Obtain news and background information about sealing technology, get in touch with innovative products – subscribe to the free e-mail newsletter.
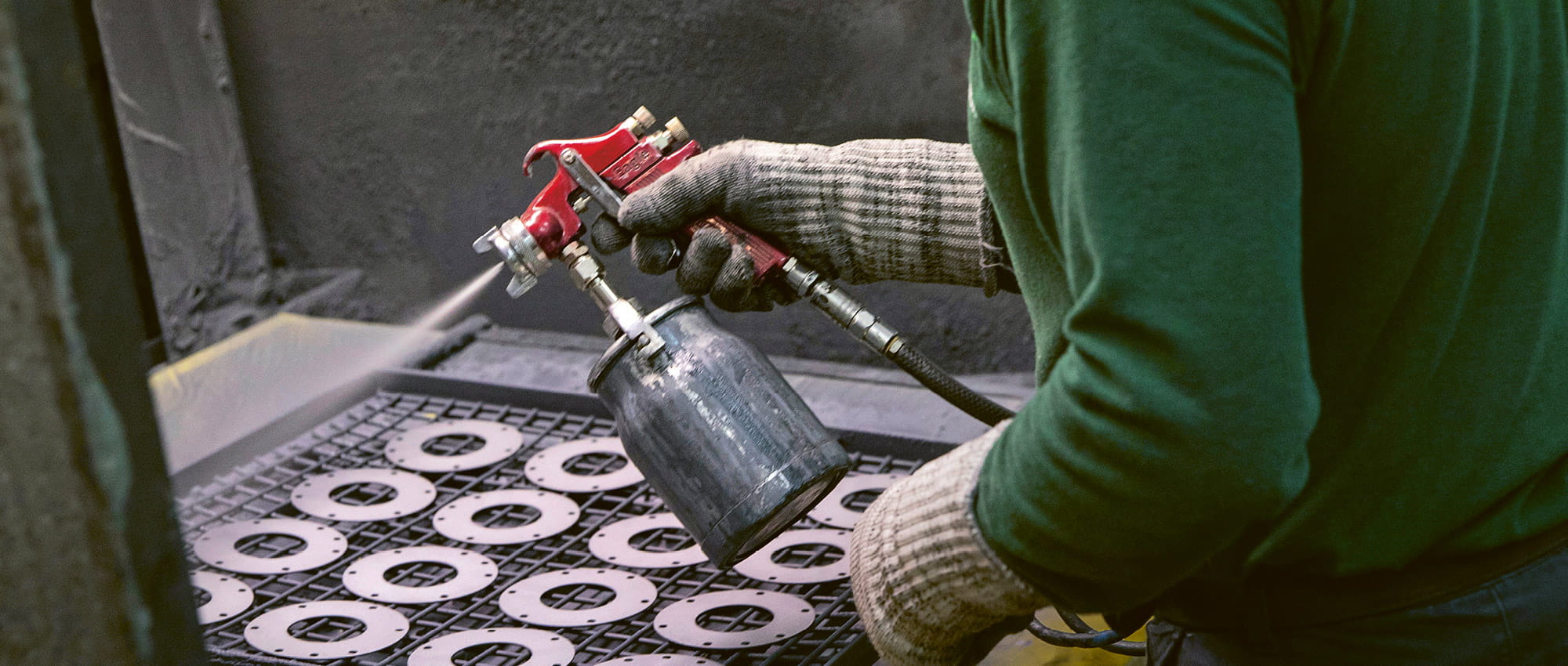
Metflex - An Addition to the Family
Metflex has been part of Freudenberg Sealing Technologies since mid-2017. The medium-sized company not only offers materials with unique quality but it also has a strong position in the natural gas market.
People know all about robust materials here, in the northern reaches of the Manchester and Liverpool industrial region. Once it was bricks from Accrington that earned a worldwide reputation. For example, the foundation of the Empire State Building is composed of the high-strength clay mined here. Today it is unique materials used in the natural gas industry. At first glance, the material that Steve Parry is holding seems anything but tough. But the fiber-reinforced diaphragm is five times as durable as any conventional elastomer. It is used in gas meters, where it continually stretches and retracts, in line with the amount of gas consumed, over a period of 20 years. Neither fluctuating ambient temperatures nor material aging can be permitted to disturb the precision of its deflection. That measurement – which determines what the consumer pays for his gas supply – is only as accurate as the diaphragm permits. In this application, an expansion of the diaphragm of just 200 µm can determine success or failure.
Environmentally friendly energy carrier
Parry, who is in charge of material development in Blackburn-based Metflex, won’t reveal the secret behind “Dispersed Fibre Technology” (DFT). At its core, it involves strengthening the flexible elastomer diaphragm in specific targeted zones by introducing certain particles. This occurs when the base material – already mixed with fibers – is injected into the tool. How the material flows into the mold determines where the fibers accumulate. The production process can even establish their orientation in certain directions. This is important because the strength of the material across the fibers is much greater than in the longitudinal direction of the reinforcement.
The material and its associated production technology were developed around the turn-of-the-millennium. There was no software that could have been used to simulate the process in advance. After countless series of tests, the DFT diaphragm began to be used in a pressure regulating unit in gas pipelines in 2003. Its use in gas meters followed a short time later; Metflex in particular was able to conquer the U.S. market with it, said Chris Greenwood, Manager, Sales and Marketing. The timing was good because the country had just reached the peak of a natural gas boom. Unleashed by domestic production, this environmentally-friendly energy source – whose CO2 emissions during combustion are 50 percent less than those of coal – gained substantial market share.
Metflex has been part of Freudenberg Sealing Technologies since mid-2017. Its former private investors sold the company. Dr. Dieter Thiel, Director of the Global Lead Center Diaphragms at Freudenberg Sealing Technologies, believes his British colleagues represent a great opportunity. “Metflex has technological expertise and market know-how in the gas market that we have lacked until now.” With 90 employees, Metflex is a typical medium-size company: It has indeed invested in new technologies in the past, but now more opportunities will be emerging with the companies combined. For example, in China and India, where natural gas is gaining importance as a source of energy. “But at the moment, we are mainly busy bringing Metflex into the Freudenberg family,” Dr. Thiel said.
At many rock concerts, our products are on stage with the stars.
Phil Rycroft
Broad product diversity
Process control and the precise design of the production tools play a role in the use of the technology. They require experienced employees like Phil Rycroft , who is in charge of production at Blackburn. He proudly guided his visitors through the hall where about 40 million diaphragms have been manufactured with the DFT technology. But even though gas diaphragms are the company’s main business, a broad range of other products is emerging here. It includes tiny components as well as diaphragms with a diameter of up to two meters.
Manual work: The challenge in the injection molding of elastomers lies in producing the component burr-free.
The array of applications is correspondingly broad. High-end speakers for concerts are one example. “At many rock concerts, our products are on stage with the stars,” Rycroft said proudly. The portfolio also includes connection elements for underwater pipelines, special seals used in aviation and dampers for energy facilities on land and the high seas – that is, products whose defect-free operation is crucial. So Rycroft does all he can to guarantee zero-defect production. This means monitoring all the individual process steps. The material is either mixed by the company on site or subjected to an incoming inspection in the lab. The process know-how not only involves vulcanization in presses – which run from 50 to 500 tons – but also the surface pretreatment of metallic materials for composite components. Metflex has also developed a process in which a fabric is furnished with an elastomer layer on both sides and then trimmed. The equipment is much like one of today’s printing presses – it’s fully automated. The Metflex engineers have developed unusual approaches again and again. For example, it is a special challenge to manufacture a burr-free component during the injection molding of elastomers. The de-burring is difficult, especially on very small components. Here Metflex has developed a special process that leaves the parts relatively free of burrs. Clever ideas of this kind have allowed a relatively small company to make its way successfully in the global market.
For several years, Metflex has had some of its products manufactured by a contract manufacturer in Malaysia. “That creates a high level of security for our customers who often order 100 percent of a product from us,” Purchasing Manager David Hudson said. “This also gives us access to growth markets in Southeast Asia.” The principle of continual quality control applies here as well. It is not only material procurement that is monitored from Blackburn – the components produced abroad regularly undergo exhaustive tests in the company’s labs.
Blackburn is proud of the “Metflex” brand and its success in the oil and gas market. Ralf Schmid, Manager of the Special Sealing Division, is confident about Metflex’s and FST’s prospects. “The company is a good fit for us based on its product portfolio, technologies, development and marketing expertise, and its strong value orientation.” That’s not surprising at all, given the history of Metflex. When it was founded in 1919, the company was called the “Metropolitan Leather Company.” The main products were flat and ring seals made of leather. But Freudenberg’s management does not intend to focus on the past but rather on the companies’ common future. “We are well on our way as far as integration goes,” Schmid said.
Read more about Freudenberg Sealing Technologies special sealing products here.
More Stories About Renewable Energy
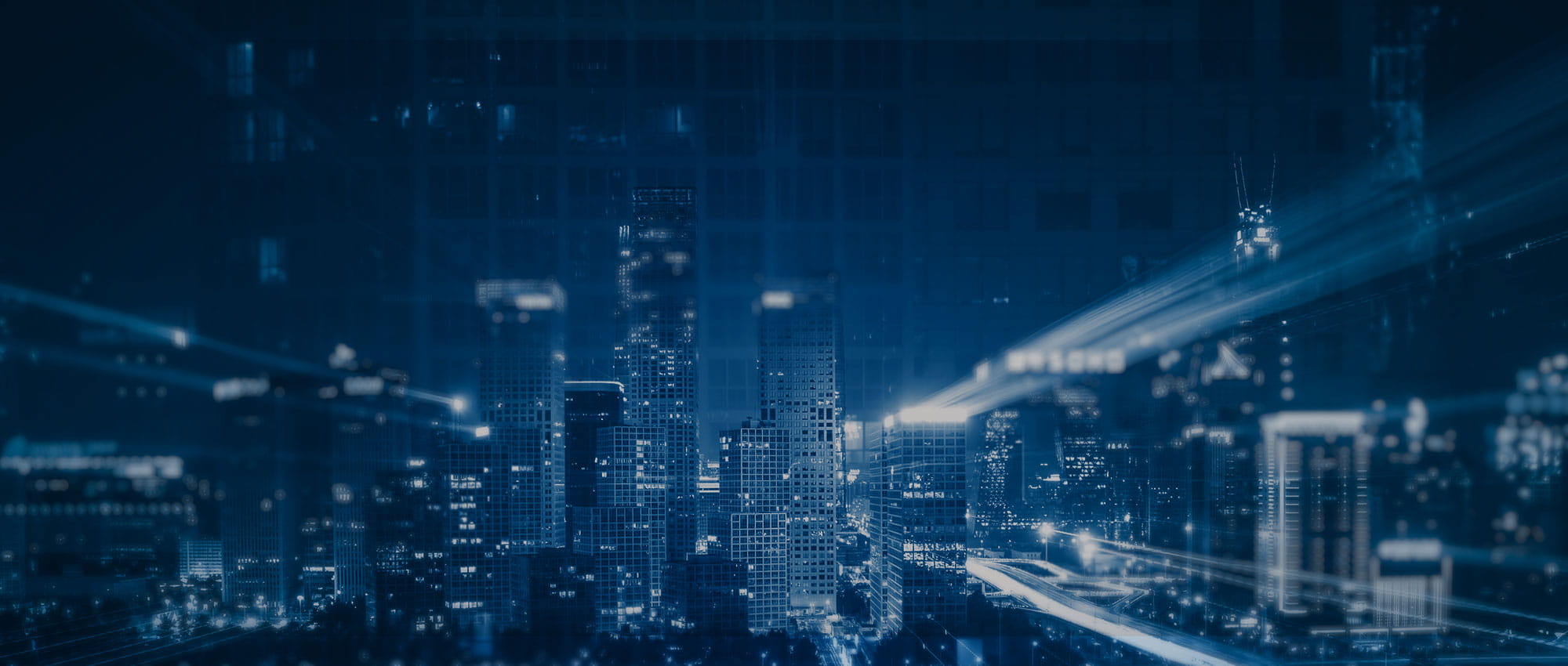
Join Us!
Experience Freudenberg Sealing Technologies, its products and service offerings in text and videos, network with colleagues and stakeholders, and make valuable business contacts.
Connect on LinkedIn! open_in_new