Obtain news and background information about sealing technology, get in touch with innovative products – subscribe to the free e-mail newsletter.
09.10.2018
Seals for Compact Fuel Cells
The climate goals of the Paris Agreement can only be met if all forms of transportation are gradually electrified. Aside from the growing use of battery-electric powertrains, fuel cells are playing an increasingly important role in buses, heavy-duty commercial vehicles and construction machinery. Freudenberg Sealing Technologies estimates that the fuel cell will reach a global market share of 40 percent in mobile applications by 2050. The principle behind them: A fuel cell consumes hydrogen as its fuel, transforming its energy into electric current. The electricity drives an electric motor. This involves the migration of positively charged hydrogen protons from the anode through a thin polymer electrolyte membrane (PEM), which is coated with a catalytic material, to the cathode, where it reacts with oxygen to form water. This results in a surplus of electrons from the hydrogen at the anode. If they are connected to the cathode with a separate electric circuit, they will migrate there. This produces electrical energy.
The membranes for the gas exchange need to remain uncontaminated to extend the fuel cell’s operating life. The same is true of the bipolar plate that serves as the carrier for the individual elements of a fuel cell stack and handles the rough distribution of the gases. In addition, the gases must not escape into the environment and the hydrogen must not come into direct contact with the oxygen. This makes it essential to securely seal the gas diffusion layer. Freudenberg Sealing Technologies seals also serve another important purpose within the cell: They compensate for dimensional variations that may result from the expansion of adjacent components due to heat or other factors.
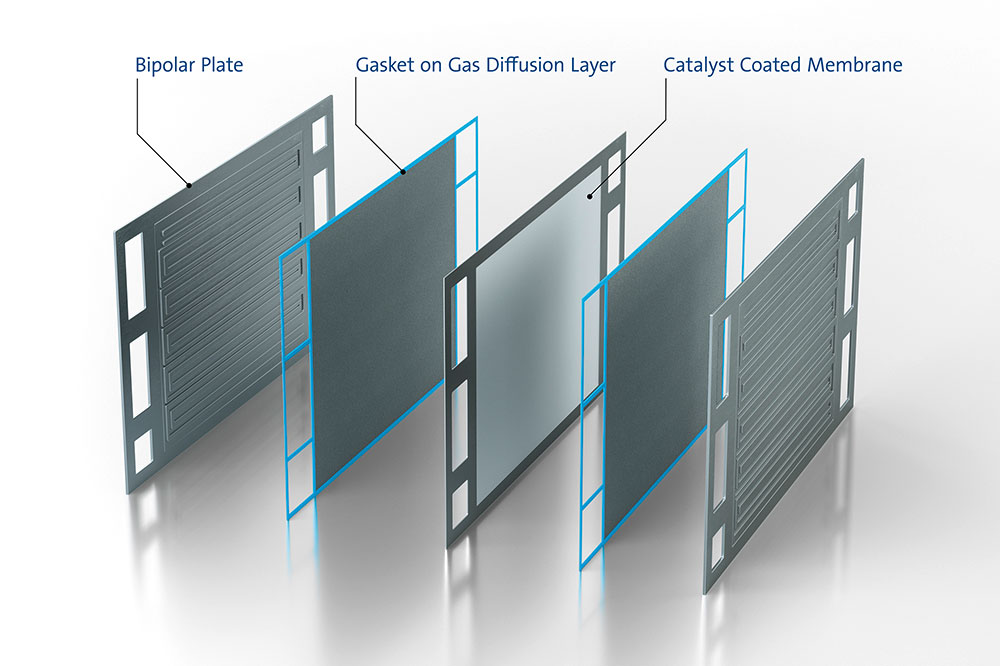
As part of a new Freudenberg Sealing Technologies sealing concept, an elastomer seal is applied directly onto the gas diffusion layers during the injection molding process. The layers handle the fine distribution of gases and other tasks such as the transport of heat and water on both sides of the polymer electrolyte membrane. The PEM forms a compact and secure sealing unit with the gas diffusion layer that it encloses. The unit can be attached between the bipolar plates of a fuel cell stack, which are responsible for the gross distribution of gases and the transport of electric current. The new concept permits thin components to be designed and eliminates the need for edge reinforcement, in the form of two polymer films, that would have otherwise had to be glued onto the membrane’s edges.
As the material for the new seal, Freudenberg Sealing Technologies turned to an elastomer especially developed for use in fuel cells. Among other characteristics, it needed to feature good resistance to heavy moisture, to temperatures from 80 to 90°C, coolants and acidic environments caused by the PEM’s electrolyte material. The elastomer must exhibit the lowest possible permeation so the reactive gases only diffuse minimally through the seal. The geometry of the seal fulfills two functions: first, it must securely enclose the PEM between the two gas diffusion layers. This is ensured by a seal edge applied directly to the border of the gas diffusion layer. Secondly, it must also seal the apertures in the bipolar plates where the supply channels of a fuel cell stack run and where the hydrogen, oxygen and coolant flow. The seal also features additional, outer seal lips for this purpose.
Since it is directly attached to the gas diffusion layer, the seal makes it easier to assemble fuel cell stacks. It is also a major advantage that both the gas diffusion layer and the seal come from the Freudenberg Group. It takes a precise understanding of the individual materials and the manufacturing process to produce the two components in an injection molding tool. For example, the tool must firmly enclose the installation space for the elastomer, yet it cannot be allowed to damage a gas diffusion layer, which is only a few tenths of a millimeter thick. Working with a German supplier of fuel cell modules, Freudenberg is now developing seals for gas diffusion layers and fuel cells to series-production readiness.
Ulrike Reich
Head of Media Relations & Internal Communications
Telephone: + 49 (0) 6201 960 5713
ulrike.reich@fst.com chevron_rightDownload Documents
News Service
You can subscribe to the Freudenberg Sealing Technologies news alert service, bringing you the news as soon as they are published. You can always unsubscribe from this service.
Subscribe now! chevron_rightFurther Articles With These Taggings
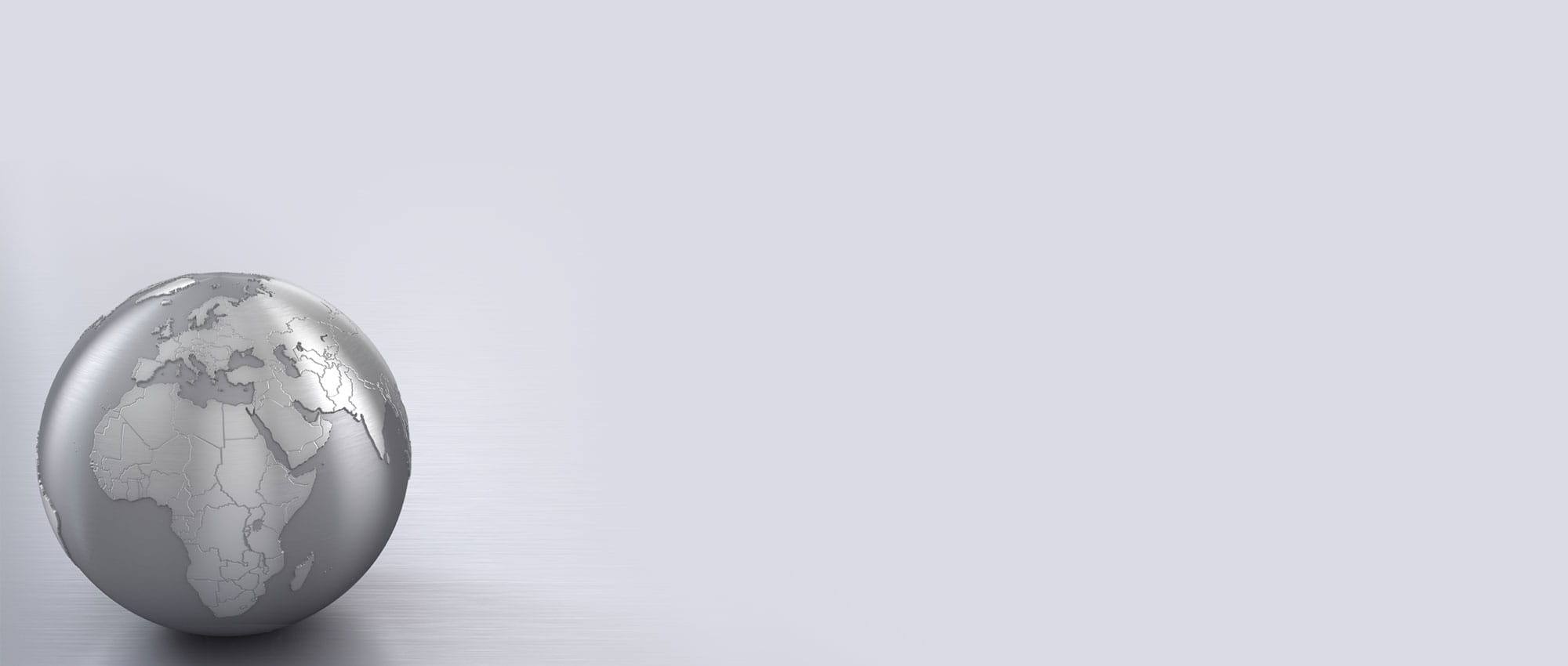
First Hand News
Best of all, keep up with the latest developments
with the Freudenberg Sealing Technologies newsletter.