Obtain news and background information about sealing technology, get in touch with innovative products – subscribe to the free e-mail newsletter.
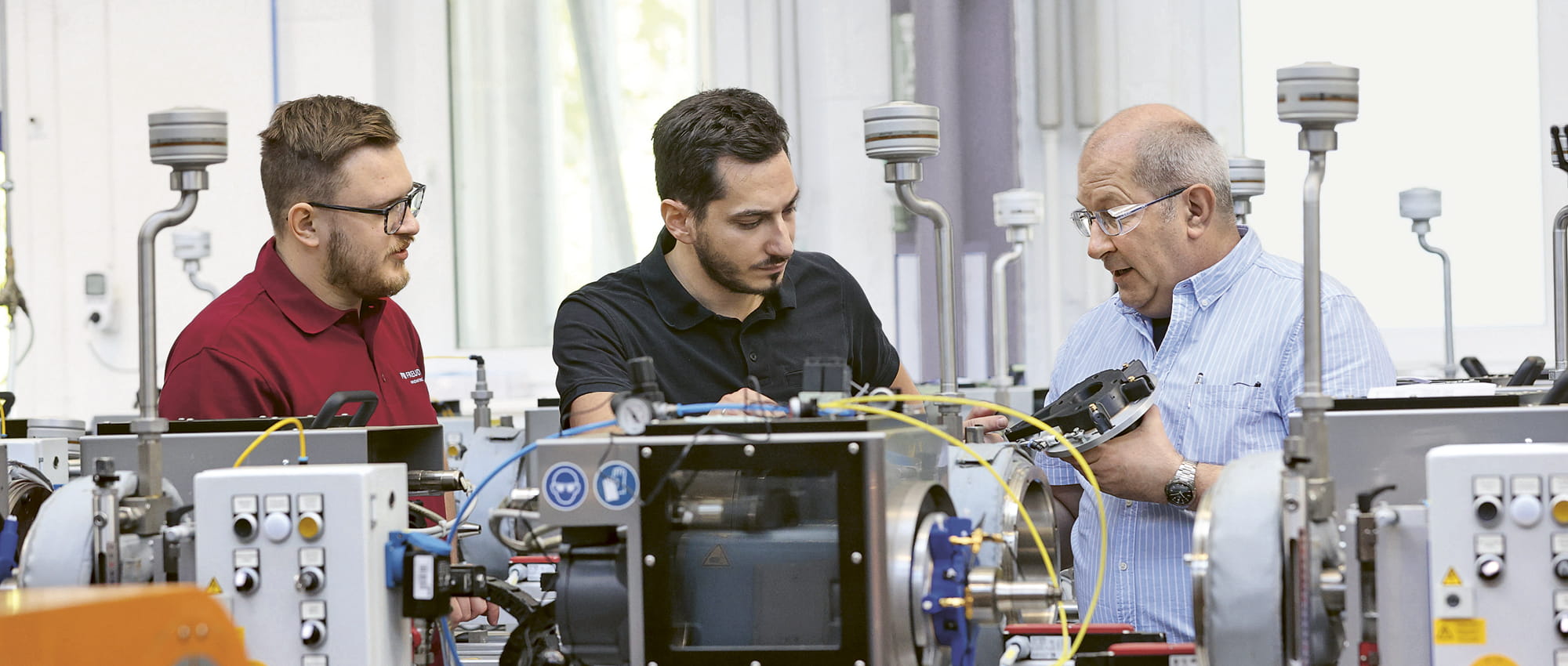
01.10.2024 | Story
Simulation on Test Stands
Before new seals and materials reach the market, they have to prove themselves in demanding tests. Freudenberg Sealing Technologies has turned to its own high-quality test stands to put them through their paces.
The first signs of trouble were the electric vehicle’s vibrations while it was being driven. Loud noises from the motor added to the impression that something was wrong. A French vehicle maker suddenly noted the problems in one of its models in 2015. But what was their source? “Electro-erosion was to blame,” explained Stefan Morgenstern, an advanced developer at Freudenberg Sealing Technologies. “After a few years, it had damaged the bearing in the electric motor, and vibration and noise were inevitable.” Due to the voltage buildup in the electric powertrain during driving, innumerable tiny sparks flew back and forth between the balls of the ball bearings and the rolling surfaces. At some point, the surfaces of the bearings abused in this way were no longer smooth – they were grooved. A motor failure was on the horizon.
Simulations of Artic and Desert Travel
In any case, eCON shows that it is not just important to have high-quality test stands. It is also crucial to set the specifications with the right objectives and expertise. At its headquarters in Weinheim, Freudenberg Sealing Technologies has a testing center with a wide range of test stands. “With their help, we are trying to come as close as possible to real life,” said Manager Robert Leins. “For example, for our Simmerring® tests, we can simulate water crossings and drives through the Arctic and deserts.
Freudenberg Sealing Technologies can reproduce a range of different conditions in engines, wheel bearings and other applications, allowing it to demonstrate its own innovations’ performance and efficiency. Leins and his staff also perform tests for manufacturers of machines, vehicles and oils after they set the specifications for them. This cuts down on testing in real life. “In the end, it is more practical to run tests on test stands than to wait until a wheel bearing has racked up 300,000 kilometers (186,000 miles),” Leins said. “On our test stands, we work with higher rotational speeds, pressures and temperatures than you find in real life. When the materials and systems withstand the stress tests, you can assume that they will achieve a certain operating life in practice.” The tests shorten the time frame to produce reliable results significantly. And if adjustments are needed, they can be made more quickly.
Like a time lapse sequence: A new Freudenberg test stand simulates how severely the challenging environment in electrolyzers attacks sealing materials. The apparatus consists of a 2-liter pressure chamber (1) 80 percent filled with a potassium hydroxide solution or sulfuric acid (2) and then heated. The chamber contains the material samples (3). Pure oxygen (4) is fed into the chamber at a pressure of 35 bar. Its gas bubbles (5) flow around the samples. Two sensors monitor the temperatures (6) and the speed (7) of the gas bubbles.
Eliminating Growing Pains in the First Place
All the test stands are basically freely programmable. The measurement data (rotational speed, torque, temperature of the media, and internal pressure) are automatically recorded and documented. “In the auto industry today, test stands play a key role in ensuring that new models with teething problems don’t make it out onto the road,” Leins said. “People were more lenient on this in the past. But now everything is put to the test in advance as much as possible. If our special test stands are included, we can produce rotational speeds up to 36,000 revolutions per minute, alternately rotating left and right. We can test seals with diameters of just a few millimeters all the way to 1 meter for their sealing performance. We can apply dust, mud and spraying water or oil to sealing systems. And when necessary, we can also simulate axial play – and do it at temperatures ranging from -40°C to 150°C (-40°F to 302°F).
Freudenberg Sealing Technologies works closely with a special machine manufacturer on the construction of its test stands. It produces the equipment based on precise specifications. The machinery is modified when new requirements make changes necessary. In some cases, Freudenberg Sealing Technologies handles the modifications on its own. “Today we hardly have a test stand that has remained in its original condition. It is essential for us to be able to add software and hardware to our computer-supported equipment,” Leins said. “Our test stands are putting us in a superb position as a company. Independent measurement labs are using comparable stands. In some ways, we are even trailblazers.”
Advanced Test Stand for Electrolyzer Materials
A test stand at the company’s facility in Plymouth, Michigan, is a good example. A a six-figure sum was spent on the equipment during the summer of 2022. It is used to painstakingly test the sealing materials used in electrolyzers, a key to the large-scale production of hydrogen. “In a few weeks with the help of a test stand, we can simulate how our materials will perform over years of constant use,” explained Dr. Alexander Hähnel, a materials specialist at Freudenberg Sealing Technologies. Whatever the conditions in different electrolyzers, this advanced test stand can simulate them and determine how the materials behave in an aggressive environment. A kind of time-lapse sequence, it makes it possible to see and measure how high temperatures in combination with a potassium hydroxide solution or sulfuric acid affect materials. Incidentally, they also have to withstand oxygen permeating them at high pressure. The results pave the way to more targeted advances in materials. The documentation from the test stand also benefits the manufacturers: They can use it to prove that the seals used in their electrolyzers are safe.
With test stands like those in Weinheim and Plymouth, Freudenberg Sealing Technologies sets itself apart from most other material manufacturers. And if a customer ever has a problem, simulations and extensive testing point the way to a solution.
This article originally appeared in ESSENTIAL, Freudenberg Sealing Technologies’ corporate magazine that covers trends, industries and new ideas.
More news on the subject Technology & Innovation
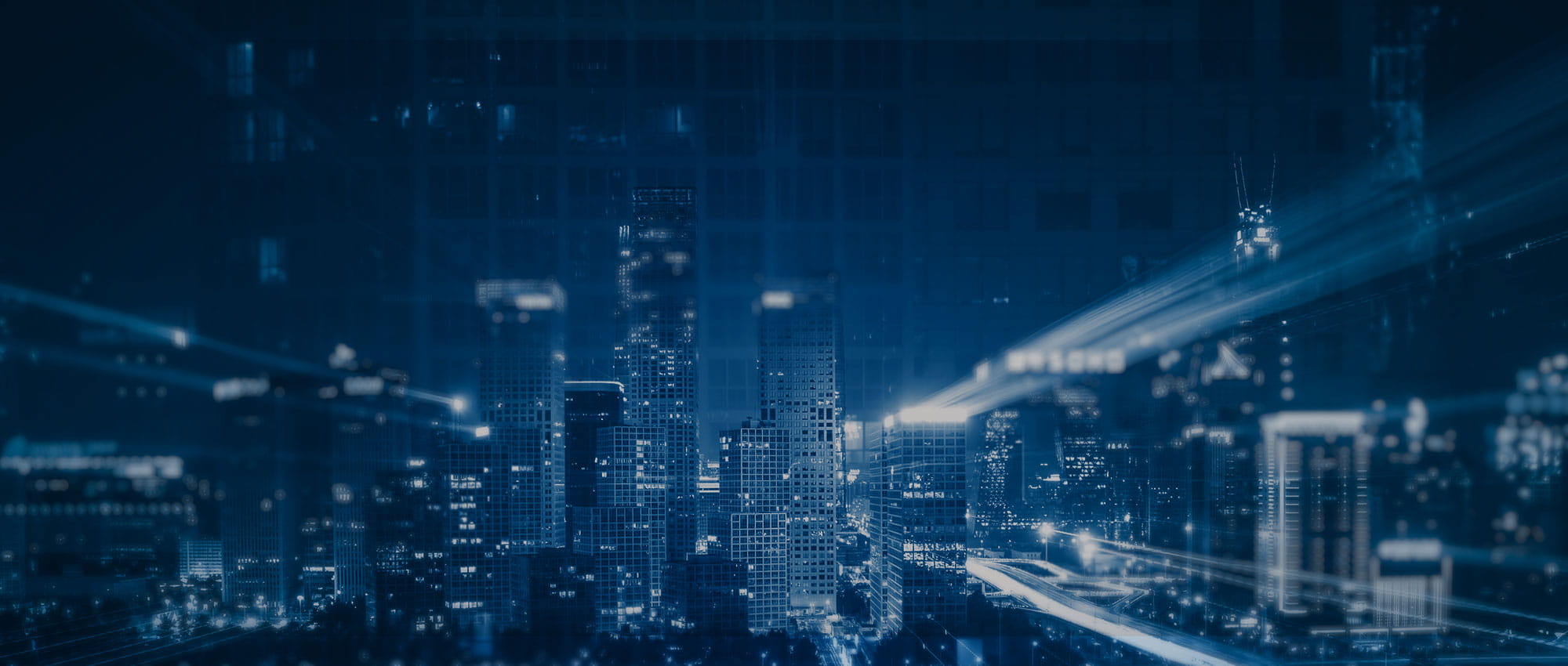
Join Us!
Experience Freudenberg Sealing Technologies, its products and service offerings in text and videos, network with colleagues and stakeholders, and make valuable business contacts.
Connect on LinkedIn! open_in_new