Obtain news and background information about sealing technology, get in touch with innovative products – subscribe to the free e-mail newsletter.
20.11.2018 | Press release
Foldable and Fireproof
Weinheim (Germany), November 20, 2018. Automakers are building electric cars with increasing driving ranges. But the larger batteries and the higher energy density become, the more important it is for their seals to be reliable. Engineers at Freudenberg Sealing Technologies have developed several solutions to meet this challenge, and they are ready for series production.
Today’s electric cars are expected to travel 300 kilometers – and, better yet, up to 500 kilometers – on a single battery charge. This requires very large batteries, which are usually mounted in the vehicle’s underbody. Every battery housing has a cover so the entire battery need not be discarded if fairly small defects appear. Accessibility is indeed important for repairs, but no road spray can be allowed through the gap between the cover and the housing. Its ingress is blocked by a perimeter seal that ranges from two-and-a-half to five meters in length, depending on the size of the housing. But the seal has even more to do than keep out contaminants. If there is a fire, it is expected to resist the flames over a relatively long period and help prevent the fire from spreading.
The battery seals for electric cars undergo flame-spread tests similar to those in use in the aviation industry. In these tests – which are harmonized with the U.S, standard UL 94 – a sample of a material is exposed to a flame at a defined temperature and then the speed of the fire’s spread is measured. The material is given a classification based on the speed. With the help of the aviation experts at its Tillsonburg facility in Canada. Freudenberg Sealing Technologies achieved “V0,” the highest classification, for one of its compounds. In the test, the flame completely died out in ten seconds.
The ability of a seal to resist a fire over the desired timeframe not only depends on the material chosen for the component – it is also related to whether the seal is properly mounted. For Freudenberg Sealing Technologies, that was incentive enough to develop a variety of different sealing solutions that completely precluded improper mounting. It was important to consider that electric cars will no longer be a niche product in the future. They will be built in ever-increasing volumes. That means the industry will increasingly need seals that robots can install fully automatically.
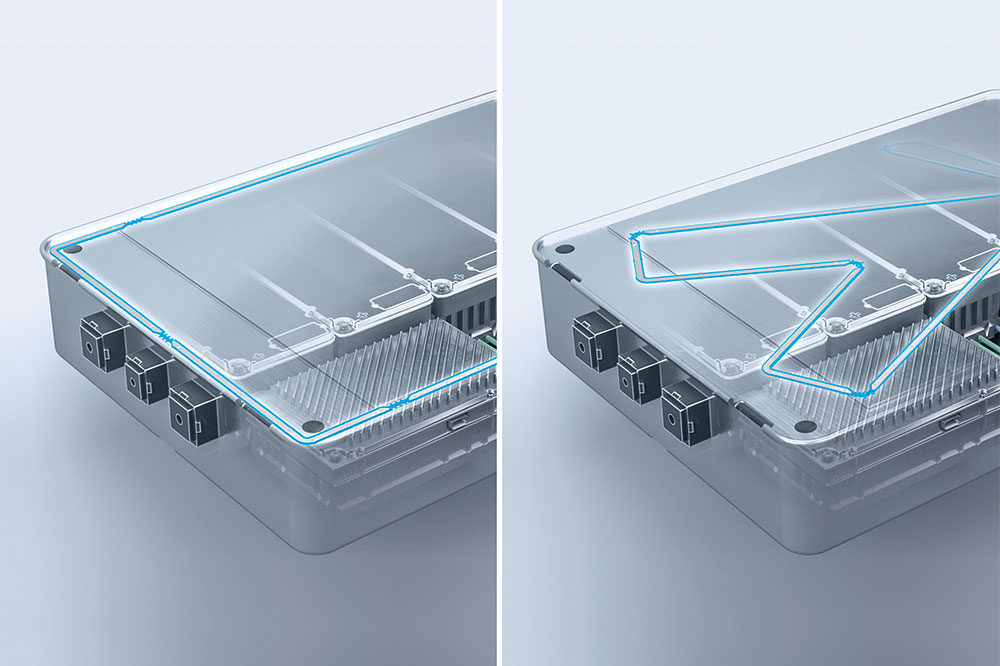
Freudenberg Sealing Technologies has developed a new solution – a foldable seal – that meets these requirements. Fixed aluminum elements equipped with a sealing profile on their outer edge not only provide stability – they integrate mounting points for the clips used to attach the seal at the housing cover. The elements are connected with one another using the continuous sealing profile, which exhibits high flexibility and can compensate for small dimensional deviations in the housing. Since the foldable seal is a complete component and does not need to be assembled from separate elements, the reliability of the installation rises dramatically. One key advantage of the approach: Metallic inlays ensure high electrical conductivity between the battery housing and its cover. This is important for the efficient screening of electromagnetic fields that result from the flow of current in the battery. Otherwise, the fields could disrupt other electronic components in the vehicle.
Freudenberg Sealing Technologies is pursuing other solutions for large batteries as well. For example, there is the possibility of manufacturing a continuous elastomer component. In this case, cast metallic bushings provide the stability and ensure electrical conductivity. The fastening elements are also cast, which promotes high installation reliability and makes defined location points possible. One employee can handle the mounting even on very large batteries.
Freudenberg Sealing Technologies has developed its own endurance tests so it can evaluate housing seals for traction batteries and verify that their operation is flawless. The process makes it possible to test the seals without using real housings since they are hard to handle due to their size. It uses a hydraulic ram with a frequency of up to 50 hertz to act on a sealed test housing consisting of two halves. This simulates the aerodynamic torsion that occurs in actual driving. A slight overpressure is continually maintained inside the housing so leaks are certain to be detected. The entire test setup is in a climate chamber so the impact of the temperature can be recorded.
“The electric car will prevail,” said Paul Hailey, Vice President of the Gasket Division at Freudenberg Sealing Technologies. “But manufacturing large batteries in high volumes is a major challenge for our customers. With our sealing solutions, we are going to help them master this.”
Ulrike Reich
Head of Media Relations & Internal Communications
Telephone: + 49 (0) 6201 960 5713
ulrike.reich@fst.com chevron_rightNews Service
You can subscribe to the Freudenberg Sealing Technologies news alert service, bringing you the news as soon as they are published. You can always unsubscribe from this service.
Subscribe now! chevron_rightMore news on the subject Technology & Innovation
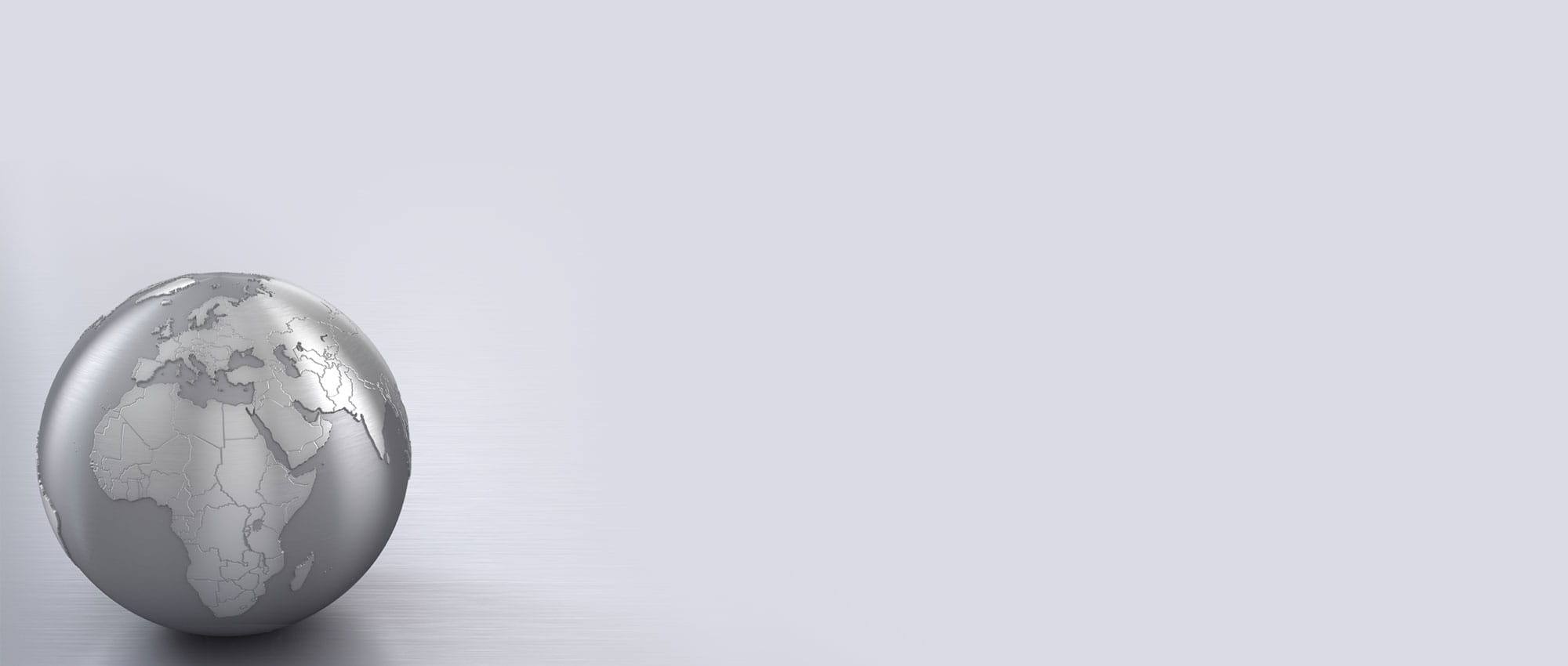
First Hand News
Best of all, keep up with the latest developments
with the Freudenberg Sealing Technologies newsletter.