Obtain news and background information about sealing technology, get in touch with innovative products – subscribe to the free e-mail newsletter.
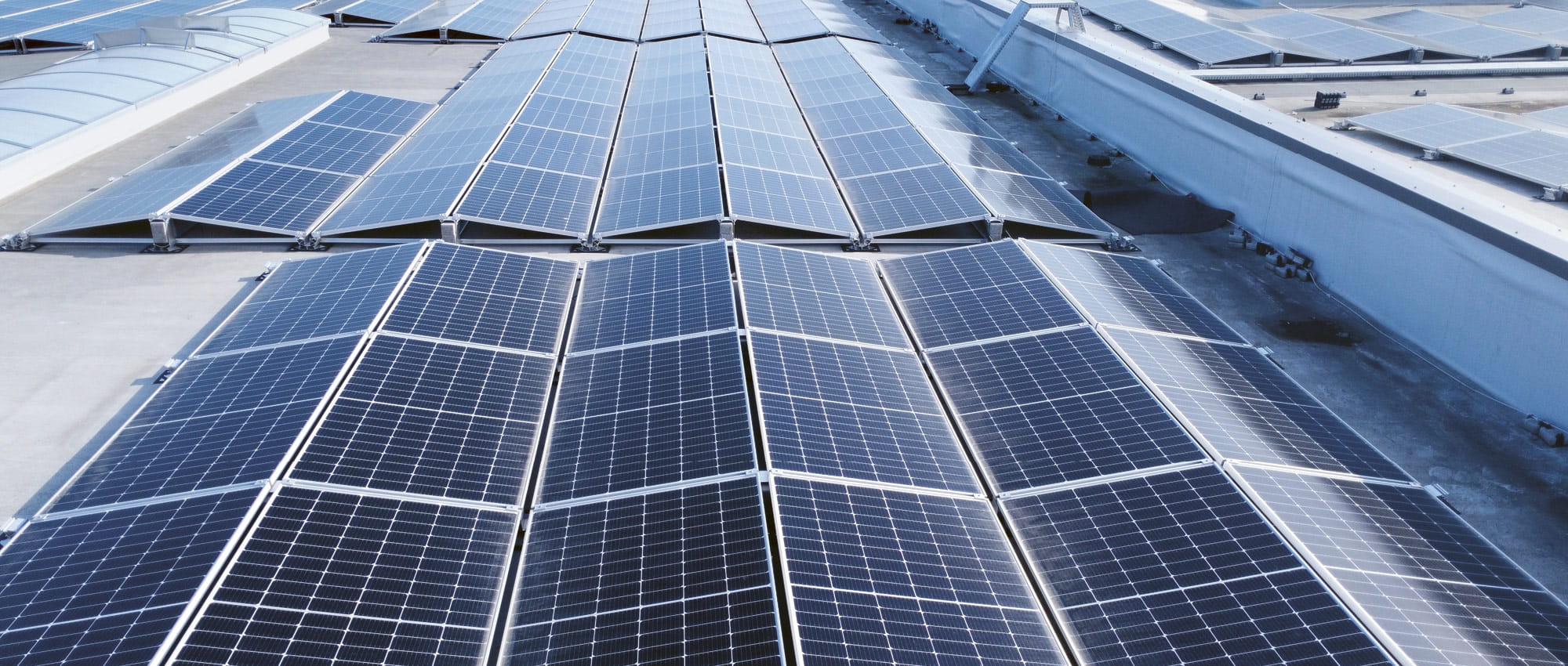
18.07.2023 | Story
Using Energy Efficiently
Economies are facing massively higher energy costs. Using energy more efficiently and sustainably is in greater demand than ever. Freudenberg Sealing Technologies has taken both imperatives to heart for some time.
Numerous work steps are required before a seal takes its final shape. Its materials are blended, kneaded, folded and rolled, among many other steps. Machines play a role at every station, and they need one thing above all else: energy.
A Groundbreaking Technology Decision
Electricity and heat are key factors in the production of high-performance products, the kind that Freudenberg Sealing Technologies manufactures worldwide. The company wants to use the energy for these processes as efficiently, cost-effectively and eco-compatibly as possible. Fortunately, it can play the cards it was dealt decades ago when a groundbreaking technology decision was made. In effect, the company’s leaders anticipated Freudenberg Group’s current sustainability program. Among other things, it advises each business group to electrify technologies to be-come less dependent on fossil fuels.
“Back in the 1980s, we started out by exiting steam-heated presses,” explains Hans Kloos, who is in charge of the Sustainability Program, Investments and Energy Auditing at Freudenberg Sealing Technologies. “There were practical reasons for this at the time. Our management was turning to smaller machines that were supposed to be erected and relocated flexibly based on production requirements. The fact that they could do without fossil fuels, usually consuming less than 50 kilowatts of power input, was a welcome side benefit.” In any case, vulcanization presses have long been heated electrically and steam-driven presses have given way to electrical systems.
Clean Exhaust Air Biologically
“Our goal is to completely do without fossil fuels,” highlights Karl Ludwig Stein, one of Kloos’ colleagues. “In manufacturing, we use them at very few locations. It is therefore increasingly a matter of doing without them for the heating and air-conditioning of buildings or for systems such as exhaust air treatment equipment.” These systems filter solvent vapors generated during the coating of steel or plastic carrier parts. The coating ensures that elastomers adhere reliably to the carrier portion of the seals after the forming process. To keep the vapors from escaping into the air, they are suctioned away and often burned with a gas ignition mixture. There are also electrical alternatives to this process, although Freudenberg Sealing Technologies is taking a different approach at some sites, such as Reichelsheim in Germany and Kufstein in Austria. “We are forcing solvent-infused waste air through a kind of composting system where bacteria break down the pollutants. This biological approach saves heating energy in the process,” Kloos explains.
Success With a Mix of Measures
The company is striving to use green electricity as much as possible and even producing its own. “We are pressing ahead with the expansion of photovoltaic systems where it makes sense,” Kloos says. The company’s sites at Emmerich in Germany, Chennai in India and Parets in Spain are already equipped with large photovoltaic systems. More locations will follow. Besides the increased use of solar energy, Kloos, Stein and the plant managers are examining sites where energy storage systems can cover energy needs at night. The switch from gas to hydrogen is also on the agenda.
On the other hand, the company’s facility in Öhringen, Germany, has no heating system whatsoever. The waste heat from the manufacturing machinery is fully sufficient. Due to the green components of the power supply mix, the site has been operating nearly CO2-neutrally for about 15 years. The new plant in Emmerich is following its example by substituting waste heat for a heating system. At sites where using waste heat would be insufficient or impossible, the heating systems will be gradually modernized. “Energy efficiency and a departure from the use of fossil fuels are approaches that we have been pursuing globally for a long time,” Stein said. “The underlying quest for CO2 neutrality has already taken us a long way and will continue to be a driving force at all of our facilities.”
Our goal is to completely do without fossil fuels. In manufacturing, we use them at very few locations.
Karl Ludwig Stein, Head of Factory Standards & Sustainable Technology Alternatives
Energy-Saving Effects Around the World
All over the world, Freudenberg facilities are turning to sustainable approaches and energy conservation. Here are a few examples:
- India
The company’s facility in Chennai covers part of its energy needs with a large photovoltaic system on its roof. Consequently, the Morinda plant that is scheduled to be put into operation in 2024 will also get one. In addition, there are plans to bring the energy-intensive phosphating system to the proper temperature with a combination of a heat pump and waste heat from the production area.
- Austria
A mountain stream crosses the factory grounds in Kufstein. Its water is not only used to cool the incoming fresh air in the production areas, but also the machines and tools. The savings in energy consumption are equivalent to the supply for 200 private households for a year.
- Spain
A new plant, including a warehouse and administrative area, is being built at the company’s site in Parets. A photovoltaic system on the building’s roof will provide a portion of the energy that it consumes. Waste heat from machines will be used for heating and hot water. A biological system handles the exhaust air treatment for the production area, thus saving energy. Fossil-based energy has been ruled out. The annual energy savings is projected to reach 844 megawatt hours, with annual CO2 savings of 110 tons.
- England
The North Shields facility located near Newcastle has reduced its natural gas consumption by nearly two-thirds. Destratification blowers under the ceiling send heat back to the work area and prevent heat loss through the roof. In the summer, roof ventilators reduce the need for air-conditioning.
- USA
Freudenberg Sealing Technologies plans to move in a different direction on climate control at its manufacturing plant in Necedah, Wisconsin. As part of the planned replacement of the heating and cooling systems there, the waste heat from the cooling system will be pumped into the ground during the summer and be recovered during the winter by using heat pumps.
More news on the subject Sustainability
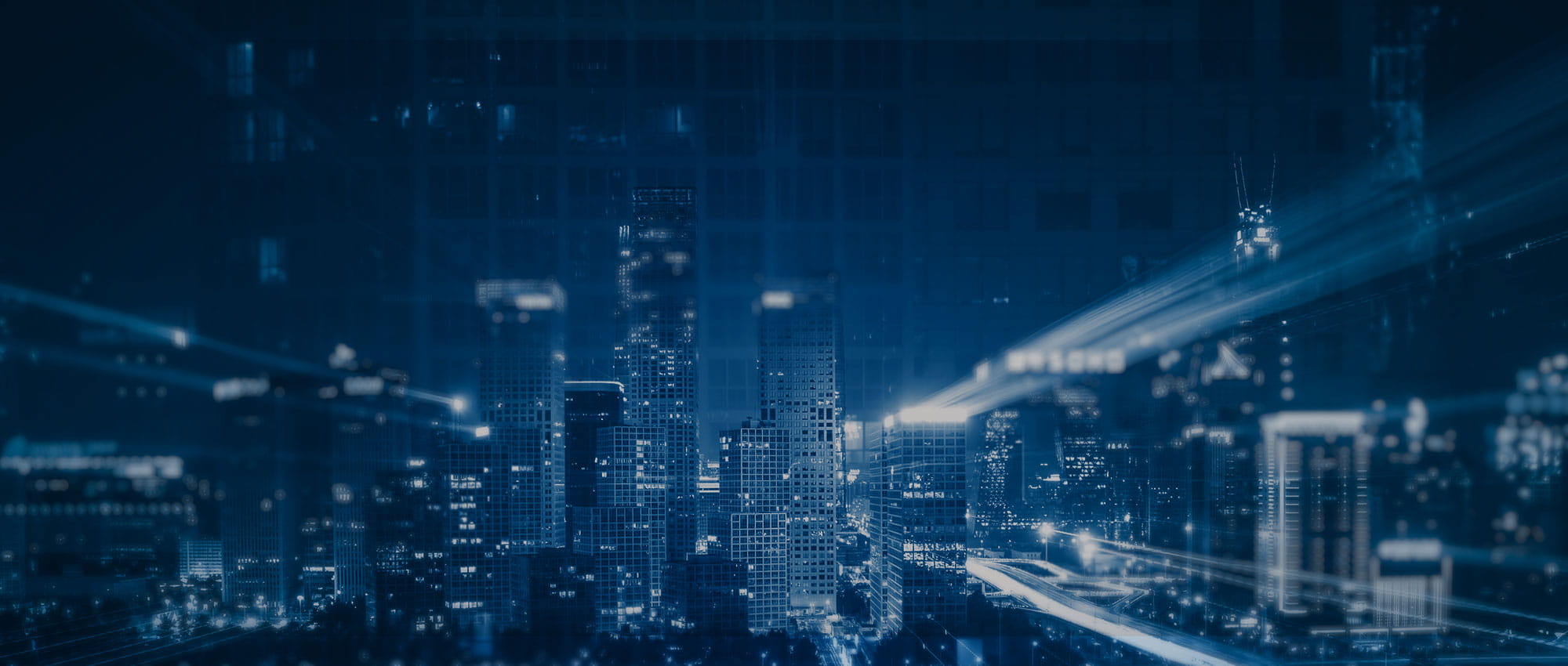
Join Us!
Experience Freudenberg Sealing Technologies, its products and service offerings in text and videos, network with colleagues and stakeholders, and make valuable business contacts.
Connect on LinkedIn! open_in_new