Obtain news and background information about sealing technology, get in touch with innovative products – subscribe to the free e-mail newsletter.
03.07.2018 | Press release
A Strong Connection
Weinheim (Germany), July 3, 2018. Selective Catalytic Reduction (SCR) emissions technology reduces the nitrogen oxide emissions of today’s diesel engines. Freudenberg Sealing Technologies has developed a new bonding agent to improve the precision and long-term stability of exhaust gas treatment systems. The technology gives designers new freedom in the configuration of these solutions.
The amount of nitrogen oxide in the exhaust of today’s diesel engines continues to decline. SCR catalytic converters are the main reason. They are in widespread use on commercial trucks and will be deployed in all new cars in the future.
SCR technology is designed to permit nitrogen oxide (NOx) reduction reactions to take place in an oxidizing atmosphere. It is called "selective" because it reduces levels of NOx using ammonia as a reductant within a catalyst system. Ammonia, which is generated onboard, reacts with nitrogen oxides to produce water and nitrogen as harmless byproducts. To provide the ammonia, cars equipped with an SCR catalytic converter have an auxiliary tank containing an aqueous urea solution known by the tradename AdBlue.
The solution is injected right before the catalytic converter. The dosing unit has to be extremely precise – it must guarantee that the right amount of the urea solution enters the exhaust gas system – and not a bit more – so the ammonia is transformed in its entirety. Otherwise, in the worst case, ammonia, a poison, would enter the environment.
The aqueous urea solution is harmless to humans. But the components of an SCR system must still be securely sealed to keep the dosing precise over long periods. This is critical in components responsible for controlling the volume: magnetic valves, valves, diaphragms and pump bodies.
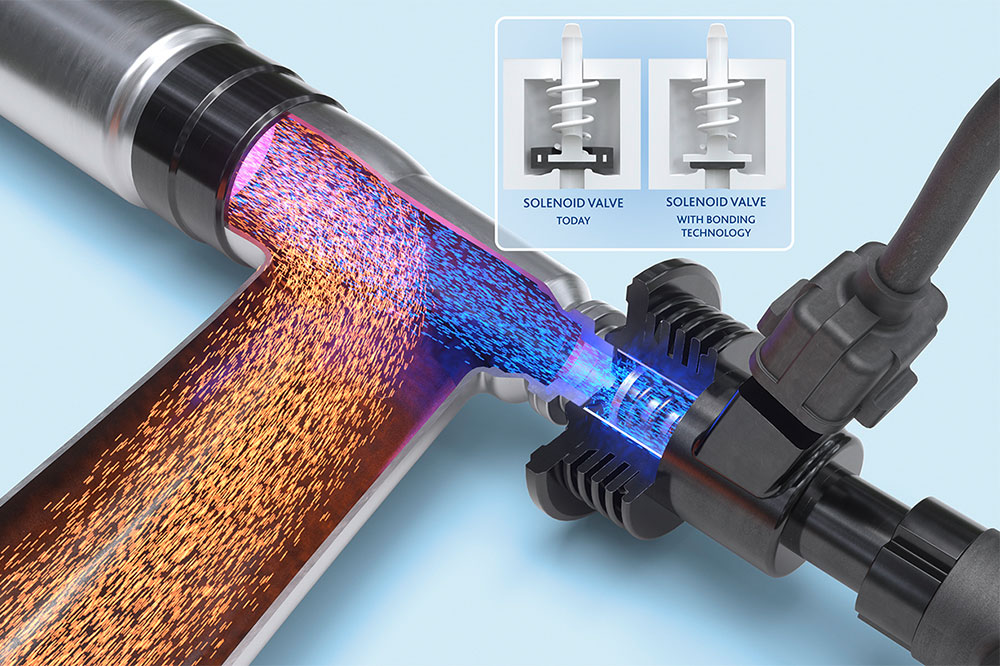
Freudenberg Sealing Technologies is already supplying several providers of SCR systems with seals made of Ethylene Propylene Diene Rubber (EPDM) and Hydrogenated Nitrile Rubber (HNBR). These materials that are stable over a long period of time. The technology is not just used in the armatures of magnetic valves or in diaphragm springs – it is employed in other components that come directly into contact with reducing agents as well. In addition, the seals in conveying units that conduct the urea solution from the tank to the dosing unit can benefit from the new binding agent technology. Until now, the sealing of these components posed a challenge: The edges of the contact surfaces between the seal and the carrier bodies of the components – which are mostly made of metal or plastic – have not been permitted to come in contact with AdBlue. The urea solution would have attacked the bond, which would have led to the detachment of the seal over time. Until now, the developers of SCR dosing units have managed the situation by avoiding all contact with AdBlue at the seam.
Freudenberg’s new bonding agent has proven extremely resistant to the urea solution in laboratory testing. For example, testing on material samples showed that the adhesion was totally intact after immersion in AdBlue for 168 hours at 85°C. Under identical test conditions, standard bonding agents lost their initial adhesion. Freudenberg experts have further expanded this testing to a valve tappet component. The tappet successfully withstood 1,000 hours of immersion in AdBlue at the same temperature.
“This is evidence that our new coating system enables more efficient and innovative sealing solutions,” said Boris Traber, who holds global responsibility for advanced materials development at Freudenberg Sealing Technologies. The new design freedom offers other advantages. The weight of switching components can be reduced. The lighter the components, the more rapid and exact the operation of the switches – and the more precise the dosing of the AdBlue. The new technology is not only being considered for the armatures of magnet valves and diaphragm applications but for components that come in direct contact with reducing agents as well. The seals in conveying units, which conduct the urea solution from the tank to the dosing unit, can benefit from the new binding agent technology.
“With this innovation, Freudenberg Sealing Technologies offers the developers of exhaust gas treatment processes much greater freedom in the configuration of components and systems and thus much more efficient and economical module design,” Traber said.
Ulrike Reich
Head of Media Relations & Internal Communications
Telephone: + 49 (0) 6201 960 5713
ulrike.reich@fst.com chevron_rightNews Service
You can subscribe to the Freudenberg Sealing Technologies news alert service, bringing you the news as soon as they are published. You can always unsubscribe from this service.
Subscribe now! chevron_rightMore news on the subject Technology & Innovation
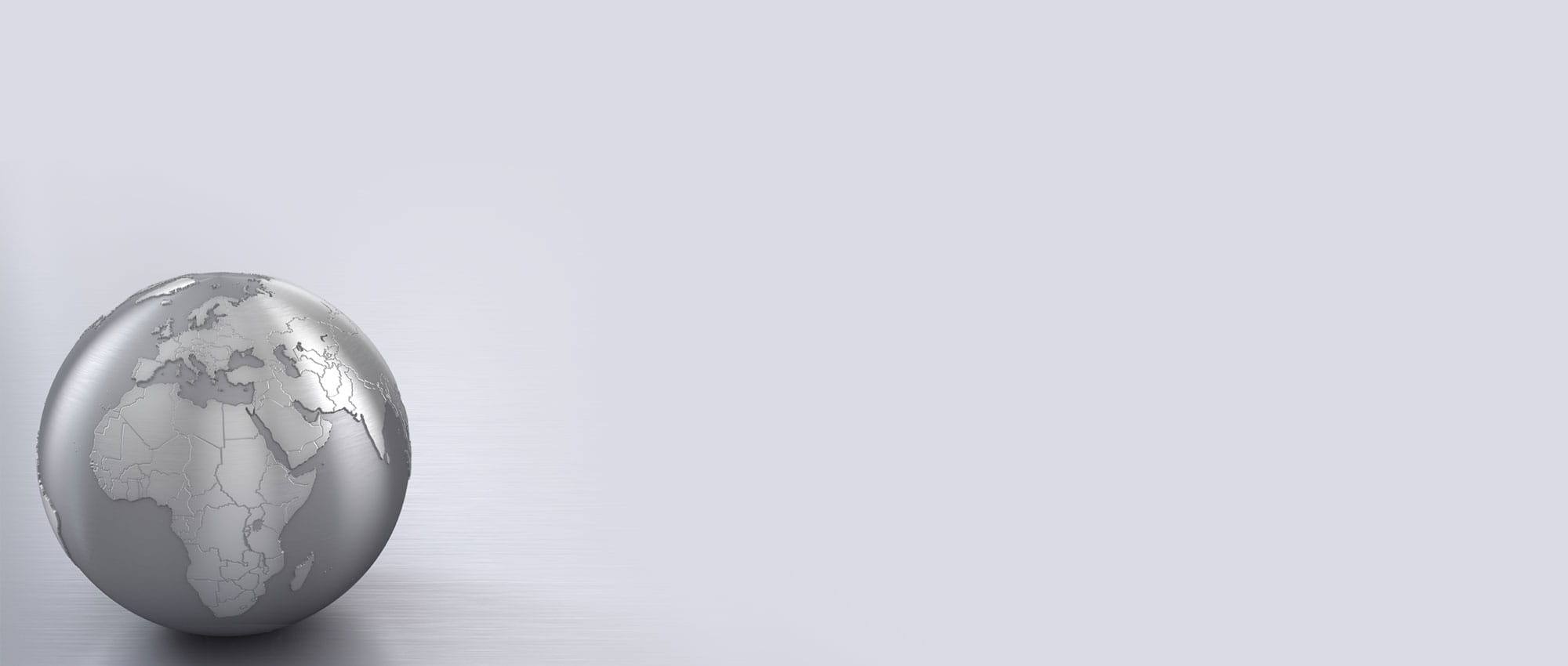
First Hand News
Best of all, keep up with the latest developments
with the Freudenberg Sealing Technologies newsletter.