Obtain news and background information about sealing technology, get in touch with innovative products – subscribe to the free e-mail newsletter.
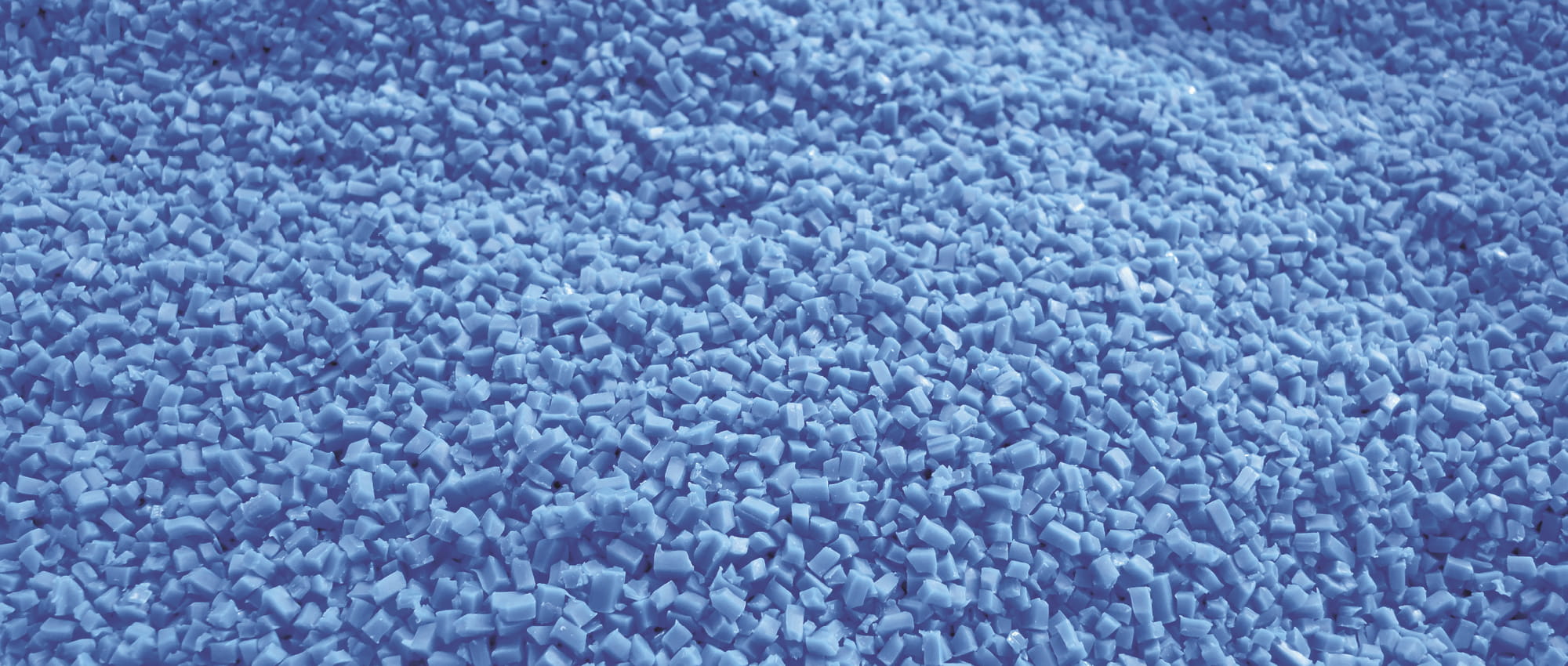
High Quality Material – Thanks to AI
Materials are sensitive. If the granulate of thermoplastic polyurethanes is a bit too moist, the quality of the parts made from it suffers. Freudenberg Sealing Technologies is putting a stop to the problem, with the help of a digital shadow.
Sometimes it is the small things that make all the difference. Process engineers at Freudenberg Sealing Technologies are aware of this. Thermoplastic polyurethanes (TPUs) are among the main materials used in the manufacture of hydraulic and pneumatic seals like those found in excavators’ mobile hydraulics. Their quality contributes to the functionality of crucial components. If the TPU granule is only slightly too moist, its flow behavior changes during the injection-molding process. The result: Polymer chains are unable to form sufficiently. Then qualities such as tensile strength and elongation-at-break are not as good as they should be.
Our samples show that AI forecasts of moisture content in the granules deviate by merely 0.005 percent from the results of the manual analytic measurement.
Armin Hermann, Manager, Materials Lab, Schwalmstadt plant, Freudenberg Sealing Technologies
The Goal: 24-Hour Monitoring
So, if you don’t want to find out at a quality inspection that an entire batch of manufactured parts is defective, you have to start with the storage of the materials, in this case, TPUs. At the company’s Schwalmstadt plant, north of Frankfurt/Main, Germany, they are stored in 6-ton silos. The determination of granular moisture is carried out manually. The silos must be opened for the samples to be extracted. But the process is only a snapshot. “What we needed was 24-hour monitoring,” recalled Armin Hermann, Manager of the Material Lab at Schwalmstadt. He has recently attained that level of monitoring as head of a 12-person project team.
Artificial intelligence was the key to success. But there was plenty of work ahead of the participants before they reached that stage. Process engineers in Schwalmstadt and a team of Freudenberg Sealing Technologies IT experts first had to learn to speak the same language. “Perhaps putting it a bit too simply, you can think of it as Analog 2.0 meets Industry 4.0,” Hermann said. “Two worlds came together in one project team.” Although communication was an obstacle at the start, the two groups were soon getting along better and better. To write an algorithm, it was important for the IT experts not only to understand certain plant processes – they had to completely immerse themselves in them. “We asked question after question to comprehend the problem and the process,” said Data Scientist Anna Lüders, a member of the in-house “Advanced Analytics Team.” It was her job to create the simulation model that enabled precise forecasts of moisture levels in TPU granules.
The Solution: A Digital Shadow
A machine-learning model had to be developed to determine the TPU’s residual moisture. The model was based on the construction of a structured data transmission and storage system. Experts on a Freudenberg team devoted to MES and IIoT systems were responsible for the model. The database’s foundation was data that had been collected manually. To enrich the information with current data, the team installed sensors inside and outside the silos. They capture temperatures and atmospheric humidity in each case. Other parameters such as storage duration go into the database as well. The moisture content of the granules can be derived from these indicators. Manual measurements have been reduced. But they continue to be needed to compare real figures with the values from the algorithm that IT expert Lüders developed. It quickly became clear that the work had paid off. “Our samples show that AI forecasts of moisture content in the granules deviate by merely 0.005 percent from the results of the manual analytic measurement,” Hermann said. Certainly a negligible difference.
By the way, “digital shadow” is the technical term for the kind of system set up in Schwalmstadt. It took the team a year to develop it from an idea to a successful implementation. Today, the moisture of the granules is calculated and visualized automatically. If limits are exceeded, the system triggers an alert so that the process technician on site can promptly intervene. This ensures that TPU granules with the proper quality reaches the production process – a fact that one major customer has been able to verify multiple times. Before production, the company always gets a sample from the batch it is due to receive. Since AI has been part of the monitoring process, the material has not been rejected a single time. “This has added to our customer’s confidence in us,” said Hermann, the project manager, “even though we have not changed the recipe for the material. With AI’s help, we are simply optimizing physical features.”
Digital Twin vs. Digital Shadow
A digital twin and a digital shadow allow real-time monitoring of a real object (for example, a silo). Both gather information and analyze events and processes relating to the object and provide collections of data. An interaction with the real object is only possible with the digital twin, however.
The Benefits: Identifying Interfering Factors More Easily
Yet another benefit was drawn from the visualization of the processes. Some materials have to be aged artificially. This involves feeding warm air into the silos over a specified period. Measurements of the exhaust air have now shown that the heat generated there is never reached. Tests showed that the insulation of pipes and a part of the silo was sufficient to achieve the same aging effect with the input of less hot air. This insight will help save energy. As its next step, the team will tackle a different topic: dust development in silos. Dust particles promote the formation of foreign bodies that pose problems in injection molding.
“We are completely satisfied with the simulation model,” Hermann said. “For one thing, because we finally have answers to the questions that have been unanswered so far. For another, because we see some of our theories being confirmed.” Lüders sees successes being achieved that fulfill the early promise of AI. “With the help of a digital shadow, we are identifying process deviations earlier and we are improving process stability as a whole. The sources of disruptive factors are easier to identify today, and our process expertise is increasingly growing in a structured way.” This is all clearly added value – thanks to the use of a digital shadow.
This article originally appeared in ESSENTIAL, Freudenberg Sealing Technologies’ corporate magazine that covers trends, industries and new ideas. To read more stories like this, click here.
More Stories About Technology
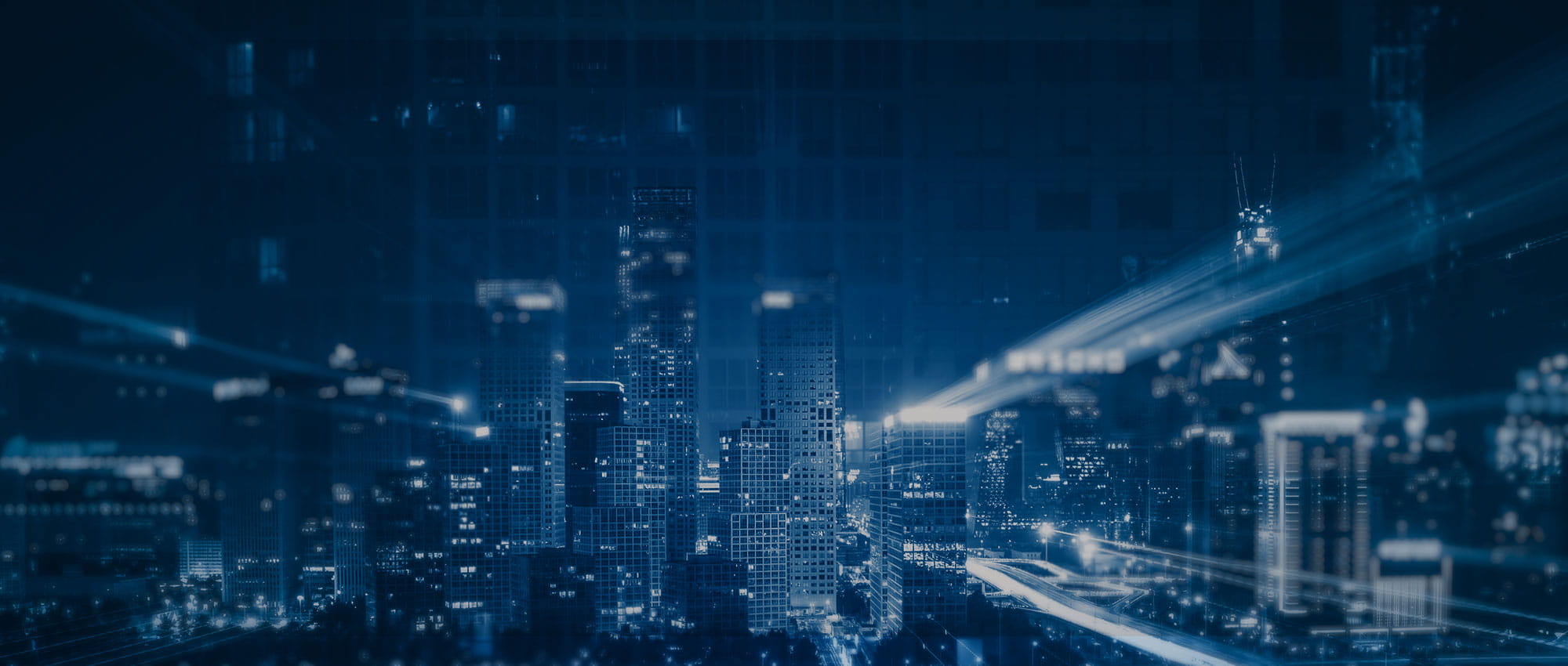
Join Us!
Experience Freudenberg Sealing Technologies, its products and service offerings in text and videos, network with colleagues and stakeholders, and make valuable business contacts.
Connect on LinkedIn! open_in_new