Obtain news and background information about sealing technology, get in touch with innovative products – subscribe to the free e-mail newsletter.

29.10.2024 | Story
Hydrogen Still Beckons
The prospects for hydrogen have been swinging between hype and disenchantment for decades. But something is different this time. Marcel Schreiner, Global Segment Director, Energy, at Freudenberg Sealing Technologies, explains why he is impressed with the technology’s long-term potential and why a radically new advance is needed in sealing technology.
Mr. Schreiner, why is hydrogen the topic for the future?
Schreiner: Let me turn that question around: why not? It is interesting that the fascination with the topic comes in waves. Early in the 2000s, it was thought that the fuel cell automobile was on the brink of a breakthrough. Then came the disenchantment. Today we have a different situation: We know that hydrogen is the key. About 170 countries now have a decarbonization strategy – anyone who really wants to be CO2-neutral needs hydrogen. The current hype is no longer limited to individual applications such as fuel cells but rather involves the decarbonization of all industry. It is especially relevant for the steel and chemical industries.
Marcel Schreiner
As Global Segment Director, Energy, at Freudenberg Sealing Technologies, Marcel Schreiner is responsible for sales to customers worldwide. He keeps an eye on every application in the energy sphere that uses sealing solutions: manufacturing, transport, warehousing, and operations. Schreiner is a graduate engineer and has worked for Freudenberg Sealing Technologies since his dual study program in 2002.
What brought the hype to a close in the 2000s?
Schreiner: What happens with any hype. At some point, it subsides. The market wasn’t ready. The availability of green hydrogen was not taken into account. But the question is, what lesson do we draw from the experience? At the start of the hype back then, we formed an independent business unit dedicated to hydrogen. We developed know-how. When there was no global breakthrough, we could have put everything back in the drawer. But we deliberately decided not to. The current trend proved us right. The opportunities for us are no longer just in hydrogen’s applications but in its production, the electrolysis, and all the steps in-between.
But there is more than one type of electrolysis ...
Schreiner: That’s right, there are currently various processes. Electrolysis with anion exchange membranes (AEM) interests us right now. It may well prove to be inexpensive and effective – but it is not yet tried and tested. Here we can contribute our development expertise. Alkaline electrolysis takes place in a strong, chemically corrosive environment, so identifying the right material is a challenge. With PEM electrolysis, the main issue is high pressure. These are two different challenges, but we know our way around both fields. We’re also good at manufacturing at high volume since we have expertise in automation. Our customers find that helpful when they want to ramp up production later.
Standardization is not yet in sight?
Schreiner: That challenge will be with us for a while: Every customer has an individualized design, and transferability is limited.
Why do the customers vary so much?
Schreiner: For historical reasons. The outputs were relatively low for a long time. By 2050, we need at least 1200 gigawatts of electrolysis capacity to achieve the global CO2 goals. The capacity today is closer to 3 gigawatts. That’s quite a difference. So companies are pursuing their own strategies: Some are comfortable with the smaller dimensions because they are good at manufacturing at that level. The others want to grow quickly because they see the potential. These approaches necessarily develop into different technologies.
So processes will improve?
Schreiner: Definitely, but we are still interested in standardization. Our advantage is that we now have so many customers in the electrolysis field that we are being integrated at an early stage. That’s where there is an opportunity for standardization. When we can turn to proven designs, the result is process reliability for customers.
It takes a radical approach. That is the standard that Freudenberg has championed for 175 years.
You mentioned stringent material requirements – in compressors, for example?
Schreiner: For mobile applications, hydrogen is stored at 350 or 700 bar, so it has to be compressed first. Hydrogen is highly volatile, permeative and combustible. Not many compressors are actually capable of achieving 300 bar. Overall, the level of wear due to these extreme requirements is quite high, so the lifespan for seals is a few hundred operating hours today.
That’s not very much.
Schreiner: That’s true. And it spurs our engineering ambitions and speaks to our souls as developers. We would be happy to develop a solution that lasts much longer. 1,000 hours would be a good start. Not many companies can meet the requirements for pressure and speed in combination with dry-running. That motivates us. In addition, if I have a seal that works well in a piston compressor, it is easy to use in many other situations, from refueling to electrolysis.
Is the type of material the challenge here?
Schreiner: It will probably be a combination of material and design. The obvious options are specially developed, wear-resistant, high-performance thermoplastics that show little extrusion under high stresses. Perhaps a fiber blend. But that’s all speculation at this point. We will certainly have to show a certain openness to materials and technologies. The solution will surely be a radical approach, but that is what is needed. That is our standard, and Freudenberg has championed it for 175 years.
Seals are also needed in transportation…
Schreiner: In transportation, we are in a situation where the industry has not yet agreed on the approach that will prevail. All the opportunities are variations of already existing technologies. It does not make much difference whether I transport natural gas or hydrogen in my pipelines. The conversion to ammonia to improve transport has been around 100 years, namely for fertilizer. So the technological hurdles are steadily shrinking. We are monitoring all this, but we believe we will be in a good position as soon as it becomes clear which solution will prevail. Other areas present greater technological challenges.
There are now more voices expressing fears that hydrogen developments will take much more time…
Schreiner: At the start, I spoke about the hype during the 2000s. We now have low-level hype coming from the announcements for various investment programs, from U.S. President Biden’s Inflation Reduction Act to Europe’s Green Deal. We are now at the realism stage. The developments are not moving as fast as many imagined they would. That is completely logical and hasn’t surprised me in the least.
We want to be ready when the customer is.
You expected this?
Schreiner: Yes. After all, before we can deal with hydrogen’s applications, we have to have the gas in the first place. It is completely logical to have a time lag the further I go along the value creation chain. Fuel cells can’t take off if the hydrogen isn’t there. That’s why many people are hesitating to invest in the appropriate projects, and the overall impression intensifies pessimism. But we must not overlook the fact that investments are moving along nicely. There are funding programs worldwide, although disbursing many billions of euros is no easy task. Political ambitions run into a sobering bureaucratic reality. Still, nothing has changed in the prospects for hydrogen.
That again sounds quite optimistic.
Schreiner: We see a much more positive mood in companies than we do in the general public. Many companies, especially the electrolysis manufacturers, haven’t had much trouble filling their order books. When the hype cycle starts again, the issue will be the capacity to quickly meet the demands of the market.
What does that come down to?
Schreiner: The standard we have set for ourselves is that our product should be an out-and-out winner when the customer tests it. We’re still not there yet in every case – but that’s not a problem at this point. But when the train gets rolling, it will make the difference. We want to be ready when the customer is.
The trend toward hydrogen is not reversible?
Schreiner: No. The potential is building. If we accelerate our production of green hydrogen right now, an even greater expansion of solar and wind projects will follow. In the meantime, we have megatrends such as electric mobility and artificial intelligence at play – both will need energy. The connections run in all directions. And hydrogen is right in the thick of them.
The Future Is Hydrogen
From H₂ Production to Usage: Comprehensive Insights on Production, Distribution, Storage, and Future Applications with Solutions. Explore full spectrum in our webspecial!
Hydrogen Webspecial open_in_newMore news on the subject Sustainability
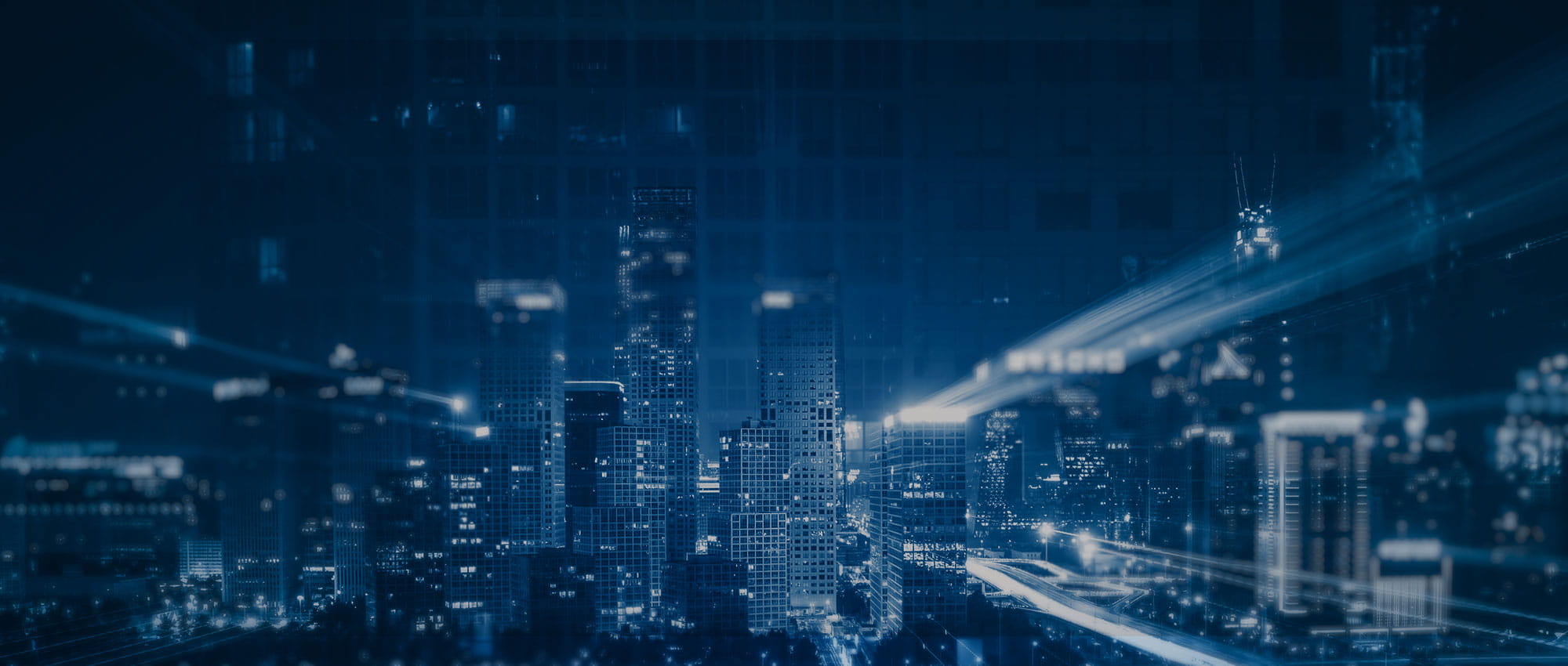
Join Us!
Experience Freudenberg Sealing Technologies, its products and service offerings in text and videos, network with colleagues and stakeholders, and make valuable business contacts.
Connect on LinkedIn! open_in_new