Obtain news and background information about sealing technology, get in touch with innovative products – subscribe to the free e-mail newsletter.

The Beginning of the End for the World’s Plastic Woes?
A U.S. research team has recently succeeded in developing a novel plastic. It not only can be recycled back into its raw materials. They in turn can be used to produce high-quality plastic.
Brett Helms holds a small piece of dyed plastic in his hands. Not withstanding its nondescript appearance, it is of enormous importance to him. And quite possibly to others in the near future. “This plastic has the potential to change the world,” says Helms, 41, who leads a research group at the Molecular Foundry at the Lawrence Berkeley National Laboratory near San Francisco. The polymer in his hands is the first compounded plastic that can be totally recycled back into its separate component parts.
This plastic has the potential to change the world.
Brett Helms, Leiter einer Forschungsgruppe am Lawrence Berkeley National Laboratory (USA)
Accidental discovery: During cleaning with a strong acid, the polymer broke down into its individual components.
Recycling Pitfalls
Plastics are being produced in ever-greater amounts worldwide, and recycling them is no small task. The major problem with classic plastics involves their fillers. They make a material softer and more elastic while imparting a color and increasing its resistance to ultraviolet radiation. The fillers are so closely linked to the plastic’s monomers that they stay in the material after shredding and processing. If they are melted into a new material, dark pellets with variable characteristics are often the result – at best, they can be used to make cheaper building materials. Nevertheless, a large share of plastics isn’t recycled at all. They go directly into the environment, where they break down slowly and may even end up in drinking water in the form of micro plastics.
More and more chemists are tackling the problems posed by the ever-increasing use of plastic. Some are seeking new approaches to the recycling of existing plastics. One is Gregg Beckham, who is doing research in Yellowstone National Park, looking for new enzymes that break down PET plastic. Others are trying to develop completely new plastics whose structures lend themselves to recycling. Ludwik Leibler, lab chief at CRNS, a French national research institute, is chalking up the first successes: In 2011, he invented Vitrimere, a glass-like material. In 2014, Jeanette Garcia of IBM made headlines with her “Fantastic Plastic” – a new class of polymers that can be recycled.
Researchers in the mountains looming over San Francisco Bay are moving in this direction as well. At the Berkeley Lab, Brett Helms and his partners are working on recyclable thermosetting polymers, which harden when heated and whose monomers enter into stable network connections. This extremely robust material is used in packaging, tubing and screens as well as car manufacturing and airplanes. But after its processing, it can no longer be melted down. It basically ends up in landfills.



The Aha Effect
That’s not the case for polydiketoenamine (PDK): “We owe our breakthrough to an accident during cleaning,” Helms said. “This newly developed material adhered so securely to our glass dishes that we had to use a strong acid to remove it.” The acid not only detached the PDK from the glass – it even broke down the polymer. “If we had just thrown the lab dishes away, we would have never observed this spontaneous chemical reaction,” Helms notes. Suddenly curious about the phenomenon, the researchers examined the material in a test tube and discovered that the individual components were present in their initial form.
By treating the PDK with the strong acid, they found that it was also possible to filter out all its additives such as dyes and softeners. The original monomers are like new and available for use. They were also able to retrieve the additives, unchanged chemically. Some of these additives, such as flame retardants, are more costly than the plastic and therefore highly valuable on their own, which incentivizes their recovery for reuse. “PDKs make possible a circular lifecycle for plastics – the quality of the recycled material is just as good as the virgin material,” Helms said. Even a higher-level material is possible: the production of a material whose quality and features are better than that of the material from which it was recycled. For example, a flexible plastic could be made from a hard plastic. “This approach is innovative, straightforward and elegant,” explains the British polymer expert Rachel O’Reilly from the University of Birmingham. “There is still no single solution to the plastic problem, but this development is a very important step in that direction.”
The quality of the recycled material is just as good as the virgin material.
Brett Helms, Lawrence Berkeley National Laboratory, San Francisco (USA)
Opportunities for Use of the New Plastic
The plastic in Berkeley is produced by mixing chemicals known as triketones with amines. “This involves a click reaction at room temperature without the need for a catalyst, an additive or even a solvent – a couple of minutes in the ball mill is sufficient,” Helms said. He and his team are working on a range of different material characteristics. “PDK could easily be built into a gym shoe or fibers in textiles that would replace the nylon in pantyhose,
Another five to seven years: The patent is filed, but there are still details to work out before the innovation is ready for the market.
But you could also imagine the kind of hard plastic used to make bottles for cleaning fluids,” he said. However, since the powdery synthetic resin in the initial material is already beige, white or transparent hues are not yet feasible. PDK currently can only be dyed darker colors.
The Berkeley Lab has patented PDK and is now looking for major partners in the hopes of jointly developing material for industrial use. “Many details in the lifecycle of the material still have to be worked out,” Helms said. “For example, the acid-based recycling process is very water-intensive.” To clear the way for PDK in the market, a completely new ecosystem is needed, including recycling facilities geared to the new material. “It will likely be five to seven years before we can talk about commercialization,” Helms concludes.
The Berkeley Lab
The Berkeley Lab is one of 17 research institutes of the U.S. Department of Energy. Since its founding in 1931, thirteen Nobel prizes have been awarded to scientists doing research there. Today 4,200 researchers work at the site, which is just outside San Francisco.
More Stories About Sustainability
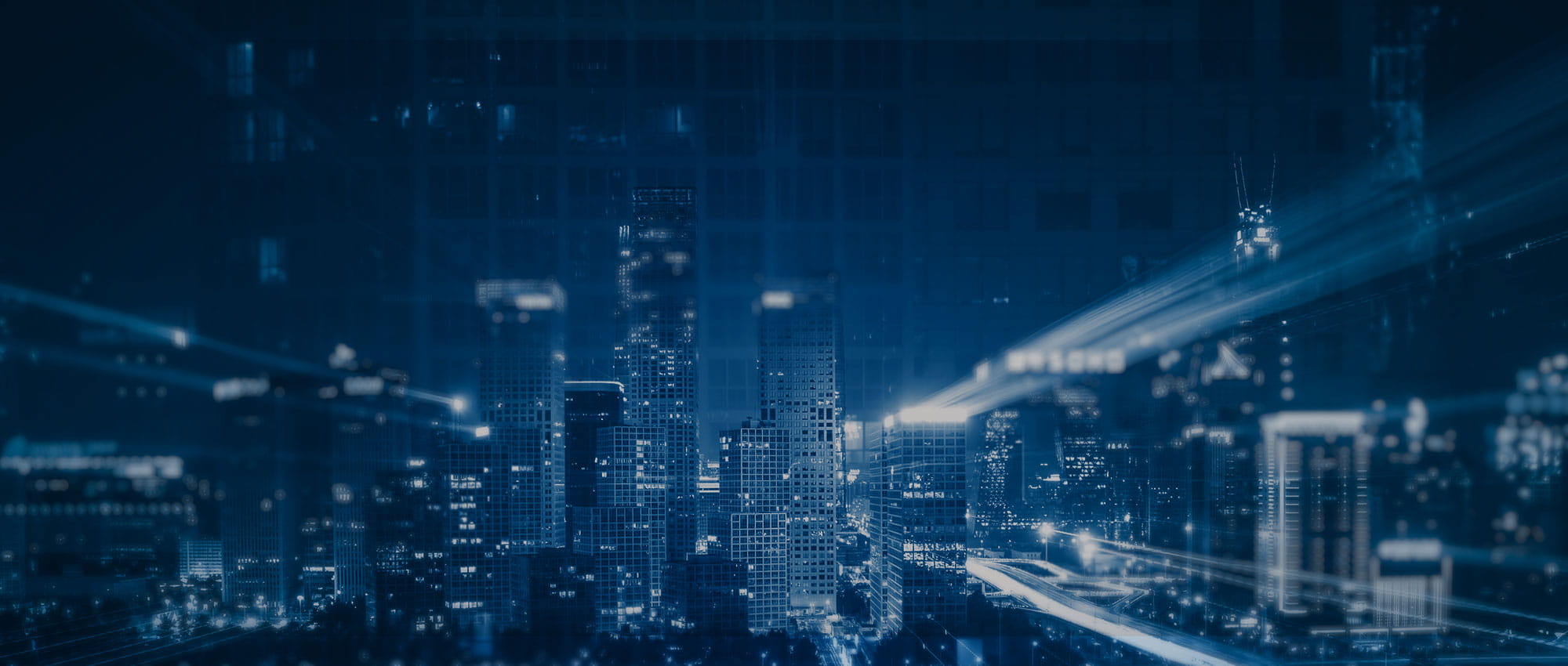
Join Us!
Experience Freudenberg Sealing Technologies, its products and service offerings in text and videos, network with colleagues and stakeholders, and make valuable business contacts.
Connect on LinkedIn! open_in_new