Obtain news and background information about sealing technology, get in touch with innovative products – subscribe to the free e-mail newsletter.
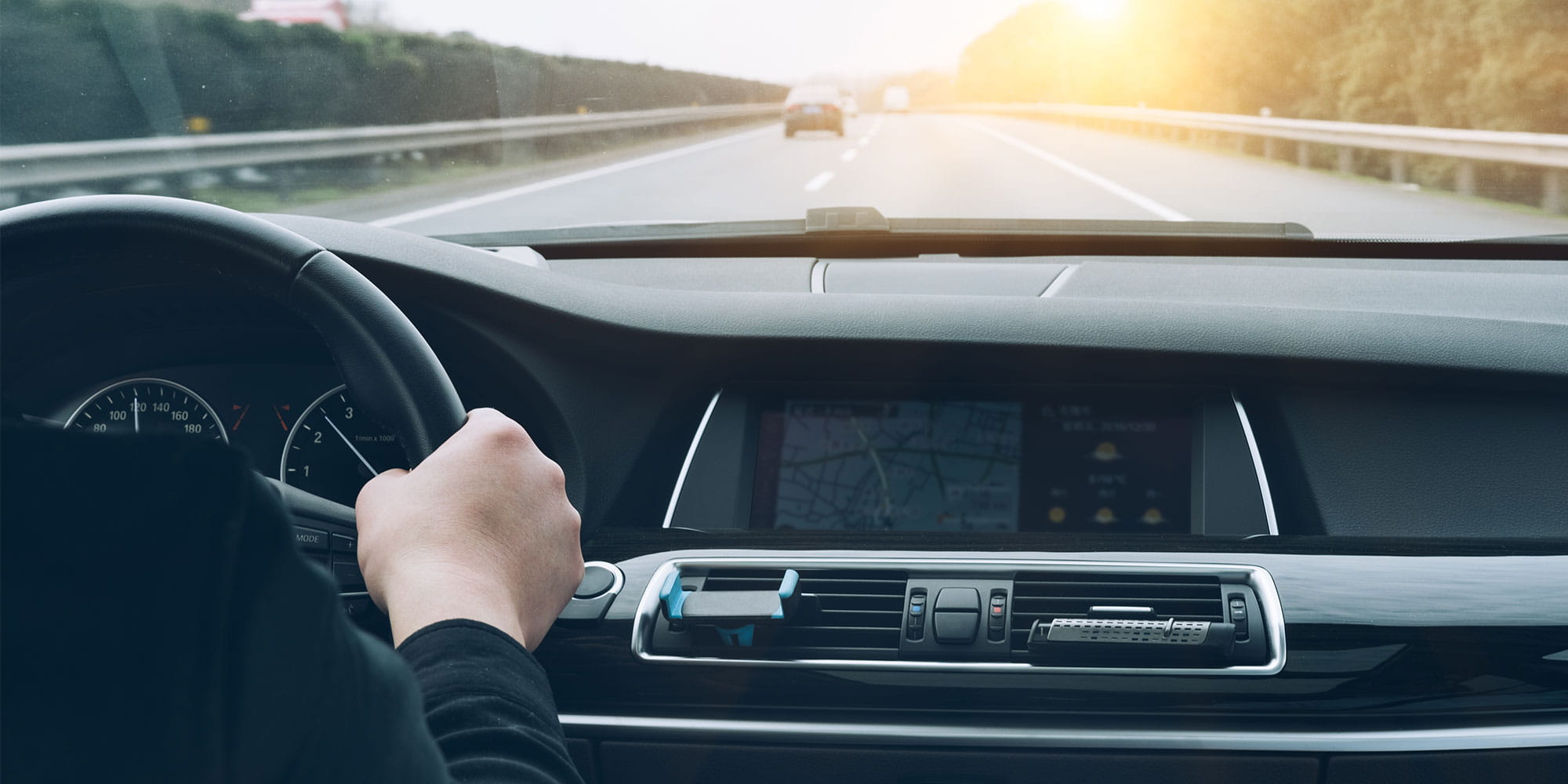
10.09.2019 | Story
High-tech Polymers for Lighter Cars
As the latest car models glitter in the footlights at IAA in Frankfurt, an important material is playing merely a supporting role. But without plastics, the automobiles would put on lots of weight and emit more CO₂.
If a person weighing 440 or even 660 pounds drops down to just 220 pounds, he would certainly earn the recognition of people at work and in his community. But it’s a different story for the plastics used in cars. At industry events such as IAA in Frankfurt, their potential is only rarely discussed. But that’s precisely what high-tech polymers do for vehicles: Based on calculations by the consulting firm Frost & Sullivan – depending on where it is used – a total of 220 pounds of plastic replaces about 440 to 660 pounds of conventional materials such as steel. This improves a car’s climate footprint: Lighter cars consume less fuel and emit less CO2.
Share of Plastic in Cars Rises
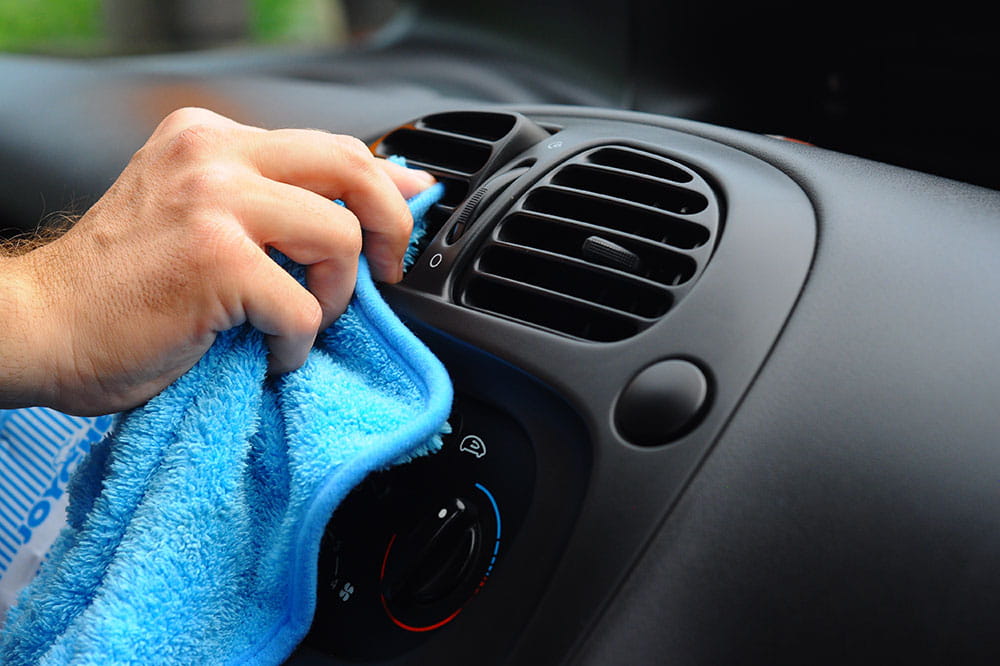
It is no surprise that the share of plastic in cars has continually risen over the last decade. While about 220 pounds of plastic were built into the typical automobile ten years ago, that figure has now climbed to nearly 265 pounds. If you include composite materials and reinforced plastics in the total, the weight of synthetic materials is nearly twice as high. “Plastic” has become an umbrella term for a wide range of polymer materials that can be assigned to three families: thermoplastics, thermosets and elastomers.
Elastomers: Flexible, All-around Players
Elastomers are elastically deformable plastics that return to their original form more or less quickly after being stressed. Elastomers are better known as “rubber” and largely consist of what is called India or natural rubber. Depending on the raw material base, people distinguish between natural and synthetic rubbers, such as EPDM. Ethylene propylene diene monomer rubber is the name behind the abbreviation. It is one of the best-known synthetic raw materials. Synthetic rubber has a great advantage: By adjusting the mixture, its qualities can be influenced selectively. Synthetic rubber can be highly resistant to extreme temperatures and to media. It is especially well-suited as a material for seals in cars.
Elastomers are playing an important role at IAA in Frankfurt, even if they can’t be seen. Inside the IAA’s stars, the Freudenberg Sealing Technologies products made from elastomers include Plug & Seal solutions for electric motors, internal combustion engines, transmission seals, boots and seals for steering and suspension systems as well as injection valves.
There is also a natural variant of rubber: Natural rubber is extracted from latex, the milky sap from the bark of the tropical tree “Hevea brasiliensis.” It offers high mechanical strength, making it ideal for products that dampen vibrations in cars, such as engine mounts, springs, dampers and absorbers.
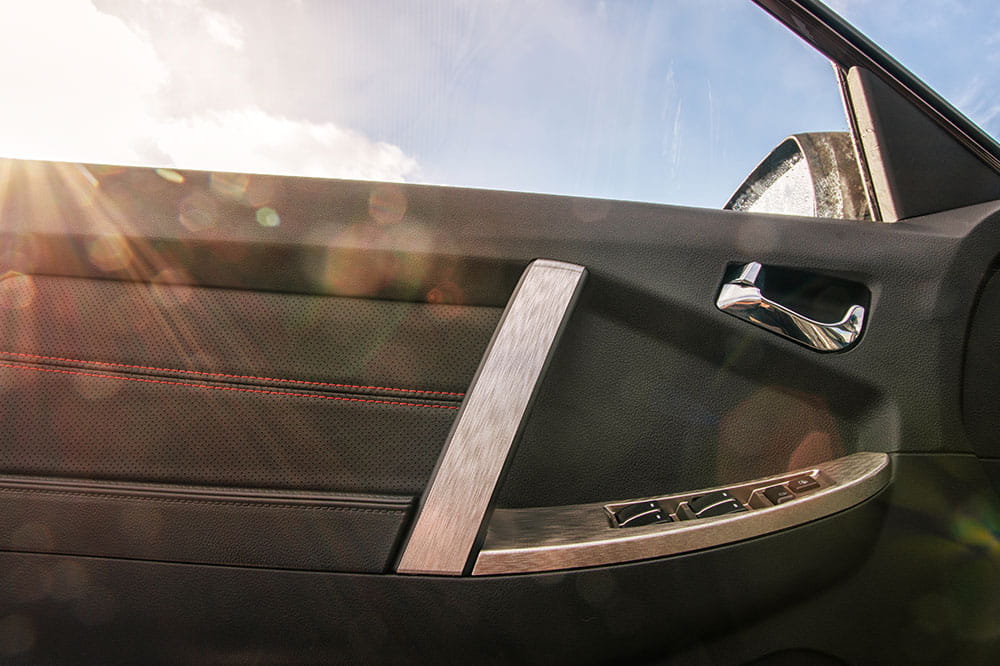
Thermoplastics: Great Freedom in Design
Thermoplastics are among the most successful plastics in cars because they can be produced in injection molding processes, permitting great freedom in the shaping of the material. Thermoplastics are the only type of plastic that can be welded. They can also be easily glued and recycled. Their disadvantage is their resistance to extreme temperatures; the material can disintegrate when exposed to excessive heat. But thermoplastics have now been developed for components exposed to high temperatures, such as intake manifolds, oil filter housings, cylinder head hoods, engine covers and air filters.
Due to their versatility, many subgroups of thermoplastics, such as polyurethane foams, have applications in cars. The foams are used as filler for A-, B-and C-pillars and door modules, as well as in automobile seats, in the cockpit and as soft coatings for control elements. Polycarbonates are hard, shock-resistant and transparent, making them suitable for the diffusing lenses of car headlamps, glasslike roof edging and panorama roofs. Polyamides are frequently reinforced with glass fibers and are increasingly replacing metal components in cars, such as lamp housings and fuel tanks, due to their high mechanical strength. Thanks to their high resistance to oils, they are also used in many applications in the engine compartment.
Thermosets Withstand Thermal-Mechanical Stresses
Thermosets are made from artificial resins whose ingredients such as dyestuffs, separating agents and reinforcing materials are mixed together. They feature high rigidity, hardness and heat resistance. As a result, they are mainly used where high thermal-mechanical strength is required, for example, for housings for water pumps, cable tracks and reflectors. Fiber-reinforced thermosets are also used for body parts such as trunk lids and fenders.
Plastic is our current focus. On single-use plastic as a burden on society – and how we can deal with the problem. And on the question of whether plastic can be a solution. You can find more on the topic “Plastic – Breakthrough and Burden” in the November edition of our company magazine ESSENTIAL.
More news on the subject Sustainability
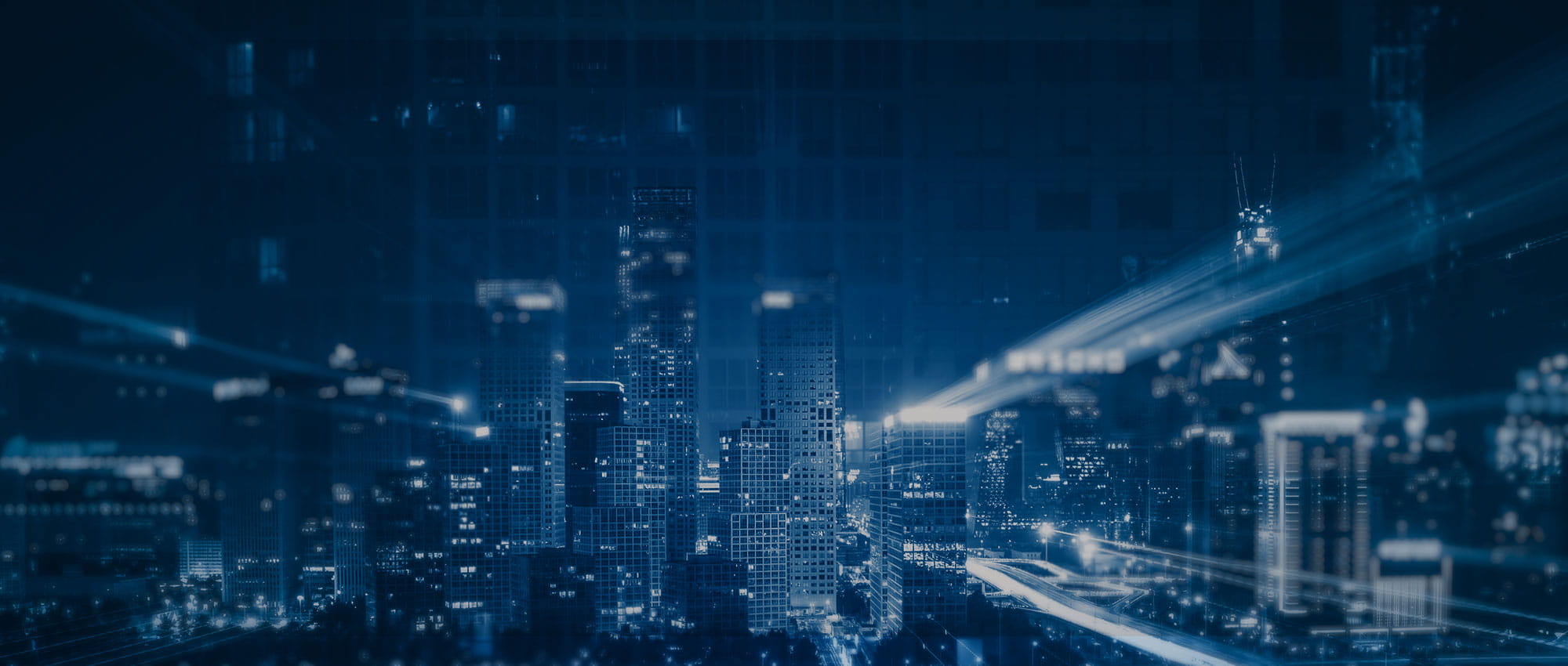
Join Us!
Experience Freudenberg Sealing Technologies, its products and service offerings in text and videos, network with colleagues and stakeholders, and make valuable business contacts.
Connect on LinkedIn! open_in_new