Obtain news and background information about sealing technology, get in touch with innovative products – subscribe to the free e-mail newsletter.
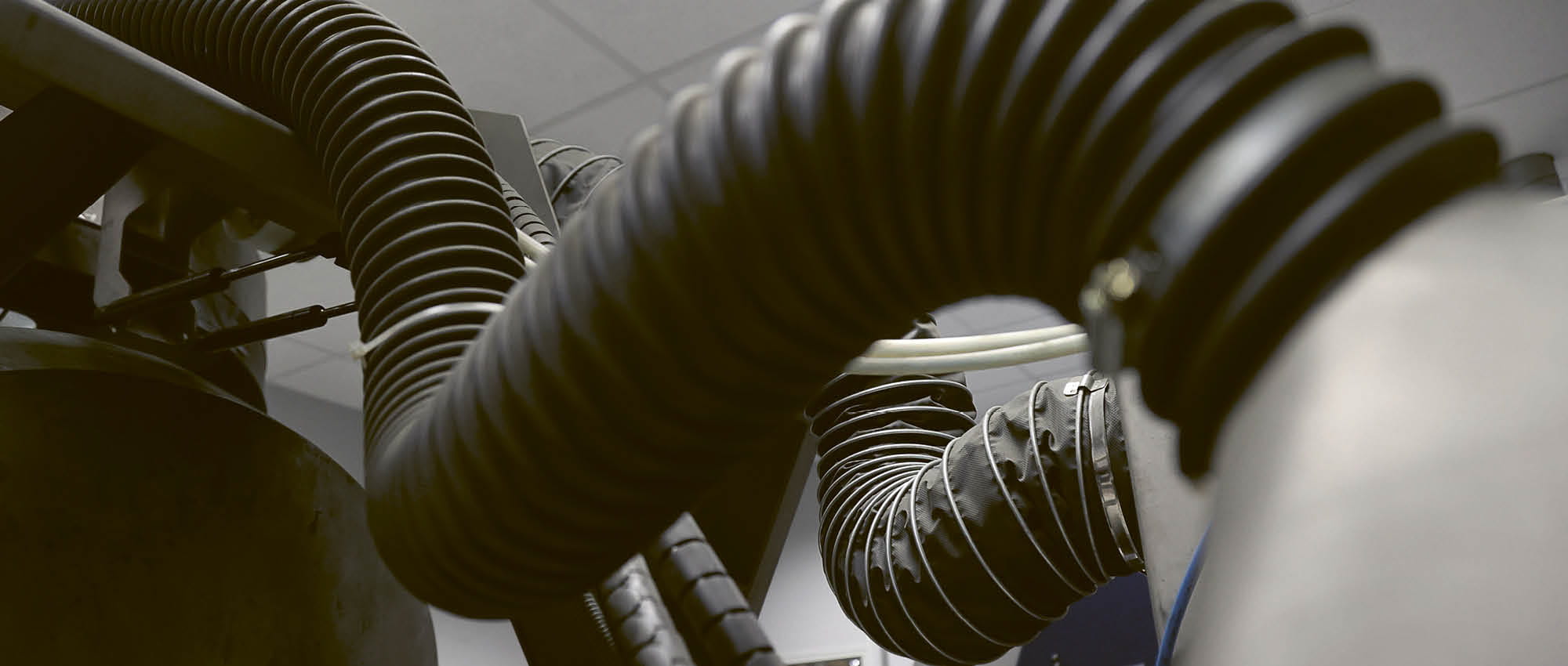
03.05.2022 | Story
A Billion Microorganisms
They cannot be seen with the naked eye. Yet they do important work at Freudenberg Sealing Technologies in Germany. The bacteria that are part of Reichelsheim’s bio exhaust air system protect the environment from solvent vapors.
A billion bacteria are bustling around. They work day and night, filtering the exhaust air from the production area. These creatures, microscopically small, cannot be seen with the naked eye. Even their home cannot be viewed from the outside. The microorganisms live in containers filled with layers of cattle mulch. This bio exhaust air treatment system at the Freudenberg Sealing Technologies site in Reichelsheim is located right behind the factory hall.
Interest in bio exhaust systems is growing quickly in response to global pursuit of sustainability.
Prof. Franjo Sabo
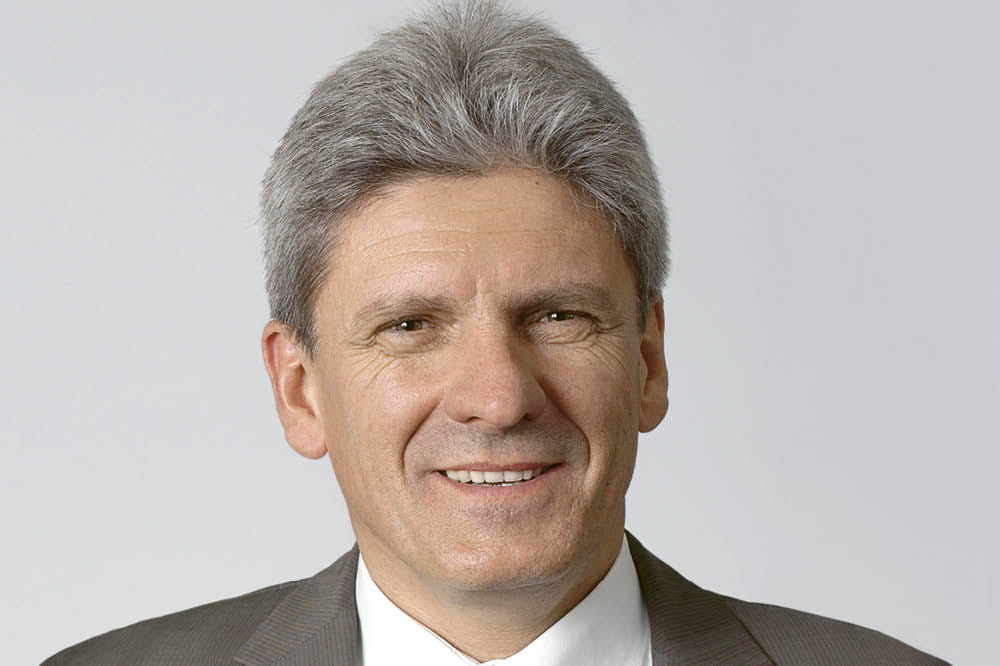
Bacteria Produce Clean Exhaust Air
The biological system has been filtering exhaust air at Reichelsheim for 10 years. Without it, there would not merely be unpleasant odors permeating the environment – another advantage is that it uses significantly less energy than other options. “For us, this made a lot of sense. We use large quantities of organic solvents that are nonetheless readily water soluble,” said Annette Reisner-Schaab, who has been in charge of environmental issues and job safety for 15 years. “These solvents have to be broken down.” Among other products, the Reichelsheim facility makes seals consisting of a metal or plastic carrier part and an elastomer. To make sure the elastomer adheres to it, the carrier part has to be cleaned, coated and dried. The process produces solvent vapors that can only be released into the environment in strictly regulated amounts. “Production has risen sharply. So has our use of solvents, unfortunately,” Reisner-Schaab said. In 2011, the environmental engineer and her team studied different ways to solve the problem. Could the amount of solvents be reduced or could the processes possibly be outsourced? What technology could be used to eliminate the emissions? “In terms of operating costs, it was quickly clear to us that the biological option would be the best,” she said. “For anything else, we would have needed more energy.” For example, if the exhaust air were burned with the help of natural gas, more CO2 emissions would have been produced and higher costs would have resulted.
A Godsend for Hungry Microbes: Solvents
This biological solution gets by with less energy. Once it is connected, the system does its job almost independently. The streams of exhaust air first run together through an active carbon filter before a scrubber moistens them. The moist air is then distributed over the cattle mulch mixture in the large containers. The air literally serves up the microorganisms’ next meal. “The bacteria like our exhaust air,” Reisner-Schaab said. They separate the carbon compounds into water and carbon dioxide and use the energy to expand their population. The filtered exhaust air ultimately goes up a chimney and reaches the outdoors. The process mimics what would occur in nature – except that the unit makes it more concentrated and controlled.
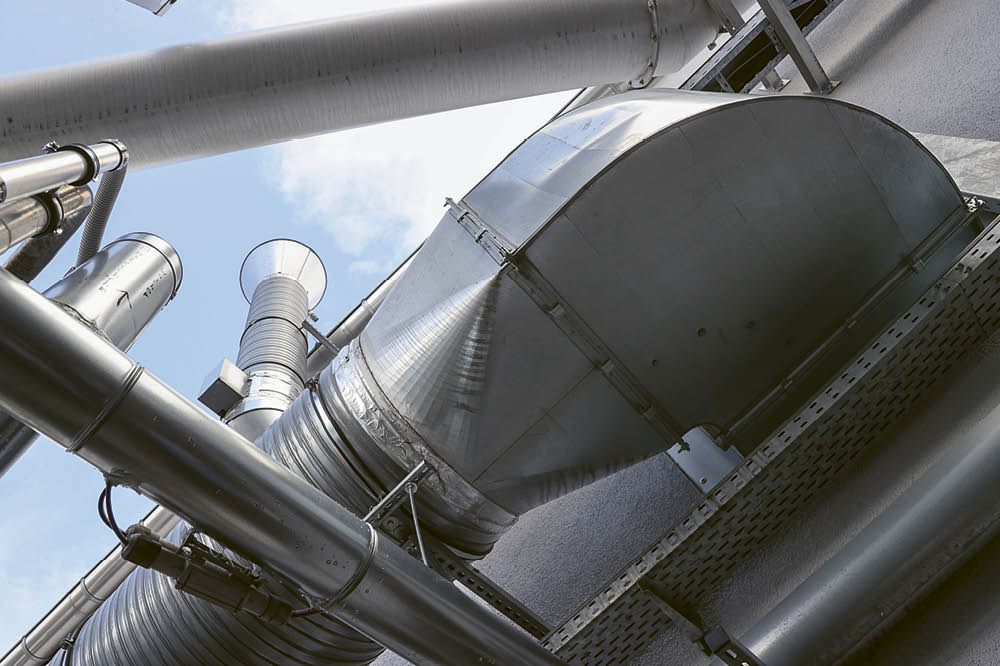
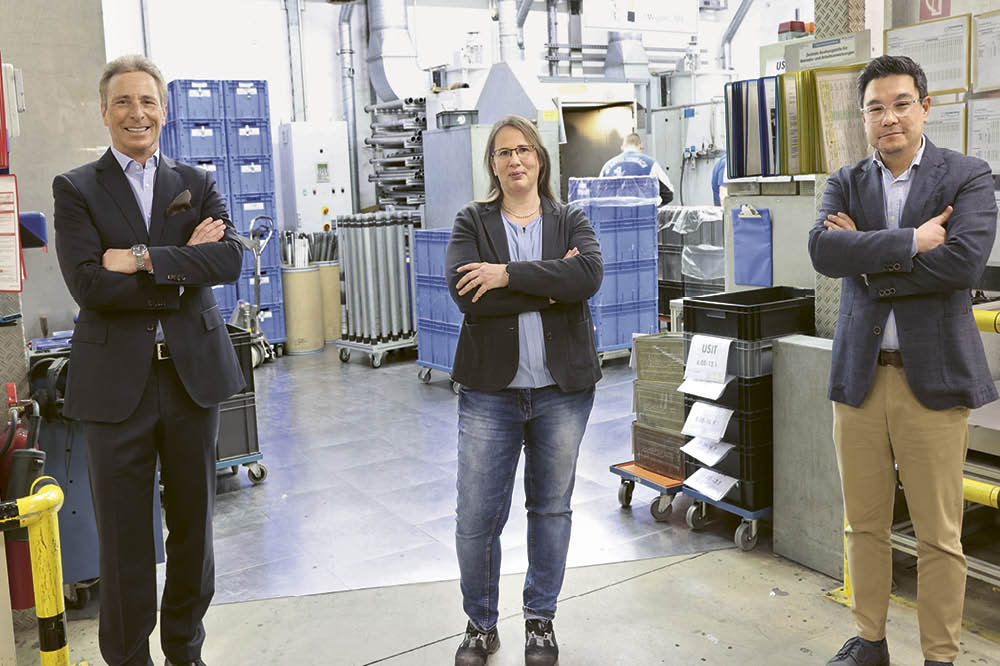
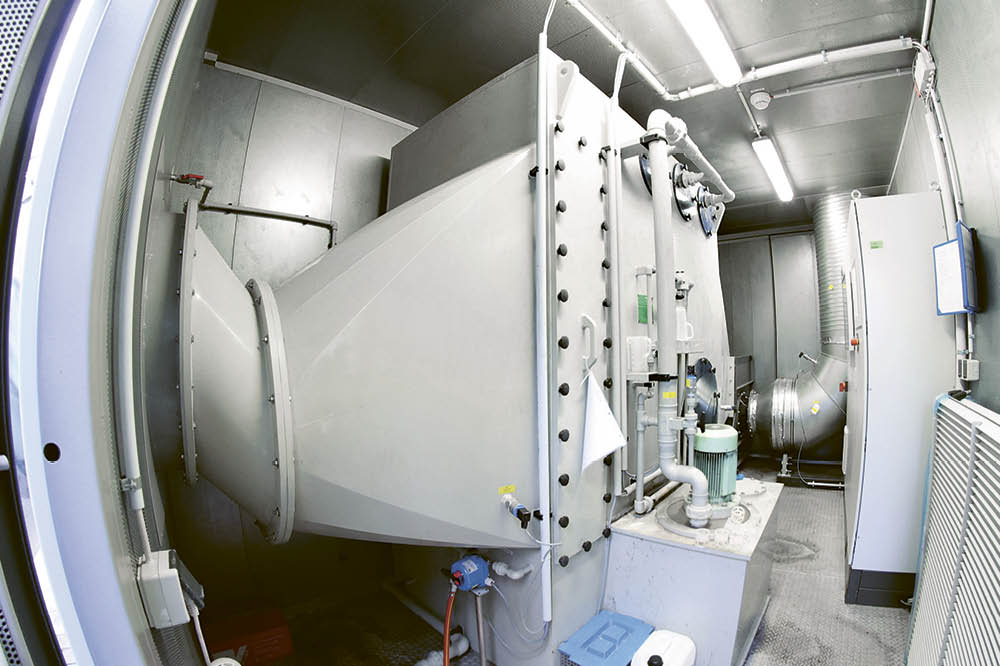
But this bio-solution requires space. While an incinerator can burn different quantities of exhaust air, the ratio between the bacteria and the solvent must be carefully calibrated. More solvent also means more bacteria and that, in turn, means more containers. The benefit: This gives the plant flexibility: “We can respond quickly and effectively when the capacity changes,” said Reisner-Schaab. “For example, if we were to have less solvent or more watery processes, we could cut out one of the containers and return it to the manufacturer.”
High Tech to Handle Exhaust Air
A company called “Reinluft” is the system’s manufacturer. Prof. Franjo Sabo, the company’s Managing Director, has been supplying bio exhaust air systems to customers like Freudenberg Sealing Technologies for nearly 40 years. “The unit in Reichelsheim is quite well developed,” he said. Future generations of the system will be more heavily automated and more easily monitored, he said. Especially when it comes to ways to keep the moisture level constant, Sabo explained that “it is hard to believe how difficult it is, even in the 21st century, to keep compost moist. It is one of the biggest challenges.” That’s because the biological mass is a living, nonlinear system and is more difficult to control as a result. “During manual maintenance, the technician takes a sample of the material and looks to see whether everything is in order. Now you have to imagine how a computer could manage that.” Sabo and his team have developed an automated control system that responds to all the metrics within the unit and provides feedback via a traffic light-type signal.
Is Compost Being Replaced?
Reinluft is focusing on another idea as well: alternative carrier materials for the bacteria. “The compost and the bacteria are an absolutely well-established technology,” Sabo said. “But as an engineer, you ask yourself whether you might be able to get away from the compost and move to a standardized material.” A carrier material like plastic could take up less space than the biomass, which has to be changed every four years. Here Sabo sees opportunities for markets outside of Europe. “Interest in bio exhaust systems is growing quickly in response to global pursuit of sustainability,” he said. “The technology is enormously popular in China. The problem is that there is almost no compost material there.” Shipping large quantities of compost would be complicated and expensive. As long as alternative carrier materials have not become fully mature, the world will continue to turn to this well-established combination.
The bacteria like our exhaust air.
Annette Reisner-Schaab
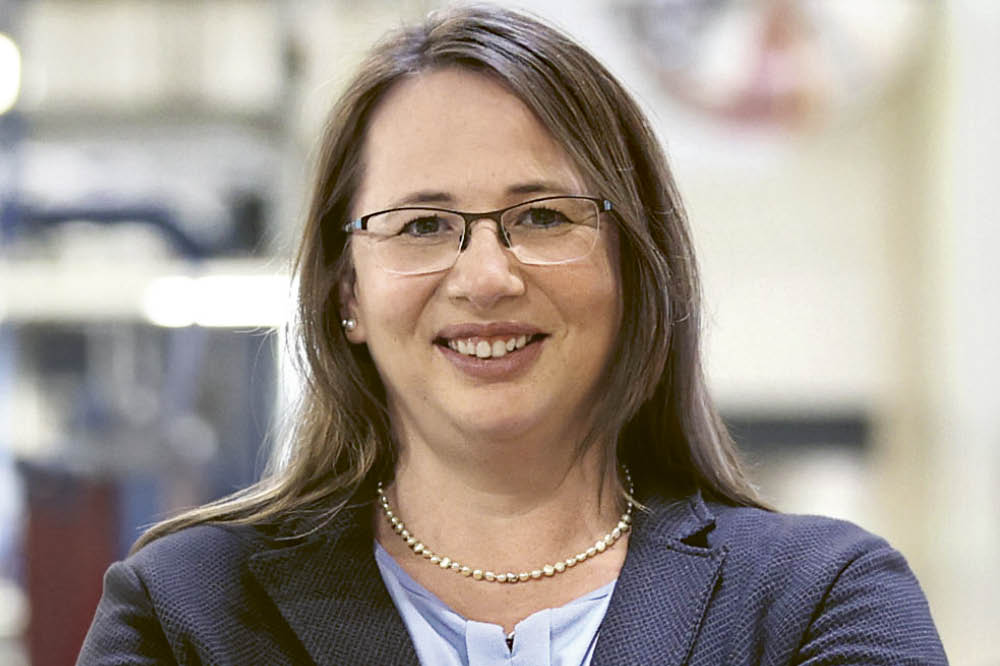
Biological Systems are Booming
Reichelsheim’s system has become am internal benchmark within Freudenberg. “As sustainability has taken on increasing importance, we have been fielding more inquiries from our colleagues in Germany and abroad,” Reisner-Schaab said. She has already introduced the plant’s system to various visitors. She has also noticed a growing consciousness of the climate and environmental protection. “The approach to sustainability has become broader. It increasingly involves what is happening in the value creation chain before and after production. The question of the CO2 footprint for each individual product will soon be asked.”
More news on the subject Sustainability
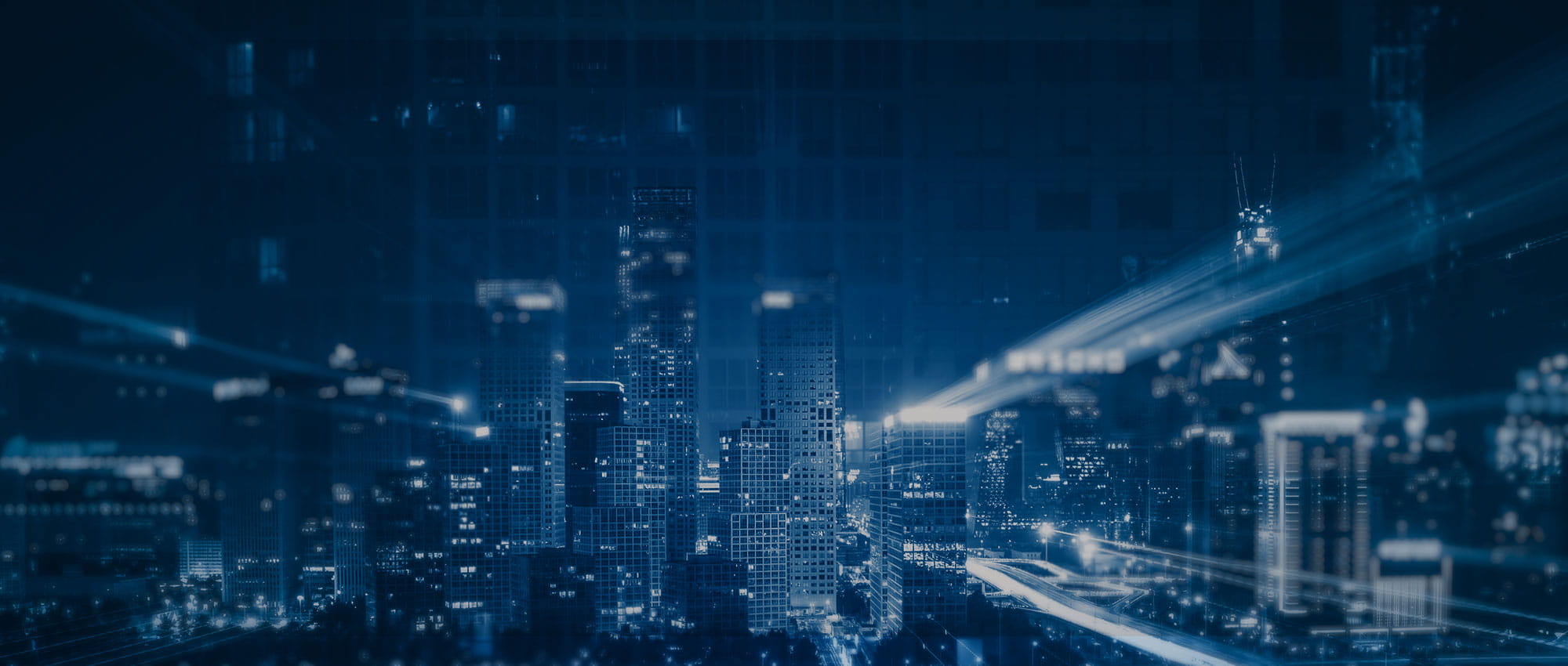
Join Us!
Experience Freudenberg Sealing Technologies, its products and service offerings in text and videos, network with colleagues and stakeholders, and make valuable business contacts.
Connect on LinkedIn! open_in_new