Obtain news and background information about sealing technology, get in touch with innovative products – subscribe to the free e-mail newsletter.
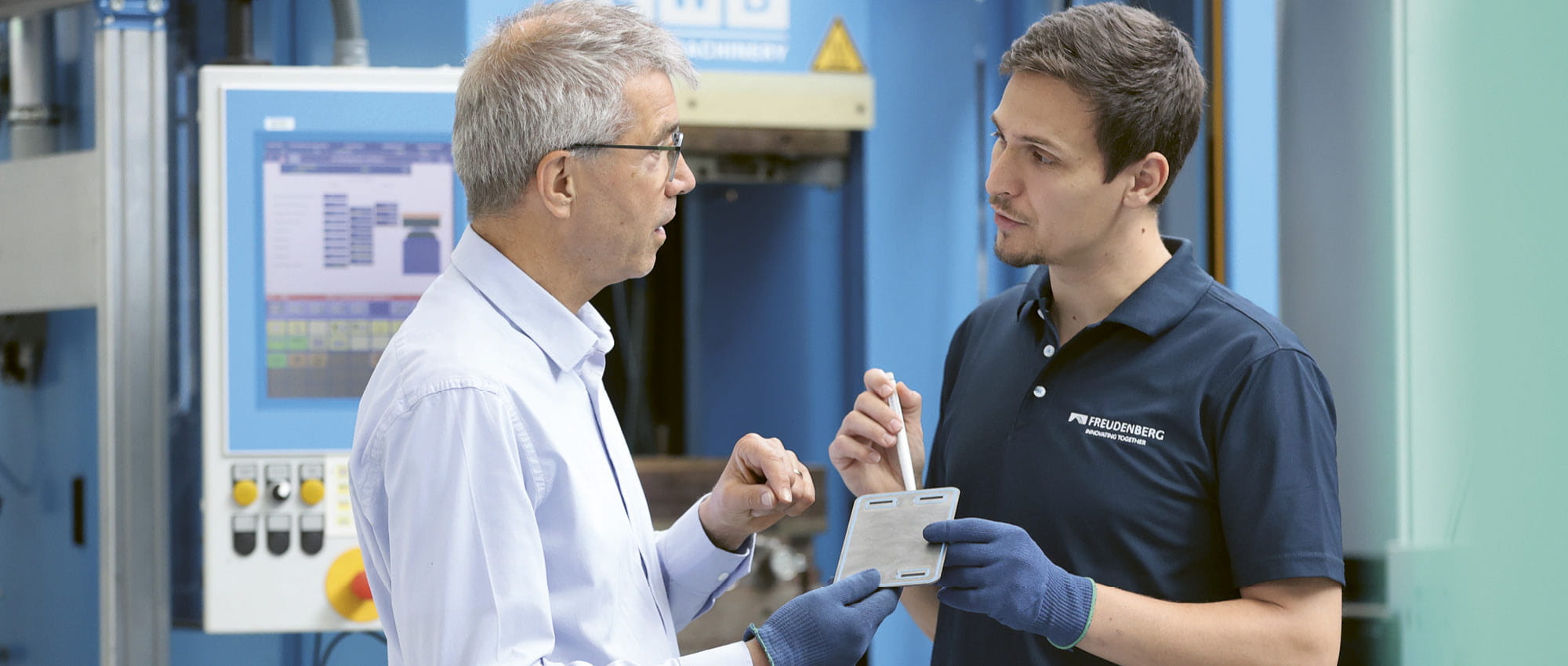
03.12.2024 | Story
The Perfect Fuel Cell Seals, Integrated Quickly
Fuel cells make sense as a powertrain technology for heavy-duty transport. Seals perform important tasks in these applications. The right seal material has to be selected. In addition, integrated solutions are in demand for manufacturing processes.
Jürgen Emig and Dr. Alexander Hähnel believe in fuel cells and their future prospects. After all, the technology has what it takes to decarbonize industrial sectors. It also has advantages over other types of powertrains. “Fuel cells allow greater ranges than those for battery-electric vehicles, and they are more efficient than synthetic fuels,” said Hähnel, a materials specialist at Freudenberg Sealing Technologies. “In addition, the energy costs for fuel cells per kilometer driven are about 50% less than for e-fuels.” Even with those advantages, the two experts see the breakthrough coming first in heavy-duty transport and stationary facilities. “Unlike passenger cars, there is already a very attractive market in trucks, buses, construction equipment, logistical vehicles, ships and aircraft,” said Emig, who is Director, Pre-Product Development Hydrogen Applications, at Freudenberg Sealing Technologies.
We know the technology inside and out. We know what is important for seals.
Jürgen Emig, Director, Pre-Product Development Hydrogen Applications at Freudenberg Sealing Technologies
Economies of Scale Thanks to Integrated Sealing Solutions
Efficient production is an important success factor for fuel cells. One way to achieve it is the rapid integration of hundreds of seals in fuel cell stacks. “In the auto industry, we are known for manufacturing our products in high volumes with reliable processes,” Emig said. “That is exactly what fuel cell producers are looking for in the seals they need.” The industry wants to be ready when the demand for fuel cells picks up. To achieve the right economies of scale, intricate seals must also be applied to the fuel cell’s bipolar plates, plastic film or gas diffusion layers using an automated process. Until now, the work has taken place in separate process steps. By contrast, Freudenberg Sealing Technologies can apply the seals directly onto the substrates that the customer desires during the injection molding process. “Since we can also manufacture bipolar plates and gas diffusion layers, customers would get everything from us as a single source,” Hähnel said. In any case, it will take Integrated solutions such as sprayed-on seals to achieve high cycle rates cost-effectively and to avoid scrap.
Freudenberg could become a key problem-solver since it has been deeply involved with fuel cell technology for more than 20 years – even as the general hype surrounding it has subsided. “We know the technology inside and out. We know what is important for seals,” Emig said. The company is serving the entire fuel cell periphery with components – from valve seals to the pressure equalization element DIAvent®. In the stacks, gaskets are being used to seal individual cells or bipolar plates firmly against one another. They keep the hydrogen in and unwanted media out.
High-performance Elastomer
The right seal material is also crucial. “In fuel cell polyolefin (FCPO), we have a material that is being installed in series-production, low-temperature PEM (PEM: proton exchange membrane) fuel cells,” Hähnel said. The strengths of FCPO are self-evident since it is impermeable. Even small hydrogen molecules can only cross it slowly. Fuel cells are often very sensitive to harmful substances like those often found in rubber compounds. These substances gradually reach the fuel cells from the seals, which reduces their performance. But FCPO contains no harmful substances. The elastomer has a longer lifespan than standard silicone solutions and withstands temperatures up to 120°C (248°F), even in contact with water and typical coolants. Another advantage: When FCPO is applied to a bipolar plate, overhead installation is possible without a bonding agent, as the material securely adheres in any position. The material alone offers sufficient adhesion, but it does not stick to other components. That means it meets the requirement for mono-material recycling. With FCPO and creative ideas for integration, Freudenberg Sealing Technologies is breaking new ground in the manufacture of fuel cells at competitive prices.
The Future Is Hydrogen
From H₂ Production to Usage: Comprehensive Insights on Production, Distribution, Storage, and Future Applications with Solutions. Explore full spectrum in our webspecial!
Hydrogen Webspecial open_in_newMore news on the subject E-Mobility
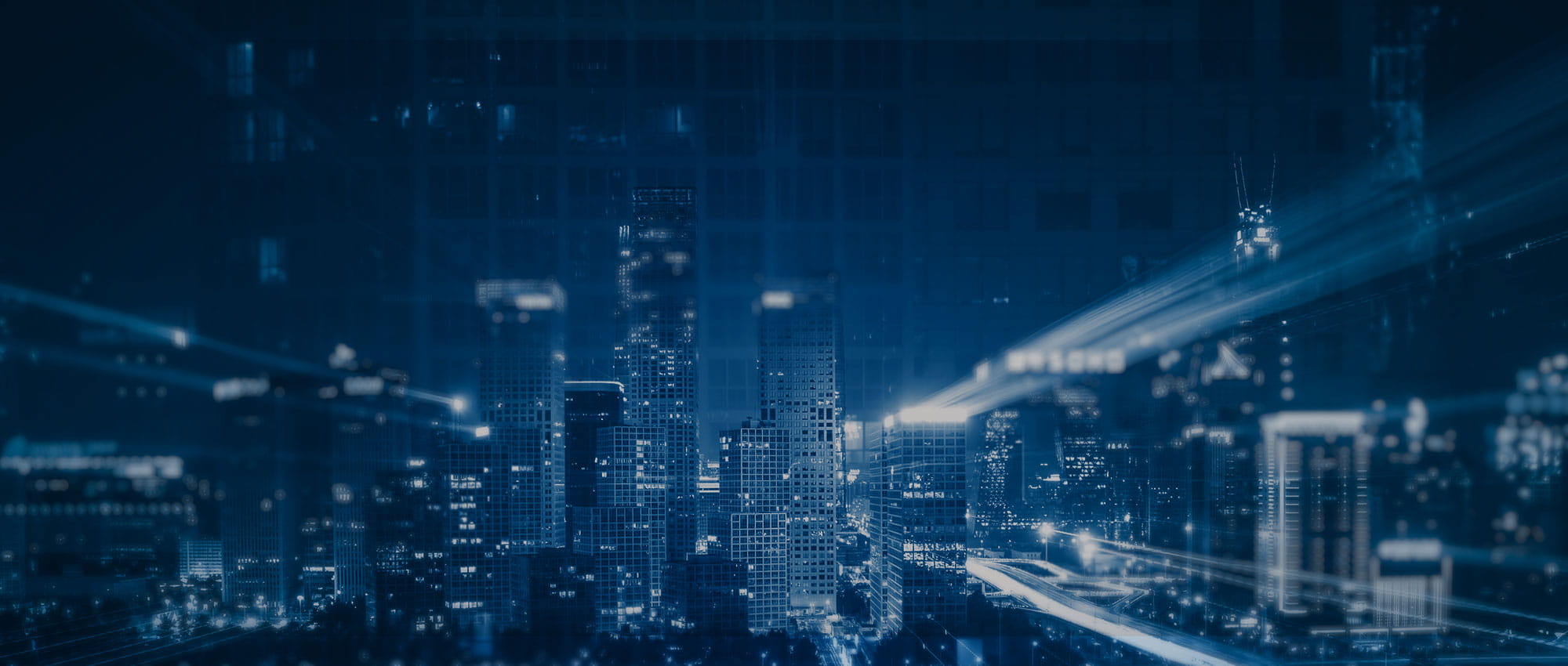
Join Us!
Experience Freudenberg Sealing Technologies, its products and service offerings in text and videos, network with colleagues and stakeholders, and make valuable business contacts.
Connect on LinkedIn! open_in_new