Obtain news and background information about sealing technology, get in touch with innovative products – subscribe to the free e-mail newsletter.

“The Material Is the Foundation for the Best Possible Seals”
The hydrogen economy without seals? Inconceivable. Freudenberg Sealing Technologies offers seals of the highest quality for the entire value chain. Their foundation: specially developed materials.
Materials for the hydrogen economy must meet extremely stringent requirements. To start with, hydrogen is the smallest chemical element on the periodic table. The diameter of a hydrogen molecule is just 0.07 nanometers, or less than a billionth of a meter. That means hydrogen gas can penetrate the tiniest openings. “The permeation definitely has to be minimized, more to make systems safe and less due to losses in efficiency. If the hydrogen reaches the ambient air, the mixture with oxygen could quickly explode,” said Dr. Alexander Hähnel, a chemist. He is a member of the Technology & Innovation team working on hydrogen applications at Freudenberg Sealing Technologies.
Facility operators are also insisting on tremendously long operating lives for seals. For example, an electrolysis system is expected to run nonstop for at least 10 years. That’s why their seals are designed for a lifespan of 100,000 hours. If a sealing material has to maintain its full function over the entire lifespan, it cannot be allowed to age prematurely. It is not the hydrogen that attacks the rubber material. It is rather the side effects of the particular application. They result from high temperature and pressure differences interacting with large temperature fluctuations.
For example, when hydrogen tanks are filled up, explosive decompression can result in the event of very fast changes in pressure. Gas bubbles explode in the sealing material as they do in the blood of a diver ascending too quickly from deep water. Fine cracks are the result, along with an irreversibly damaged material structure. Other chemical effects cause the seal’s rubber compound to age. One example is oxidation from the oxygen in an electrolysis system. At a system pressure of 35 bar, the oxygen content is 175 times greater than the level in ambient air. The impact: Extremely aggressive oxidation acts on the sealing material and greatly accelerates the aging process. High temperatures intensify the effect.
A Material’s Selection Is Based on Pressure, Temperature and Duration of Operation
“The material is the key to the seals’ optimal performance and the perfect operation of any system,” said Jürgen Emig, plastics technology engineer on the Technology & Innovation team. “We develop components specifically for a particular application. Our strength: The company recommends the optimal design to the customer based on the best-possible materials in close coordination with the requirements profile. The seals deliver the desired performance over the entire required lifespan.” Experts from various disciplines pull together – true to the company’s guiding concept of “Innovating Together.” The seals can also be combined with various other components to form a single part. Some examples are bipolar plates, thermoplastic films and gas diffusion layers.
The material is the key to the seals’ optimal performance and the perfect operation of any system.
Jürgen Emig, Director Pre-Product Development Hydrogen Applications, at Freudenberg Sealing Technologies
The product portfolio for the hydrogen economy is wide-ranging. Two examples: Especially for low-temperature, proton exchange membrane (PEM) fuel cells, Freudenberg Sealing Technologies has developed the 35 FCPO 100 as a material for seal cells. “It is a very clean elastomer based on polyolefin,” said Dr. Hähnel. “It contains no harmful substances that could damage the catalysts of a fuel cell or otherwise reduce its efficiency.” The portfolio also contains LSR (liquid silicone rubber) materials. The company also has a made-to-order sealing material for high-temperature fuel cells running as high as 200°C (392°F). The material 60 FC-FKM 200 – FKMs are fluorocarbon rubbers – established itself in the market early on. Due to a change in the raw material, 70 FKM 256261 recently advanced to the industrial stage, becoming its successor. Like 60 FC-FKM 200, it releases no substances that would impair a fuel cell’s operation. Another advantage: The material is just as suited to PEM electrolysis. “The first series production for cell seals using 70 FKM 256261 was launched recently,” Emig said. At present, EPDM (ethylene properly diene rubber) is the standard for alkaline electrolysis, “We are currently working on a material class with an even longer lifespan.”
Investment in Sophisticated Test Facilities
Freudenberg Sealing Technologies’ expertise relies on more than just materials, design and production processes. Wide-ranging lab research and component testing are essential components of its development process. Does a newly developed material meet the objectives set for it? Older testing technologies are reaching their limits in light of the more demanding requirements. “We want to know in greater detail what happens under operating conditions so we can do our development work even closer to real-life applications,” Dr. Hähnel said. “Depending on the result, we are adjusting recipes and processes, pushing the limits of what is feasible.” All the tests make material qualities comprehensible to customers and allow operating life estimates for entire systems.
Freudenberg Sealing Technologies is now investing in other test equipment that will play to its strengths, especially in hydrogen applications. Some examples are new test stands to measure impermeability with higher precision and a greater range of pressures. Experts can gauge the impact of higher oxygen concentrations on aging with targeted tests. Electrochemical test stands are also expanding horizons: “Properties are affected by the electrical current running in the technical processes of fuel cells and electrolyzers. Now we can apply electric current to materials on a targeted basis and examine the effects,” Emig said. A number of research projects are also underway to explore material effects even more fully.
“This is the highest level of material development. The work is paying off. Our customers are purchasing considerable knowhow with every seal,” Dr. Hähnel said. “In exchange, they are mainly getting higher process reliability for their facility.
This article originally appeared in ESSENTIAL, Freudenberg Sealing Technologies’ corporate magazine that covers trends, industries and new ideas. To read more stories like this, click here.
The Future Is Hydrogen
From H₂ Production to Usage: Comprehensive Insights on Production, Distribution, Storage, and Future Applications with Solutions. Explore full spectrum in our webspecial!
Hydrogen Webspecial open_in_newMore Stories About Renewable Energy
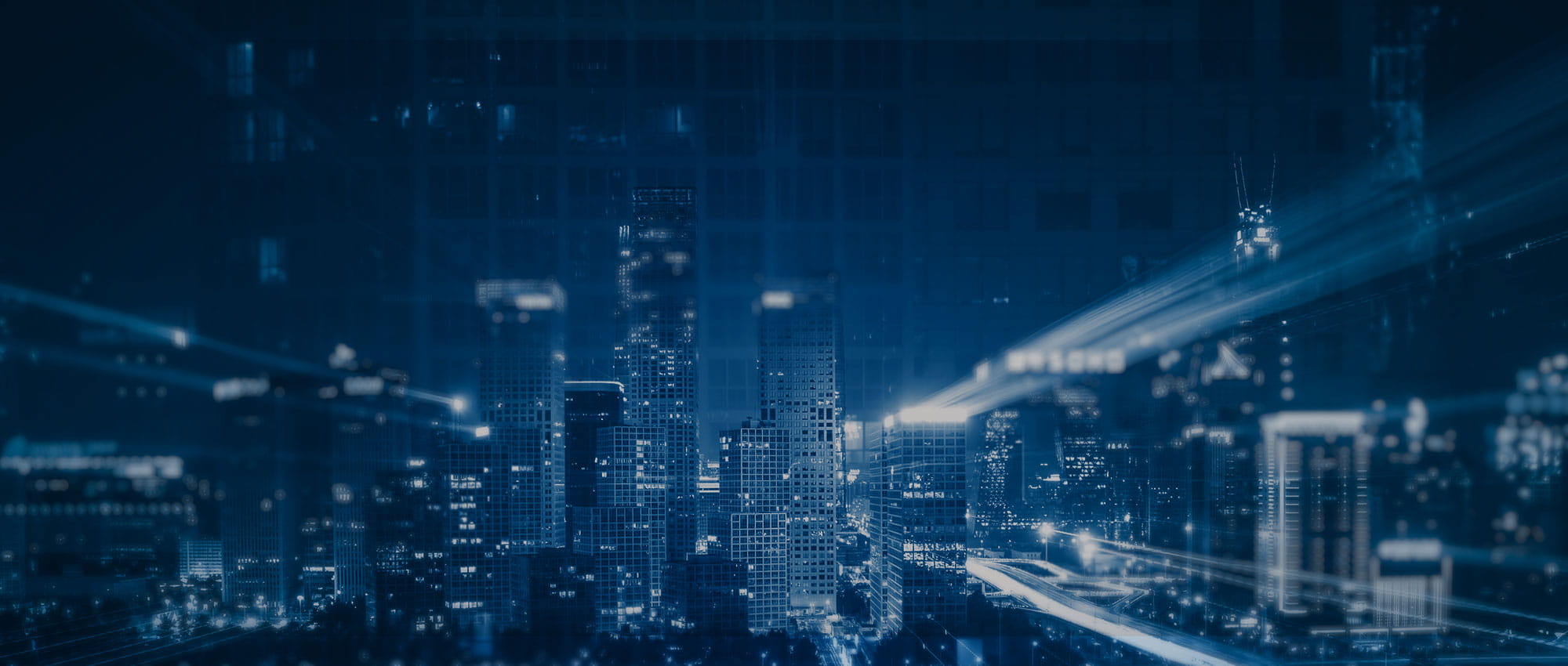
Join Us!
Experience Freudenberg Sealing Technologies, its products and service offerings in text and videos, network with colleagues and stakeholders, and make valuable business contacts.
Connect on LinkedIn! open_in_new