Obtain news and background information about sealing technology, get in touch with innovative products – subscribe to the free e-mail newsletter.
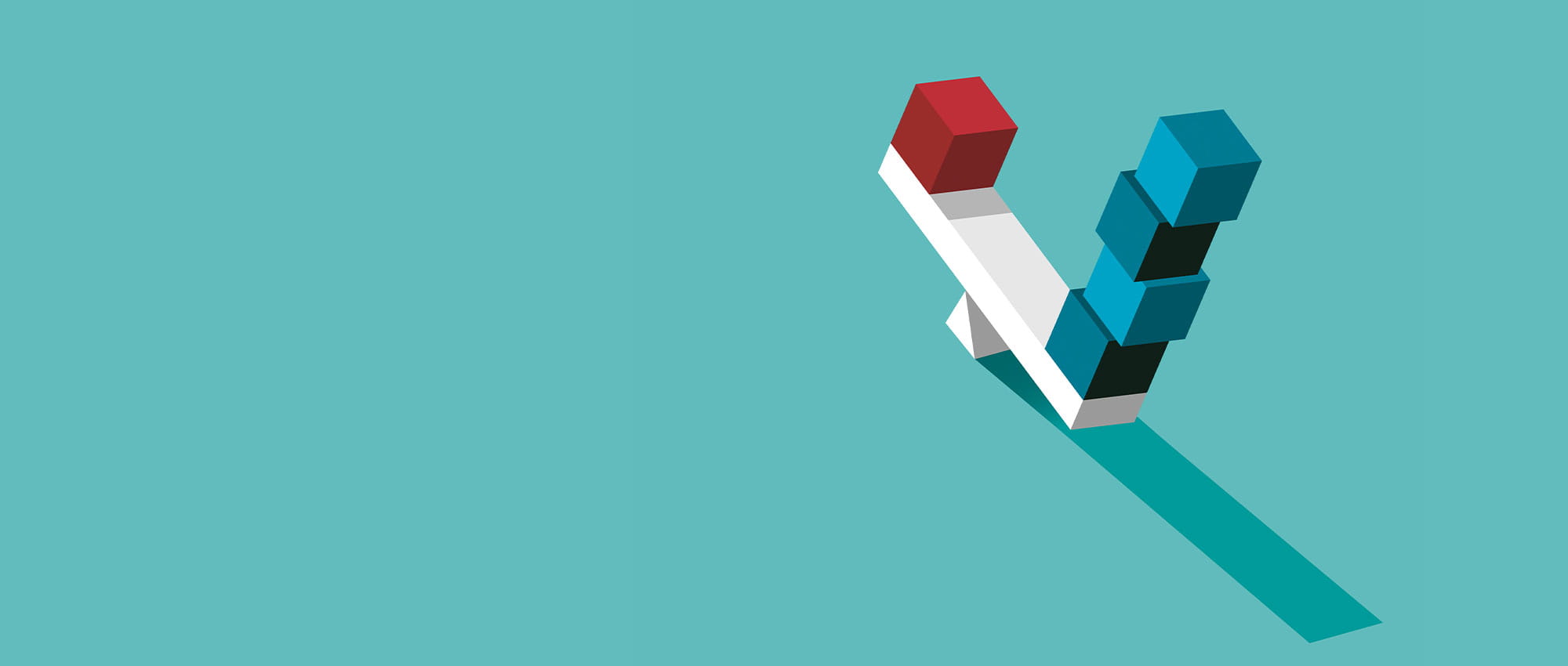
11.02.2020 | Story
All-Around Player
Components made of plastic are not just lightweight – they can also handle multiple functions simultaneously. This is possible due to materials that are adapted precisely to the requirements and the high degree of flexibility available in plastic-parts production.
Plastic is useful for more than just plastic bags. Formed into a multi-faceted component, it can handle multiple functions simultaneously. Experts call this “functional integration.” It is the so-called injection molding process, a way of producing plastic parts, that makes this possible. It enables just about any shape to be manufactured. Consider thermoplastics as an example: In the primary shaping process, the thermoplastic material in granular form is first melted in the injection molding machine at 200 to 300 °C (392 to 572°F) and conveyed to an injection nozzle with the help of a screw conveyor. Then, under high pressure, the molten material is introduced into the mold whose hollow space delineates the form of the plastic part. When the molten material is cooled in the mold, the plastic becomes dimensionally stable and is ejected from the mold as a finished plastic part.
Integration of Functions
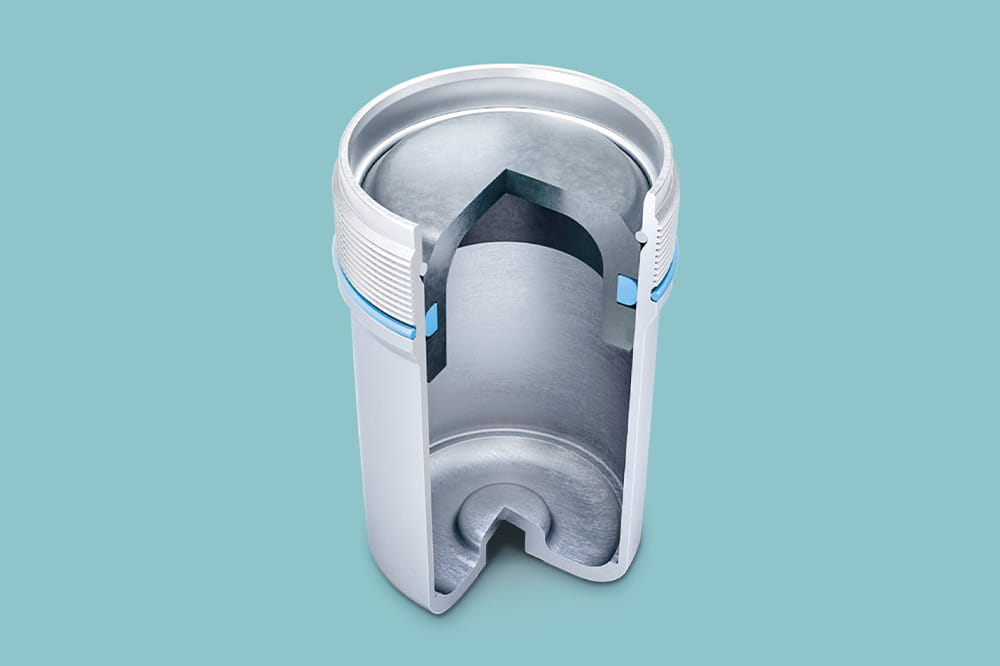
“Depending on how the mold is designed, the injection molding process can produce very complex geometries and varying wall thicknesses from a single primary material,” explained Matthias Hauer, an expert in plastics processing at Freudenberg Sealing Technologies. “The plastic parts are literally all of a piece – for example, a reinforcement ring that would have to be welded on in an additional step can be integrated directly into the component using injection molding.” With the right combination of material properties and geometries, a plastic part can then take over various functions. Reinforced areas, for example, can absorb mechanical stresses from dynamic parts such as rotating shafts. Sealing requirements can be met with other features.
The integration of functions offers many advantages: For one thing, fewer parts are needed, which can reduce weight and costs. For another, the production and assembly of systems are simplified and the related processes become less complex and prone to failure.
It All Comes Down to the Mixture
This is all related to the fact that Freudenberg Sealing Technologies material developers adapt the characteristics of the material exactly to a part’s function and range of use. This involves changing the properties of the basic material – a thermoplastic, for example – with the help of fillers and additives, among other measures. For instance, if a component in a particular location is exposed to especially strong friction, the developers add agents that improve abrasion resistance. This turns a component into an all-around player like a Swiss Army knife.
Plastics are our current focus. On single-use plastic as a burden on society – and how we can deal with the problem. And on the question of whether plastic can be a solution.
You can find more on the topic “Plastic – Breakthrough and Burden” in the latest edition of our magazine ESSENTIAL.
More news on the subject Sustainability
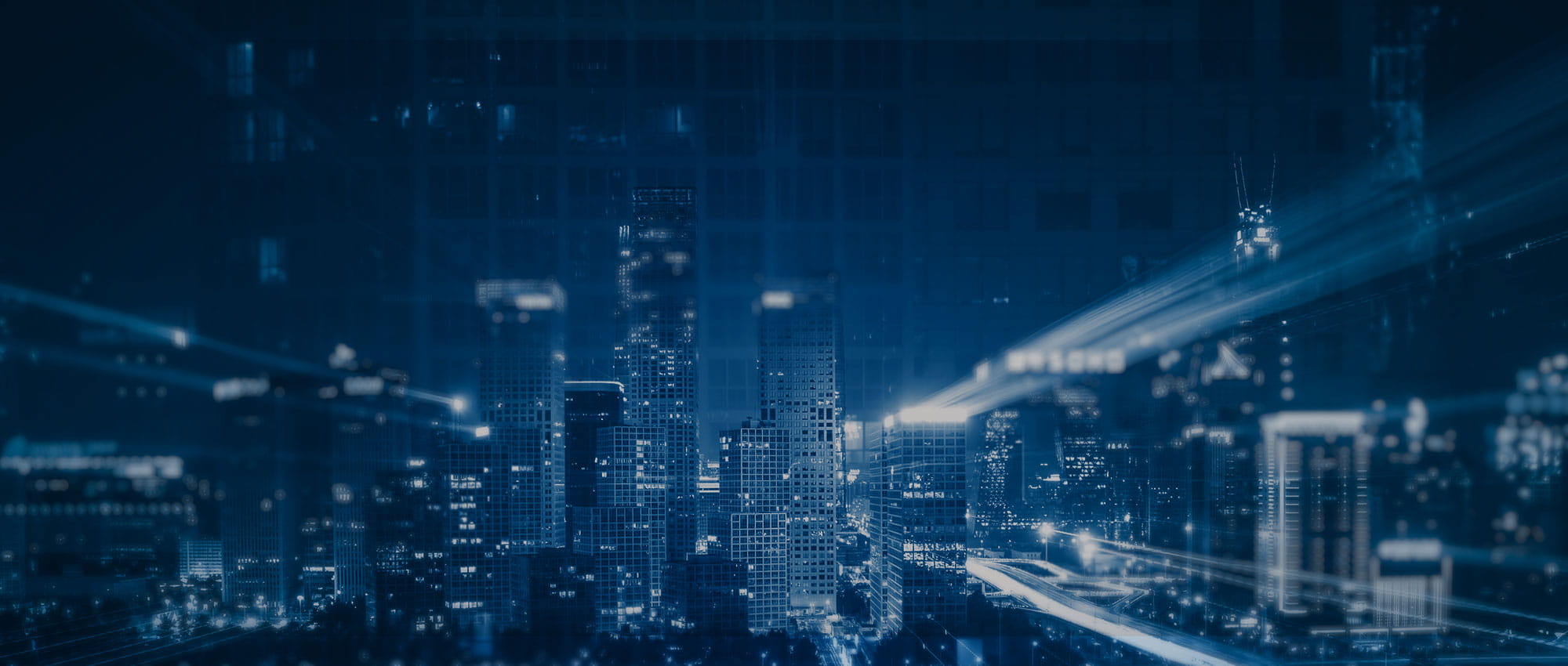
Join Us!
Experience Freudenberg Sealing Technologies, its products and service offerings in text and videos, network with colleagues and stakeholders, and make valuable business contacts.
Connect on LinkedIn! open_in_new