Obtain news and background information about sealing technology, get in touch with innovative products – subscribe to the free e-mail newsletter.
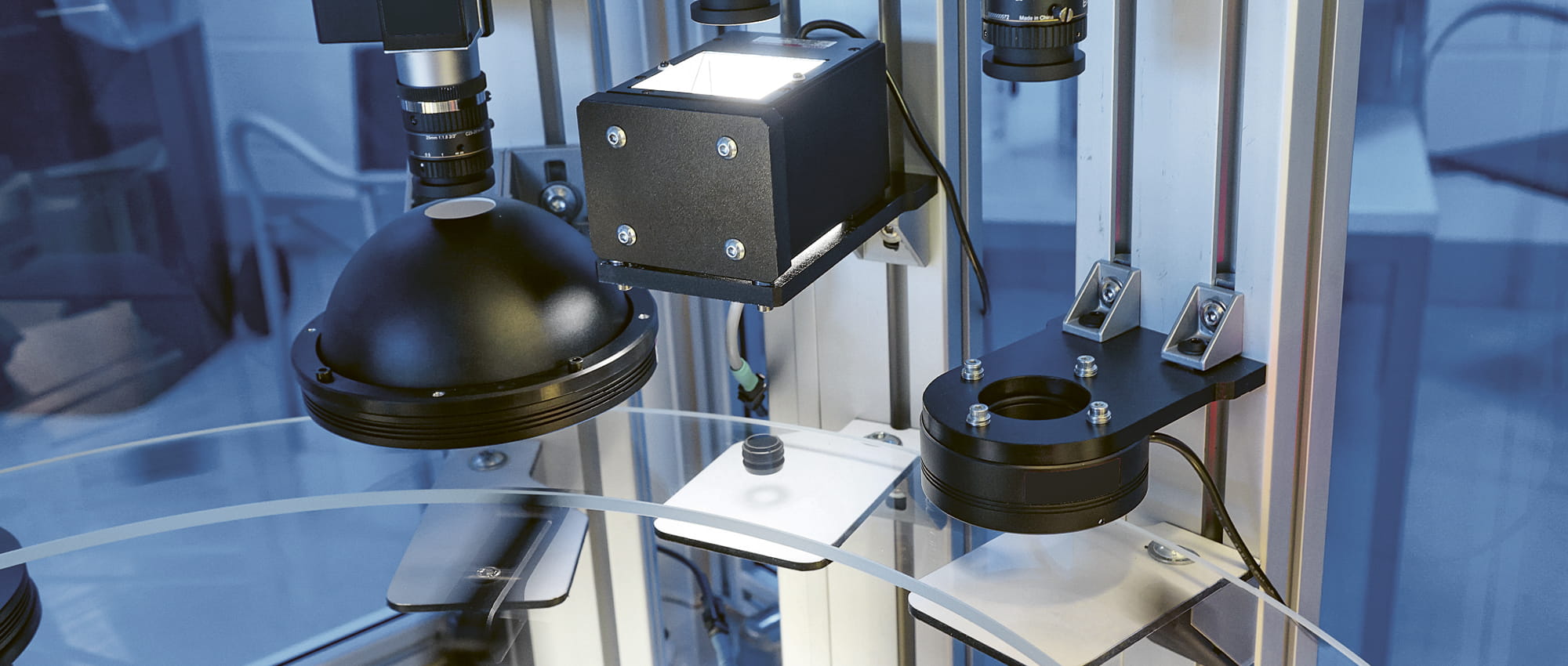
Greater Efficiency Thanks to AI
If a product is identified as flawed and discarded after final inspection, and it’s not even defective, that has an impact on costs – and, in lean terms, qualifies as waste. With the help of AI, Freudenberg Sealing Technologies is significantly reducing its pseudo-scrap rate.
It goes without saying that products leaving Freudenberg Sealing Technologies plants must function flawlessly. Aside from smooth-running manufacturing operations, it takes reliable quality control to guarantee high performance. But ostensibly defective products may be rejected even though they are actually problem-free. To reduce the scrapping of these parts, the seal maker is turning to the use of artificial intelligence in automatic visual inspection at some plants. The results are gratifying, according to Dr. Stefan Geiss, Vice President, Process Technology. “The use of AI in our final inspections helped us reduce pseudo-scrap by 50 percent, leading to a decline in total scrap,” he says. “That translates into fewer wasted resources.”
This shows that automatic visual inspection can be significantly optimized by using AI. “Thanks to the adaptation, we can more easily discover whether the rejected product actually deviates from the norm, or whether a shadow has produced a false result,” says Senior Engineering Specialist Dr. Helmut Hamfeld. “AI allows us to better differentiate between subtle differences.” Here it was in Freudenberg Sealing Technologies’ best interest to harness the added value of artificial intelligence.
Building an In-House AI Expert Team
Five years ago, the company began to build up its own AI resources by forming an advanced analytics team. One of its first tasks was to tackle the implementation of artificial intelligence in final inspections. The team worked on a pilot project at the Oberwihl plant in southern Germany in close cooperation with an expert group on site. This collaboration is crucial for the successful introduction of AI. Dr. Steffen Wissmann wrote the algorithm that makes sure that less pseudo-scrap is generated. “To start with, the basic decision was the choice of a suitable AI model that could be easily integrated into our processes. Then it was a matter of working with the expert group and carrying their requirements into the algorithm,” he says.
Thanks to AI, we have improved our ability to detect whether a rejected part actually shows a deviation from the norm.
Dr. Helmut Hamfeld, Senior Engineering Specialist, Freudenberg Sealing Technologies
The classification of the image material – which shows what a good or a bad part is – took place in Oberwihl. This type of data set is the basis for training AI and is essential to its performance and improvements in final inspections. Each participant learned something from the introduction of the system. Wissmann summed up the lessons learned: “We noticed that it can be a disadvantage when a specific product is evaluated as good or defective by different people. Inconsistencies in the data can result, and AI ultimately doesn’t know what to do with them. So, we are proposing that the complete data set used for training AI be based on the judgment of a single competent person.” In the end, a simple set of rules resulted from these experiences. They include the rule that people should not change parameters on their own. This is important during normal operations, and even more crucial when AI is involved. The AI solution is now being used at two additional plants.
Identifying Errors When They Appear
At its North Shields facility in northern England, Freudenberg Sealing Technologies has adopted another AI-optimized, automatic visual inspection system. But in this case, it involves a molding machine during the production process. The system recognizes whether the mold or the cavity into which the sealing material is pressed is free or still occupied. When an alarm quickly sounds, the part still in the mold can be removed quickly. “We are identifying errors as they come up and not at the very end of the production chain,” Hamfeld explained. “This leads to less mold damage, and we were able to reduce the need for replacement parts. Moreover, we are reducing machine downtime significantly. For one thing, because errors can be rectified quickly, and for another, because there is less damage to repair.” Another positive side effect is that production processes can be accelerated. Thanks to the latest experience, the system is due to be introduced at plants in Spain, Mexico, and Turkey.
Freudenberg Sealing Technologies has developed extensive experience and expertise in the use of AI in automatic visual inspection. The company is now turning to machine controls to test another AI application. This involves the use of up to 3,500 measuring points and sensors to capture the heating time or pressure conditions in seal production processes. If the data is within a range that does not guarantee a good result, there is an immediate prompt to adjust the parameters. It will take some time to implement the process. But it would be a step toward reaching a desirable goal: a zero-error, automated process chain that would make final quality inspections unnecessary.
Less Pseudo-Scrap, More Sustainability
“We are aware that we now can solve a great many problems with AI that we were unable to solve before. But AI is not a silver bullet,” Hamfeld says. “We are still seeing that our engineers have such specialized knowledge that we are unable to configure it into an AI application.” Gaining an understanding of how AI makes its decisions continues to be a challenge as well. But the advanced analytics team and AI expert Wissmann are making progress in this area. “We are now using algorithms that allow us to check the correlation underlying AI with regard to causality,” he says. In any case, the advantages of AI use at Freudenberg Sealing Technologies are uncontested, as Geiss points out: “We are gradually moving toward sustainable production thanks to AI. We are producing less pseudo-scrap and discarding less material as a result. This is improving our CO2 footprint. That’s also impressive.”
This article originally appeared in ESSENTIAL, Freudenberg Sealing Technologies’ corporate magazine that covers trends, industries and new ideas. To read more stories like this, click here.
More Stories About Digitalization
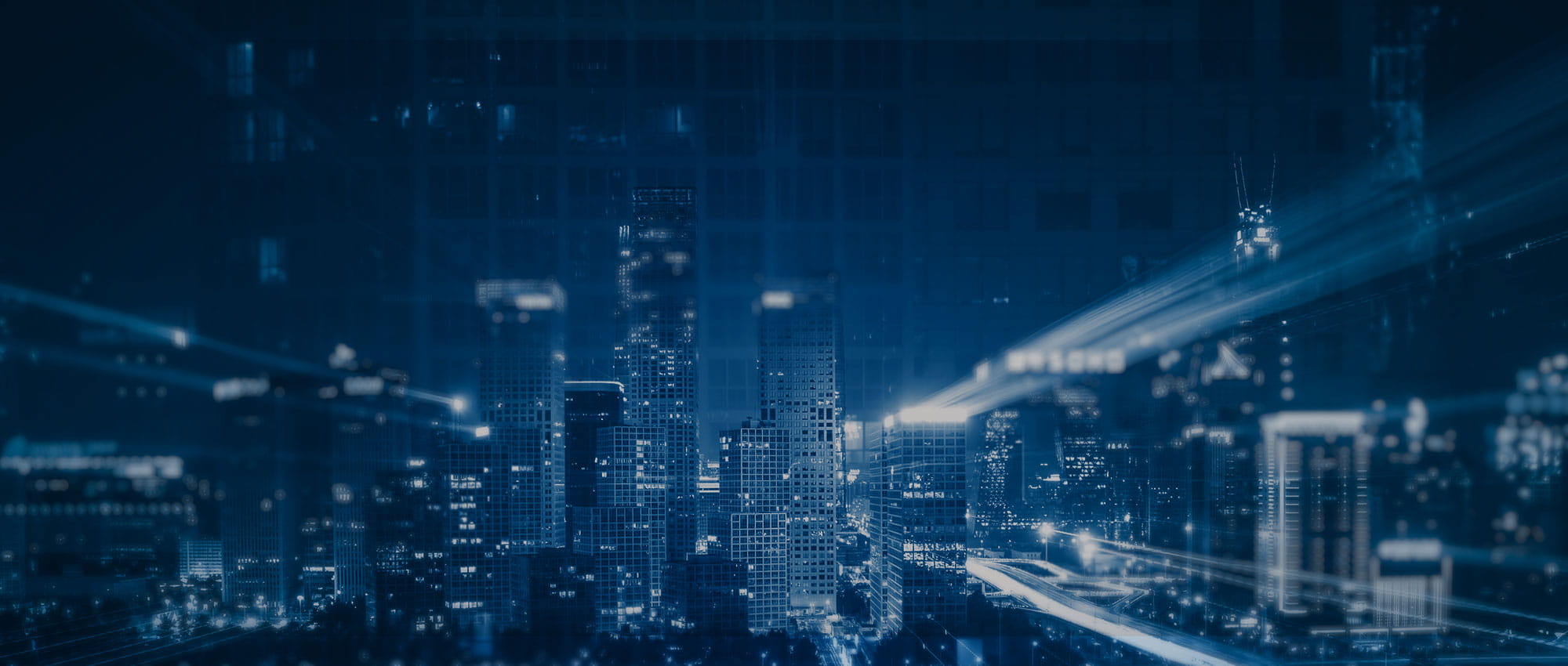
Join Us!
Experience Freudenberg Sealing Technologies, its products and service offerings in text and videos, network with colleagues and stakeholders, and make valuable business contacts.
Connect on LinkedIn! open_in_new