Obtain news and background information about sealing technology, get in touch with innovative products – subscribe to the free e-mail newsletter.
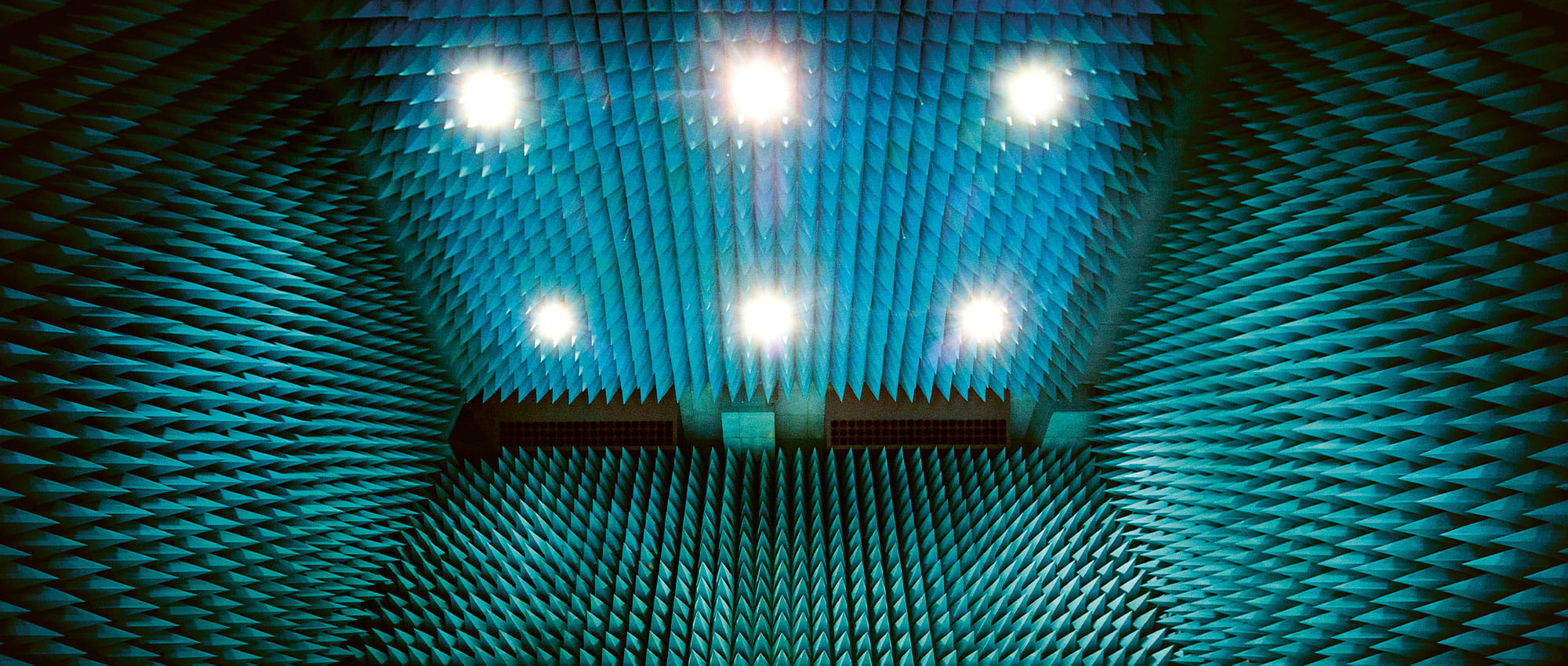
11.04.2022 | Story
Uninterrupted Lightness
Plastics can do more than just insulate – they can conduct electricity as well. Where would something like that be needed? The electric car of the future, to cite just one example. With the help of special plastics and coatings from Freudenberg Sealing Technologies, a vehicle can shed a few pounds.
Wherever electricity flows, electric and magnetic fields are generated. In an electric powertrain, however, the electricity seldom flows in one direction. (The exceptions are during certain charging processes.) The car’s power electronics send alternating current at high frequencies into the veins of the electric motor, which – depending on its design – runs at rotational speeds up to 30,000 rpm. Field strengths change at a corresponding rate, producing electromagnetic waves that move through the space at the speed of light. If they are not stopped, one major result will be the disruption of the many control units on board, and maybe even in a car stopped at the same traffic light. The only reliable option in the battle against electromagnetic waves is to confine electric components to a housing made of an electrically or perhaps magnetically conductive material or whose electrically conductive surface reflects the waves.
We have developed various cost-effective alternatives for large-scale production.
Volker Schroiff, Director, Technology Management, at Freudenberg Sealing Technologies
Plastics to Replace Aluminum
In the current generation of electric cars, the housings for batteries, motors and power electronics are made of aluminum – almost without exception. First of all, it is a good conductor of electricity. Second, it is a lightweight metal with a low specific weight. In addition, it is easily processed with pressure-casting, making it a low-cost option. To the experts at Freudenberg Sealing Technologies, all this is good – but not good enough – since every pound of excess fat has an impact on the vehicle’s range. If you could replace the aluminum components with plastics, you could reduce the vehicle’s weight even more. But there is an obstacle: You need an electrically conductive plastic for this. This form of plastic does exist, but it is quite expensive and is almost exclusively used in the manufacture of electronics, including displays.
One Goal, Multiple Paths
“These intrinsically more conductive plastics – that is, plastics that are conductive by their very nature – have proven to be too costly,” said Volker Schroiff, who is in charge of Technology Management at Freudenberg Sealing Technologies. “But for large-scale production, we’ve developed various alternatives that are less expensive.” The first alternative is a plastic housing with a conductive coating, which is applied like paint. Along with colleagues at the Special Sealing business unit, Schroiff is working on a way to industrialize the process. The second alternative is to impart plastic particles of a conductive material to a nonwoven before the injection molding stage. The advantage of this approach: No additional steps are needed in the production process. This offers cost advantages, especially for relatively small components. And in the end, there is a third approach that is well-suited to large surfaces – such as the housing cover for a traction battery. After a nonwoven’s fibers have been given an electrically conductive coating, the material is inserted into a mold where a plastic part is produced. “We’re working closely with the nonwovens experts at Freudenberg Performance Materials on this solution,” Schroiff said.
Starting with an annual production of at least 30,000 parts, these special plastics from Freudenberg Sealing Technologies are less costly than aluminum.
There were a number of findings from the first pilot projects, which involved three large, direct suppliers of electric powertrains: The ideas derived from the physics of electromagnetism perform well in practice – that is, in real-life components. And at the point where output reaches at least 30,000 parts a year, the special plastics from Freudenberg Sealing Technologies have a cost advantage over aluminum. Meanwhile, Schroiff is already moving in a new direction. In the future, the conductive layer could also consist of a razor-thin elastomer, manufactured in a single mold along with the housing, using the two-component injection molding process. The elastomer serves as a protective shield against electromagnetic waves, even as it seals against liquid and gaseous media.
A Plastic That Shields Against Magnetic Fields
Today Schroiff and his team are dealing with yet another challenge posed by electric vehicles. Conversations with customers have sensitized them to the need to shield against magnetic fields in the kilohertz range. The magnetic fields surrounding an electric drive system are harmful to humans. So far, manufacturers have had to resort to workarounds to mitigate them, and aluminum is not a complete solution to the problem. So why not identify a plastics-based solution here as well? “We had not made progress in this area with our past approaches. So we built a test stand to do more analyses, to identify reliable shielding options and run tests on them,” Schroiff said. The results are promising and have already been presented to original equipment manufacturers. He is confident about the future. “We are on track for a solution with a hybrid technology that we developed, and we have piqued the interest of manufacturers. We are now taking the next steps. Our goal is to produce a prototype,” he said. With this approach, the plastic would keep electric as well as magnetic fields in check, killing, so to speak, two birds with one stone.
More news on the subject E-Mobility
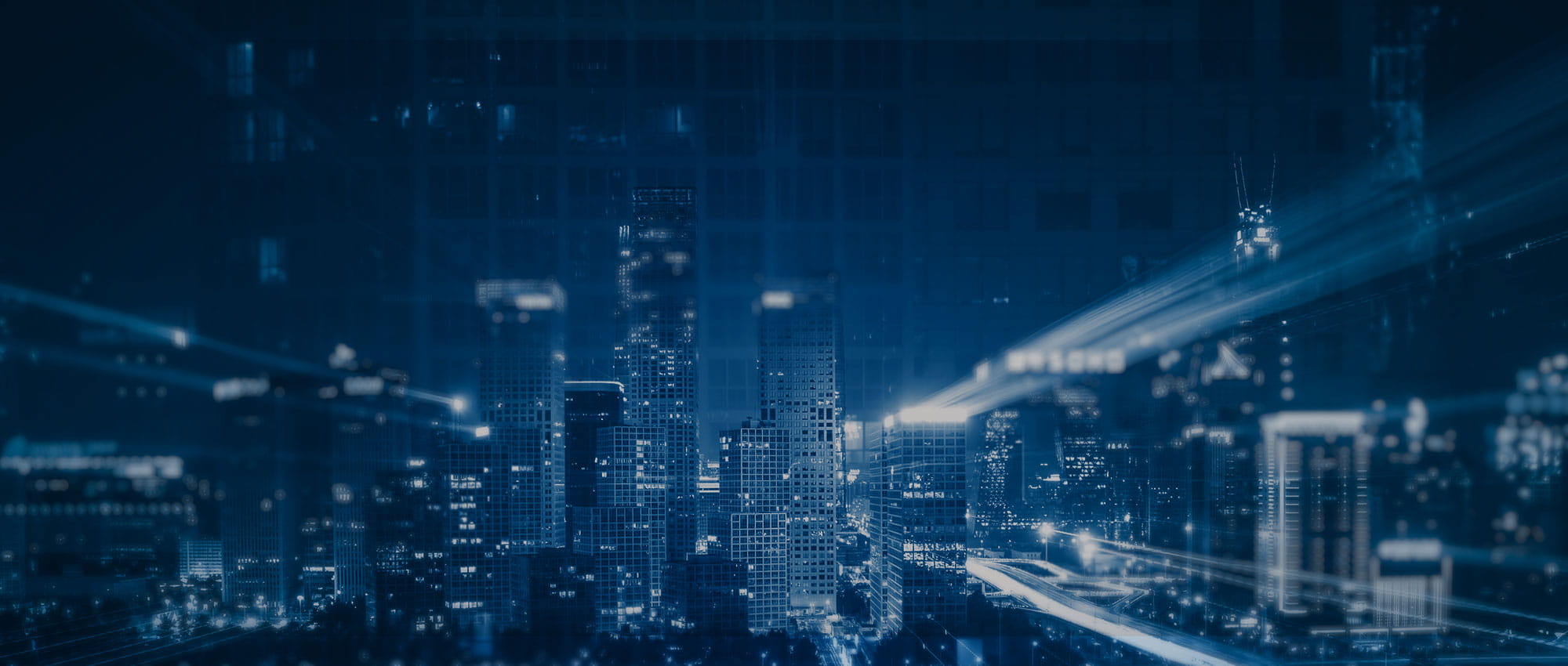
Join Us!
Experience Freudenberg Sealing Technologies, its products and service offerings in text and videos, network with colleagues and stakeholders, and make valuable business contacts.
Connect on LinkedIn! open_in_new