Obtain news and background information about sealing technology, get in touch with innovative products – subscribe to the free e-mail newsletter.
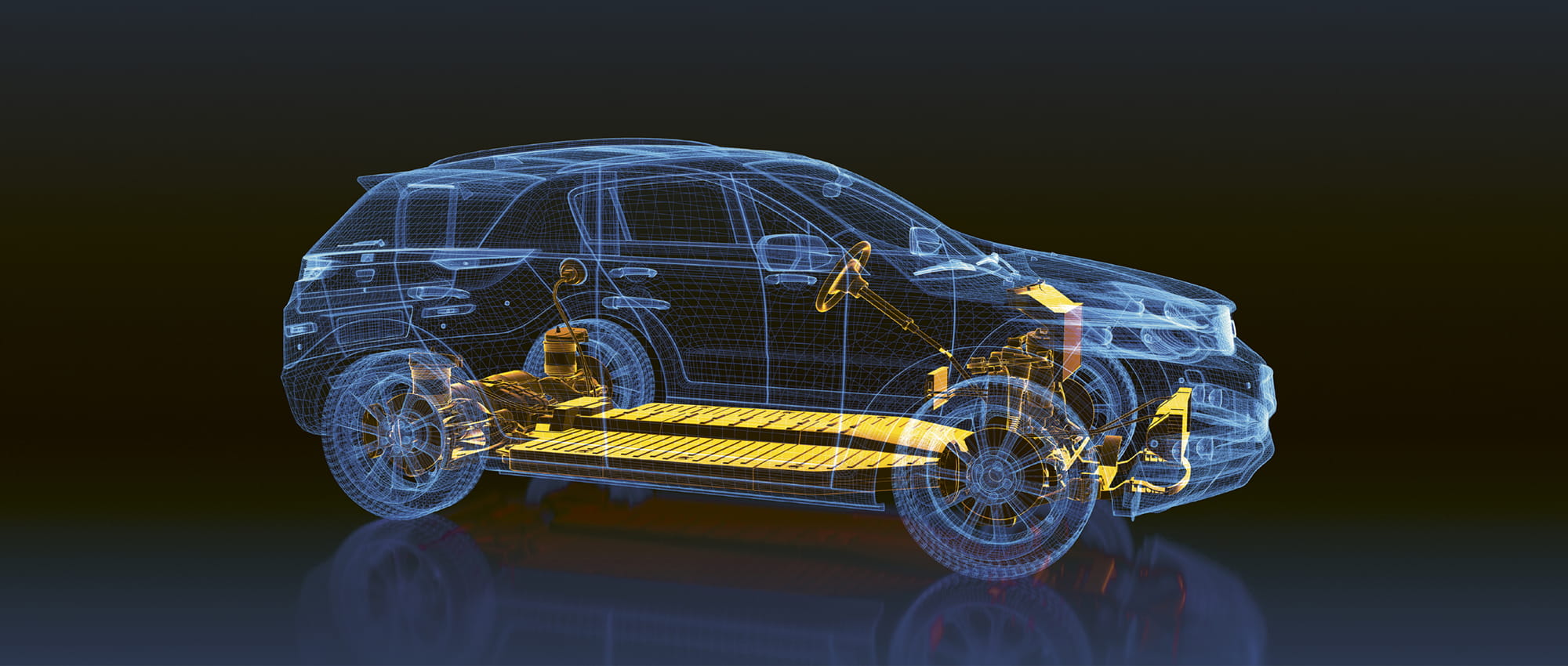
Reliable Seals for Busbars in E-Mobility
Copper or aluminum busbars ensure the flow of electricity in the drivetrains of electric vehicles. However, their rectangular cross-sections make these conductor rails hard to seal. But that concern is a thing of the past, thanks to an innovation from Freudenberg Sealing Technologies.
Initial Situation
Busbars are built into many different applications to handle high levels of electric current. Manufacturers of electric vehicles like to use these robust rectangular conductor rails. For example, in the car’s charging system, battery management system and the electric drivetrain. Since electric cars often have oil-cooled electric motors, the sensitive power electronics of their inverters have to be protected against leaks. One potential entry point for the oil is the conductive busbar, which is encased in a plastic housing. So, it is important to seal the gap between the two components effectively.
The Problem
As a matter of fact, the busbar’s rectangular cross-section is technically challenging for manufacturers of conventional seals. Unlike round designs, the corners of the conductor rail make it harder to compress the sealing material evenly onto the surface. The seals, therefore, remain susceptible to leaks as the copper heats up and expands while conducting electricity, and contracts when it cools. The process of constant expansion and contraction occurs more quickly for copper than with plastic and sealing materials. This makes it easier for fluids to slowly penetrate the part.
The Solution
Previous sealing solutions have not been sufficiently reliable in preventing leaks. They have also required extra space, which has an impact on the design of the busbar module. That is changing with the innovative elastomer seal from Freudenberg Sealing Technologies. The highlight: It doesn’t produce a mechanical connection – it brings about a chemical bond between the components. With the application of heat, the molecule chain of the sealing rubber bonds integrally with the copper and the plastic. Three components become one part, which prevents the intrusion of oil even at temperatures far above 100°C (212°F).
This article originally appeared in ESSENTIAL, Freudenberg Sealing Technologies’ corporate magazine that covers trends, industries and new ideas. To read more stories like this, click here.
More Stories About Renewable Energy
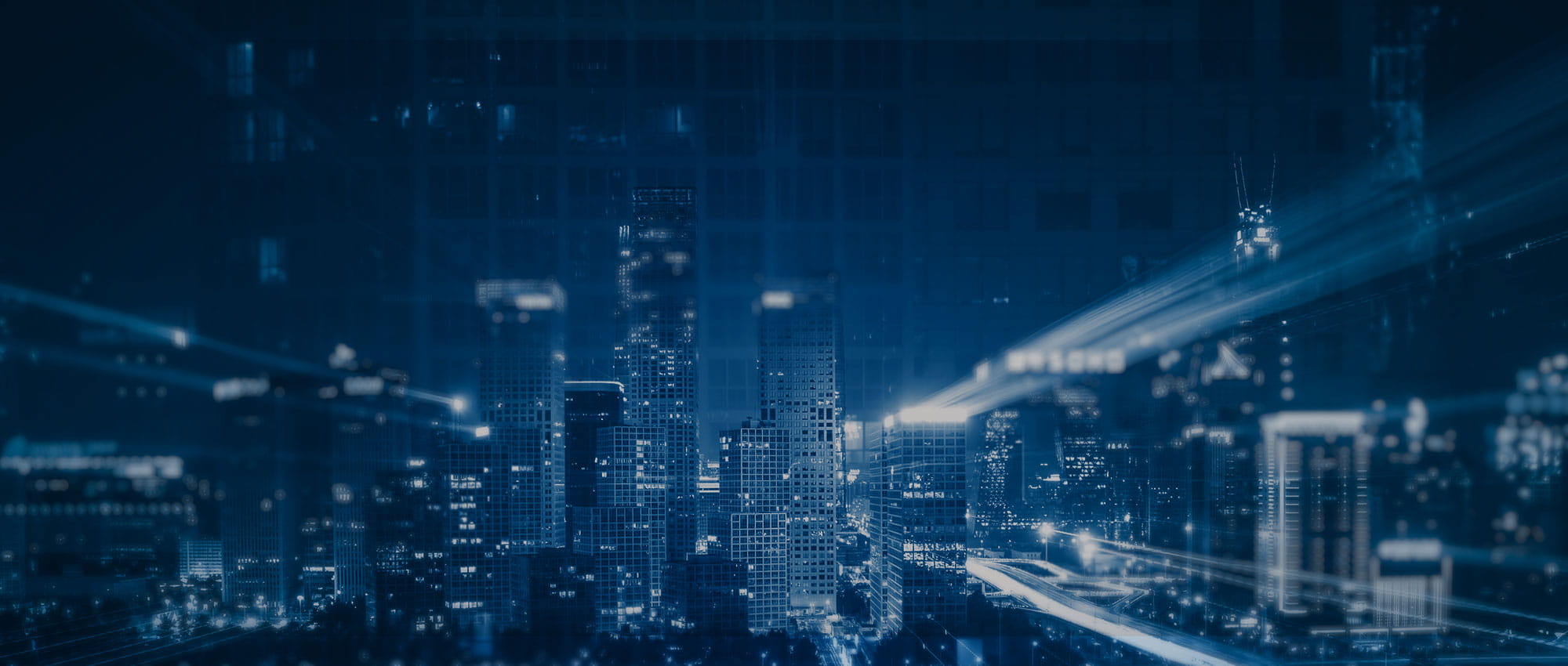
Join Us!
Experience Freudenberg Sealing Technologies, its products and service offerings in text and videos, network with colleagues and stakeholders, and make valuable business contacts.
Connect on LinkedIn! open_in_new