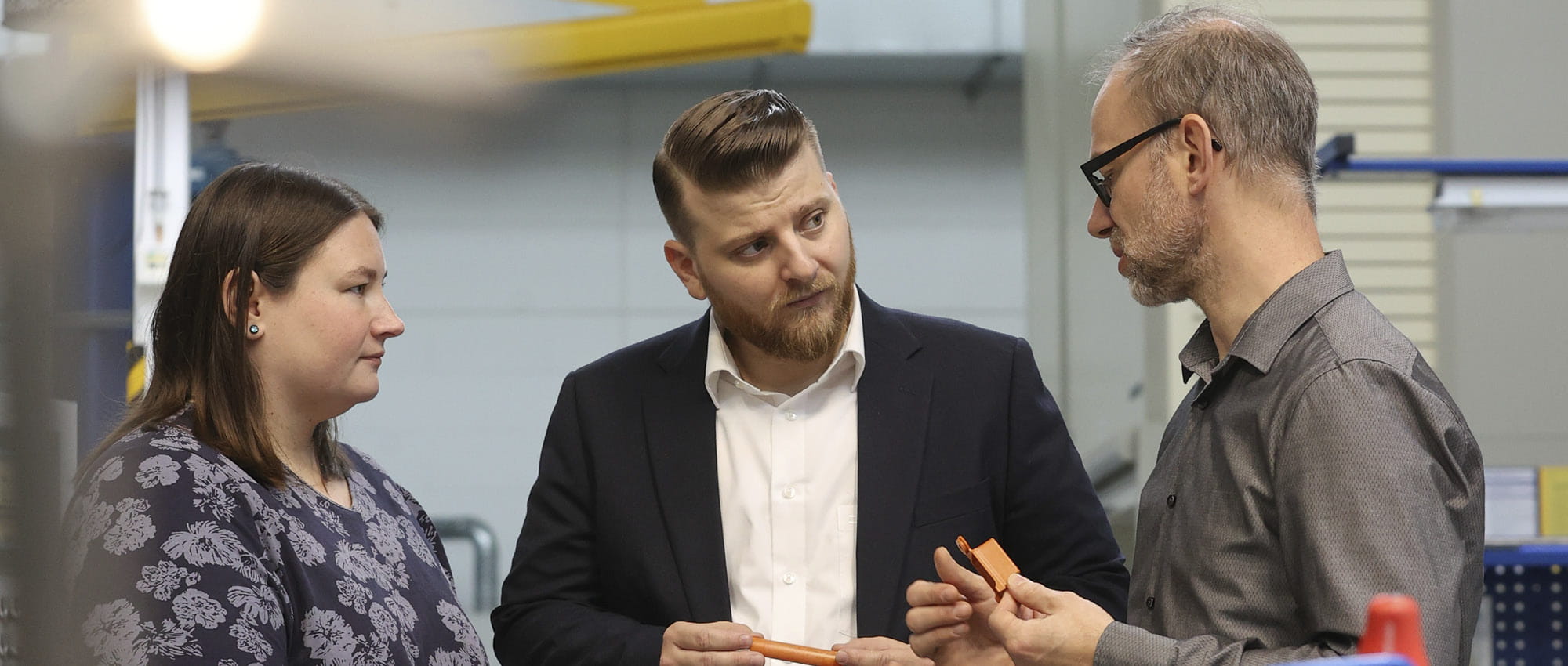
Electric Cars: Curbing the Risk of Fires
Drive batteries are the core of electric cars. To contain fires that may break out in them, a world-renowned automaker has turned to a new flame-resistant plastic from Freudenberg Sealing Technologies.
Electric cars are in the fast lane worldwide, sales figures show. In the spring of 2023, the International Energy Agency (IEA) predicted sales of 14 million electric cars this year. That is about 4 million more units than in 2022. The growth has been uninterrupted since electric cars first broke the 1-million-unit threshold in 2017. The demand has continued to grow in the United States and Europe, with China in the lead.
The material that we developed does not exclude any fillers or reinforcing materials. That means all options are open to us for cross-linking, which gives us a unique position in the market.
Dr. Björn Hellbach, Material Expert Thermoplastics at Freudenberg Sealing Technologies
The Battery as a Safety Factor
Aside from ecological considerations, the improved reliability and performance of electric cars have been crucial to their success. The drive battery is responsible for the increased performance. It is packed full of battery cells, which have some drawbacks. In the worst-case scenario, if they are damaged and deformed in an accident, thermal runaway can occur, and they may catch fire. So automakers are paying close attention to fire protection – not least of all because any plastic part installed near the battery has to be flame-resistant. It must neither catch fire nor lose its original geometry.
Here Freudenberg Sealing Technologies is getting some attention for its Quantix® ULTRA, an innovative plastic that is much more flame resistant than aluminum and many other materials with special flame protection characteristics. This has been demonstrated with a unique stress test using a pyrotechnic product. It involved blasting the new material with particles heated to 1200°C (2192°F). Dr. Björn Hellbach, Materials Expert Thermoplastics, at Freudenberg Sealing Technologies, draws a vivid comparison. “It is as though you were aiming a 1200°C sandblast continually on one spot.” Quantix® ULTRA can withstand the stress test with the heated particles for 20 seconds. The result for an aluminum part 2 millimeters thick is just 2 to 3 seconds. In a lab test using a 1200°C burner flame, a millimeter-thick piece of the new thermoplastic resists the heat for well more than 25 minutes.
Innovative Material for Busbars and Battery Housings
Quantix® ULTRA therefore meets the high flame retardancy requirements of electromobility. It is suitable to ensure safety around the drive battery of an electric car. The plastic could prevent a fire's spread from the battery to the electric car or at least slow it significantly. More specifically, Quantix® ULTRA could be used for the casing for conductor rails, the so-called busbars, especially since the plastic is an outstanding electric insulator and helps to prevent short-circuits. Due to its unique flame resistance compared to aluminum, the material would also come into consideration as a material for battery housings. One international automaker will be starting to install components made of Quantix® ULTRA to regulate the temperatures of drive batteries. “With the products we have already developed, we were able to attract interest at international trade fairs,” said Marco Sutter, Global Market Segment Manager at Freudenberg Sealing Technologies. “As a result, we were able to initiate projects with other customers in the area of battery safety.”
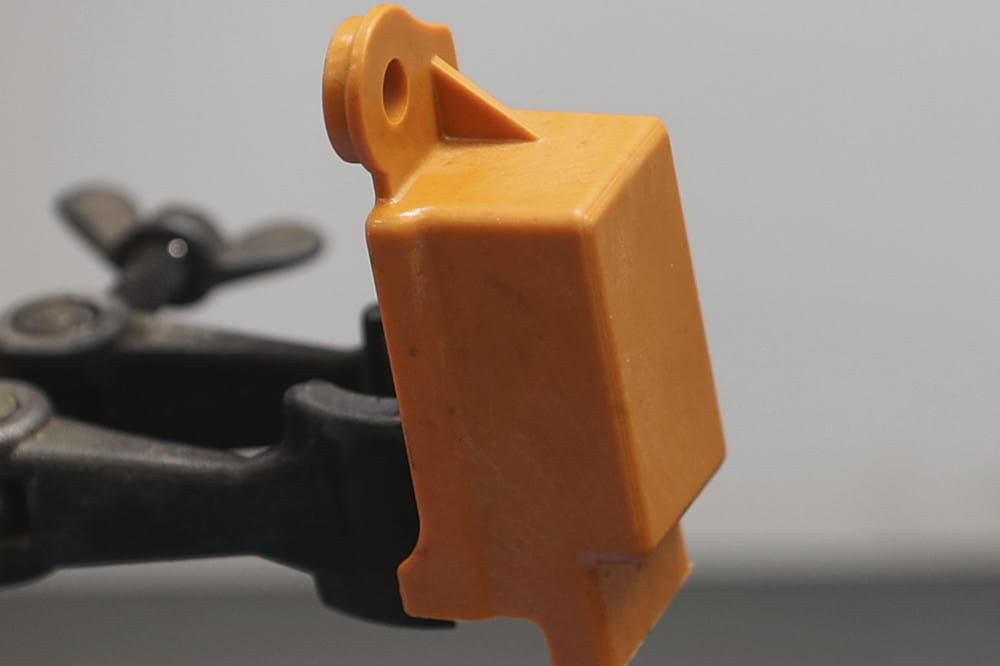
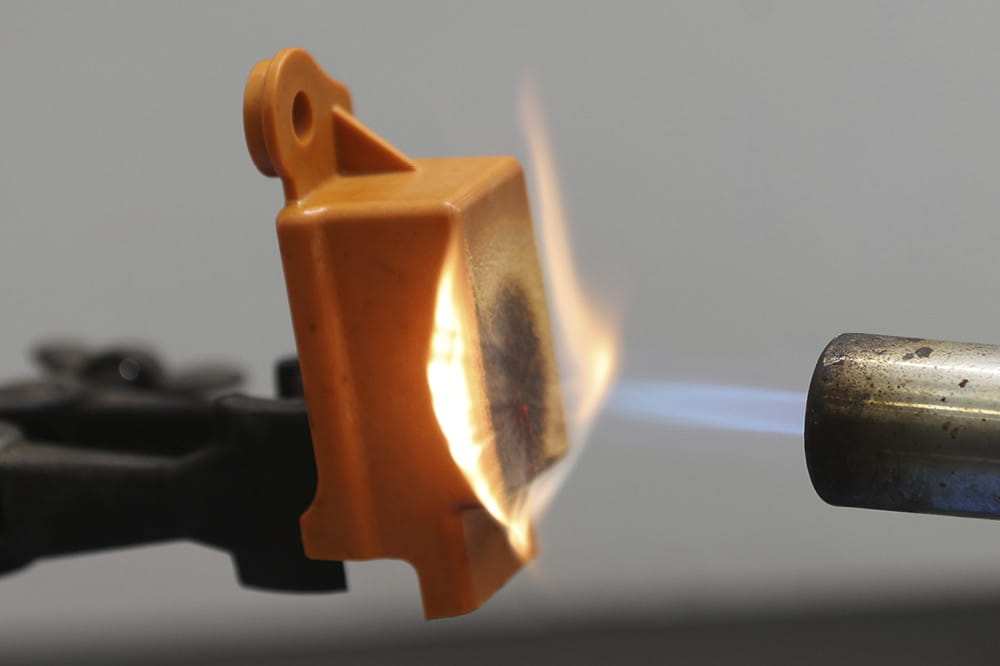
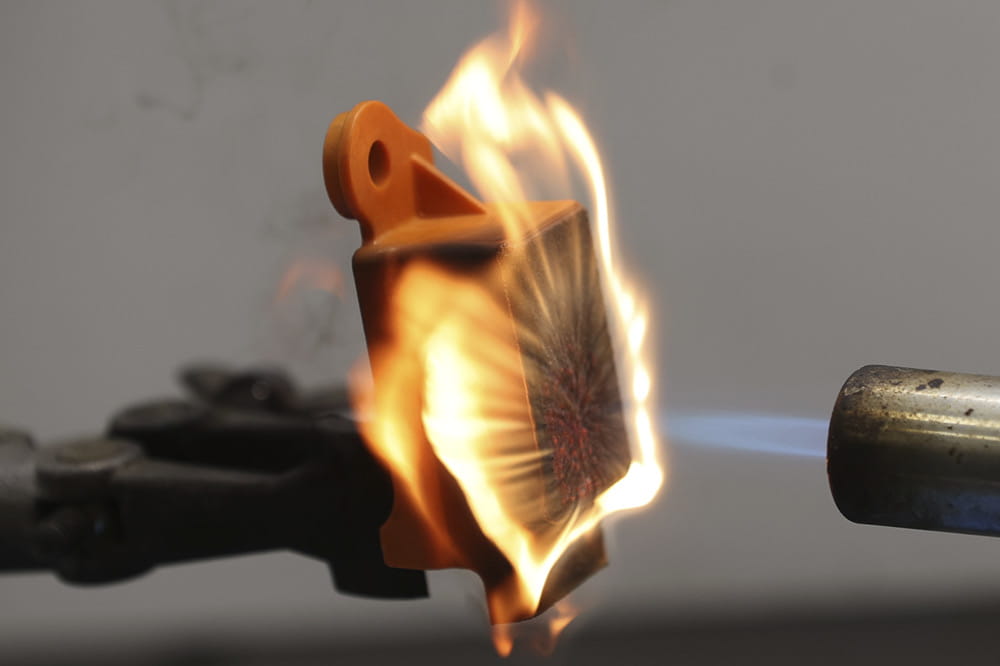
Another advantage of Quantix® ULTRA is that it offers the greatest possible design freedom that injection molding manufacturing allows. “We can meet specific customer desires down to the smallest detail,” said Kira Truxius, Material Expert Thermoplastics, at Freudenberg Sealing Technologies. “For example, mounting clips can be integrated into the desired part during production without difficulty. Providing large volumes is just as feasible as the production of large components in short cycle times.”
Joint Research Brings Fast Results
Incidentally, the initial impetus for the development of Quantix® ULTRA dates back to a strategic decision by the Freudenberg Group. It cleared the way for research into new materials that were supposed to play out their strengths under extreme operating conditions. Expertise from an interdisciplinary employee team flowed into the strategic program. The team first chose the high-performance polymer polyaryletherketone (PAEK) as the base material. They modified its characteristics with cross-linking agents while gathering valuable insights into the ideal production process. With the filing of the first patents in 2018, the Quantix® ULTRA family of materials was born. Their distinguishing characteristic: They lend themselves to tailor-made solutions to customer problems in a wide variety of markets. The spectrum ranges from a reduction of friction and abrasion in the food industry all the way to the above-mentioned electrically-insulating, flame-resistant components for electric mobility.
Compounding in the Injection Molding Process
To achieve its flame-resistance goals, the Quantix® ULTRA project group had to do more development work. Materials based on PAEK were expected to be cost-prohibitive for automakers. By turning to polyketone, the project group chose a more affordable technical polymer that could achieve the desired features through cross-linking. Design freedom was also a requirement, to allow the material to be shaped into any desired form during the production process.
For this, the team refined their newly developed material in the production process. The cross-linking took place in one step via the injection molding process. “We are dealing with an in-line process here,” Truxius said. “It takes place with injection molding. Quantix ULTRA arrives directly into the predesigned injection molding cavity.” The final product no longer melts and withstands extremely strong flame exposures. “With Quantix® ULTRA in the in-line injection molding process, we have shown that we can bring innovations to market quickly thanks to the know-how that we have gained. It took us just two years to go from the first ideas to market readiness,” she said. “This highlights our expertise in the development of recipes, production processes and products – the perfect triad.”
With Quantix® ULTRA in the in-line injection molding process, we have shown that we can bring innovations to market quickly thanks to the know-how that we have gained. It took us just two years to go from the first ideas to market readiness.
Kira Truxius, Material Expert Thermoplastics at Freudenberg Sealing Technologies
Sustainable and Flexible Production Process
The desired characteristics of Quantix® ULTRA can be targeted with the admixture of filler and reinforcing materials. For example, the addition of fibers can impart extra form stability and strength. Here Freudenberg Sealing Technologies ensures that the processing and cross-linking are in a good balance with one another. “The material that we developed does not exclude any fillers or reinforcing materials,” Hellbach confirmed. “That means all options are open to us for the cross-linking, which gives us a unique position in the market.”
The sustainability of the production process also appeals to customers. This factor influences the CO2 footprint of their end products. Compared to conventional polyamide 6.6 (PA 66), the production of polyketone, a base material of Quantix® ULTRA, produces very little CO2. The so-called emissions factor is 61 percent less and represents 2.8 kilograms of CO2 per kilogram of granulate. Another factor comes into play: While prior cross-linking processes for thermoplastics relied on gamma radiation or took place in solvents, the Freudenberg process totally does without solvents and is thus more economical and sustainable.
To sum up, Quantix® ULTRA represents a new class of plastic materials. They currently stand at the pinnacle of all technical plastics when it comes to flame resistance. And that makes the composite a sought-after material to increase battery safety in electric cars and to curb fire hazards in an emergency. Once again Freudenberg Sealing Technologies is highlighting the full extent of its support for electric mobility with innovative products.
Read more stories like this in ESSENTIAL, Freudenberg Sealing Technologies’ corporate magazine that covers trends, industries and new ideas.
More Stories About E-Mobility
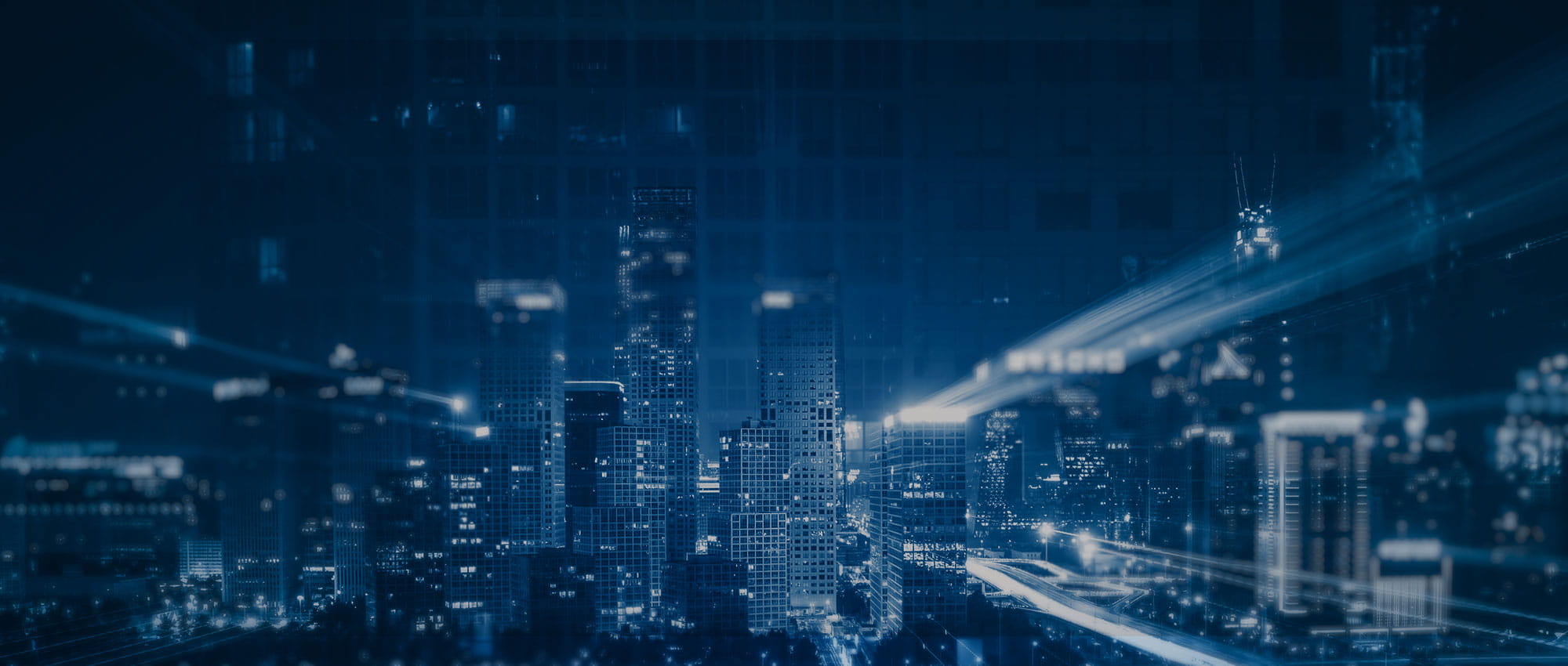
Join Us!
Experience Freudenberg Sealing Technologies, its products and service offerings in text and videos, network with colleagues and stakeholders, and make valuable business contacts.
Connect on LinkedIn! open_in_new