Obtain news and background information about sealing technology, get in touch with innovative products – subscribe to the free e-mail newsletter.
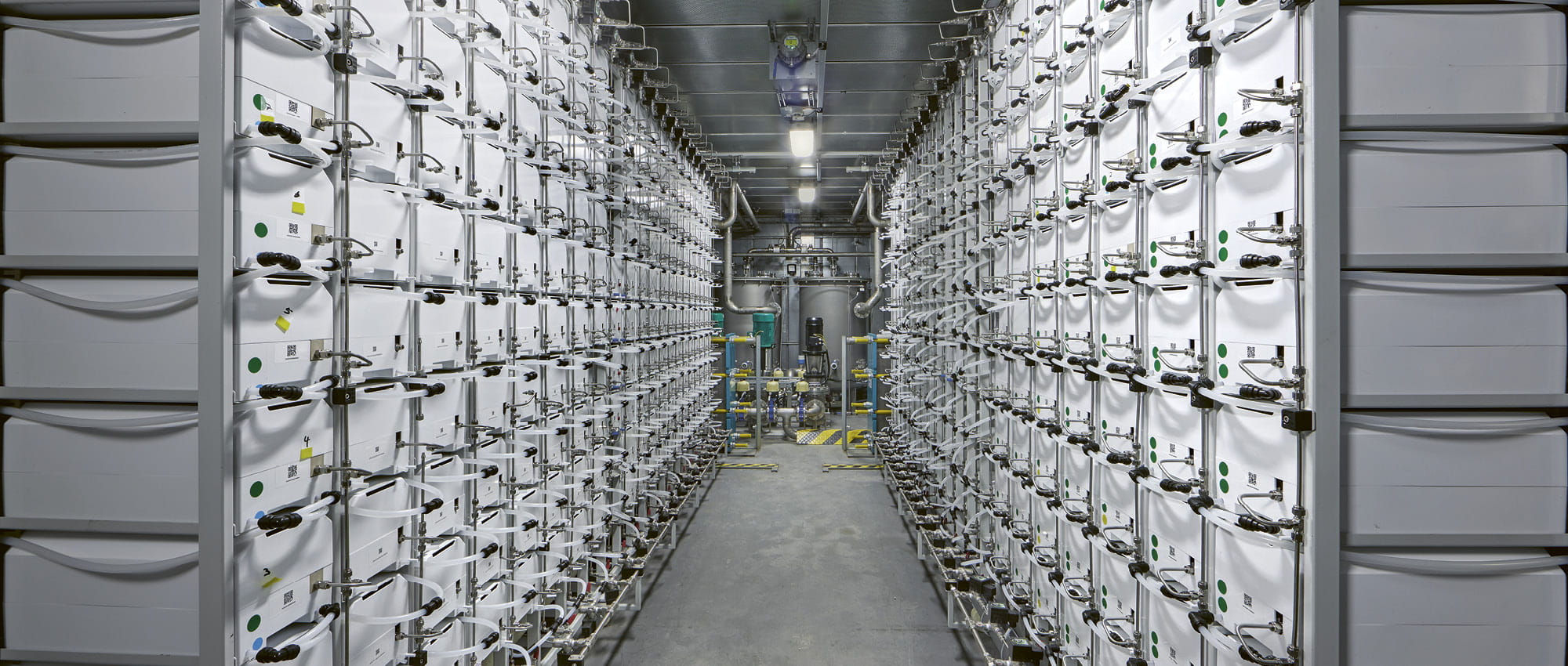
Electrolysis: Global Market Leader Uses Freudenberg Seals
A German-Italian company has developed a patented process to produce green hydrogen. Enapter AG has turned to flexible, easily scalable devices for its production. One key to success: seals from Freudenberg Sealing Technologies.
How does a company become a global market leader? For example, by refining a little-noticed electrolysis process and making it so attractive that companies and households feel it is perfect for them. That is what Enapter AG has achieved. The German-Italian company manufactures systems using anion exchange membrane electrolysis (AEM). Until now, the process has been a minor player in the global electrolysis mix. Enapter is changing that, and co-founder Jan-Justus Schmidt is confident about its prospects. “Thanks to the flexibility of our AEM electrolysis, we can compete with the processes that have been in the lead until now.” They are the proton exchange membrane electrolysis (PEM) and traditional alkaline electrolysis (AEL) systems.
Without seals, there is no electrolysis.
Jan-Justus Schmidt, cofounder Enapter AG
The advantages are clear: PEM electrolyzers use expensive, rare precious metals like iridium. Enapter’s AEM stacks get by with less costly nickel and steel and still produce extremely pure hydrogen. Additional purification steps are unnecessary. Another plus is the comparatively simple construction of the Enapter systems. It permits modular planning and execution, which reduces development times for new stacks. AEM electrolyzers have advantages over the AEL variety since AEL is suited for large facilities. By contrast, Enapter can fabricate small AEM modules at competitive costs, enabling it to develop new, attractive markets.
Modular solutions
The bottom line is that Enapter designs and builds high-performance systems at appealing prices. The systems are based on small 2.4 kilowatt modules that can be quickly assembled into larger configurations. This allows Enapter to adapt electrolyzers to special needs. The company also offers standard sizes. One example is the 2.4 kilowatt electrolyzer’s single-core solution. The other possibilities are two-multicore systems: Enapter’s AEM Flex 120, in which 50 of the 2.4 kilowatt stacks are installed, and the AEM Nexus megawatt solution, that has bundled 420 stacks into a container system. “This modularity makes our technology attractive and accessible to the hydrogen market,” Schmidt said. “It brings the energy transition to small and medium-size companies, and even for households.”
For example, the single-core electrolyzer, which is the size of a microwave oven, is suited for households looking for energy self-sufficiency. “The energy of the summer sun is collected as green hydrogen in a storage system and is used to generate heat in the winter,” Schmidt said. A medium-sized brick factory recently began using the AEM Flex 120. It allows the company to be more independent of natural gas when clinker bricks are burned – an energy intensive process. The Enapter electrolyzer transforms solar energy from the factory roof into green hydrogen and feeds it directly to the manufacturing operations. Since the cost of electricity in commercial electrolysis represents the largest share of the overall costs, renewable energy from a company’s own production system is the most economical option. Enapter’s megawatt electrolyzer is particularly well suited for hydrogen filling stations, among other uses.
Electrolysis seals
Various sealing solutions from Freudenberg Sealing Technologies are incorporated at a number of sealing points in Enapter AG’s electrolysis stacks. The opportunities emerged because the company offers a wide array of sealing solutions, from O-rings and gaskets to integrated 2K-component sealing products. The company’s sealing experts can customize the design and materials of the seals especially for environmental conditions prevailing in electrolysis applications. The goal is to keep the electrolytic liquid, oxygen and hydrogen in their prescribed locations.
Expertise in materials, design and processes:
-
Integrated sealing solutions
seal fastened to a plastic frame or bipolar plate
-
O-rings and gaskets
from rapid prototyping to large-scale production
Energy Transition for Industry and Commerce
Enapter products give companies easy access to the hydrogen economy. “They don’t even need to make a major investment to get started. They can get involved with our solutions and expand over time,” Schmidt said. “Customers who initially acquired smaller systems are turning to our megawatt solution today. And due to industry’s demand for green hydrogen, our megawatt solution is in greater demand than it was just a few years ago.” In the meantime, Enapter’s AEM electrolyzers have reached more than 1.5 million operating hours worldwide. That makes the company the world leader in AEM electrolysis. Software monitors the systems to guarantee safety and reliability. Additionally, the data collected allows for further development of the systems. Established electrolyzer manufacturers are also embracing AEM electrolysis in the pre-commercial sector. Schmidt considers it a positive sign that the competition recognizes the potential of the AEM technology.
Enapter is turning to a tried-and-tested partner strategy to expand in two dynamic, fast-growing markets: North America and the Far East. Enapter trains and certifies partners who sell AEM electrolyzers as components of an overall system. In China, Enapter has even entered into a joint venture with Wolong. The company is one of the world’s three largest manufacturers of electric motors. Schmidt hopes the collaboration will quickly facilitate market access for its AEM electrolyzers.
Demand for High-Level Sealing Expertise
But even a well-designed electrolyzer would be nothing without the many high-performing seals inside it. If just one fails, the result would be a loss in pressure that would damage the stack and interrupt hydrogen production. “Without seals, there is no electrolysis,” Schmidt said, zeroing in on a key issue. Enapter electrolyzers have incorporated seals from Freudenberg Sealing Technologies for several years, especially where quality and safety requirements are high. “We are reassured about our partnership by the outstanding mix of very high technical expertise and very good interpersonal interactions,” Schmidt said. “From the beginning, we worked extremely well together and developed solutions.” A mutual understanding of the hydrolysis technology has been the foundation for the collaboration over the years. Enapter sees the sealing technology company as a problem solver as it ramps up production with the help of integrated sealing solutions. “We don’t need to discuss the quality of the materials and process reliability at Freudenberg Sealing Technologies. They are both top-notch.”
In any case, Enapter sees itself as extremely well-equipped to promote growth in the hydrogen industry with its AEM systems. After all, Schmidt is sure that “the hydrogen economy is on the move worldwide. It won’t be stopped. And we are on board.”
This article originally appeared in ESSENTIAL, Freudenberg Sealing Technologies’ corporate magazine that covers trends, industries and new ideas. To read more stories like this, click here.
The Future Is Hydrogen
From H₂ Production to Usage: Comprehensive Insights on Production, Distribution, Storage, and Future Applications with Solutions. Explore full spectrum in our webspecial!
Hydrogen Webspecial open_in_newMore Stories About Technology
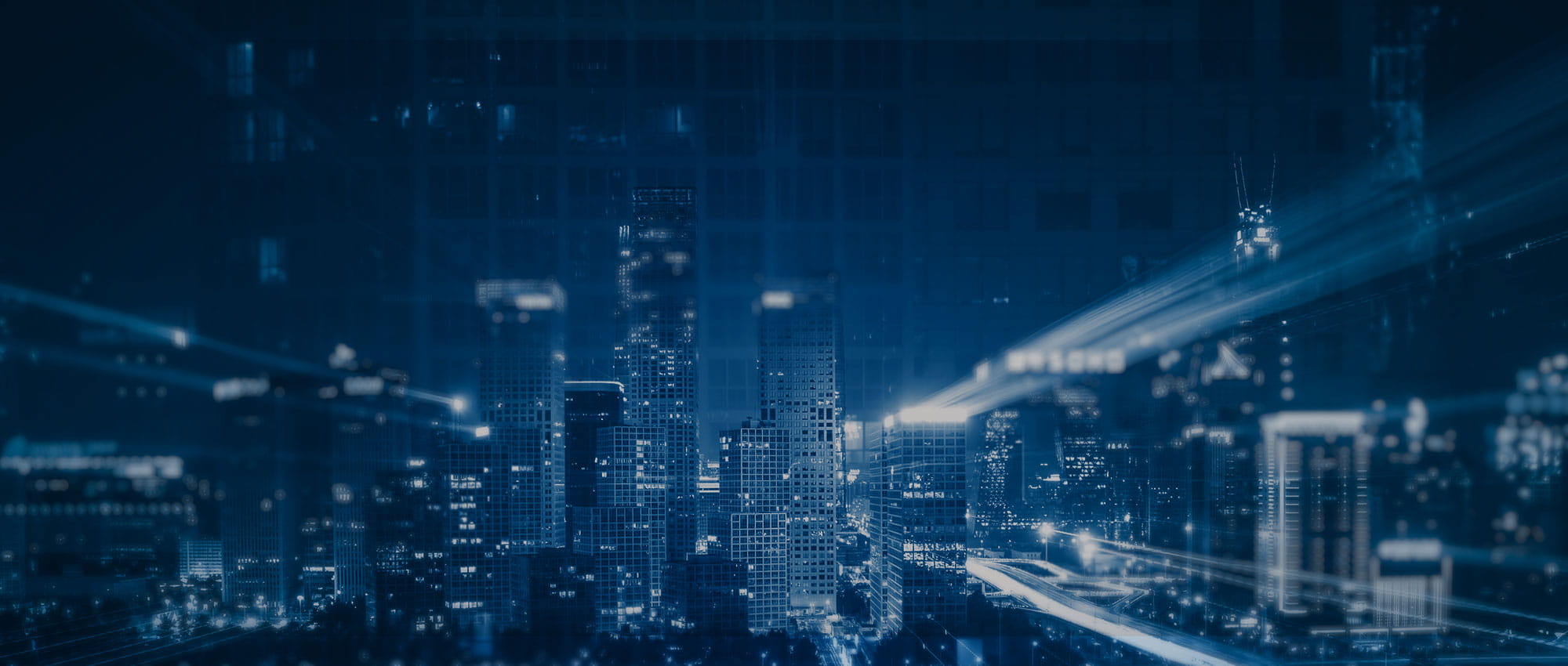
Join Us!
Experience Freudenberg Sealing Technologies, its products and service offerings in text and videos, network with colleagues and stakeholders, and make valuable business contacts.
Connect on LinkedIn! open_in_new