Obtain news and background information about sealing technology, get in touch with innovative products – subscribe to the free e-mail newsletter.
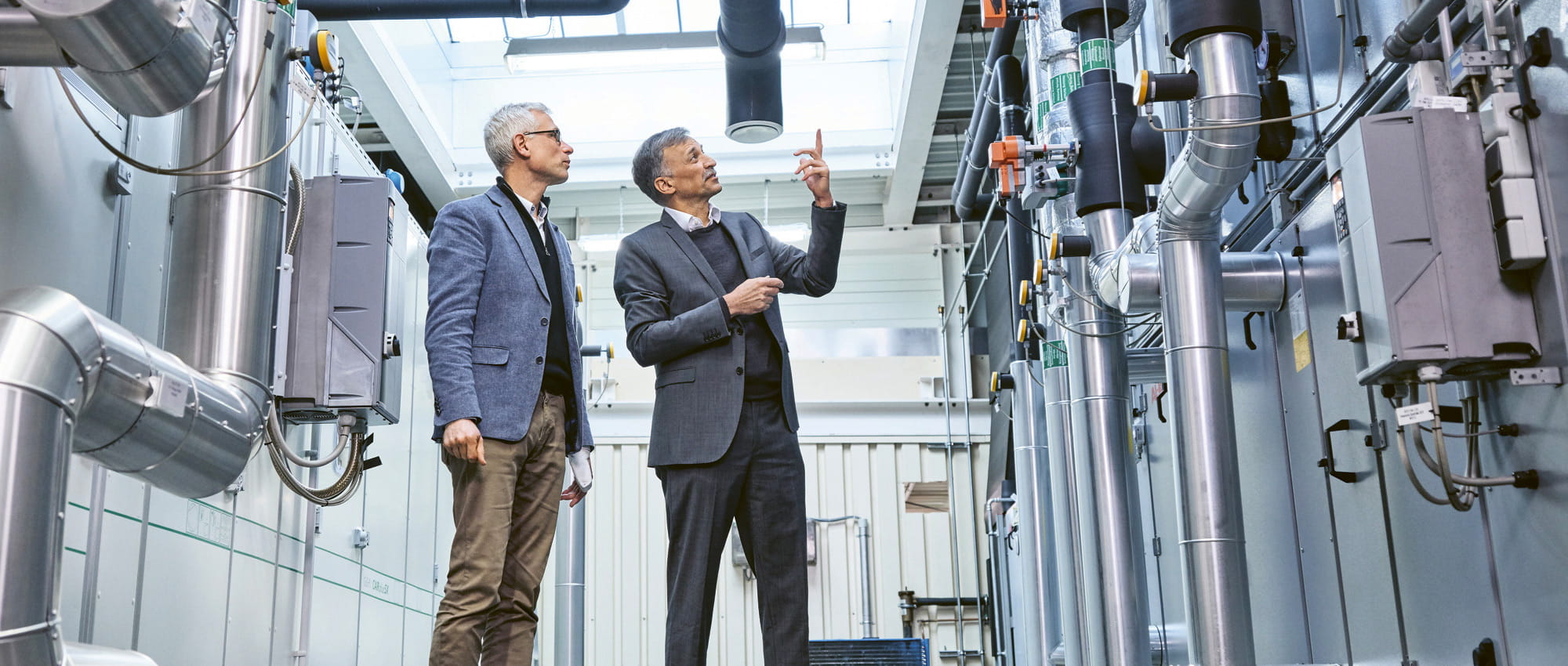
24.05.2022 | Story
Leaving No Stone Unturned
Eliminating fossil fuels as fast as economically possible: Freudenberg Sealing Technologies is demonstrating that this is possible at the Oberwihl plant, on the southern edge of the Black Forest in Germany. But you have to operate many levers at the same time to make it happen.
Freezing cold under a bright blue sky, with views extending into the Alps. In January 2022, half a foot of snow – less than the usual amount but snow, nonetheless – lay upon the fields. This manufacturing site on the edge of Oberwihl, sitting at an elevation of 700 meters (2300 feet), is embedded in the most beautiful natural setting that the southern portion of the Black Forest has to offer.But even if Hans Bruno Hänle, an avid cross-country skier, is able to enjoy the surroundings, the fact that he wants to improve the climate balance sheet of the facility – where Freudenberg Sealing Technologies produces more than a billion O-rings – is not a personal matter at all. Hänle, Commercial Director of the O-Ring Division, rather sees measures to protect the climate as an investment in the plant’s future capabilities. “We are noticing that more and more of our customers want to sell climate-neutral products, so we have to move forward, but in a way that we are working sustainably in an economic sense.”
We are noticing that more and more of our customers want to offer climate-neutral products, so we have to get moving but do it in a way that we are working sustainably and economically.
In 2015, a factory expansion, the partial equivelent of a new plant, laid the groundwork for the current measures. Energy efficiency rose significantly as a result of numerous activities. One was related to heat recapture in the building’s climate control system. Another involved the installation of an energy monitoring system in the finished plant, which could be used to record energy consumption for individual manufacturing areas (see ESSENTIAL 1/2018), and set limits for the maximum load. These efforts paid off: When the Freudenberg Group was looking for two plants in 2019 to showcase climate neutrality, Oberwihl was high on the list. At the time, the plant’s annual energy consumption was about 10 gigawatt hours, of which 82 percent came from the electrical supply and the rest from the consumption of heating oil, which had already declined. The CO2 emissions rooted in energy purchases came to 4,500 tons per year, an amount equivalent to the average annual CO2 emissions from about 500 German citizens. With the help of a professional energy services provider, the plant’s management first identified all the ways that the facility could be made climate-neutral. One initial condition applied: The efforts had to bring real savings. Merely offsetting the emissions by paying compensation was not one of the measures envisioned. “There were also some crazy ideas,” said Dr. Rainer Weiss, who is in charge of both employee safety and sustainability measures at the site. For example, experts have calculated that it is possible to convert the entire supply of electricity to photovoltaics – if solar energy systems were set up on an area the size of five football fields near the plant.
Saving Energy Is Still Important
By the time all the options were on the table, the first wave of COVID hit. But Hänle and Weiss were not held up for long: A second energy services provider jumped into the race with significantly more concrete guidelines, including the amount of investment and amortization timeframes. During the spring of 2021, there were specific, achievable proposals on the table. At their core, they could be divided into three pillars of activity: One, to continue boosting energy efficiency; two, to provide energy to heat the plant without resorting to heating oil, a fossil fuel; and three, with assistance from decentralized systems, generate green energy in amounts that made economic sense.
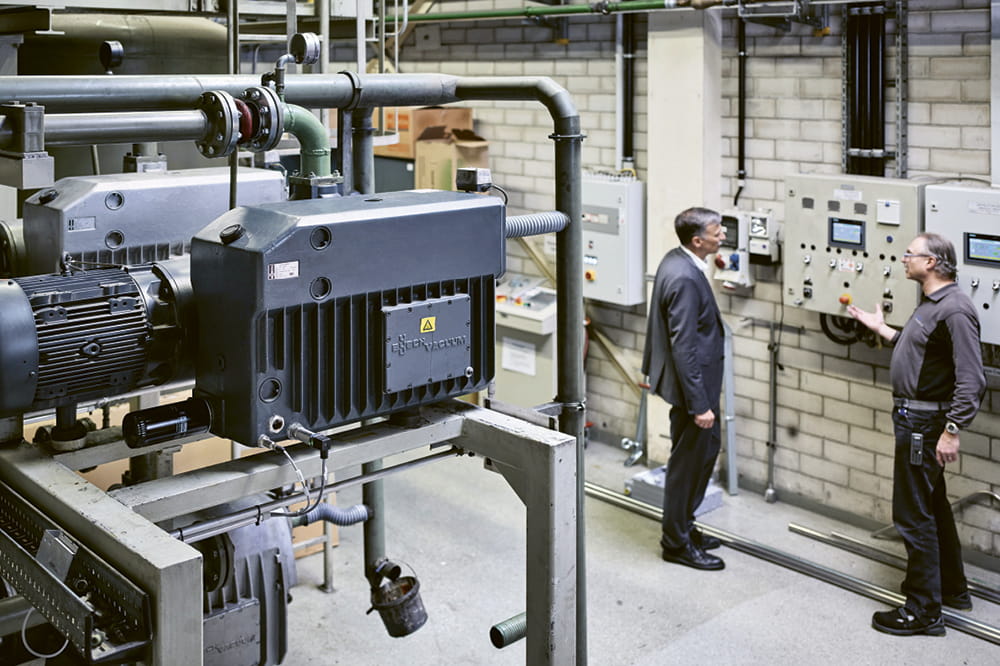
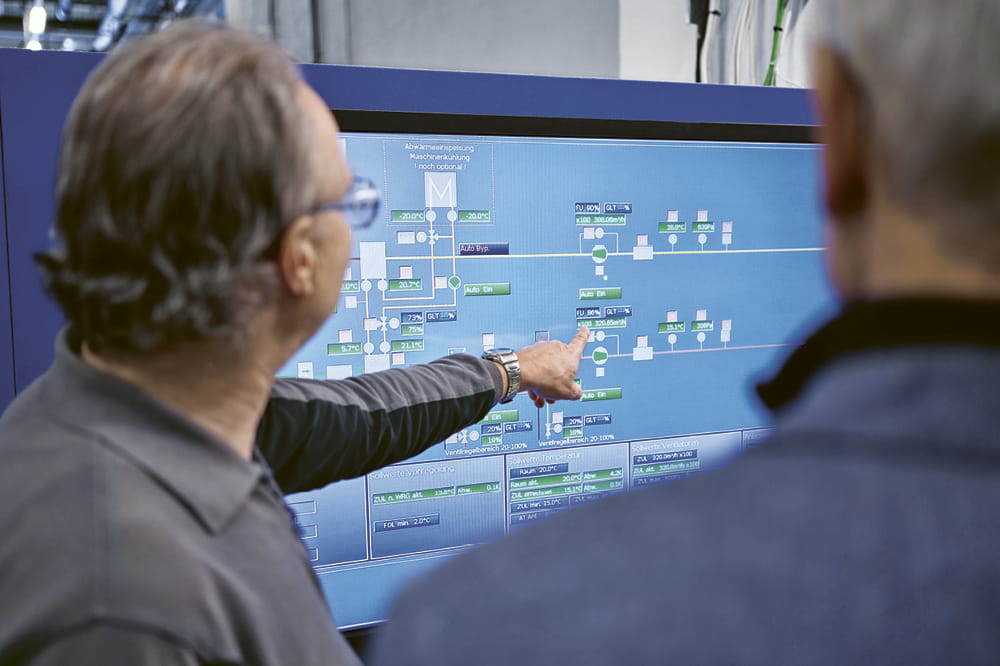
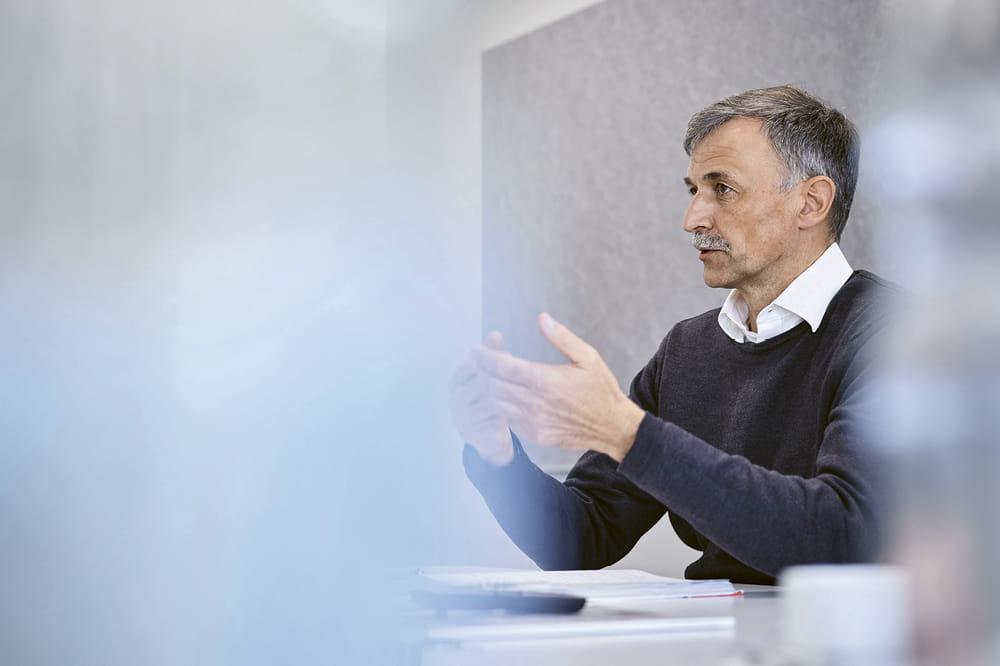
Technician Günter Kaiser cites the example of a rolling mill where a primary elastomer material is processed into a thin layer that is used to produce seals. He points to the fact that energy efficiency in manufacturing is far from being maximized. “It is like a pasta machine. When you feed the mass inside at the start, the machine needs a great deal of power. Later, when the layer is rolled again, the required effort declines with each pass.” So far, hydraulic drives that always operate at maximum output have been used in these rolling mills – as in many other machines. By converting to adjustable servo-hydraulic drives, a substantial share of the drive output can be saved. Kaiser plans to determine the exact amount of savings in the next few months, laying the foundation for investment decision-making. The situation seems similar in many other areas. For example, waste heat generated by machine cooling systems is still not being used. And the copious data that would come from the continuous monitoring of building technology could be analyzed prospectively using artificial intelligence, to identify anomalies more quickly.
New Sources of Heat and Electric Current
In Oberwihl, however, all machines – including the ovens needed for downstream heat treatment – are heated electrically. But the building heating continues to use fossil fuel heating oil. With the Black Forest on its doorstep, the solution is literally not far off: wood chips, generated by the nearby woodworking industry, are the fuel for two heating boilers. Equipped with an automatic filling system, they produce more than 600 kW of heat output. The construction application for the boiler house has already been submitted. The boilers should go into operation in early 2023. The amount of heat produced from wood could continue to increase if a small combined heat and power plant is added to the facility. “Then it would be possible to reduce the current heating oil consumption by up to 96 percent,” Weiss said.
Energy for heating as far as possible without fossil-based heating oil.
The conversion to renewable electricity is easier in some respects – and more difficult in others. It is easier because the electricity for all the Freudenberg plants in Germany is sourced centrally, so a rapid conversion is more efficient due to the large volumes being purchased. It is more complicated because Oberwihl hopes to generate a portion of its electricity on its own, on the plant grounds. The plan to cover the entire employee parking lot with solar surfaces is dormant for now. That’s because simple stilts are not an option due to the amount of snow in the region. The structure would have to be made of steel. Thus, the overall system is not being amortized over a long depreciation period, at least in terms of current steel and construction costs. “We are now examining what we can achieve with roofs,” Hänle said. The work won’t be easy: Exhaust air systems and light hatches are obstacles. Yet it is important to him to leave no stone unturned as he monitors every aspect of sustainability, including the economic issues. The bottom line is that he and his colleagues are helping to keep the Black Forest covered in a blanket of snow each January.
More news on the subject Sustainability
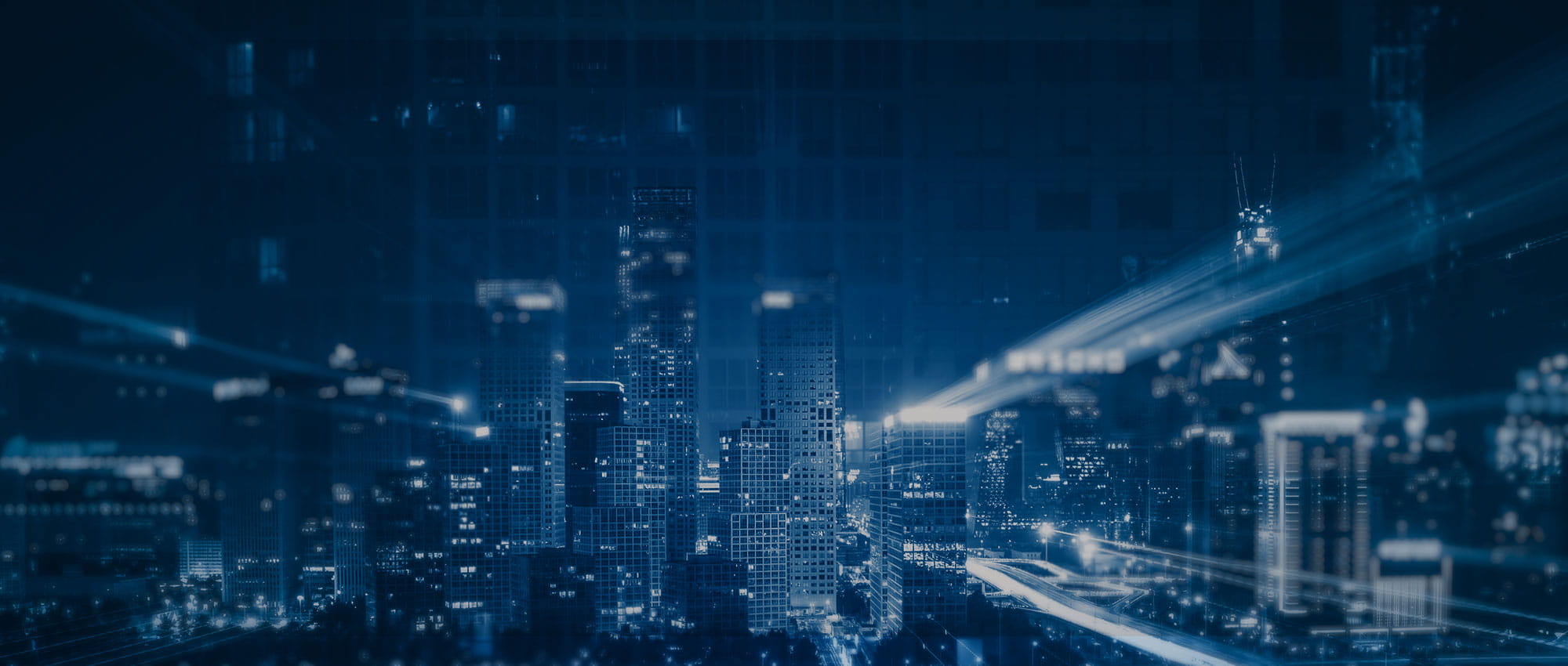
Join Us!
Experience Freudenberg Sealing Technologies, its products and service offerings in text and videos, network with colleagues and stakeholders, and make valuable business contacts.
Connect on LinkedIn! open_in_new