Obtain news and background information about sealing technology, get in touch with innovative products – subscribe to the free e-mail newsletter.
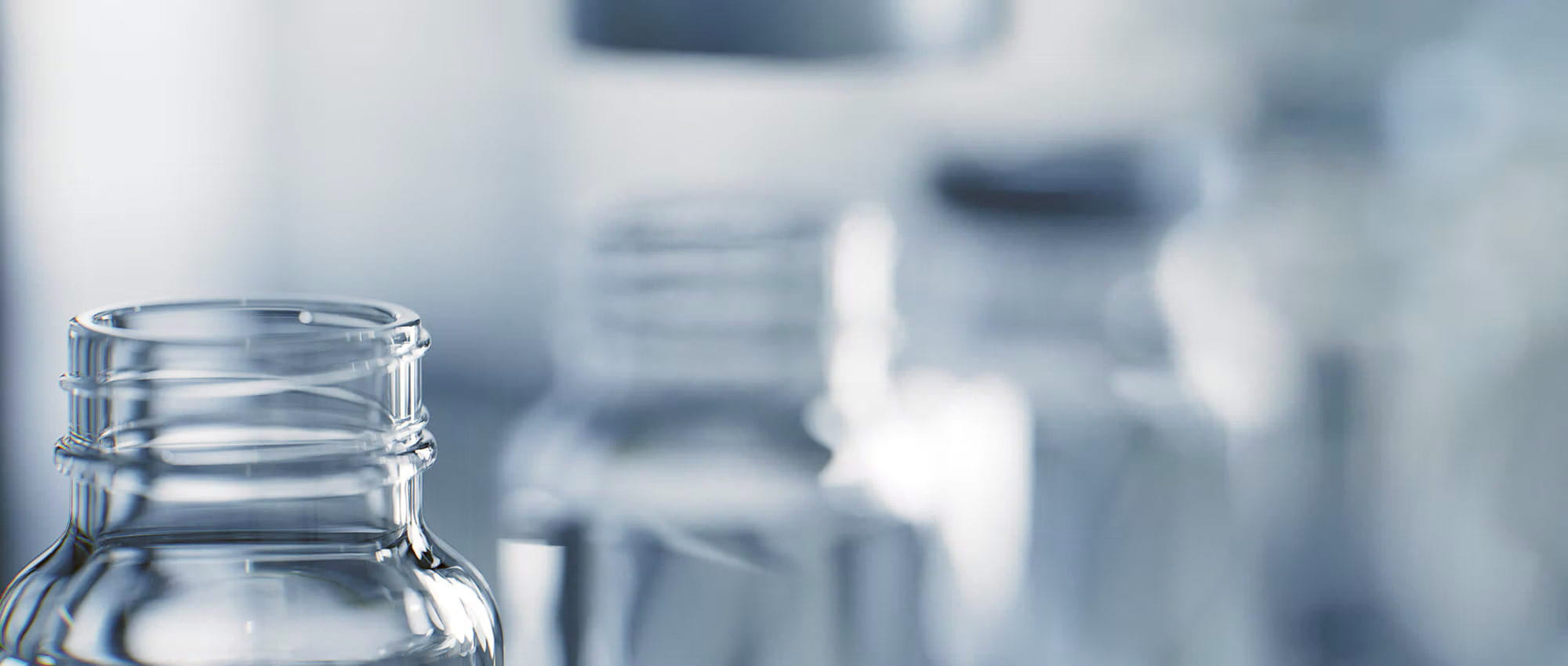
31.01.2023 | Story
Not Just Safe but Pure
Clean surfaces are essential when it comes to the production of pharmaceuticals. Impurities often show up at the microscopic level and cannot always be recognized immediately. Here is how the industry ensures safety with standards and the right materials.
When infants around the world were born with abnormalities in the 1960s, doctors and scientists looked feverishly for the cause. It took several years for them to identify the connection between the abnormalities and the sedative Contergan. The new drug had not been adequately tested for side-effects before it was introduced. As a result, scientists demanded clearer and stricter rules. In 1968, the World Health Organization (WHO) finally called on manufacturers to follow guidelines for “good manufacturing practice,” or GMP for short.
Stainless Steel 1.4301
This material is the earliest example of non-rusting steel that is still commercially available today. It can be used from 600°C (1,112°F) down to almost absolute zero. This steel is resistant to food acids, weak organic and inorganic acids, water and atmospheric humidity. It is used where surfaces have to be hygienically clean, as in the food-service and pharmaceutical industries.
© iStock: josemoraes
The guidelines did not merely involve side effects. They called for companies to ensure that the product remained pure at each step in the production process. Contamination had to be prevented. These GMP guidelines are the standard today. The WHO examines and reworks them regularly, and they serve as a foundation for medical drug laws in individual countries. The regulatory framework covers the entire lifecycle of the medicine, from quality management during production, to transport and storage, all the way to its consumption by the patient. That’s because there is the risk of pharmaceutical contamination at each step.
Contamination Can Happen at Any Time
All of this was new at the time. There had never been the continued monitoring of medicines beyond their actual production before. But it became increasingly clear that contamination can happen at any time, and the tiniest particles can enter the product at any point in the chain.
One of the most obvious solutions available today is to thoroughly clean surfaces and machines. This is where the material used in the machines becomes crucial. If machine surfaces are cleaned with aggressive chemicals, they have to withstand the exposure. It is even better to design surfaces so they are easier to clean. For decades, a rule has been applied to the pharmaceutical industry: Ingredients are not the only thing that are all-important – it is just as crucial to use the right materials. And that applies to the materials in all the machines and on all the surfaces that play a role in the process.
Stainless Steel, Grass and Plastics
Materials such as stainless steel and glass quickly caught on in the pharmaceutical industry. They were both resistant and robust. In concrete terms, that often meant stainless steel type 1.4301. This material has been used in the pharmaceutical industry since the 1920s. It offers still other advantages: It doesn’t rust and can withstand a wide range of temperatures – from -273°C (-459°F) to +600°C (1,112°F). These qualities make stainless steel an ideal material for surfaces and pharmaceutical equipment and machine components.
But not everything could – or can – be made from stainless steel. Even before the era of widespread plastic use, medical devices had individual components made of these materials, especially buttons and switches. Today plastics have prevailed on a broad front. So it is all the more important to pay attention to details like chemical resistance. Some pharmaceutical developers are increasingly turning to antibacterial materials containing a percentage of silver ions. This special additive destroys the cell walls of microorganisms, killing them. This doesn’t eliminate the need to clean surfaces regularly, however, but it does minimize the risk of contamination between cleaning intervals.
The key aspect of the GMP guidelines is that they especially hold the pharmaceutical manufacturers responsible. Before a medicine is introduced, they have to define a multi-step release process and continue to monitor the product after the launch. As a result, nearly every pharmaceutical company today has its own quality assurance department. The employees who work there constantly audit the purity of the medication and the cleanliness of the manufacturing and packaging operations. The formula is stringent guidelines, complemented by the right materials, to produce a reliable quality standard. For a medication to heal the patient, it is not just important to consider its effectiveness or its side effects. The environment where it is manufactured is important as well.
This article originally appeared in ESSENTIAL, Freudenberg Sealing Technologies’ corporate magazine that covers trends, industries and new ideas.
More news on the subject Technology & Innovation
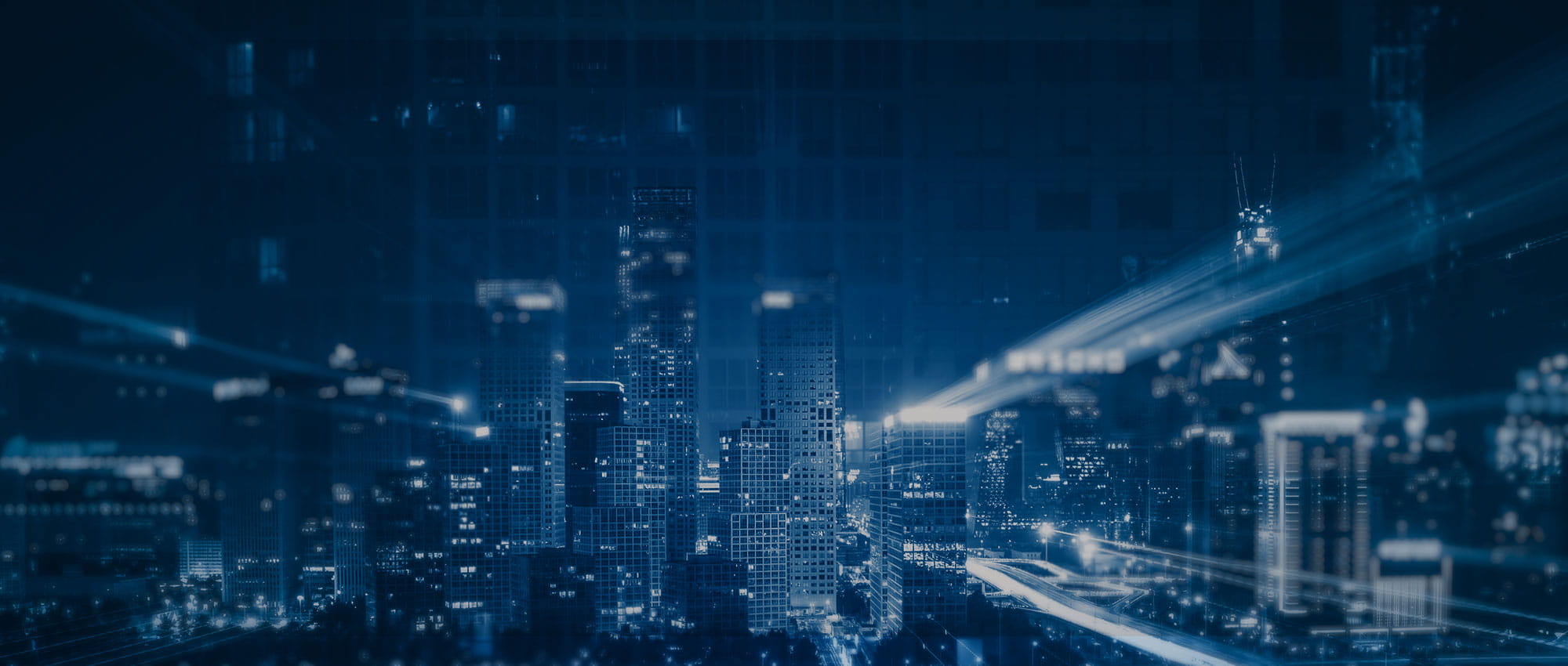
Join Us!
Experience Freudenberg Sealing Technologies, its products and service offerings in text and videos, network with colleagues and stakeholders, and make valuable business contacts.
Connect on LinkedIn! open_in_new