Obtain news and background information about sealing technology, get in touch with innovative products – subscribe to the free e-mail newsletter.
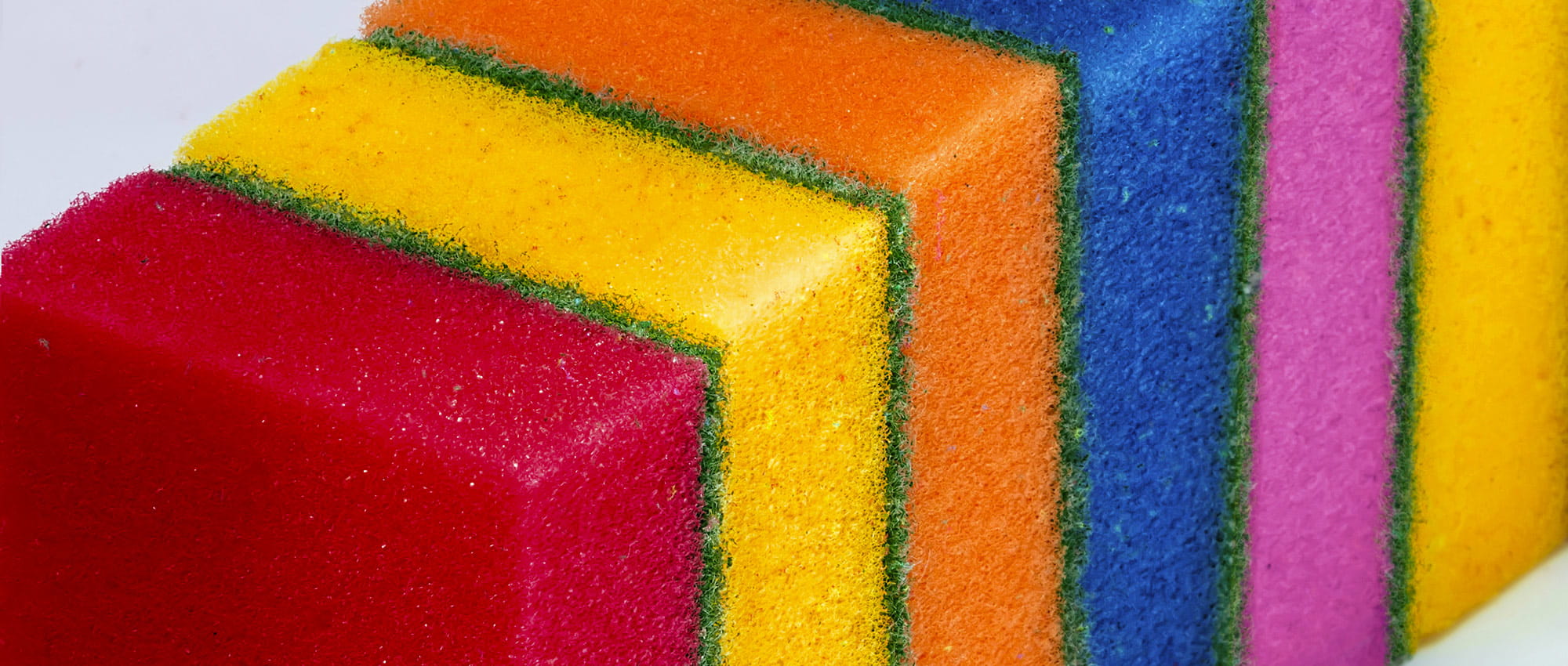
10.01.2023 | Story
Polymers
They are in the packaging for our foods and in the paneling of our vehicles. In our daily life, we mainly interact with them as plastics. But polymers are so much more.
Polymers
Polymers also occur in nature and even in people, in the form of enzymes, hair or silk, for example. Even our genetic material, deoxyribonucleic acid, is a polymer. The first man-made fibers and plastics were made of natural fibers. Some have been in use for a very long time: rubber is a natural polymer still used in tire production, among other applications.
The name of the material reflects this. The syllables “poly” and “meros” are derived from ancient Greek and can be translated as “many” and “part.” The many parts are so-called monomers: molecules that react with one another and branch into long, chain-like macromolecules. The different macromolecular structures found in polymers have allowed scientists to bind polymers by families. For example, the molecular chains of materials grouped into the thermoset polymer family form a dense network that becomes hard and stable. In the elastomer family of polymers, which includes rubber, the molecular chains are less densely meshed, giving them their typical elastic properties. Thermoplastics polymers have molecular chains that resemble loose threads. Thermoplastics are solid at low temperatures but melt when heated and can be reshaped as needed. Thermosets and elastomers, on the other hand, are heat-resistant and do not melt. When further processed with additives, thermosets and elastomers develop new performance characteristics that can result in the creation of complex plastics, plastic fibers and even dyes or adhesives. In some cases, polymers even become additives themselves. In the cosmetics industry, for example, the hyaluronan polymer family includes hyaluronic acid, an eagerly sought after and proven defense against skin wrinkles.
Petroleum-based polymers are certainly less stable than other raw materials such as wood, iron or other metals. But they are lighter. In vehicle components, they cut down on overall weight and help reduce fuel consumption. Especially with the development of electric and hybrid powertrains, lightweight plastics are making it possible to meet ever more stringent environmental and safety requirements for the first time. The use of polymers in production also requires comparatively low energy inputs. But in an era of climate change, another issue has become important: Synthetic polymers like plastics and other elastomers can only be separated and recycled to a limited degree. The solution could involve using biological materials from renewable resources, such as plastics made of corn, or textiles made of spider silk. But biologically based materials often increase manufacturing costs, and thus, prices for consumers. And there is another environmental consideration as well: The longevity of synthetic polymers such as plastics has a positive effect on their ecological handprint. So, it is important to consider whether it is more sustainable to turn to synthetic materials that hold up well or to bio-based alternatives that may not last as long.
This article originally appeared in ESSENTIAL, Freudenberg Sealing Technologies’ corporate magazine that covers trends, industries and new ideas.
More news on the subject Technology & Innovation
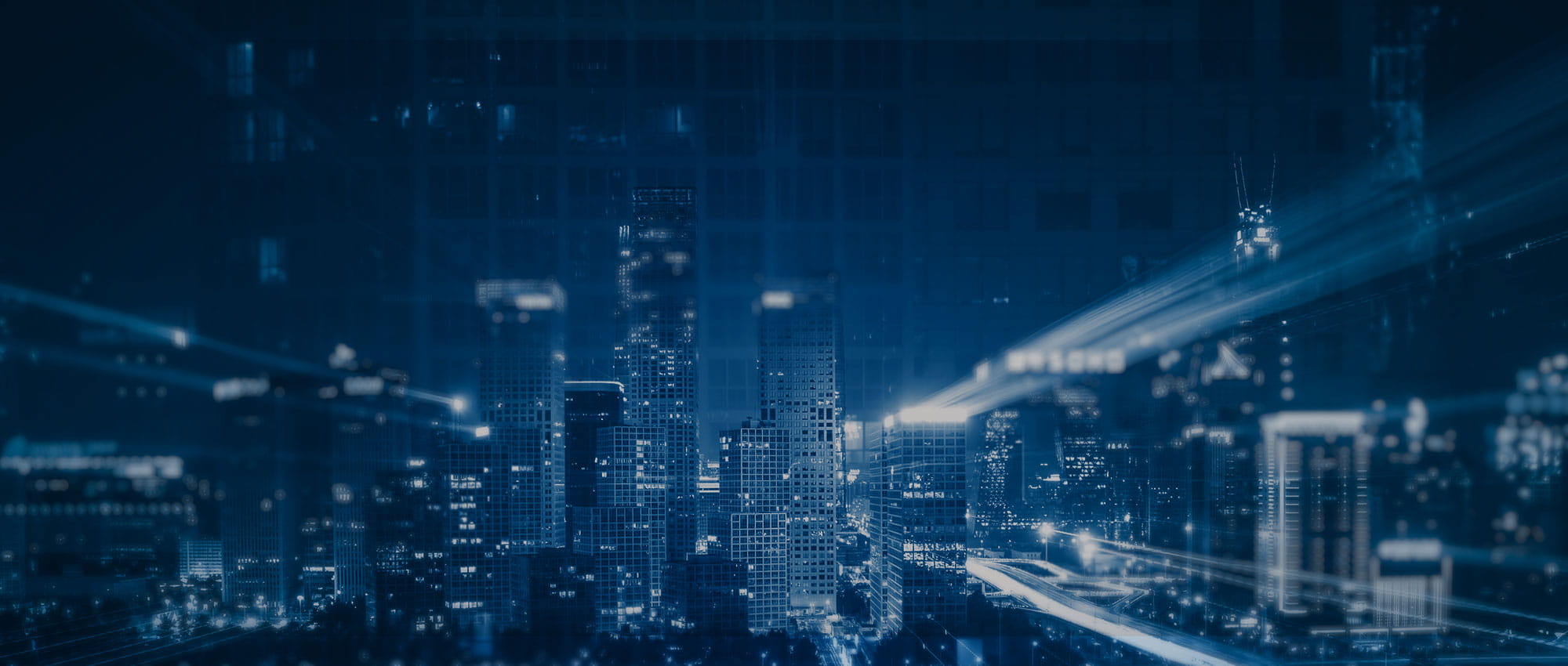
Join Us!
Experience Freudenberg Sealing Technologies, its products and service offerings in text and videos, network with colleagues and stakeholders, and make valuable business contacts.
Connect on LinkedIn! open_in_new