Obtain news and background information about sealing technology, get in touch with innovative products – subscribe to the free e-mail newsletter.
04.04.2022
Expanding Material Portfolio for E-Motors
In a recorded presentation to be shown at the SAE International’s WCX™ World Congress in Detroit, Freudenberg experts Ray Szparagowski, Engineering Fellow, High Performance Plastics, and Saikrishna Sundararaman, Senior Research and Development Scientist, will outline the benefits of using advanced TCEI materials in slotted rotors. Slot liners molded from Quantix 90-5 thermoplastic, for example, can mold thin cross-sections required for the application.
“E-motors powered by slotted rotors are commonly used in today’s electric vehicles,” said Szparagowski. “Building on our development work with bobbins molded from our TCEI materials – which we introduced at SAE’s 2021 International WCX World Congress – we now offer our customers TCEI slot liners that offer superior mechanical properties, temperature capabilities and thermal conductivity. In addition, these TCEI grades provide good electrical resistance to isolate the system for safety reasons.”
Providing New Options for E-Motors
Plastics are often used in electric components and systems. Despite their ability to offer good electrical resistance, they are poor conductors of heat compared to metals. Losses in electric motors due to windage, friction, iron, and winding, for example, manifest as undesirable heat build-up that raises the temperature inside the motor. As a result, the optimal material would offer both high thermal conductivity and good electrical isolation – exactly the benefits that Freudenberg’s TCEI materials provide.
Freudenberg’s TCEI polymers are designed to address the unique challenges associated with e-motor rotor and stator applications. Primarily used to provide insulation in the slot between the motor winding and the metal laminates, slot liners and bobbins also act as container for stator windings, help retain shape, provide rigidity, offer ease of assembly of the windings onto the stator core and help protect the windings from damage and vibration during assembly and operation.
The Next Generation of Thermoplastics
Engineered plastics are heavily influenced by filler reinforcements. Although unfilled polymers typically have a thermal conductivity of ~0.2 W/m/K, the appropriate choice of fillers can significantly increase this value. Szparagowski and a team of material experts have successfully developed several material grades that enable Freudenberg to offer a customized solution that can be matched to specific application requirements. Each grade offers a unique blend of material characteristics such as tensile strength, elongation, electrical and thermal properties, that are achieved by adjusting the filler. Quantix 90-5, for example demonstrates high thermal conductivity of 0.6 W/m/K through plane and 4W/m/K in-plane. Extensive material testing confirms the material’s superior thermally conductive while maintaining high, electrically isolating properties (volume resistivity of 2 x1014 Ohm·cm).
“Freudenberg TCEI materials will help our customers address e-motor performance improvements through better thermal management.” Szparagowski said. “The reduced internal temperatures within the e-motor can offer significant benefits including higher motor power density, simplified cooling strategies and longer life as both winding enamel and potting materials tend to degrade at higher operating temperatures.”
The TCEI materials for slot liners presentation will be shown at the at the SAE International’s WCX™ World Congress on April 5 at 11 a.m. EST. Szparagowski and Sundararaman will answer questions submitted by email.
Ulrike Reich
Head of Media Relations & Internal Communications
Telephone: + 49 (0) 6201 960 5713
ulrike.reich@fst.com chevron_rightDownload Press Release
Further Articles With These Taggings
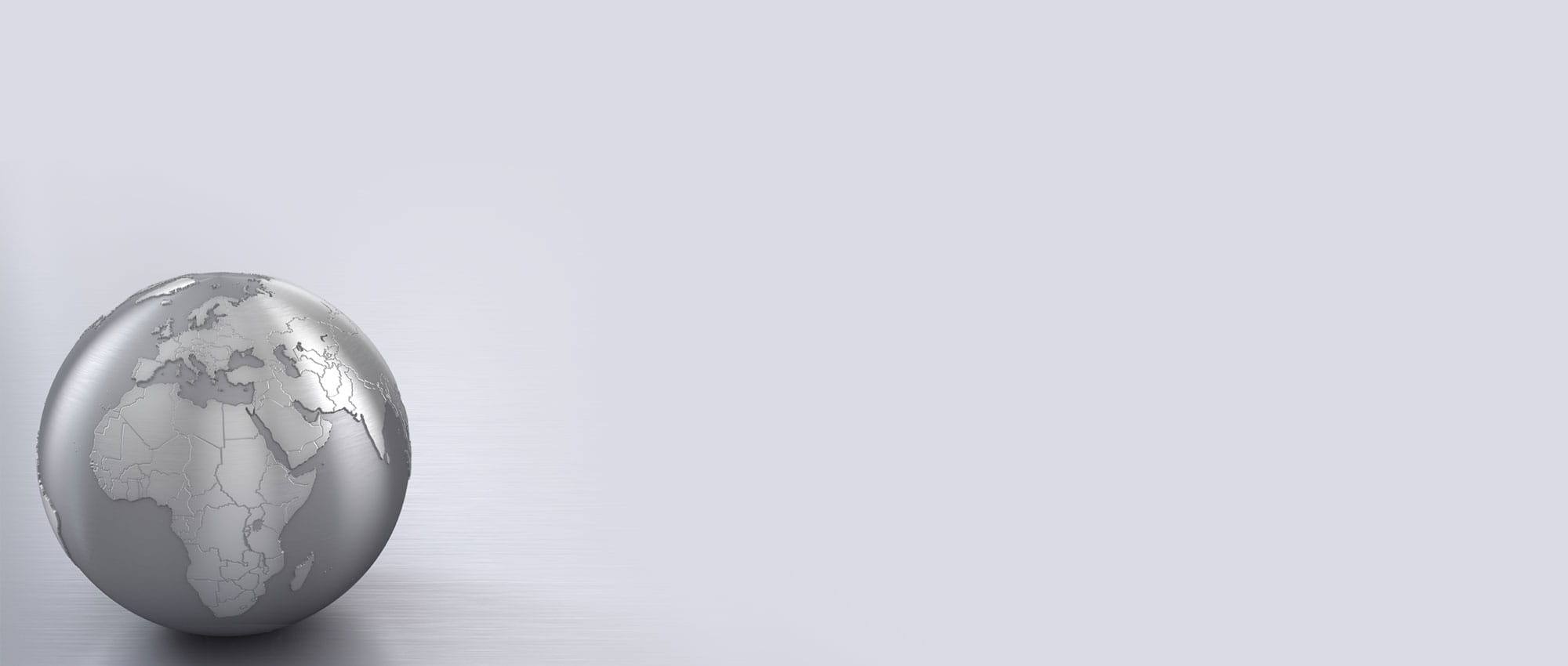
First Hand News
Best of all, keep up with the latest developments
with the Freudenberg Sealing Technologies newsletter.