Obtain news and background information about sealing technology, get in touch with innovative products – subscribe to the free e-mail newsletter.
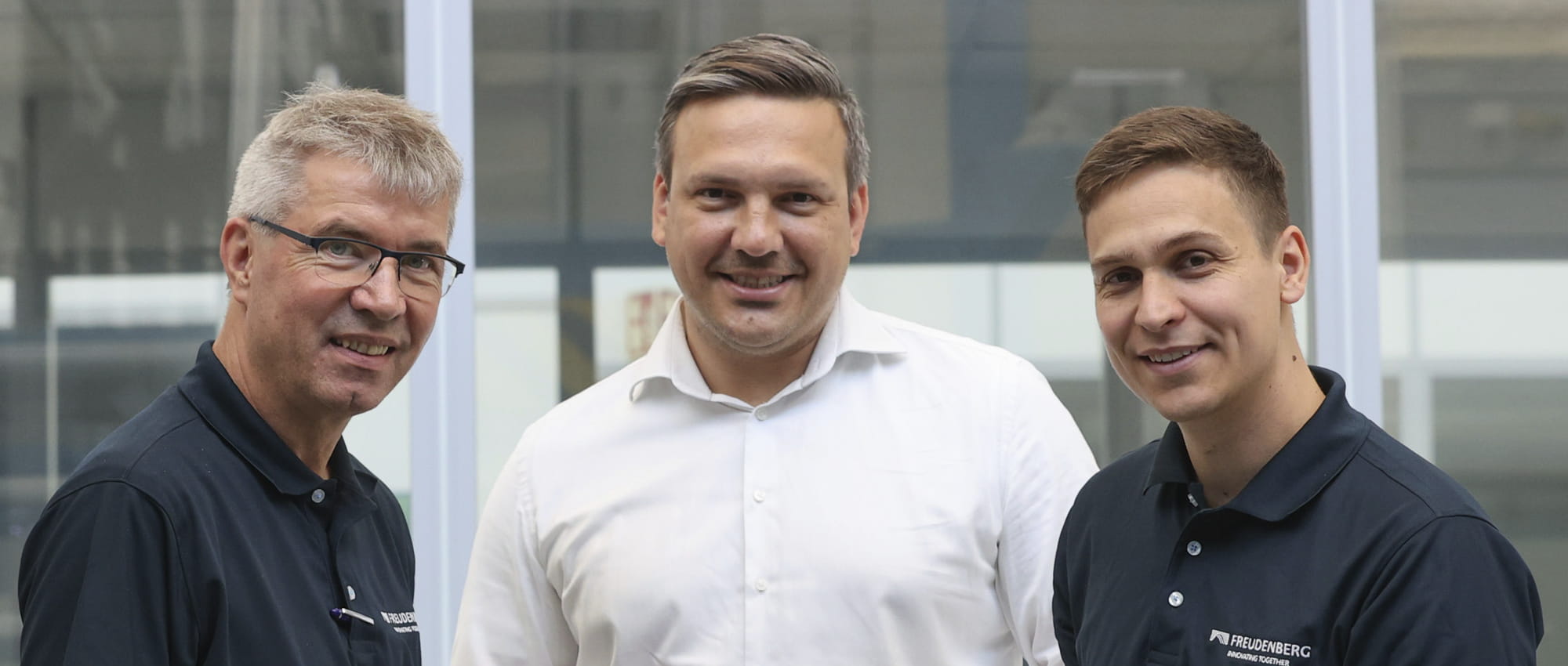
23.08.2022 | Story
“We Get the Most Out of It“
Hydrogen is both a source of energy and a means of storing it. In this era of energy transition, it is especially in demand. All the more if the electricity to produce the hydrogen comes from renewable sources. Freudenberg Sealing Technologies offers expertise and solutions supporting the rapid build-up of huge production capacity.
There is hardly an issue that preoccupies governments more right now than the question of energy production and supply. The desire to diversify the energy mix and embrace green energy sources is strong and widespread. To achieve this, more and more government officials and companies are turning to hydrogen. More than 20 countries have already adopted national hydrogen strategies. The European Union intends to provide additional funding and subsidies for these approaches, which are very promising. Freudenberg Sealing Technologies delivers high-performance seals for the production facilities and sees the hydrogen market’s dynamism. “In the last few months, some of our customers have indicated that they want to massively ramp-up their capacity. They would like to produce green hydrogen on a large scale today, rather than tomorrow,” said Artur Mähne, global Segment Manager, Hydrogen Technologies.
Good teamwork: Jürgen Emig, Artur Mähne and Dr. Alexander Hähnel (from left) at the Weinheim, Germany plant.
The Desire for Large-Scale Green Hydrogen Production
If the EU gets its wish, 10 million tons of green hydrogen will be produced in its member states in 2030. That will require a total production capacity of up to 100 gigawatts. That is a completely new order of magnitude. After all, the global capacity for green hydrogen is currently in the single-digit gigawatt range. Production facilities will have to be considerably larger to achieve this kind of expansion. Until recently, they provided about 1 megawatt on average, but giga factories will be in demand from now on. The production process for electrolyzers is a key factor for this growth since they are the core of the systems, breaking water down into oxygen and hydrogen. “The production of electrolyzers is a time-consuming process,” Mähne said. “So, we have to move from manufacturing to an industrialized process. That is the only way to boost production capacity into the gigawatt range, along with economies of scale to reduce costs.”
Today every electrolyzer manufacturer is working on semi-automatic or automatic production. Freudenberg Sealing Technologies can already offer sealing solutions for these processes. The seals are then applied to or injected onto a bipolar plate or a frame. The cells can be stacked, and systems produced, more quickly, and sources of error are minimized. “An electrolyzer is composed of several stacks consisting of numerous cells. It takes seals up to 1 meter (about 3.3 feet) in diameter to separate the cells from the environment and the hydrogen from the oxygen,” Mähne said.
Expertise in Materials and Processes Is Crucial
Every manufacturer of electrolyzers has its own requirements for seals, and Freudenberg Sealing Technologies provides solutions tailored to the company’s needs. “Thanks to our experience, we are able to recommend where and how our seals are best attached. When it comes to the design of the seal, it is helpful for us to be involved in the conception of the stacks,” emphasizes Freudenberg material specialist Dr. Alexander Hähnel. The sealing specialists offer yet another advantage: their considerable material expertise. “As the basis for application-specific material development, we can draw on more than 1,500 series mixtures. We can select from them when we design the seals, but we are also capable of implementing a new material at any time.”
It all comes down to the material. After all, the seals made from it have to function reliably and durably in an aggressive environment during electrolysis. Chemical resistance and the ability to withstand strong compressive deformation and high temperatures are in demand. These are characteristics that high-performance elastomers guarantee. “Our expertise in materials and processes makes us a valued partner to help our customers at critical points,” Mähne said. Meanwhile, nearly all the large electrolyzer manufacturers have turned to Freudenberg, and specific development projects have been launched. “We are getting plenty of positive feedback for our technical ideas,” Mähne said. Some recent feedback came from Siemens Energy, which is interested in optimizing its sealing concept and process steps. “As with all inquiries, we first held a workshop and discussed expectations and open questions in the dialogue. In a follow-up meeting, we presented proposals, which we then refined into a promising solution,” Mähne said. “In the process, it must be clear to the participants that they need to think in terms of months and not just a few weeks.”
Our expertise in materials and processes makes us a valued partner to help our customers at critical points.
Artur Mähne, global Segment Manager, Hydrogen Technologies
Various Types of Electrolysis With Major Market Opportunities
When sealing systems are designed, it should be noted that the various kinds of electrolysis have different requirements. There are a number of technologies: PEM (proton exchange membrane), AEM (anion exchange membrane), AEL (alkaline electrolysis) and SOE (solid oxide electrolysis). Freudenberg's experts are convinced that each will end up with some market share. AEM electrolyzers are suited to individual households and municipalities. PEM electrolyzers play out their strengths alongside wind turbines, whose energy they store in a matter of seconds. AEL electrolyzers are in demand in large technical facilities. While PEM electrolyzers respond quickly and have to digest the electricity in seconds, AEL facilities are designed for continuous operation. In comparison with their PEM counterparts, AEL electrolyzers have lower investment costs (CAPEX) yet higher operating costs (OPEX).
“Since we expect strong demand for alkaline electrolyzers, we want to position ourselves properly for this technology,” Dr. Hähnel said. But the challenge is the potassium hydroxide solution that they use in combination with a constant feed of pure oxygen. The combination attacks rubber seals, decreasing their operating life. The seal also has to withstand a pressure of 35 bar and temperatures up to 150°C (302°F). But the sealing experts have a solution for this: “With a cleverly optimized seal design combined with the right material, we’re able to offer stable seals for this kind of electrolysis as well.” Thanks to its material expertise, Freudenberg stands out in the AEM and PEM market segments while scoring points with seal designs for AEL systems. Now its experts have begun to deal with SOE electrolyzers whose glass seals have to withstand temperatures as high as 800°C (1,472°F).
Unique Freudenberg Test Stand Provides Precise Aging Forecasts
The company‘s facility in Plymouth, Michigan underscores Freudenberg’s enormous electrolysis expertise. Over the last few months, it has developed a unique test stand with a six-digit investment. “Over just a few weeks, we can use it to simulate how our sealing materials would prove themselves over years of constant use,” Dr. Hähnel said. “To my knowledge, we are the only material producer with this kind of equipment.” At an accelerated pace, the test stand shows the interactive effect of high temperatures, potassium hydroxide or sulfuric acid, along with oxygen at high pressure, on individual materials. Dr. Hähnel highlights the advantages: “Our test stand makes it possible to simulate the application’s specific requirements. In this way, we determine how a specific environment affects our materials. Using the information, we can continue targeted development work and then establish the number of operating hours with effective sealing action. So, we get the most out of it.” Electrolyzer manufacturers can also use the test stand’s documentation to demonstrate the reliability of the seals that they install.
The test stand can also verify the lifespan of thermoplastic carrier materials. Their interplay with the rubber seals is crucial to the performance of the integrated solutions. “When the carrier material, bonding agent and rubber are perfectly matching with one another, the sealing function is optimized,” Dr. Hähnel said. “We always think these components together as combination. Our customers can earn advantage on our activities of developing tailormade thermoplastics materials. We streamline process steps and boost performance.”
In any case, the advanced test stand in Plymouth contributes to a holistic view on the suitable sealing solutions for each customer. “We offer all the key qualifications from a single source, including our seal designs, our expertise in processes and production, and the materials we have developed,” Dr. Hähnel summed up. “That gives us the crucial know-how to industrialize the manufacturing of electrolyzers,” added Mähne. "And additionally, we don't have just one production facility. We can switch to plants in various countries. As a major customer, we are reliably supplied by our suppliers and experience fewer raw material shortages as a result." Freudenberg is expanding its workforce in research and development and in sales. “We are making sure we can continue to meet the growing customer demand.”
More news on the subject Technology & Innovation
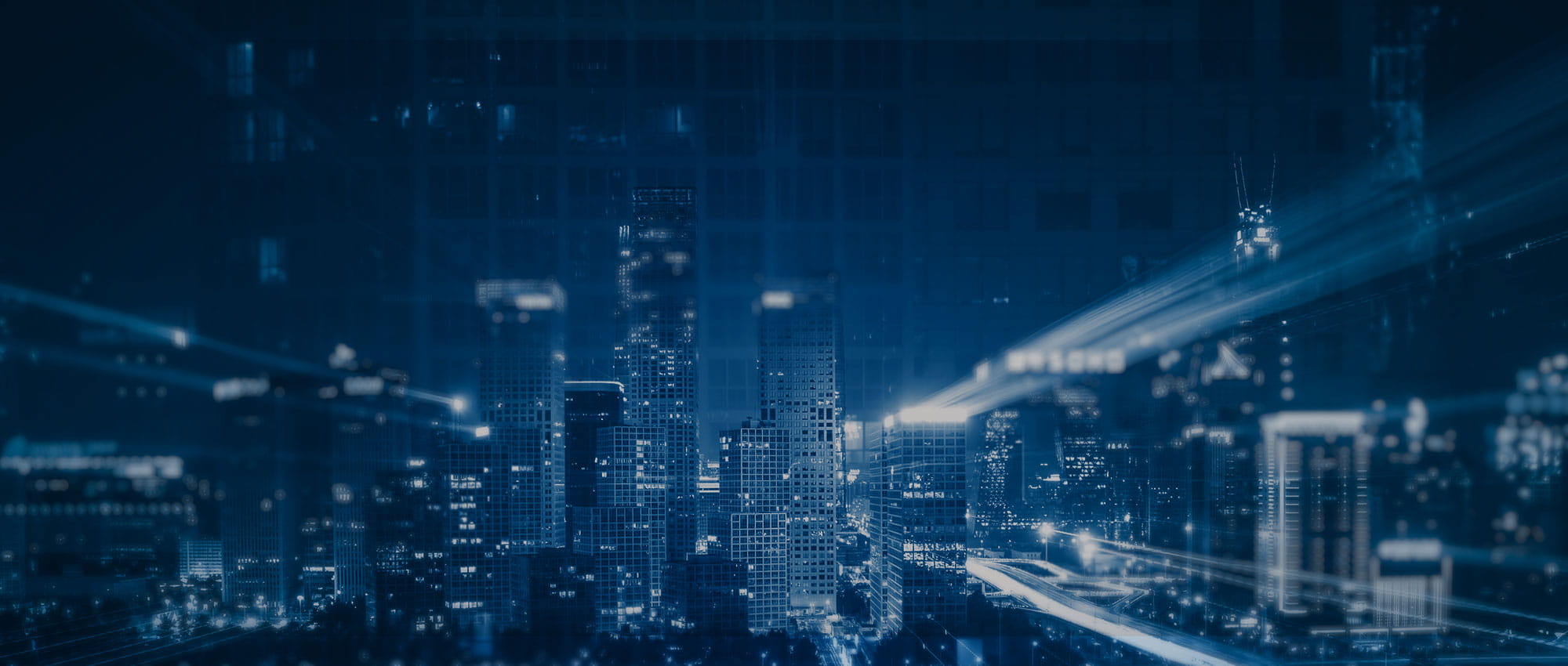
Join Us!
Experience Freudenberg Sealing Technologies, its products and service offerings in text and videos, network with colleagues and stakeholders, and make valuable business contacts.
Connect on LinkedIn! open_in_new