Obtain news and background information about sealing technology, get in touch with innovative products – subscribe to the free e-mail newsletter.
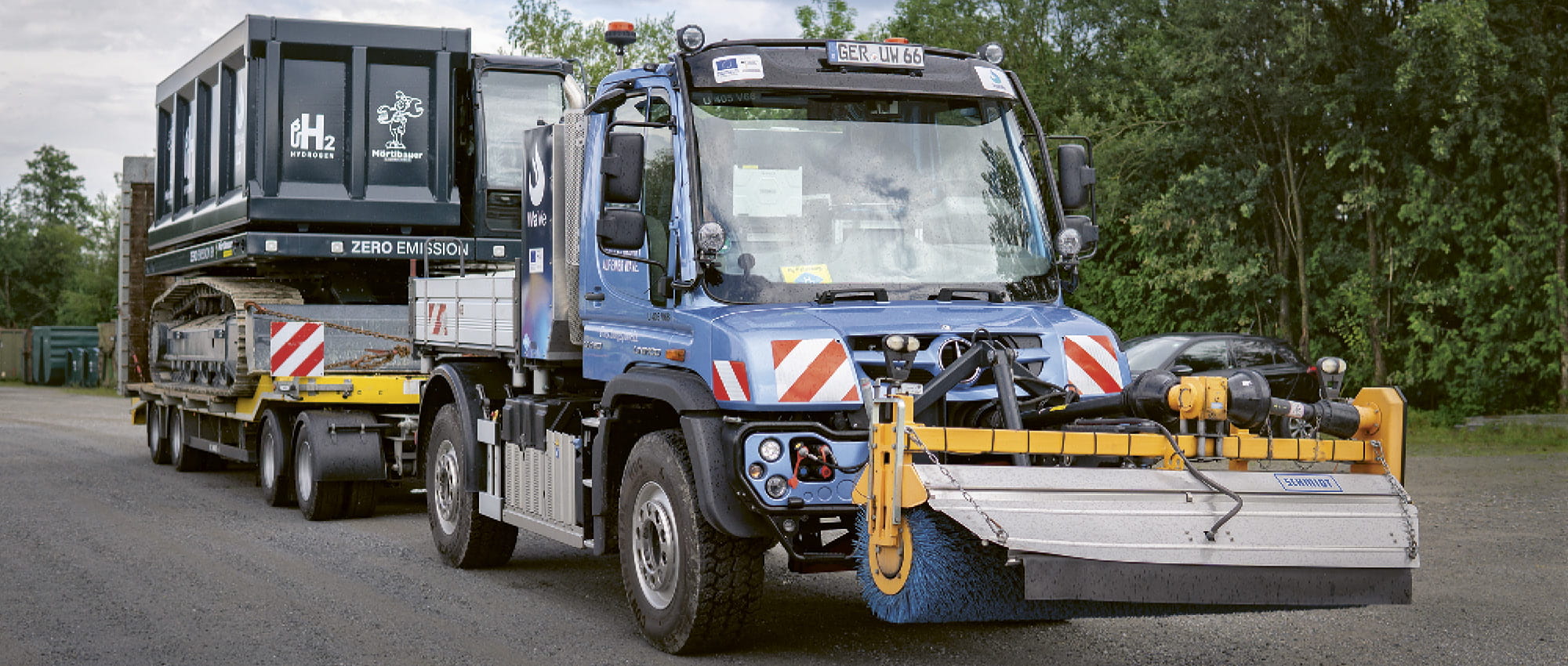
10.12.2024 | Story
“An Alternative for Demanding Applications”
Hydrogen engines have come a long way technically and are ready for series production. In many cases, they can directly replace a conventional internal combustion engine.
On land, in the water or in the air: Combustion engines propel vehicles and generate electricity in stationary equipment. Ideally that’s what we will see in the future – an environmentally-friendly and carbon-neutral technology, without CO2 emissions or other pollutants. This scenario focuses on hydrogen as a fuel. Instead of fossil fuels such as gasoline or diesel, it is hydrogen that ignites in the engine’s combustion chamber, providing the drive energy. The combustion is clean – only water vapor and nitrogen oxides result as waste. If the hydrogen is produced carbon-neutrally, no CO2 emissions are involved. This makes the hydrogen engine a good alternative to battery-electric drives or fuel cells.
The technology is quite advanced. Major engine manufacturers have introduced the first hydrogen engines or are preparing for series production. They are zeroing in on applications where diesel engines have largely been successful.
Deutz is one example. Its TCG 7.8 H2 hydrogen engine generates 220 kilowatts (299 horsepower) and develops 1,000 newton meters of torque. It is based on the TCD 7.8 diesel six-cylinder engine. The hydrogen version can be used wherever the diesel is used – and with the same displacement, 7.8 liters, the company says. Series production is set for late this year. The first customer, a Chinese company, envisions using it as a stationary unit to power an electric generator.
Engine Conversion Is Necessary
Hydrogen engines benefit from the fact that combustion technologies are very advanced, engine manufacturing is well-established, and the service networks are dense. Still, it’s not just a matter of giving a diesel engine the other fuel. “A conversion is required. For example, the seals must be geared to hydrogen. The injection system, in particular, has to be totally reworked to achieve efficiencies similar to those for diesel fuel,” said Robin Möller, Global Segment Director, Power Generation, Freudenberg Sealing Technologies. “The hydrogen engine is a further development of well-known combustion technologies and is viewed as a way to reduce emissions in demanding applications in the medium and long term future. That makes products for hydrogen combustion an integral part of our hydrogen strategy.” The company has an excellent starting point: It has decades of experience with developing and manufacturing the many different seal components for combustion engines that consume natural gas.
Our customers see Freudenberg Sealing Technologies as an innovation partner. As we advise them, we draw on our in-depth knowledge of seals, including materials, designs, and production processes.
Robin Möller, Global Segment Director, Power Generation at Freudenberg Sealing Technologies
But the demands on seals in hydrogen engines are much greater than those for conventional models. There are two main goals here: The first is to minimize hydrogen permeation – that is, the escape of this extremely volatile gas from the system, and its penetration into the sealing material. The second is to maintain the seals’ lifespans during the engine’s operating life and maintenance cycles, despite the chemical and mechanical factors in play.
Filling up as usual: It only takes a few minutes at the fueling station to give a hydrogen vehicle its full range. © Alamy/imageBROKER/Jochen Eckel
High-tech Sealing Materials Are Available
“The selection of the sealing material is crucial,” Möller said. “We not only have very broad knowledge of materials but also have the high-tech materials for hydrogen applications available.” As in the case of traditional internal combustion engines, the company is using its wide-ranging expertise to help perfect the new hydrogen engines, he added. “The first step is reliable operation. In parallel, engine developers are improving efficiency to make their fuel consumption as low as possible.”
The U.S. company, Cummins, is one of the world’s largest engine manufacturers and has already exhibited the B6.7H hydrogen engine. It generates 216 kilowatts (290 horsepower) and 1,200 newton-meters from a displacement of 6.7 liters. Cummins says the assembly is based on a completely new engine platform to optimize power density, frictional losses, and thermal efficiency. As a result, the engine offers the same performance as a comparable diesel engine and is completely compatible with its existing drivetrain, transmission and cooling system. Another B6.7H advantage is that it is much quieter.
As a test, the hydrogen engine has been installed in a standard truck in the 10- to 26-ton gross-vehicle-weight-class commonly used in distribution. There is no difference in road performance, payload, or cargo space. Maintenance and the costs associated with it are comparable to diesel engines. Cummins says the solution is a cost-effective technology to drive the decarbonization of the transport sector. Its concept truck stores the hydrogen in two 700-bar, high-pressure tanks, giving it a range of up to 500 kilometers (311 miles) – enough for typical every day operations and more than the range for a comparable truck with a battery-electric drive. The two tanks can be refilled in just 10 minutes. Cummins is also working on its X15H hydrogen engine with a displacement of 15 liters for heavy commercial vehicles.
Stationary Use of Hydrogen Engines
Hydrogen engines are also an important option for stationary equipment, Möller said. “Emergency generators are one example. The spectrum extends to very large versions with several megawatts of output for institutions such as hospitals, airports, and data centers.” The lifespan of these large engines is 20 to 30 years, and seals must maintain their function over that time.
“Our customers see Freudenberg Sealing Technologies as an innovation partner. As we advise them, we draw on our in-depth knowledge of seals, including materials, designs, and production processes. We continually invest in research and development as well, to further improve the performance and lifespan of our seals,” he said. This includes research into new materials and production processes to meet rising requirements. “That’s how to get the best possible results and advance hydrogen technology,” Möller concluded.
The Future Is Hydrogen
From H₂ Production to Usage: Comprehensive Insights on Production, Distribution, Storage, and Future Applications with Solutions. Explore full spectrum in our webspecial!
Hydrogen Webspecial open_in_newMore news on the subject E-Mobility
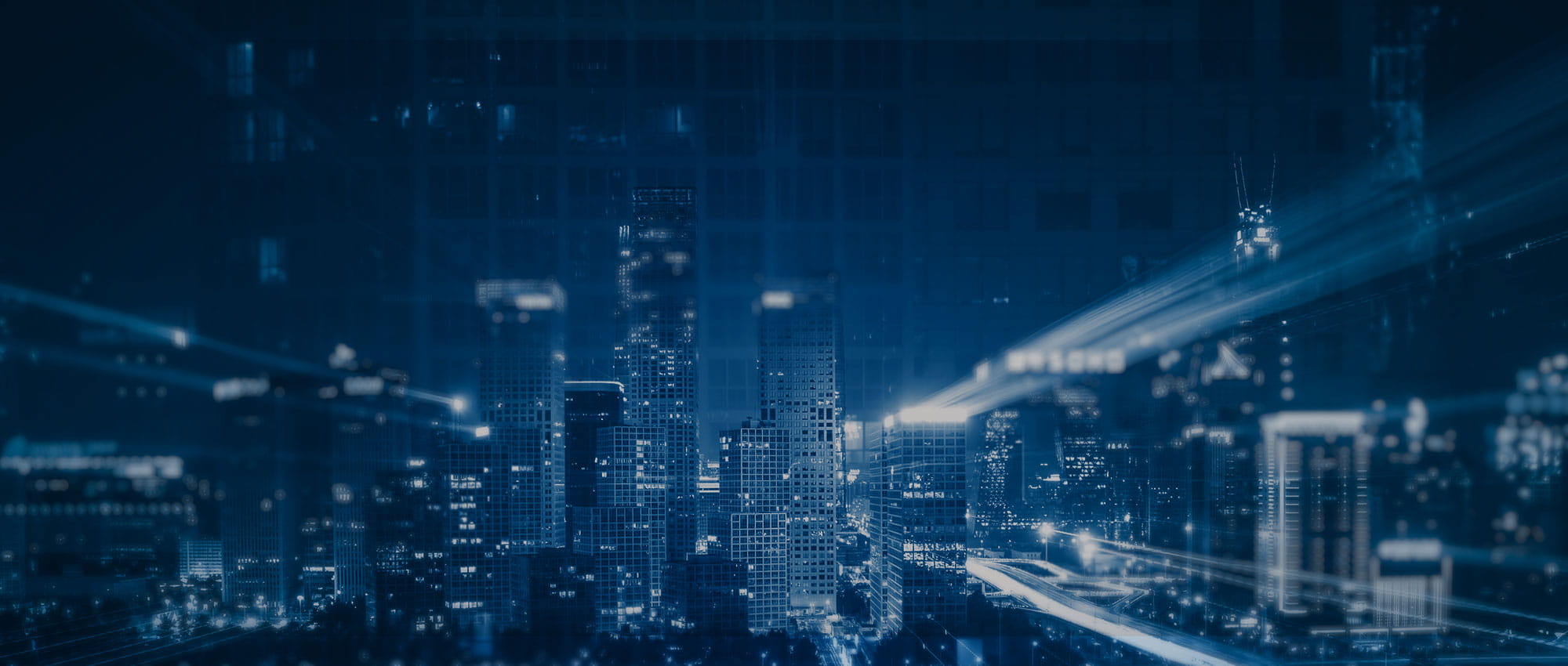
Join Us!
Experience Freudenberg Sealing Technologies, its products and service offerings in text and videos, network with colleagues and stakeholders, and make valuable business contacts.
Connect on LinkedIn! open_in_new