Obtain news and background information about sealing technology, get in touch with innovative products – subscribe to the free e-mail newsletter.
02.06.2020
Clever Combination
Whether it’s to knead bread dough, mix a cake batter, puree soup ingredients or blend a smoothie, most people reach for an electric kitchen appliance to get the job done. The durability of the appliance depends largely on how well the seal at the outlet point of the drive shaft protects the interior from ingress of food residue or liquids. Seals made of high-quality elastomers or the polymer polytetrafluoroethylene (PTFE) combine low wear with excellent long-term resistance against leakage. In the past, a metal case was the best option available to maintain the integrity of the seal’s performance over a long period of time. Freudenberg Sealing Technologies has now succeeded in developing a modular sealing concept with a plastic case that meets the specific requirements for long-term performance as well as those made of metal. There are three major advantages to the new design: Significantly, in the price-sensitive, small appliance industry, the lower production costs associated with forming enclosures from plastic is an important consideration. In addition, Freudenberg's modular concept accommodates the integration of additional components, such as shaft bearings. Finally, because small appliance housings are typically made from plastic, fastening the seal case to the appliance housing is easier to achieve.
Modular design
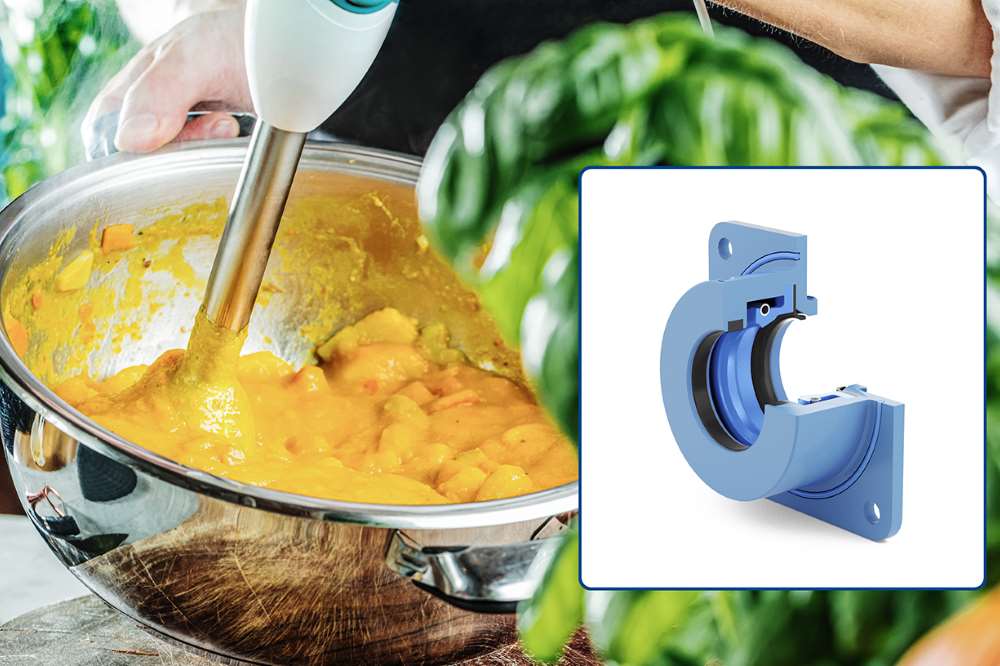
Freudenberg Sealing Technologies has developed a new, innovative sealing concept for small, electric household appliances. // Copyright: Freudenberg Sealing Technologies 2020
The basic idea that the engineers at Freudenberg came up with is quite simple: In the design, they decouple the plastic case, consisting of an inner and an outer ring, from the sealing ring. The case, an injection-molded part, can then be precisely matched to the installation requirements inside the device. This means there is no longer any need to take rotational symmetry into account. The case can be made of the same plastic used to mold the appliance housing, which insures the components will uniformly respond to various heat and pressure conditions when the appliance is in use. Depending on performance requirements, the seal itself can be made from a variety of advanced formulas found in Freudenberg’s material portfolio. For example, companies can request a standard or custom engineered seal design that can be made of elastomers with or without profile, with PTFE or a nonwoven, each made of different material compounds.
The seal is inserted into the outer portion of the case using a highly automated process at Freudenberg. If required, the caser can also accommodate other components such as bearings as part of the assembly process. The inner ring is then either clipped into place to form a positive connection, or the two rings are joined permanently by ultrasonic welding. The Freudenberg sealing experts are already working on another solution for the future, in which the sealing ring is directly over-molded with a thermoplastic.
Engineers based at Freudenberg’s Weinheim, Germany, headquarters campus performed extensive tests on the new design. Data shows that there is no degradation in seal performance ty at temperatures ranging from -25 to +90 degrees Celsius, the temperature range within which most small appliances operate.
"Compared to standard sealing solutions currently in use, we achieve better quality and performance at an attractive price level," explains Malte Müller, who is responsible for the Simmerring® business for General Industry at Freudenberg Sealing Technologies. "This enables us to tap into a market that comprises many millions of electrical appliances worldwide every year.
Drones, robotic lawn mowers and cordless screwdrivers
Freudenberg is also exploring other uses beyond kitchen appliances for its modular plastic seal design. Electric tools like cordless screwdrivers, and drones, commonly found in modern households, are weight-sensitive; the lighter the weight of the appliance, the easier it is to use. The new design can also be used to seal the wheel shafts of robotic lawn mowers securely against moisture and grass particles. The first series order for the modular seal concept for use in a lawn mower manufactured by a well-known supplier took place in January 2020 with a quantity of around half a million seals per year. Thanks to the modular concept, battery-powered devices can also be fitted with low-friction seals to reduce energy consumption and extend the operating life of the battery.
Ulrike Reich
Head of Media Relations & Internal Communications
Telephone: + 49 (0) 6201 960 5713
ulrike.reich@fst.com chevron_rightDownload Documents
Download Images
News Service
You can subscribe to the Freudenberg Sealing Technologies news alert service, bringing you the news as soon as they are published. You can always unsubscribe from this service.
Subscribe now! chevron_rightFurther Articles With These Taggings
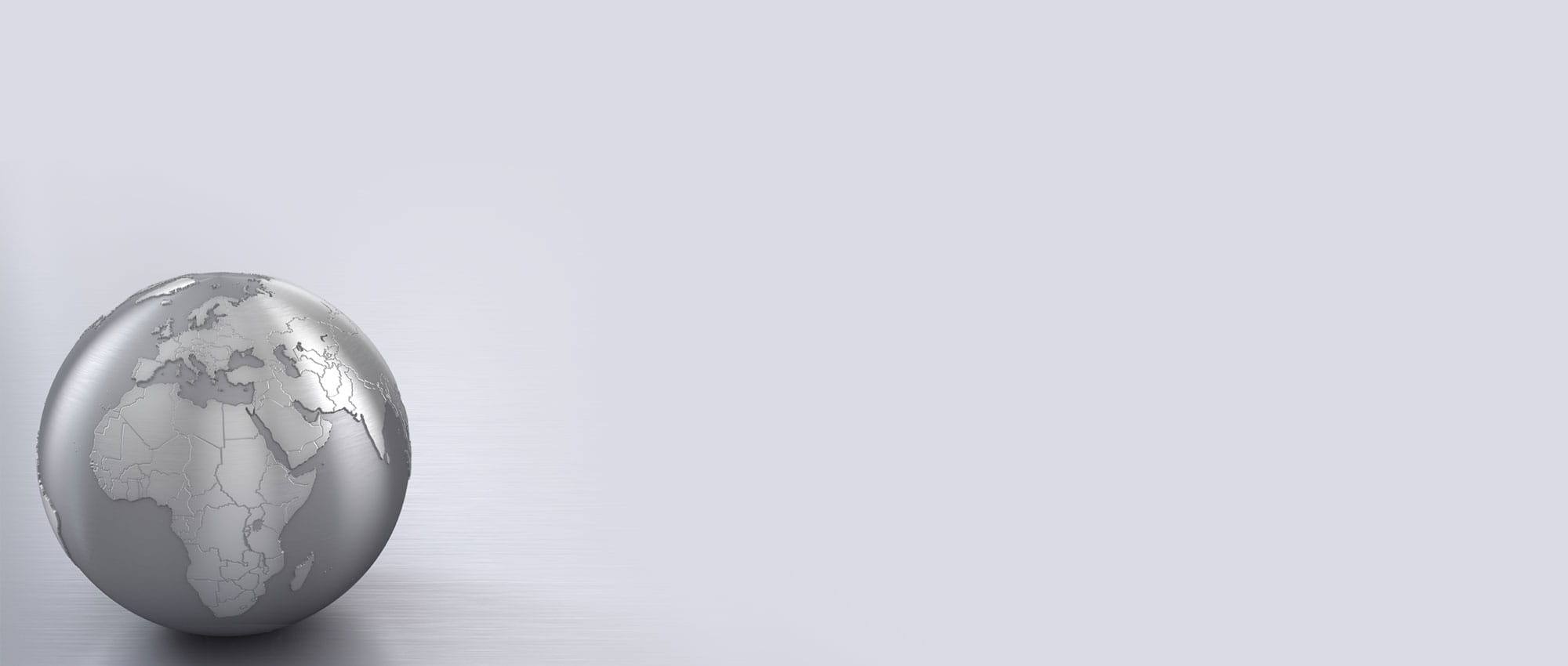
First Hand News
Best of all, keep up with the latest developments
with the Freudenberg Sealing Technologies newsletter.